Designed by the flow – The Revolution of Evolution
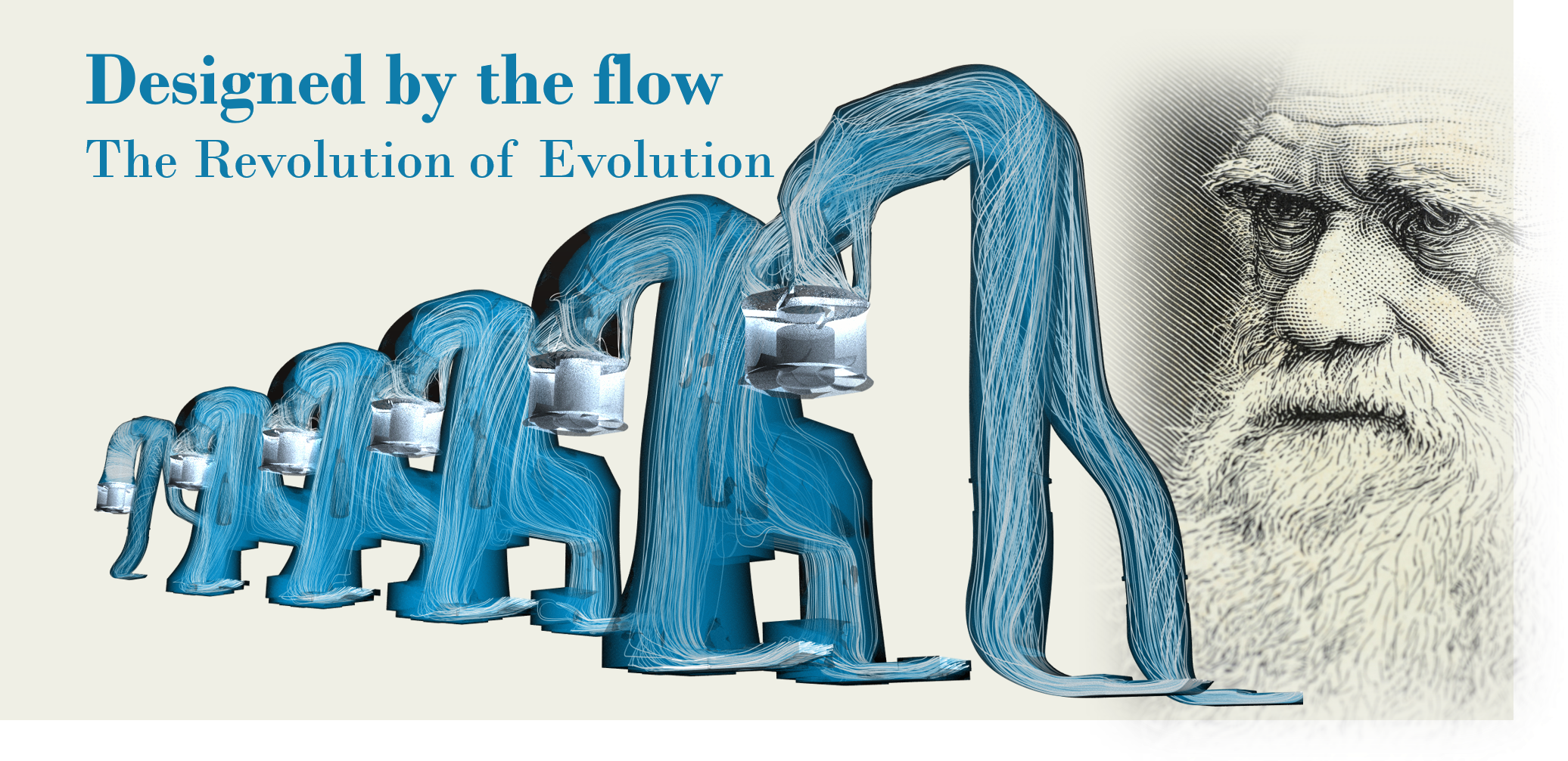
Panta rhei – Everything Flows
The world flows! Literally. There is fluids and flow all around us and there are amazing solutions from nature to tackle associated flow problems. Take the shark nose: Nature came up with the most streamlined nose for this guy to be fast in the water. Same for the Penguin; Did not do a good job on flying for that one to be honest… But there‘s more: Rivers find the best possible way through a given terrain even shaping it for better throughput. Wind shapes trees to minimize the drag on them. Dunes form from out of nothing but sand driven by the wind, creating an aerodynamic bulk of grains. Our very own heart is a flow optimized solution to transport blood through our body in the most economical way etc. etc.

Now – as an engineer – why do I tell you this?
Well, in recent decades engineers have started to look at nature and technically leverage the solutions nature came up with! They started to understand the power of those solutions in nature and began to mimic them to solve engineering problems. Very famous stuff. Called Biomimicry or Bionics.

Admittedly this is amazing engineering, no doubt about it. But there is a bunch of issues associated with it…
- It takes ages for nature to come up with those solutions
- What if nature has not (yet) solved your flow engineering problem?
- What if the solution is great in nature but can’t be manufactured?
Now imagine what would happen, if we don ‘t mimic the few flow-optimized designs that evolution came up with, but instead
we mimic the evolutionary process itself – but an evolution a million times faster!
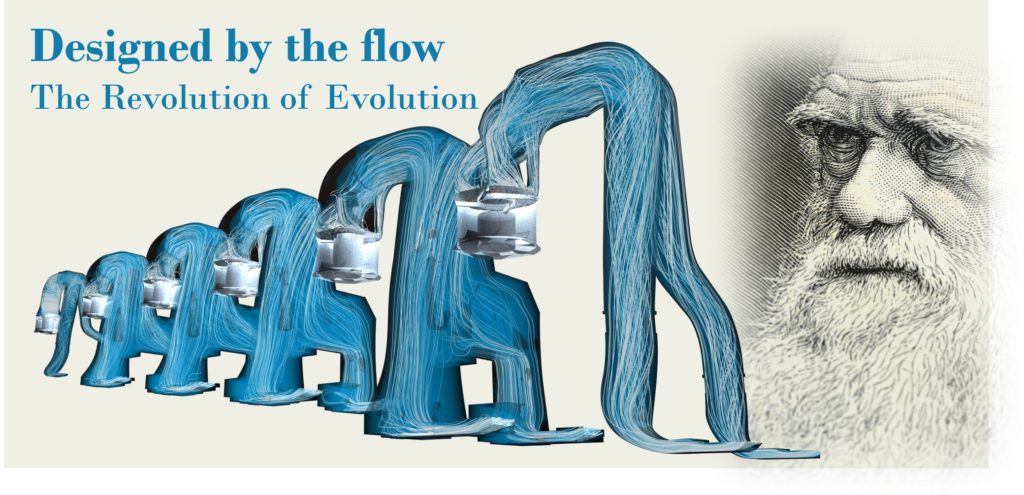
Well, in order to do so, just like for your coffee this morning you need only two ingredients… Number one:
Computational Fluid Dynamics (CFD) Simulation
No worries I will not discuss the equations. But let me tell you this one thing: There is a mathematical equation, called Navier-Stokes Equation that describes the behavior of liquids and gases in all its kinds. And, that one is among the most important equations on this planet. Its Business impact is probably the highest of all equations, I would guess it‘s at least heads up with Maxwell equation for electrodynamics. It‘s probably more business relevant than the well known E=mc2. (it‘s hard to measure to be honest and I may be biased- but undoubtedly the thing is huge!)
But in any case, some find that thing so cool they have it engraved on their arm.

So now, CFD in two sentences, is just this: Split the space of interest into millions of small volumes, called cells, solve the Navier stokes equation in each of them and transfer the physical quantities from one cell to the other. That way you will be able to numerically predict the physical behavior of the fluid.
Anyways, let‘s scratch math here… and come straight to ingredient number two which is probably less famous:
Topology Optimization and the “Adjoint of Marathon”
In order to understand the way a Topology Optimization works imagine you would like to become a six-star medal winner, i.e. finish all big marathons of this earth successfully.
In a nutshell Topology Optimization for CFD (and six star medaling) is an algorithm that works like this:
- For a given domain that the fluid may enter we run the flow simulation using CFD
(You run any marathon)
- Then we assess something called the adjoint: A mathematical function that gives us an idea of which local area has which impact on the cost function, e.g. the pressure loss or the flow rate.

(For the marathon the adjoint goes like this:

- Next, we let the algorithm make those areas inaccessible for the flow (by a wall or solidification) that have the most negative impact on the performance function
(You start training those parts of your body that were showing the biggest negative impact on your run time, detected by those parts that hurt the most. Yes, pain can be a good teacher!)
- In the Simulation we start running the CFD with the newly formed remaining flow domain. So you are back at step 1 but with an updated domain. This time, the cost function – when reassessed – should show an improved value
(You are going to run the next Marathon after training the most relevant parts of your body. This time your finishing time should have improved.)
- We do these steps 1 to 4 in loops until the shape of the flowpath does not change significantly.
(You run one marathon after the other until all parts of your body are trained such that pain is minimized/sufficiently low and in return finishing times are the best possible within the given constraints – aka your physiological preconditions
Topology Optimization – the shortcut
If that was too much…
It‘s just like… a River defining its way! BUT in hours, not ages!

So, with these two ingredients you will have a tool at hand that comes up with optimal solutions for a yet unsolved engineering flow problem within a few hours.
However, there is still issue #3:
Topology Optimization? Great! But that thing can’t be manufactured!
Ten years ago, this story would probably have stopped here. I will always remember my PhD supervisor tell his story about his freeform surface optimization of a turbine blade. As a young engineer he was super-thrilled about the great performance gains the blade showed in the CFD simulation, so in excitement he went to his boss, who then went to the designers, who then said:
“Well, no. We can’t manufacture this. Let’s make this a proper circle and this straight and this plain and …. Boom! Gone was the excitement! Gone was the performance gain! Gone was freeform-based surface optimization!
But the times they have changed!
Meanwhile CAE got a big buddy: Additive Manufacturing
CFD engineers, I am not sure if you all realized yet, but this is a game changer! It is the moment that unchains our creativity, delivers yet unseen freedom in the way we look at possible flow solutions, it’s the moment where we can dig out the old freeform surface optimized shape for the turbine blade.
And, it is the moment where the flow becomes the new designer. It is the revolution of CAE based evolution.
But then, I hear you say, while this digital process sound great in theory and you tell me I can print the wildest shapes now, I still have some doubt:
Why would I trust topology optimization for real life product development?
Well, it’s Darwin Day, so what better test to see if eight million years of evolution can be imitated by a few hours of Simulation, than what’s closest to our hearts? Take a look at this:

For reference, we took an aorta geometry from http://www.vascularmodel.org/miccai2013/. We then generated a sufficiently big box around it as the starting domain, constrained the inlets and outlets in accordance to where they are for the real aorta, then added some (admittedly simplified boundary conditions – blood can be a nightmare in cfd) and let the magic happen.
Check this out, Charles.
Admittedly it’s not perfect, but given it took a few hours on a Laptop, I think we can call it en-par with 8 million years of evolution.
But again, I hear you say. All right, nice toy! But, I am an engineer not a biologist.
Why would I care about this methodology?
Now, I don’t tell you why! I just let you see what has happened to those engineers that already did care.
On 4: Siemens – The brake cooling duct
Brakes of a car can get quite hot. So cooling them through air guided to them is crucial but may cost aerodynamic performance. In the study at hand the goal was to improve the heat rejection a front wheel brake disk through brake cooling duct design. Topology optimization was set up to optimize heat transfer thereby constrain pressure loss in duct to be ~90% of original design. Moreover as a constraint, 10-20 % of design space should remain fluid space
Compared to the reference duct the new cooling duct design showed a 4.4 percent improved cooling performance (heat transfer) at a 21 percent reduced pressure drop. All that achieved within a few days of autonomous CFD simulation.
On 3: EDAG – The scaleable battery pack cooling device
Electrification in automotive is currently a hot topic of discussion. Electric vehicle batteries are continuously improving delivering more power and having greater autonomy but one of the biggest challenges that remain is battery safety and the ability to design an effective cooling system. EDAG as mobility engineering experts explored, with the help of Siemens, the use of additive manufacturing and topology optimization for designing an optimized battery pack water cooling system.
Employing the topology optimization method lead to a 6.4% increase in the mass flow of the inlet duct and 46.9% reduction in the pressure drop of the outlet duct. All this in just 2 days of simulation time (~50 hours in 336 cores). See the video for the amazing new organic design.
On 2: HP – The mighty duct
On 1: What is your flow problem?
In Simcenter STAR-CCM+, the Siemens multiphysics CFD solution, version 2020.3, we introduced an integrated solution for fluid/thermal adjoint based topology optimization. This was inspired by the success but also the lessons learned from the “Mighty Duct” project which was one of the early pilot projects applying the technology. Streamlined and easy to setup, the newly implemented Topology Optimization feature mitigates any need for complicated JAVA macros or third-party tools. It features an integrated constrained optimization method. This allows you to solve engineering problems with competing attributes. By defining one objective and multiple flow and thermal constraints as well as volume constraint it offers numerous possibilities for flow topology optimization.
So the only question left is
When will the flow become your new designer?
Find out more about topology optimization in Simcenter STAR-CCM+
With that said, I wish you a HAPPY DARWIN DAY!
Comments
Comments are closed.
@Simon…Outstanding…Revolution Indeed.