Stitch in time with Simcenter STAR-CCM+ Surface Repair
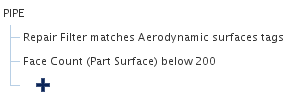
Are you one of those CFD engineers always running up against time with too many finger-crossing moments? Are those moments most frequent at the geometry preparation and volume grid generation stages? If the answer is yes and you have been experiencing sleepless nights thinking how to reduce the model prep time, you are not alone! It is very common to get consumed with the geometry handling difficulties. Anxiety and frustration peak when geometries with tens and thousands of parts are involved. It has been observed that, on average, more than a half of the project time is spent manually or semi-automatically preparing geometries for a good quality engineering solution. Whether your goal is to get a thumb waving answer or nail a benchmark, you can’t escape from this reality. Since the quality of geometry defines the quality of volume grid, one can extrapolate the fact and say that the solution accuracy is ultimately tied with the underlying geometry. So, a stich in time certainly saves nine in alleviating later stage anxieties. Today, I would like to introduce you to the surface repair tool inside Simcenter STAR-CCM+ and focus on a new feature that provides you deeper intelligence over an identified area of interest. Check out the examples and short videos towards the end of this blog.
Challenges with CFD model preparation
There are two key challenges when it comes to CFD geometry preparation: Parts Organization and Surface Repair.
Overall project efficiency depends on how quickly and easily one can organize the geometry, and identify, dissect and fix the surface errors before high-performance machines take over for heavy duty meshing and solver processes. For a typical CFD analysis, simple geometries are usually imported in CAD or non-CAD formats (or in more scientific terms, discrete or tessellated formats), while complex geometries usually come in mixed or hybrid formats, containing both CAD and non-CAD parts. There are many push button tools, both commercial and open source, available in the market for quick geometry prep to solutions. The problem is, they either limit themselves to certain formats of geometry import or ignore those treacherous surface errors by generating simplified volume grids. Let’s not even talk about their solution accuracies in this article!
Once the geometries are organized, the most time-consuming task is to identify and fix surface errors. For real life complex geometries with a sizable number of parts, the surface wrapping technique provides a big respite. Surface repair plays a significant role as a complimentary tool by easily identifying and fixing obvious errors before the initiation of the wrapping process. It ensures wrapping efficiency, helps maintain details of the important surface and hands over a good quality surface to the volume mesher.
When it comes to the geometrical errors, commonly encountered issues are holes or leaks, overlapping faces, intersecting parts or faces, missing faces, duplicate faces, non-manifold edges and topological validity to name a few. We all know that almost all surface repair tools in the market do a reasonable job at fixing most of these issues. What they fail to provide is an intelligence over the errors. This is where you can spend a lot of time puzzling over the correct solution for the problem.
Introducing Simcenter STAR-CCM+ Surface Repair Tool
The Simcenter STAR-CCM+ surface repair tool is a full featured surface repair toolbox which is provided with no added license or cost to help you get your geometry run-ready in record time. As well as providing a wide range of surface fixing options, it contains advanced diagnostics and search capabilities for better understanding of the geometry and any errors it contains. Its intuitive selection toolset lets you highlight, rename and combine parts, faces, edges or vertices easily to organize your model. The underlying java client lets you access all possible automation tools from scripting to batch processing. One of the most important elements of surface repair tool is its diagnostics tool. It offers functionality to identify error prone parts, surfaces and feature edges and provide real time information via the browse tool as you fix them.
Simcenter STAR-CCM+ Surface Repair UISearching for errors
In Simcenter STAR-CCM+ v13.02, we take the diagnostics tool to the next level by providing intelligence over errors with a new search functionality. Let me explain what I mean. When it comes to diagnostics, the majority of surface repair tools provide error information without pin pointing exact details. It takes an experienced engineer significant time to filter them out before suggesting suitable corrections. With the latest release of Simcenter STAR-CCM+ v13.02, we are enabling a whole new feature that lets you filter multiple queries simultaneously and fix the parts or surfaces that can’t be easily investigated. For the first release there are six basic repair filter types (or predicates) available to use. The tool will continue to be expanded and gain more capabilities with every upcoming releases.
Predicates or Filters
- Part Name: Search for parts based on the presentation name
- Part Surface Name: Search for part surfaces based on the presentation name
- Area: Search for faces/surfaces based on the area
- Volume: Search for closed surfaces based on the volume
- Area/Volume Ratio: Search for closed surfaces based on the area/volume ratio
- Face Count: Search for faces/surfaces based on the face count
Filter predicates can be used individually to search for parts or pieces of geometry but the true power of search can be seen when predicates are compounded within a filter, using logical operators (AND, OR or PIPE) to provide additional control. This is especially true when combined with different grouping mechanisms for evaluating different topology structures that can result when contacts have been created due to imprinting.
Now, let’s look at some examples and explore the power of a new search feature under the diagnostics tool.
Example 1: With my complex geometry, how do I quickly isolate tiny closed volumes within a specific range?
- Use the predicate, ‘Topology Part Surface is closed’ to identify all closed volumes. To locate the side mirrors and similar volumes, use a query tool to determine the volume of one of the Wing Mirrors as 6.58e-4 m3, and create a ‘Volume’ predicate to isolate the rest.
Example 1
Example 2: I know surface area of one of my parts. I also know that I have multiple of them in my model. How can I flag all of them quickly?
- Use a query tool to get a surface area of one of the tires and use an ‘Area’ predicate with range to isolate all four tires. The wheels can be isolated in a similar filter.
Example 2
Example 3: I have spent time tagging all the key parts and assemblies under Simcenter STAR-CCM+ simulation tree. Now, I want to investigate one specific tagged parts for its surface quality while I am in the Surface Repair tool. How do I locate it?
- Let’s say the Struts are tagged among others under Simcenter STAR-CCM+ simulation tree. Using ‘Object’ filter, ‘Struts’ as a predefined tag under simulation tree can be quickly identified.
Example 3
Example 4: Now that I have isolated all my tagged Aerodynamic surfaces, as a part of surface quality check, I want to further find all the surfaces with a face count less than 200. Can I use multiple filters simultaneously?
- Assuming you have already isolated
the tagged ‘Aerodynamic surfaces’ using an ‘Object’ filter, select it under ‘Repair’ filter and combine it with the ‘Face Count’ predicate of a value fewer than 200 faces.Example 4
Today, every serious investor in CFD measures returns on end-to-end solution time; CAD to post-processing. Having an embedded surface repair tool, Simcenter STAR-CCM+ provides significant advantage over all other tools in the market with a robust, reliable and repeatable processes. While you wait for your experienced engineer to show you how to locate those annoying errors, search filters have already done that work for you! It will certainly give you a break from those sleepless nights for fresher mornings…give it a ride!
The author thanks Kevin Jones and Sabine Goodwin for their valuable inputs in writing this article.
Comments
Comments are closed.