MBST: the marriage of Test and Simulation – part 3
![[3/22/2021 2:57 PM] Sales, Ricardo (DI SW STS TEST DEV ATH): Simcenter Vehicle Sound Simulator](https://blogs.stage.sw.siemens.com/wp-content/uploads/sites/6/2021/03/Simcenter-MBST-Simulator-test-and-simulation.jpg)
Have you ever thought about how the NVH (noise, vibration and harshness) of your vehicle influences your driving experience? The manufacturers know that and are implementing innovative techniques to evaluate the NVH perception during the vehicle development process.
This article is the third article in a series where we illustrate how test and simulation are combined increasingly in vehicle development. Here I will show an example where test and simulation run together in real-time.
NVH performance during development cycles
Some trends in the automotive market are — globalization, increased competitiveness, and more demanding customers. Consequently, this puts more pressure on development cycles (time x cost x quality) and increased vehicle variants in the market. As NVH is a crucial vehicle attribute impacting the customer’s choice, an A-OEM needs to control it throughout the complete development process.
As hinted in the introduction, NVH directly impacts the emotions and perception of the driver. It can play a crucial role in the buying process of the end-customer. How can we make these subjective NVH aspects part of the vehicle development process? Or in other words, how can we evaluate NVH perceptions of our vehicle as early as possible, even long before prototypes are available?
The answer to that requires first to go beyond pure objective NVH target setting approaches. Using classical frequency-based target curves on vehicle and component level is not enough. Firstly, one needs to translate those curves into a real NVH driving experience that allows one to listen to and feel the vehicle in the early stages of development. Secondly, how to validate this is exactly where a vehicle NVH simulator comes into play.
Driving a car that doesn’t exist
The Siemens vehicle NVH Simulator allows you to “drive” the digital twin of your vehicle. This digital twin is essentially build-up from two models:
- a performance model that simulates the driving response of the vehicle to the driver input;
- NVH models that create the NVH time series from the output from the performance model.
The NVH model is build-up from different frequency domain curves and includes an “engine” that can synthesize the NVH output to the driver on the simulator. With this, it directly translates the classical NVH target curves into actual NVH data that can be experienced by the “driver,” being an NVH expert or not.
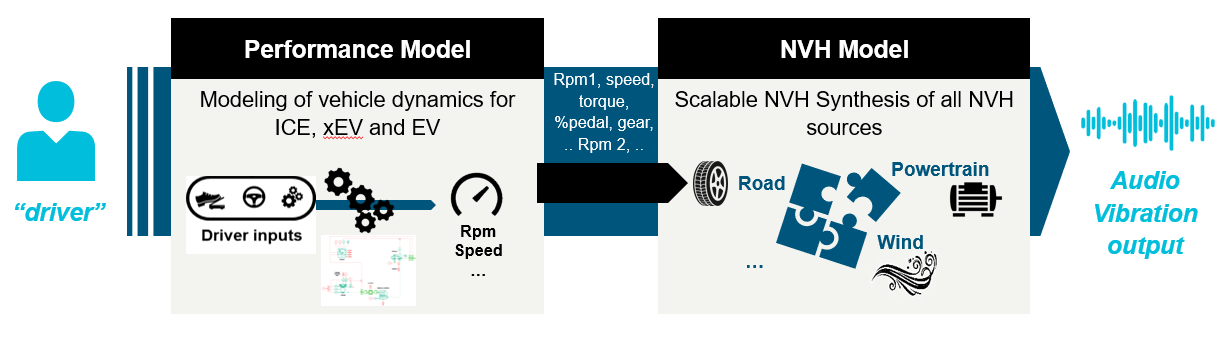
Drive it, change it, feel it!
To get the complete picture of NVH perception, it is not enough to only concentrate on the NVH modeling. The link of the NVH perception to vehicle performance is equally important. Some examples are:
- How exactly does a driver expect the vehicle to sound while performing a very rapid full-throttle acceleration?
- How should it behave while driving at a constant speed?
- And how to evaluate the NVH perceptions with complicated hybrid powertrains that switch between fully electric modes, regenerative braking, and operations with the combustion engine operating?
Here the vehicle performance model plays a crucial role. A complete vehicle driveline model needs to be modeled in this case. You can do this in Simcenter Amesim, for instance, including any level of detail of controls. The below example shows a relatively simple example of such model, where a Tesla model S is modeled. You can imagine much more complicated scenarios for hybrid vehicles.
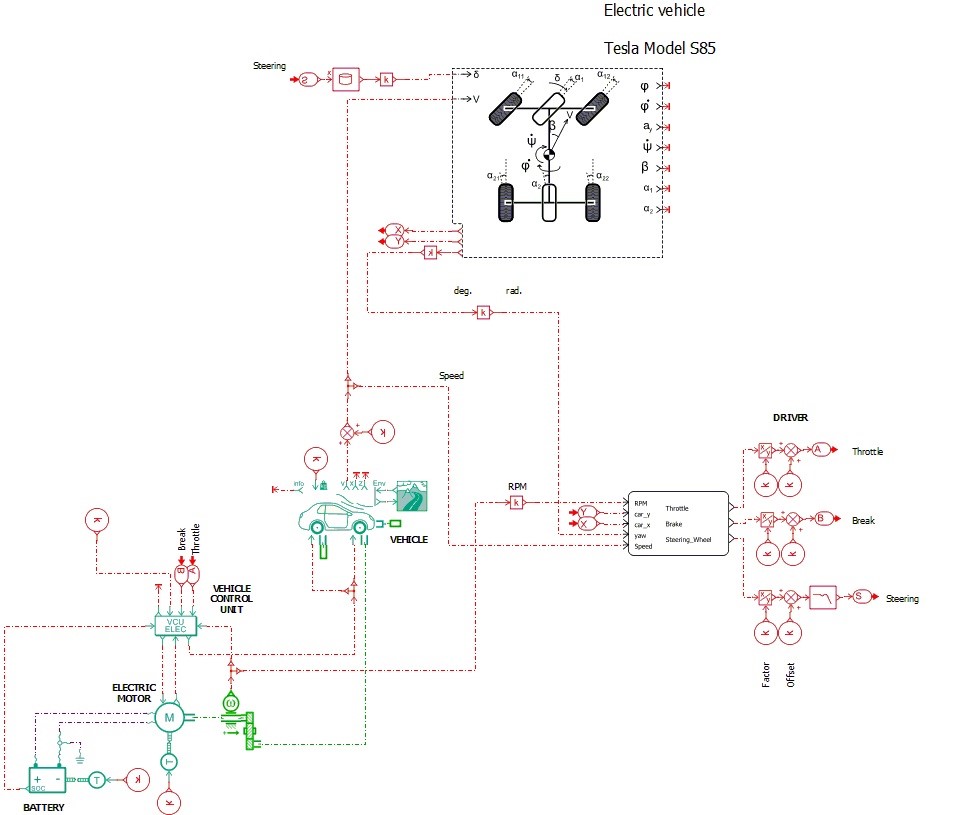
When you apply changes to the vehicle performance model (e.g., changing vehicle controls), the NVH performance is affected. Therefore, it is crucial to be able to make real-time modifications to those models. It is exactly here that test and simulation come together: it becomes a must to run simulation driveline models in real-time and be able to tune parameters in real-time.
To allow assessments of real-time modifications on the vehicle, Siemens enables you to load and run the complete vehicle performance model onto a Siemens real-time machine. The principle is simple:
- The real-time machine converts the “driver” input in real-time into the vehicle state outputs that the NVH model uses to generate the vehicle NVH.
- Model parameters are changed/updated, and the impact on the driver’s NVH perception is then assessed in real-time.
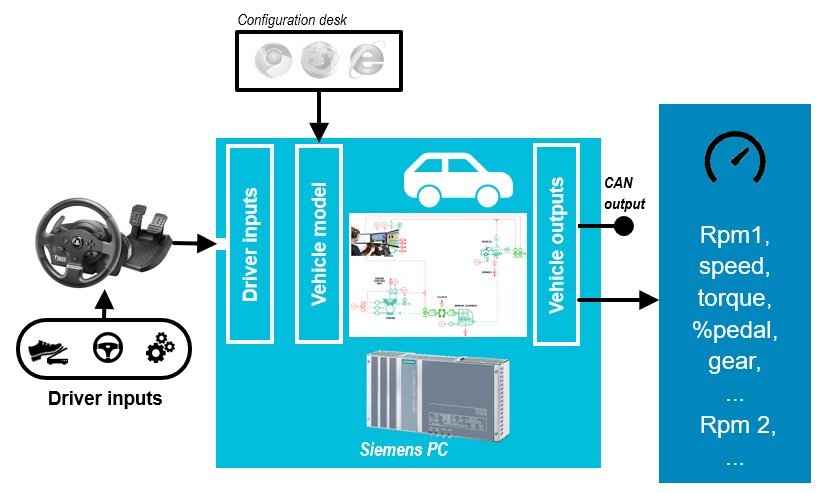
Besides providing real-time inputs for the vehicle NVH model, the real-time machine can also emulate a vehicle CAN-Bus. This feature allows real-time tuning of active sound models. Imagine, for instance, modifying and tuning operational sound models for different vehicle variants in literally minutes. Moreover, you can load other models onto the simulator, avoiding testing them on separate physical prototypes.
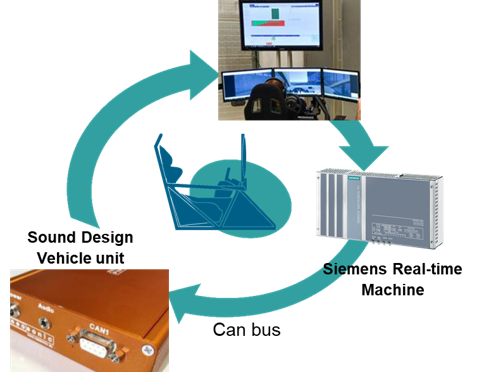
This brings impressive flexibility as it allows to evaluate modifications applied to the simulation model in a few minutes. It’s easy to understand the enormous gain in time and cost by avoiding these activities in the prototype phase.
Full control of NVH by combining test and simulation
In this Model-based system testing (MBST) blog series, we talked about how test and simulation can collaborate in an efficient move towards model-based development. This is a smart move as the engineers will have the possibility to evaluate performances early in the development cycle. And again, this represents a gain in time and money!
In the first part we explain how simulation engineers use test data to validate their models. Test data can both serve to validate models and to provide realistic input to the simulations.
In the second part we went through an application where simulation models are used to enrich test datasets. In this case, data in difficult-to-measure locations is added during the testing campaign by using virtual sensors. This represents gains in efficiency, processing time, and accuracy of the data.
Finally, in this third and last blog post, we saw how you could use test in combination with simulation in real-time applications. Simulation models running on real-time machines provide accurate and reliable output to drive simulators, allowing the users to sense any modification done to the models and this in real-time.
The vehicle sound simulator represents an amazing application with best-in-class technologies like MBST, NVH synthesis, artificial intelligence, and even active sound design. These give the best sound perception and can be combined with larger simulators and motion platforms to provide a complete driving experience.
You can also apply real-time applications for components/sub-systems testing in test benches. In this case, the simulation model will provide the loads acting in the components. Therefore, the physical components can be tested and evaluated before being integrated into the vehicle.

MBST represents a significant evolution in how vehicle performance evaluation happens during a development cycle. The ability to work with digital twins of your product will boost development processes. It allows you to shorten your development while reducing the cost.
I’d like to invite you to check out the part 1 and part 2 of this blog series. And if you would like to know more about the Vehicle Sound Simulator, please check the on-demand webinar: