Where’s the real digital twin action?
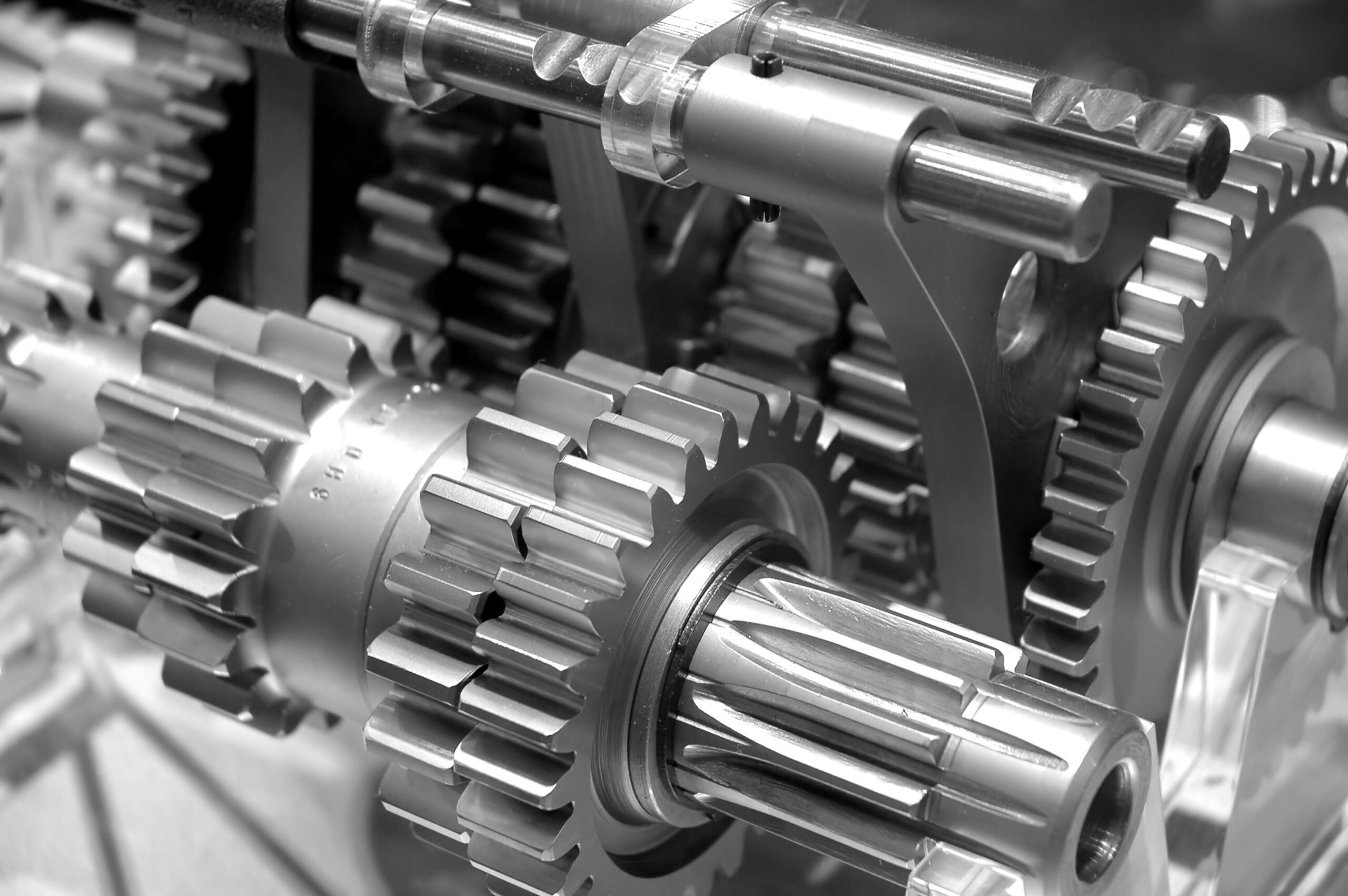
Where’s the real digital twin action, you ask? In research, of course. Or how EU and Belgian research projects help engineers validate lightweight gear models for a greener tomorrow…
Before we all take off on our much-anticipated summer vacations, I wanted to share a little story about a team of innovators right here in our own backyard. For years, the RTD team at Simcenter in Leuven, Belgium has maintained close ties within the European and international research communities. Projects range from internal and university partnerships to Marie Skłodowska-Curie Initial Training Networks and EU framework projects, and Flemish, Belgian and international projects and working groups as well.
Technically possible?
As a rule, research projects target a complex technology domain for Simcenter customers. These customers usually face challenges with industrial product design engineering processes. The primary goal tends to be developing new simulation and test solutions and proving technology ability. The end goal, in many cases, is a path to technology commercialization. Or in other words, creating technology that ends up in a product on the market. This, as one can imagine, can take a while. (For example, one of the principle projects DEMETRA, that we’ll talk about here, started in 2014.)
The real digital twin action is in research
So it seems, the real digital twin action, one might argue, is in research. Now, this isn’t a surprise to me since I have always enjoyed checking in with the researchers at Simcenter. One project that caught my eye a few years ago was DEMETRA. (DEMETRA stands for Design of Mechanical Transmissions: Efficiency, Noise and Durability Optimization.) It was an EC Marie Curie project coordinated by the University of Calabria (UNICAL) in Italy.

Although the DEMETRA project formally ended in 2017, the research work continued via the ECO-Powertrain project, funded by VLAIO. As one can imagine, many researchers were involved along the way. Today, Ali Rezayat, a Research Engineer at Siemens Digital Industries Software in Leuven, Belgium, and Cristian Enrico Capalbo, a visiting PhD student from the University of Calabria, have recently wrapped up the digital twin and algorithm validation parts. We caught up with them to talk about the experimental validation of composite gears and digital twins.
But first, a bit of background
From the start in 2014, the basic goal of DEMETRA was to study promising state-of-the-art modeling methods for transmission subsystems. The focus was mainly gears and bearings. The idea was to analyze and optimize a mechanical transmission as a complete coupled dynamic system. Over a four-year period, researchers used a systematic approach to develop advanced simulation methods and digital twins, supported by experimental validation using Simcenter solutions.
Throughout the years, many Simcenter RTD researchers have worked on the project. As explained in the movie, many aspects of this research work have resulted in highly innovative solutions that are part of Simcenter 3D today, such as the Simcenter 3D Motion Transmission Builder and the Simcenter 3D Motion Advanced FE Preprocessor.
For those of you who want more details, there is an excellent white paper available here.
The proof is on the test bench
Towards the end of the project, the focus was on testing and validation. The team had proven they could build accurate models of complex lightweight gears using Simcenter 3D Motion Transmission Builder. But, they wanted to be sure that they could experimentally validate these models to obtain a digital twin. This, of course, meant acquiring real data. This is where the precision gear test rig steps into the picture. The test rig is located in the test facilities of Simcenter Engineering Services in Leuven.
The team had proven they could build accurate models of complex lightweight gears using Simcenter 3D Motion Transmission Builder. But, they wanted to be sure that they could experimentally validate these models to obtain a digital twin.
Various types of conventional and lightweight gears, including reinforced composite gears, were put through runs using Simcenter Testlab software and a 48-channel Simcenter SCADAS data acquisition hardware unit with a rotating machinery card. Using the Simcenter testing solution, the team gathered the necessary data to validate the models, a process that turned out nicely. The team successfully analyzed experimental results in Simcenter Testlab, including correlation and validation of the simulated gear digital twins. This is definitely an advanced Simcenter simulation and testing solution that will help engineers design and validate lightweight gears for a greener tomorrow.

What’s next?
Today, simulating and testing gears and drivetrains remains a very active research area for the three research partners. Siemens Digital Industries Software and KU Leuven will continue to focus on modelling and optimizing drivetrain components. And UNICAL has started to investigate applying the composite technology used during these projects to develop better-performing, lightweight robotic arms.
This is definitely an advanced Simcenter simulation and testing solution that will help engineers design and validate lightweight gears for a greener tomorrow…
Click here to read the full story about how this research has helped Hyundai reduce gear whine in drivetrains.