The Digitalization of Industrial Machinery
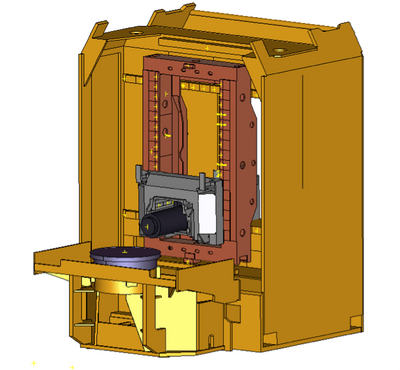
Providing realistic virtual simulation
Throughout the computer-aided engineering (CAE) design process, engineers must balance a variety of critical performance aspects to validate whether the product under development will work as intended. This complex task cannot be based on a test-and-repair approach. Such an approach would lead to expensive iterations on physical hardware. Other unique projects require that the first prototype is the final product. Testing these kinds of products under extreme boundary conditions can have dramatic consequences.
As a result, Siemens PLM Software solutions provides engineers with the necessary tools to conduct upfront analysis for a variety of applications during the design process. To be successful, machine manufacturers must use models to reproduce the complex behavior within the operational environment. Engineers require pinpoint accuracy to understand how structures work and expedite the analysis of new designs for potential modifications that optimize performance.
The right solution for any nonlinear application
Computation of accurate dynamic loads in structural analysis often requires the consideration of nonlinear behaviors. Simcenter Samcef nonlinear motion analysis fully exploits the augmented Lagrangian method and the large-displacement-large-rotation approach to deliver this capability. The software features an extended library of flexible kinematic joints that can be included in FEA. By coupling these joints to super elements and beams, the complete kinematics and dynamics of the system can be simulated.
When combined with Simcenter Samcef nonlinear structural analysis, nonlinear and fully meshed components can be included to capture material and geometrical nonlinear structural behavior. Furthermore, Simcenter Samcef can be used to integrate sensors, actuators, and controllers in the simulation. These can be imported from Matlab®/ Simulink® and Simcenter Amesim™ software or preprogrammed in Simcenter Samcef. In that case, the control parameters can be optimized. Simcenter Samcef can also be coupled to Matlab and Simcenter Amesim for co-simulation. This co-simulation capability is done through a dedicated module that enables coupling between different transient solvers. This mechanism is used to connect Simcenter Samcef to the AMRC tool (a research center linked to the University of Sheffield) that provides the cutting forces of the machines.
Twin-Control Project
Twin-Control is a European project (H2020, grant agreement nº 680725) aimed to develop new concepts for machine tools and machining process performance simulation. It is coordinated by IK4-TEKNIKER in Spain, with additional partners Renault, COMAU, MASA, Gepro Systems, ModuleWorks, Artis, Predict, TU Darmstadt, University of Sheffield and Samtech, a Siemens Company, in Liège, Belgium.
In the Twin-Control project, Siemens focuses on the dynamic modeling of machine tools, including its Computer Numeric Control (CNC), and its interaction with the machining process. To properly simulate modern high-speed tools, which show close interactions between the dynamic behavior of the mechanical structure, drives, and the CNC, it is crucial to build models that represent the flexibility of all components and interactions.
Simcenter Samcef Mecano enables accurate modeling of machines by considering FEA modeled components connected by a set of flexible kinematic joints. Models are implemented to deal with drive-trains and motor dynamics. To fully capture the dynamic behavior of the machine tool, force interactions between the cutting tool and the workpiece are also considered in the models. These forces consider the dynamics of the tooltip, combined with the tool work-piece engagement determined by Module Works CAD/CAM for toolpath generation and simulation.
As seen in figure 1, a model of the CNC is connected to the machine model by specialized elements that compute motor forces from controller inputs, calling a dynamic library embedding the Matlab Simulink model of this controller.
Figure 1: Coupling scheme
To properly model the machine tools when operating, the following objectives are followed:
-
- Properly account for flexibility of all structural components, connections and feed drive to obtain a model that can represent interior vibrations. The guiding system is modeled by flexible slider elements, which constrain a node to move along a deformable trajectory represented by beam elements.
-
- Limit the number of degrees of freedom (DOF) as much as possible to use the model in the time domain (small time step imposed by the machining simulation module and the controller model). This is done by using a super-element technique. The model contains super-element techniques and can represent the desired levels of vibrations.
The proposed technology is applied to build a flexible multibody mechatronic model of a box-in-box fast machine of project partner COMAU, as seen in Figure 2. This approach provides comprehensive simulation capabilities for virtual machine prototyping in working conditions.
Figure 2: A Multibody model of the COMAU machine tool. Courtesy of Comau.
Another example that illustrates this technology is the 5 axes machine from project partner Gepro Systems (shown in Figure 3).
Figure 3: A Multibody model of a five axes machine tool with multiple spindles. Courtesy Gepro Systems
An industrial CNC controls the motors of the axes to follow the desired trajectories with minimal error. In the model, all frames are fully flexible, as the rails and screw drivetrains, which are represented by a set of slider elements. The control loops are modeled in MATLAB/Simulink, translated into a dynamic library associated with specific control elements to manage the coupling between 1D models and flexible 3D models.
The resulting Twin-Control simulation package is dedicated to both machine tool builders for design activities and machine tool users looking to improve their processes. In both cases, this virtual model will avoid performing costly physical. Simcenter Samcef, coupled with the different modules from our partners, allows building this virtual model in the form of a fully flexible and nonlinear finite element based digital twin.
Join our webinar series on machinery simulation.