Why anisotropic meshing increases your happiness
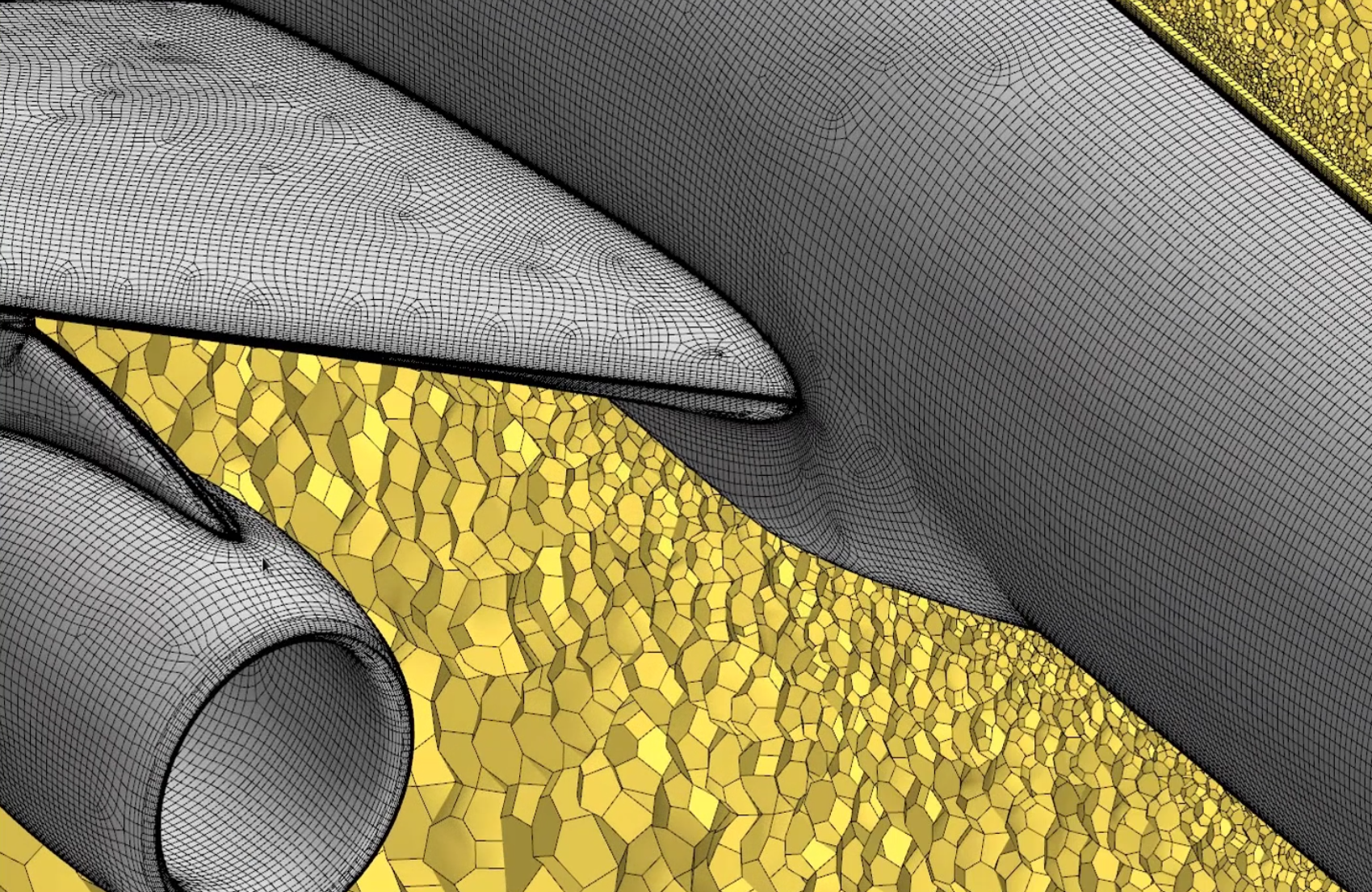
The easiest way to increase happiness is to control your use of time. Can you find more time to do the things you enjoy doing?
Daniel Kahneman, Thinking Fast and Slow
One of the most influential books I have ever read is “Thinking Fast and Slow” by Daniel Kahneman. It is a book about judgment and decision making, heuristics and biases, intuitive thinking, and many other topics. At the end of chapter 37, Professor Daniel Kahneman mentions the quote above. The quote is essentially is one of the concluding summary statements of the chapter. Amongst the many different topics and ideas from his book, the quote above strongly resonates with me. Time is precious and it can be difficult to spend it entirely on activities that we enjoy doing. This is true either at work or in our personal life. Do you often consider how you can spend your time more effectively? Which actions/activities take up most of your time?
Stop spending so much time in meshing
In the simulation world, one of the activities that can be very time-consuming is meshing. Meshing is a fundamental part of pretty much every simulation process. The generated mesh needs to be of high quality to ensure an acceptable accuracy of results. On the one hand, meshing typically takes a lot of time for CFD engineers. On the other hand, to innovate, one needs to evaluate 100s of designs and produce accurate results in a fraction of time. Every engineer wants to spend her time in activities that improve a product, such as considering alternative designs and spending time on what-if scenarios.
Simcenter STAR-CCM+ offers a unique automated CAD to mesh pipeline that comes with highly scalable parallel volume meshing algorithms (information about the benefits and speedup of our industry-leading polyhedral mesher can be found here). Consequently, these tools empower the CFD analyst to spend less time meshing and consequently more time innovating. On top, the upcoming release of Simcenter STAR-CCM+ 2021.3 comes with two powerful new features that significantly reduce meshing time and computational resources required for aerospace and marine applications.
Anisotropic Meshing
Simcenter STAR-CCM+ 2021.3 comes with a semi-automated anisotropic quad surface mesher that can generate high-aspect-ratio cells to capture high curvature geometries. As a result, users can obtain an efficient mesh distribution leading to decreased overall mesh count, mesh generation time, and associated memory requirements. The animation below shows an example of how we use it in a generic aircraft geometry. You can enable anisotropic meshing via custom curve controls which allows for the creation of anisotropic layers around a set of feature curves. We modified the pre-existing quad mesh algorithm based on an advancing front approach to allow the generation of anisotropic faces.
Firstly, this can provide a greater degree of flexibility and the possibility to adapt to different situations e.g., where opposite fronts collide. Secondly, another distinct advantage of the algorithm is that it is better at handling corners with angles close to 90 degrees and the mesh does not retract at corners.
Two different studies, one from the marine, one from the aerospace industry demonstrate the amount of time savings you can achieve by using these two new features together.
Speeding up in the marine industry – Potsdam propeller case with anisotropic meshing
The Potsdam propeller case (or web link) was analyzed with the new parallel core advancing layer mesher with anisotropic surface refinement. We ran case 2.3.1 (J=1.019) with the polyhedral and anisotropic quad meshers. For this case anisotropic meshing brings significant improvements in meshing time (4x speedup) and run time (~2x speedup) as shown in the table below:
Mesh type | Meshing time (minutes) | Run time (minutes) |
Isotropic mesh | 36 | 106 |
Anisotropic mesh | 8 | 54 |
The results of the simulation matched the EFD results very nicely. The thrust coefficient differed by just 0.95%, with the measured thrust coefficient. The torque coefficient differed by 0.45% with the CFD result. Take a look at the experimental facility here. The experimental observation matches well with the simulation results shown in the animation below.
Faster aerospace aerodynamics – The NASA juncture flow experiment with anisotropic meshing
Next, we analyzed the NASA juncture flow geometry using the new parallel core advancing layer mesher with anisotropic surface mesh refinement. This case uses a full-span wing-body configuration and primarily focuses on the flow separation that occurs near the trailing edge of the wing at the wing-body junction. The case modeled had a 5-degree nose-up angle of attack. The Mach number was 0.189, and the Reynolds number was 2.4M.
Anisotropic meshing can bring significant reductions in mesh count (~3x reduction) and associated run time improvements (~3.8x speedup) as demonstrated in the table below. The predicted lift for the new mesh is within 1% of the original value derived by the isotropic mesh, while the drag differed by 4%. Overall, there is good agreement between the CFD results and the experiment. The animation above shows the wall shear stress contours over the wing surface.
Mesh type | Mesh count (Million cells) | Run time (CPU core hours) |
Isotropic | 37.3 | 287 |
Anisotropic | 12.7 | 75.6 |
Parallel core Advancing Layer Mesher (ALM)
The Advancing Layer Mesher (ALM) allows for the generation of high-quality prismatic cell layers on surfaces i.e. it generates the boundary layer mesh. In the upcoming release of Simcenter STAR-CCM+ 2021.3, when using the ALM, the core mesh is now generated in parallel bringing significant speedup and time savings.

Mesh generation speed and consistency
The chart above shows the parallel scalability for 4 industrial cases representing meshes between 30 to 109 million cells. All generated meshes are high-quality polyhedral meshes with prism layers. The submarine case can be meshed now approximately 6.3x faster which means that it takes 34.5 minutes to generate 39 million cells in 120 cores. For this case ~1.14 million cells were generated every minute. For the largest case of 109 million cells, the mesh generation time was 2.4 hours in 120 cores (compared to 9 hours in serial). You can find more information about the parallel scalability of our Polyhedral Mesher and Prism Layer Mesher here. Prism Layer Mesher is another approach in Simcenter STAR-CCM+ to generate high-quality prismatic cell layers on surfaces.

Mesh consistency across many core counts is of paramount importance as simulation results should not differ whether you are meshing in 1 core or 200 cores. Throughout the algorithm development process, we have paid extra attention to ensure high mesh consistency. For parallel core ALM when testing it on 24 industrial cases, the average cell count difference, from serial up to 160 cores, was below 0.1%. This brings trust and confidence that the difference in stimulation results will be negligible. The image above shows an example of mesh consistency, comparing serial and 120 cores. Note the similar volume mesh distribution both in contour and histogram plots.
Spending your time where it really matters
To conclude, these two new features in Simcenter STAR-CCM+ 2021.3 will offer a faster turnaround time leading to increased simulation throughput and productivity. They will empower you to take your product ideas to the market faster. Consider using these enhancements to save time and spend it more on the things you enjoy the most! Spending your time where it really matters may after all make you happier!
Read more about all top new features of Simcenter STAR-CCM+ 2021.3