Model-based design from ICEs to ICUs: Bridging the industries to improve software quality for medical devices
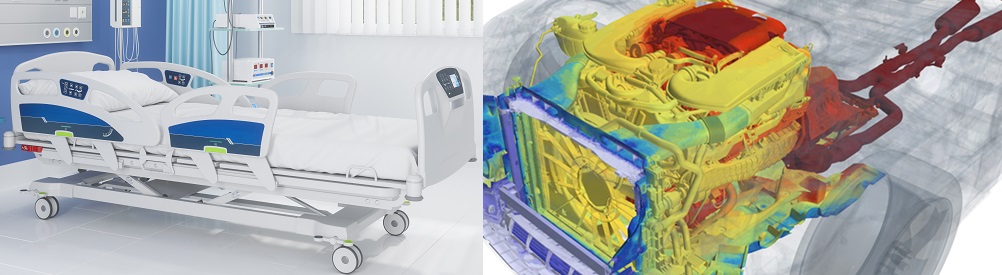
The events of the past few years have turned global attention towards health and, more specifically, healthcare. From the images of overcrowded hospitals to the race to create, test, approve and roll out safe and effective vaccines, we have seen both the limitations and the sheer potential of healthcare as we know it.
Learning from the automotive industry
We at Simcenter Engineering Services believe that automotive engineering offers many clues to possible applications of model-based design for the development of medical devices, equipment and systems. Admittedly, cars and medical devices may not seem to have much in common. But there are many parallels that can be drawn when it comes to their design and analysis processes.
The first is the regulatory landscape and ISO standards that must be met in both fields—as a matter of life and death in the most extreme circumstances. Another is that, whether for an engine component or a medical scanner, system performance is critically dependent on not just controls that drive the electrical, mechanical and hydraulic functions, but also on the underlying software quality. But despite these commonalities, the automotive and medical device industries are worlds apart in terms of maturity; if automotive is the figurative veteran in this scenario, the medical devices industry is the young apprentice.
For this reason, we believe that the medical industry can learn and leverage best practices from the automotive industry—in particular, by adopting model-based design processes to improve software quality for medical devices. First, let’s take a step back and look at why this is so critical to the medical device industry, especially now. With the advent and application of big data, AI, robotics, and digitalization, the field of medical devices is becoming increasingly complex.
Big data and AI

Big data and artificial intelligence have become increasingly important in nearly every industry. They have also created some uncertainty: How should companies deal with big data? How should they structure it? How can engineers make good use out of it? How can AI be applied?
In the medical device industry, this issue is compounded by the enormous amounts of data that are being developed in the form of personal biometric devices, such as fitness watches, heart rate monitors, and more. Visits to the doctor add another layer of health data, such as MRI images, test results, etc. This all adds up to terabytes or even petabytes of data over a person’s lifetime.
This data presents a challenge to engineers and doctors who need to determine not only how to make good use of all the information collected in order to provide accurate diagnoses to patients, but also how to use that information collectively to help future patients and prognoses.
Robotics
For most engineers, the term “robotics in medical” will likely conjure images of surgical robotics systems. However, there are many applications for robotics in healthcare.

Consulting firm Mercer estimates that, by 2025, the US will face a shortage of:
- 446,300 home health aides
- 95,000 nursing assistants
- 98,700 medical and lab technologists and technicians
- 29,400 nurse practitioners

This creates opportunities for robots to take over several tasks, such as automatic routines that a physical therapist would perform for a stroke patient, helping people with mobility, delivering hospital food, providing concierge services, transporting patients, and more.
Consequences of recalls

In addition to the possibilities that these enabling technology trends offer, there also comes risk—and we are seeing this play out in real-time.
Case in point: search the FDA’s Medical Device Recalls database and you will see that Class I recalls (the highest and most serious recall the FDA can issue) are frequent. In worst-case scenarios, this is due to resulting death from a device—say, an insulin pump, for example—malfunctioning.
Aside from potential design issues, the predominant reason for these recalls is software. After all, as the functionality and design complexity of these electro-mechanical tools and systems increases, the more is asked of the underlying software design. And sometimes, it seems, it is simply not up to the job.
Software is the main driver wtih [medical device] recalls. It’s been the top reason for 17 of the last 18 consecutive quarters. I predict that it will continue to be a large focus as more of these devices become more connected.
Steve Harvey, VP of Stericycle Expert Solutions


For an industry whose mission is saving and improving lives, this must be resolved if the medical devices industry is to maintain the trust of those who use and ultimately benefit from its products. Additionally, recalls as a result of design and software failures are known to have significant market impacts. The automotive industry knows this only too well, which is why it has long embraced the concepts of simulation and model-based design in product and software design. Now, the medical devices industry is ripe and ready to transform and benefit in similar ways.
What is model-based design?
Let’s briefly recap on model-based design (MBD) before going any further. In its simplest form, MBD is a mathematical and visual method for designing complex systems that involve controls, signal processing and communications.
It is an approach that Siemens has applied in numerous fields to enable products to be brought to market faster, more cost-effectively and with higher reliability. Key to the MBD approach here at Siemens is the simulation environment that Simcenter provides, to deliver integrated simulation and testing.

But MBD is not limited simply to mechanical engineering; we also apply this methodology to develop the software that increasingly controls the products that are under development in today’s connected and highly digitized world. Our MBD approach encompasses open-loop and closed-loop simulation and testing across the development lifecycle, from Model-in-the-Loop (MiL) through to Software-in-the-Loop (SiL) and Hardware-In-the-Loop (HiL).
How can model-based design be applied to the medical devices industry to improve software quality for medical devices?

Imagine an ICU hospital bed. The patient in that bed and their medical caregivers are relying on a thermal management system to regulate that vulnerable patient’s temperature. The bed and the thermal system are actually two devices working together, both encompassing mechanical and electrical components, hydraulics and circuit boards to deliver the right level of heat to the patient. The margin for error is low; the potential for problems with any one of the constituent parts is considerably higher.
Software is the digital brain of the whole system, enabling the hardware to do its job in an effective and reliable way. Software can also deliver additional functionalities and benefits, such as load sensors to determine the weight of the patient without requiring them to move. Throw in some additional functionality through digital signal processing (DSP) and it becomes possible to determine vitals such as heart rate via load signal analysis.
However, these kinds of possibilities do not come to life by chance. We see much trial and error in the medical devices industry when it comes to developing software and controls, along with costly and slow-to-develop prototypes. But as proponents of MBD, we know that there is another way. To make software as robust as it can be, and to develop it and bring it to market alongside the hardware it drives as quickly and cost-effectively as the market demands, MBD can bring undeniable value and significantly improve software quality for medical devices.

Our MBD approach for software development is rigorous and meets ISO standards for functional safety. Siemens’ Polarion, an asset lifecycle management solution, has been successfully leveraged by several medical device companies to set up an orchestrated workflow and a systematic approach to development. The level of traceability it offers is especially valuable to the medical devices industry, making it possible to demonstrate to regulators at any point that standards in code testing, risk assessment and more are being met.
Mapping best practices from the automotive field to improve software quality for medical devices
We believe that, especially in fast-evolving fields such as medical devices, the wheel does not need to be re-invented. Some clear parallels can be drawn between functionalities and system requirements in automotive and medical devices. As the more mature industry, automotive can offer some tried-and-tested approaches that would work to develop new solutions and improve software quality for medical devices.

Let’s go back to that ICU bed, for example. Thermal models that safely and reliably predict temperatures to allow for them to be accurately controlled are already highly developed and proven in automotive in the form of under-hood components and seat ventilation, using CFD and controls.


Another automotive engineering domain that can be leveraged in medical device design is noise and vibration testing. Take the example of a highly complex robotic surgical grasper whose design incorporates hundreds of delicate cables: predicting and managing the effects of noise and vibration on such tools is vital to system performance and ultimately, to avoiding recalls.
Model-based controls that we have applied in automotive can also benefit the design of medical devices like insulin pumps and ventilators. Like automotive, these devices combine software, mechanical, electrical, hydraulic and thermal components. Adapting tried-and-tested simulation models to predict elements such as pressure and flow under multiple conditions could enable these kinds of medical devices to be developed, improved and put to use far more quickly than before.
What’s possible for the medical devices industry with MBD?
In short, MBD and simulation can significantly improve software quality for medical devices and help accelerate product development.
A tool like a surgical stapler might cost around $5,000 to prototype. Yet in a standard prototype-test-and-iterate approach, more than thirty such prototypes would be needed across the development lifecycle, in order to get the necessary statistical variants and meet quality standards for each test group. What if you have fifteen types of tools or develop? That’s when prototyping runs into the millions of dollars and development time to match.
A model-based approach not only assures software and product development quality, but also embraces simulation and co-simulations with hardware components earlier in the process. The result is better productivity and quality. We also know that MBD approaches can even negate the need for animal testing in certain devices, and a reduced need for human testing in clinical trials, thanks to sophisticated simulation.
The FDA appears to agree that MBD not only has much to offer the medical devices industry, but that it is now a preferred route to software and product development. It has stated:
Historically, software safety has been focused on the software development and system-level testing… in recent years the focus of the software engineering community has shifted from the traditional “design-test-fix” to a model based approach… the FDA has recognized that if product developers had tools that enable them to examine and evaluate software earlier in the development cycle, then there would be a greater likelihood that the resulting software would be more robust.
Infusion Pump Safety Research at FDA
Learn more about how Siemens can help you improve software quality for medical devices:
To learn more about how Simcenter Engineering and Consulting Services can help you to accelerate and improve software quality for medical devices, please contact Ammon Wright.
If you’d like to learn more about Simcenter solutions for medical device design and development, watch our on-demand webinar.
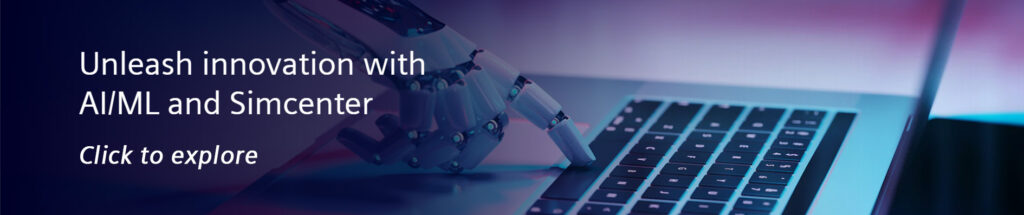