Meet marine regulations … no matter the weather!
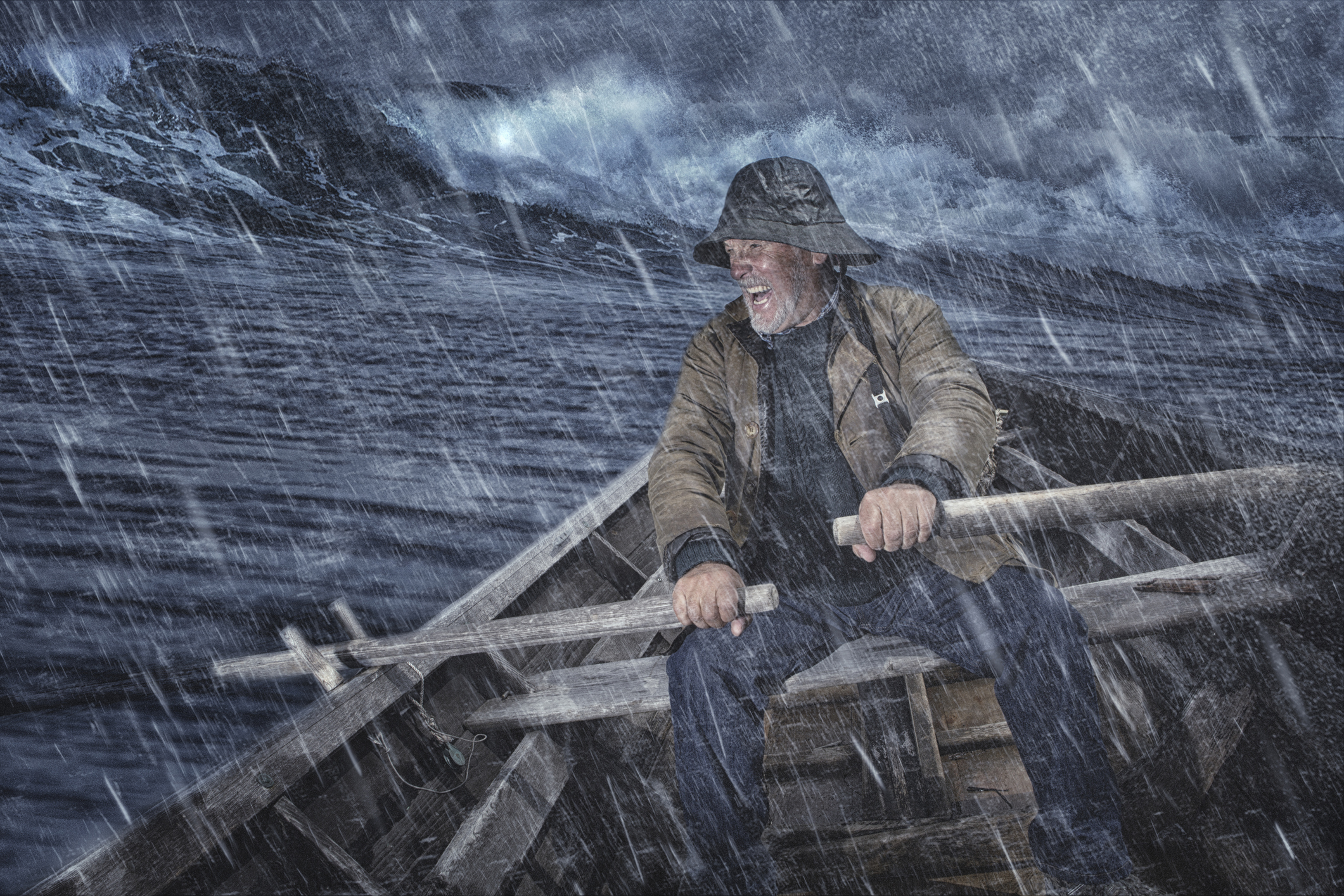
Climate change is a challenge looming over human life and ecosystems. Now, the maritime industry faces new challenges to reduce its carbon footprint. Everyone in this industry must comply with International Maritime Organization (IMO) marine regulations. These regulations are increasingly targeted at drastically reducing carbon emissions. To help the industry design innovative vessels, Siemens with its Simcenter portfolio, provides tools that will help you meet IMO regulations.
In this post, we will focus on Simcenter Amesim. Learn how it can help you to make informed design choices. See how to model a vessel and use it to evaluate fuel consumption and greenhouse gas (GHG) emissions in realistic weather conditions.
Simcenter Amesim provides you with all the tools to easily create your vessel model using different kinds of propulsion architecture from standard diesel propulsion to a hybrid one.
To showcase these Simcenter Amesim capabilities we will use a hybrid offshore construction vessel operating in Norway.
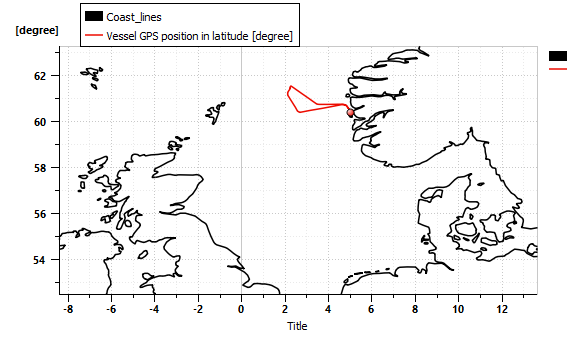
In Simcenter Amesim it is possible to simulate the mission profile of your vessel in representative weather conditions. You will see where the current, wind, wave, and even water temperature and salinity variation will impact the hull resistance.
To easily set up these simulations with representative mission profiles, we provide a series of different routes for different types of vessels from offshore construction vessels to tankers. There is a total of 13 routes. Each of these has a different level of weather condition: good, medium, and bad.
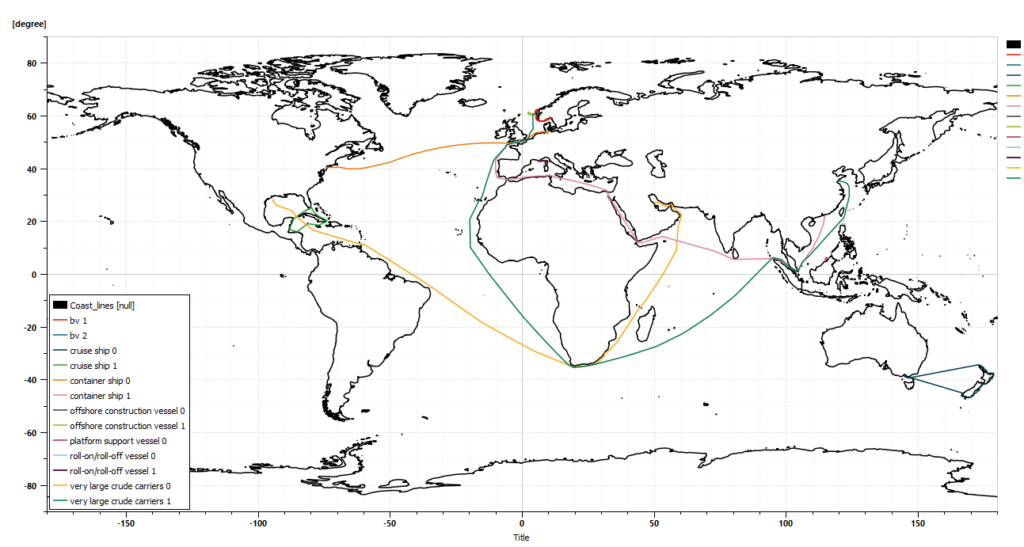
To create these routes, we have requested the expertise of OSE Engineering. OSE Engineering specializes in data analysis, algorithms development, and IA solutions for the marine industry. They have inferred these routes from a combination of historical worldwide maritime datasets and past weather information.
Expertize from OSE Engineering
For each given vessel type, they used advanced clustering techniques to identify the most common routes and re-simulated at various times. They then statistically sampled these numerous simulations to obtain spatial, speed and weather representative routes.
In our example, we will focus on the OCV operating in Norway. This post explains how to build a Simcenter Amesim model of a hybrid propulsion. We will use a peak shaving energy management strategy, where the focus is set on fuel consumption and CO2 emissions in realistic operation conditions.
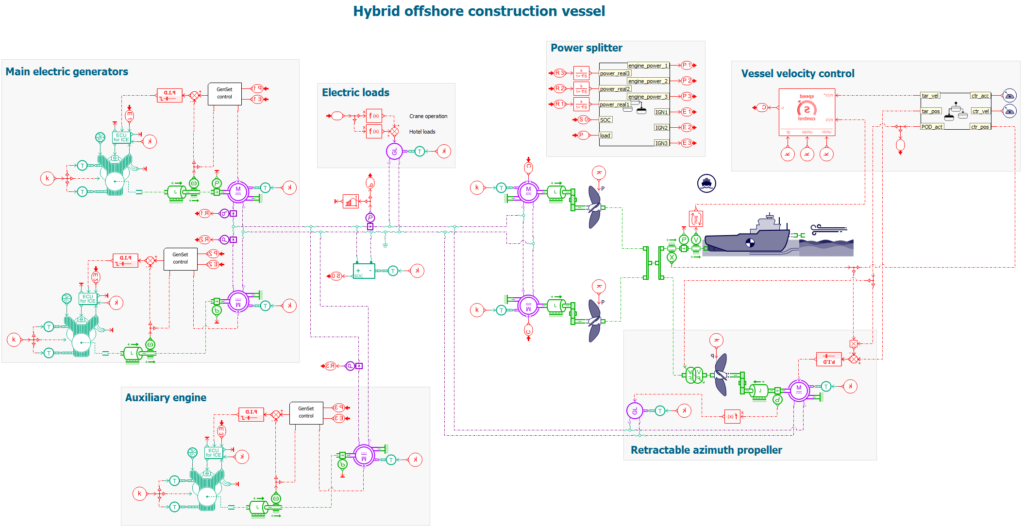
Vessel velocity control
The vessel mission profile alternates travel and dynamic positioning phases.
The 2 main propellers propel the vessel during travel phases. At dynamic positioning, a retractable azimuth propeller is activated to better stabilize the vessel.
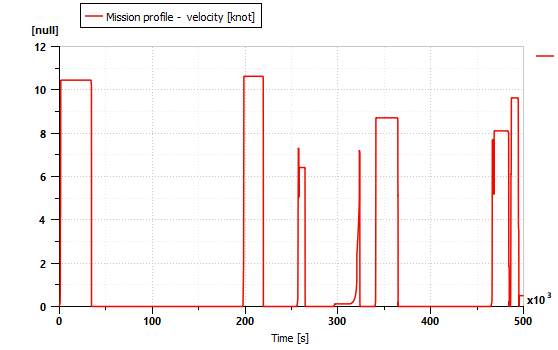
When in the travel phase the control is done by the motion controller submodel of the signal library. This submodel is dedicated to controlling moving masses with dry viscous friction. This better fits the dynamics of a vessel than what a PID can do. It especially provides better results during slowdown and low-speed phases.
As for the dynamic positioning phases a PID is sufficient to control the azimuth propeller and to stabilize the vessel, as the target velocity is zero.
Finally, a statechart is used to supervise the switch between the travel and dynamic positioning phases.
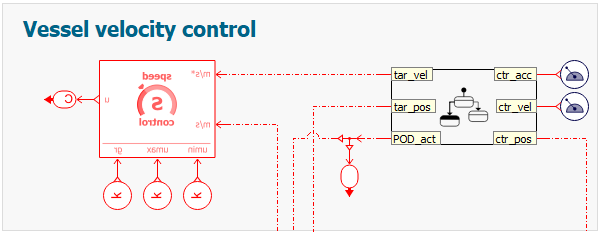
Power management strategy
This model uses the “peak shaving” power management strategy. The GenSets are used at constant rotary velocity and a power splitter manages which engines are started or stopped depending on the battery state of charge and requested power.
The power management strategy presented in this demo follows these rules:
- The battery SOC is always kept between 80 and 20%
- To preserve the battery lifespan, the charge/discharge cycles are kept to a minimum
- The GenSets are started only when the power request goes beyond the maximum power the first GenSet can provide
- Engines rotation speed is always kept at 1800 rpm for maximum efficiency
OCV operating missing under realistic weather conditions
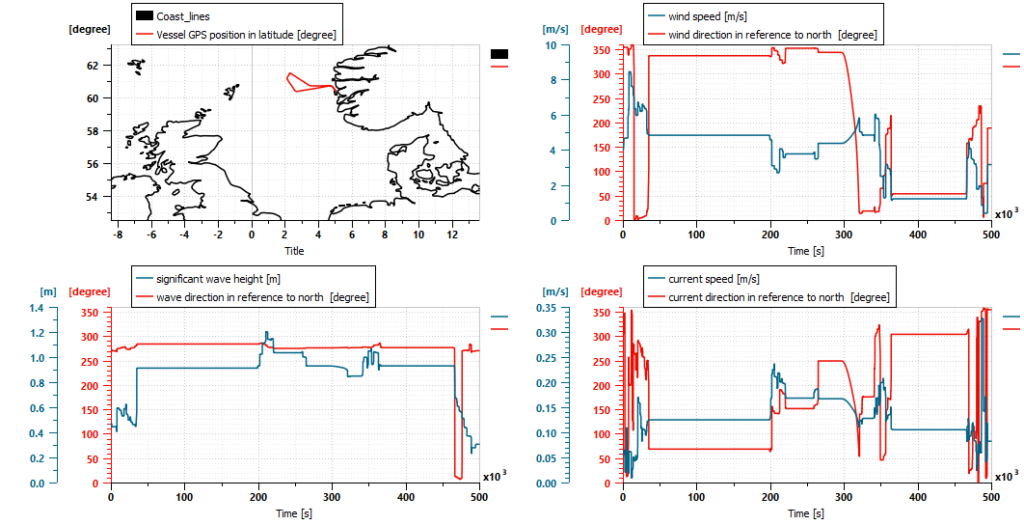
The above plots represent the vessel position on the route, as well as the wind, wave, and current properties at each vessel position. The weather conditions are variable during the simulation.
Then these weather conditions are translated into additional hull resistances:
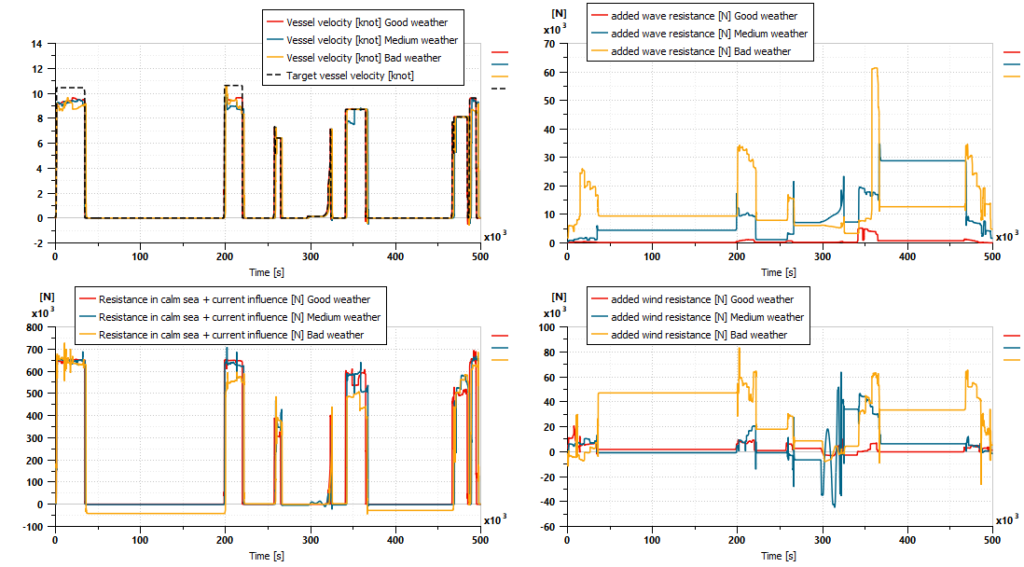
The top right and bottom plots represent the added wave and wind resistance, as well as the calm sea resistance with the current influence.
The top left plot is the vessel velocity (full lines) and the targeted vessel velocity (dot line). When the target velocity is maximum, the vessel is not able to reach that speed, especially under bad weather conditions.
Finally, we can note that the added resistance is sometimes negative. This happens when the wind, wave or current are behind the vessel.
Power management strategy
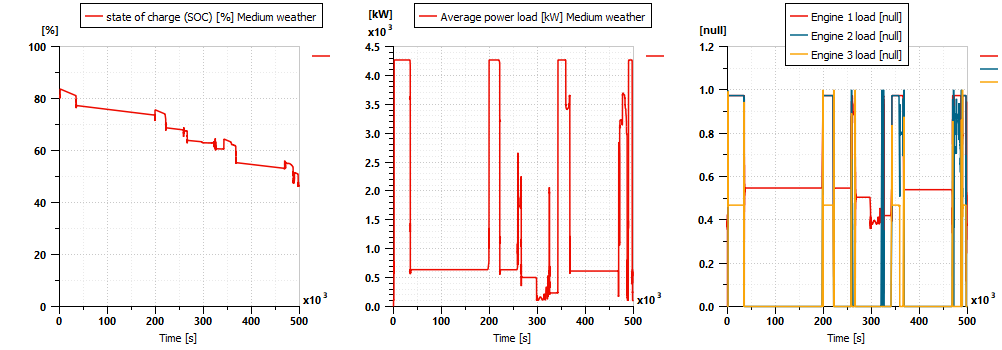
The power management strategy’s purpose is to activate and deactivate the engines, depending on the power load requested. The battery serves the role of a power buffer between the generated and consumed power. Therefore allowing the engines to operate at the highest efficiency possible.
The left plot shows the battery state of charge, is slowly decreasing during the mission. We would expect to see this as the PMS purpose is also to avoid having too many charge/discharge cycles to protect the battery lifespan.
The middle and right plots show the power requested and engine loads. During travel phases at high speed, engines 1 and 2 are at full capacity. The third one is at half its capacity. But during dynamic positioning phases, only the first engine is used. The other ones are stopped as the power requested is lower.
Total fuel consumption and CO2 emissions
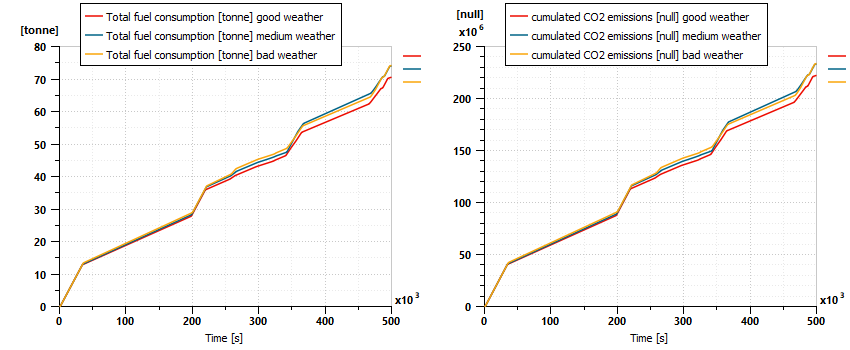
Finally, the total fuel consumption and CO2 emissions can be evaluated. As expected they are lower for the good weather case.
To go further with the model, it would be possible to optimize the PMS (power management strategy). Eg. to reduce the energy consumption even further, find the best engines, electric motor, battery, and propellers design. Resulting in the main subsystems of the vessel operating at the best possible efficiency, during a representative mission profile.
Conclusion
Simcenter Amesim provides all the tools necessary to optimize vessel design on a complex operating profile, associating cruise and dynamic positioning phases, taking into account the weather conditions and the power consumed by the different consumers of the vessel: propulsion, hotel loads, and crane operation.
Check out this short demo video:
Learn more
Read this blog post to learn more about the new capabilities of the Simcenter System Simulation release 2022.1.
About the author:
Valérian SIMONIN is a system simulation marine application specialist. He has been working in system simulation for more than 10 years in different industries, first as a customer, then physics developer and now as an application specialist.