Improve your NVH process for an eDrive and its housing in one simulation – that’s e-mag-ical
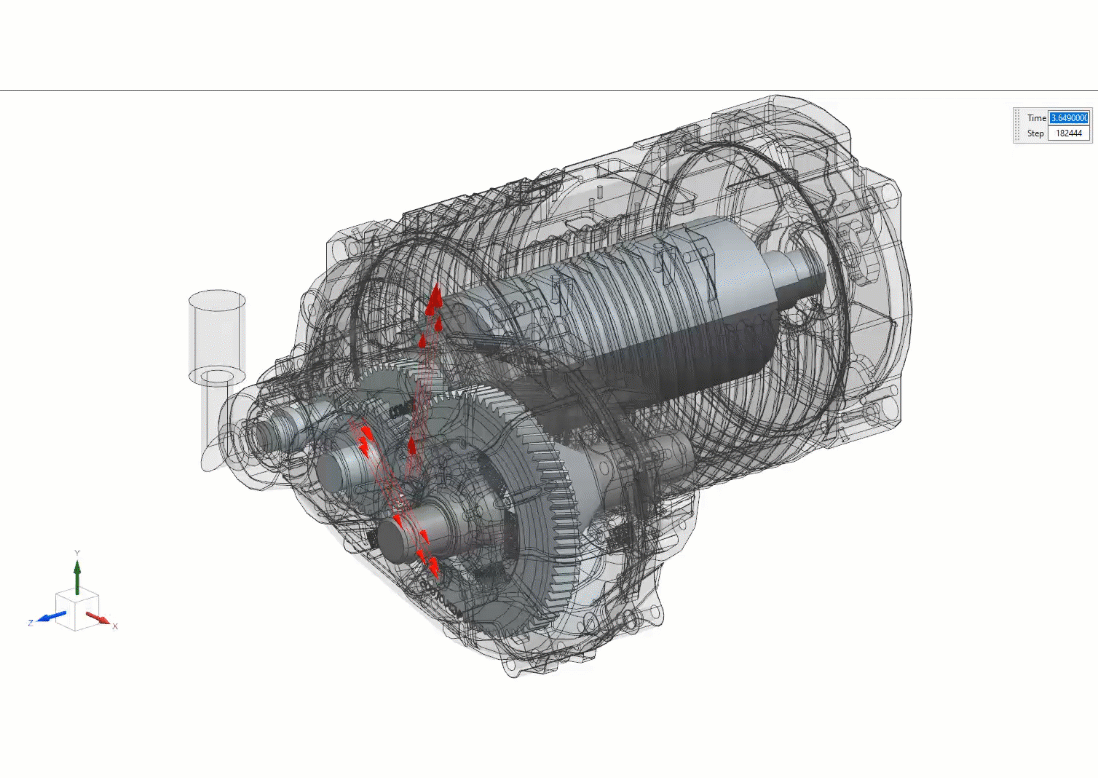
The NVH process used to develop electric powertrains changes the vehicle occupants’ experience and perception of quality. Vibrations have become more important to car manufacturers as the demand for electric vehicles increases and the competition heightens. In the last three years, despite covid reducing the number of people on the roads, electric vehicle sales have tripled. By far the largest Electric Vehicle (EV) market is China, which bought almost as many EVs as the rest of the world combined. In China, the competition between manufacturers is growing fast. Seven different companies manufacture the top ten selling electric cars.

Competition in the EV market
The Wuling Hongguang Mini EV was first released in July 2020 and has already sold over 500,000 units. In just two years, the competition has identified the Wuling Hongguang Mini EV success and released their own models to compete. Competitive models include the Chery QQ Ice Cream, Dongfeng Fengguang MINI EV, and the BAW S3. Not to be outdone, this year Wuling Hongguang will release an update to the Mini EV drivetrain. Therefore, any new competition in this market must be able to design and develop their products quickly to stay relevant.
What is the most desirable category for manufacturers?
The list of top ten EVs sold in China can be split into three categories: Cheap city cars that are circa 4,000 euros, family cars that are between 19 and 25,000 euros, and luxury cars that are in excess of 45,000 euros. If we then add the total sales of each vehicle in these three categories together, we can see that the luxury cars make up the largest contingent, with 498,410 vehicles sold. This figure is slightly higher than the 471,830 cars in the cheap city car category. The high sales and valuations are attracting the attention of many manufacturers looking for a return on the high costs of EV development.

There is no history of what an electric sports car engine should sound like.
Jud Knittel, noise, vibration and harshness (NVH) lead engineer at Karma Automotive
Why the NVH process matters
For many considering the switch to an EV their biggest concern is the car’s range on a single battery charge. For luxury cars that ensure comfort with a long wheelbase, there is much more room for batteries. More batteries can increase the range of the car between charges and significantly reduce range anxiety. A longer range and plenty of high-paying customers make luxury EVs appealing to manufacturers, but not without their own challenges.
High-quality vehicles are either high performance, and the engine sound can be a key selling point, or luxurious for which buyers generally desire silence. Electric motors don’t tend to make a sound, and any sound they could make, a buyer may find undesirable.
Therefore to stay competitive in this rapidly growing competitive part of the market, manufacturers need to pay attention to details.
We work with individual components to keep them from making as much noise as we can, and when they have to make a noise we keep it from being annoying
Jud Knittel, noise, vibration and harshness (NVH) lead engineer at Karma Automotive
A whine is an awful tone
Tonal noise e.g., motor whine and gear whine, is more prominent for an electric drive (e-drive) powertrain in Hybrid Electric Vehicles or EVs, because there is no Internal combustion engine (ICE) to mask it. The source of the motor whine is the motor’s electromagnetic forces. Whereas, as explained in a previous blog, the vibrations that create gear whine result from the gear geometry and the contact behavior between gear teeth. The structural response of the powertrain to these excitations can result in excessive noise that can negatively affect customer satisfaction.
Addressing motor and gear whine requires a deep understanding of the electrical and mechanical systems. Properly capturing relevant effects requires a lot of detailed information. This includes the stiffness of the assembly, EM excitation, gear micro geometry, stiffness of light weighted gears, bearing clearances, bearing preload, etc. Developing all these areas in unison requires a robust system-level NVH approach. To achieve this some refinement is needed before e-drive models are at the same standard as ICE engines.

End-to-end E-Drive NVH performance engineering: E-mag to Motion to Acoustics in one NVH process
Simcenter 3D now offers a single environment to tackle the complete eDrive NVH process. The new environment considers the mechanical excitations and the coupled EM excitations. You can find some more info on this process in a separate blog.
In a nutshell, Simcenter Motorsolve calculates the electromagnetic loads generated by an electric motor as a function of the operating conditions, i.e., external load and rotation speed. We can consider the net effect of those loads on the rotor as torque. However, distributed loads acting on the stator affect the structure’s dynamic behavior, contributing to its vibrations and the noise generated. Adding these contributions to the mechanism’s simulation increases the accuracy of the predicted behavior of the vibrations and corresponding noise. In three easy steps, you can add the calculated electromagnets loads to a Simcenter 3D Motion simulation.
Engineers can investigate why noise occurs
In the previous blog, we met Dave, the NVH CAE Engineer, when he used the latest updates in Simcenter 3D to listen to his simulations and discover what his Powertrain program manager meant when she said, “it doesn’t sound right.” Now that he knows where the noise is coming from, he can investigate why it occurs and fix it.
First, he looks at the high-level overview of the eDrive NVH process in Simcenter 3D:


Time to simulate
The Starting points are the structural FE simulation in Simcenter 3D and the electromagnetic FE simulation in MotorSolve.
- The structural FE simulation calculates the modal database used in Simcenter Motion to consider the housing’s structural compliance and dynamic behavior.
- The EM simulation results in time domain forces on the stator teeth for different RPM.
Next, he extrudes these forces from 2D to 3D and maps them to the structural model. This step is required because the EM FE and structural FE models are typically different.

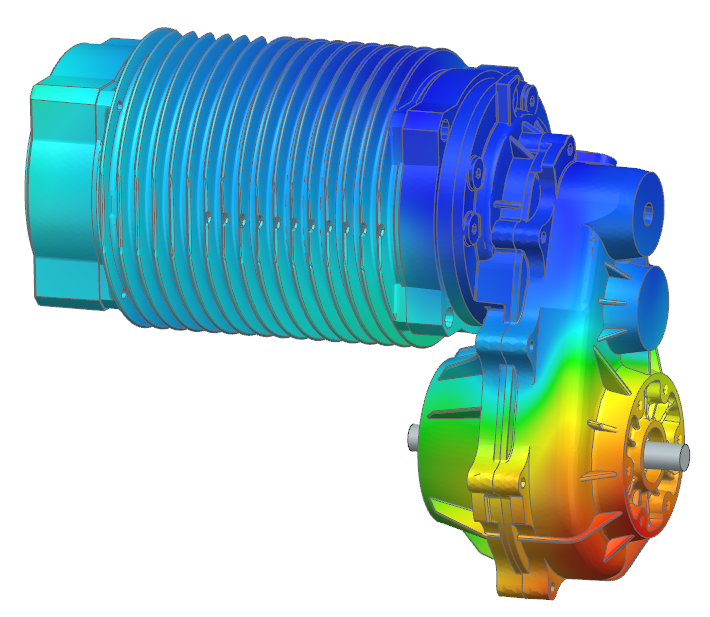
Due to past experience, Dave reaches the next step with apprehension. He knows that applying the time domain forces directly to the flexible stator teeth can be laborious. Therefore, he logs in to Siemens Support Center, to look for recent updates that improve the process, and finds exactly what he needs. The new force element (Electromagnetic Force) in the Simcenter 3D Motion application allows him to apply these time domain forces directly to the flexible stator teeth in the Motion model. With this method, the solver will interpolate for the correct loads depending on the rotor angle and rotor RPM. Once the Motion solution is completed, the modal participation factors of the flexible stator available in the Motion results contain the structural response considering both EM and mechanical excitations. He can then use this as the input for the vibroacoustic simulation in Acoustics.
Conclusion – how to improve your NVH process
Simcenter 3D users have a new, complete eDrive NVH process. The new process starts from the calculated electromagnetic forces generated by the electric motor. These calculated forces and their effects can now be included in a detailed simulation of the entire mechanism’s dynamic behavior. This simulation includes noise due to the vibrations of the motor housing and makes predictions with higher accuracy.
Upcoming events
The NVH team has recently had their eDrive NVH paper accepted by the panel of the NAFEMS Iberia conference, which they will be presenting. More information on the event can be found here.