Re-think Lithium-ion battery cell design now – with 3D high fidelity simulation
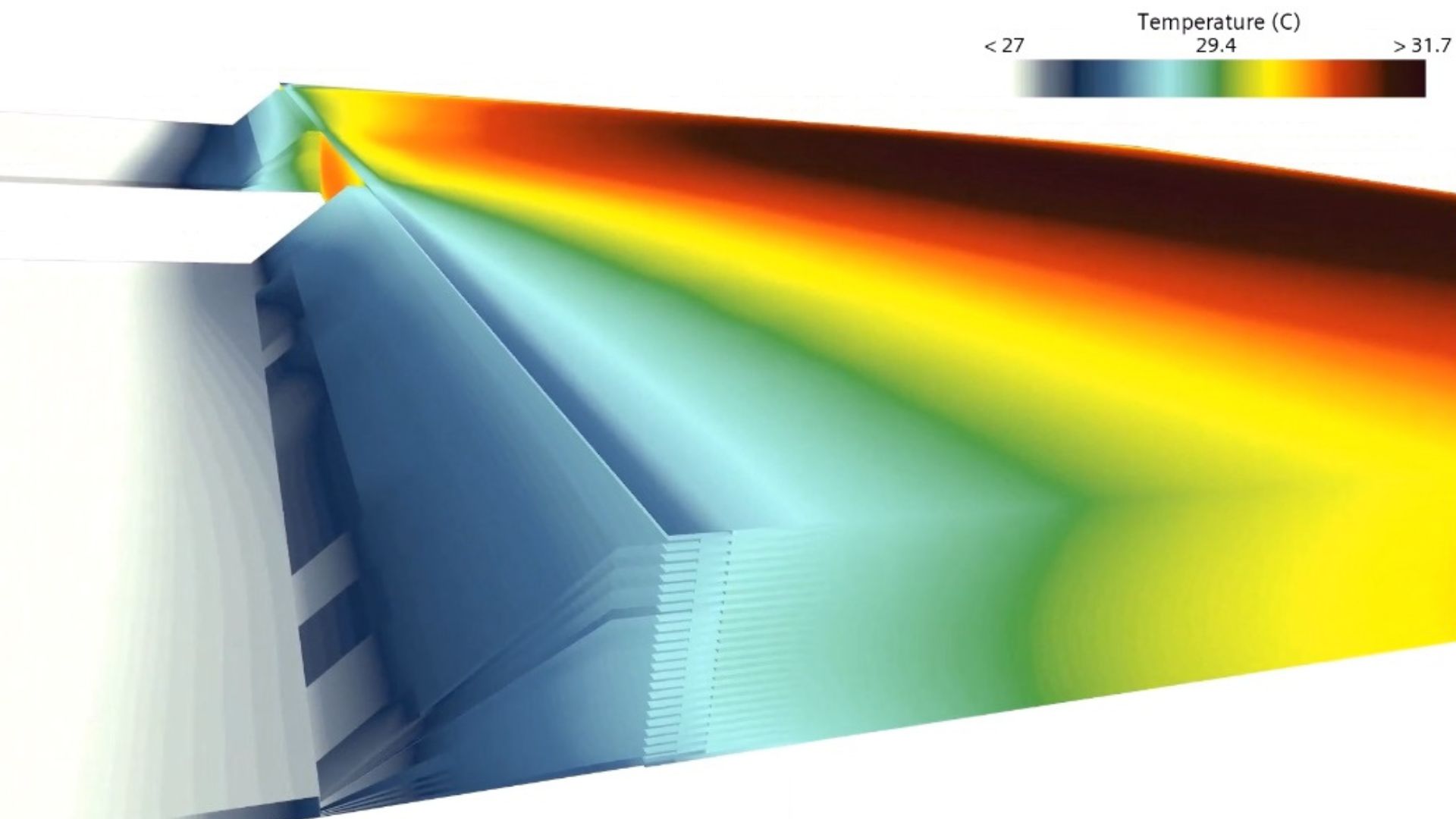
Throwback battery packs
California, USA. 1999. In the motherland of Apple, mobile phones are still a black brick with a lot of battery for a bit of display; e-scooters and bicycles are human-powered and the battery in a car contains lead – not Li – and serves the sole purpose of starting the vehicle and operate a few auxiliaries. An electrified transport sector? Science fiction – even in the motherland of Tesla. Battery cell design? A topic for the consumer electronics industry.


And yet, California 1999 is also where and when a company named Battery Design LLC decides to create a piece of software that enables engineers design better batteries for longer lasting operation. The first lines of code of what should later become Simcenter Battery Design Studio (BDS) say hello to the world. At the time BDS is the very first cell design software with a dedicated interface to support cell designers through geometrical definition of a Lithium-Ion cell and a coupling to a Pseudo-2D (P2D) physics-based model. The very first releases were even distributed as a freeware. As it developed, this innovative solution was providing to cell designers the first virtual testing lab, predicting cell behavior while accelerating development time and reducing prototyping cost.
At the time Lithium-ion was very much a technology for the consumer electronics market and over the last decades virtual tools like BDS transformed the clunky black bricks with a bit of display of 1999 into incredibly powerful revolutionary gadgets in your pocket.
Batteries, go big to go home
But 24 years forward, and many more revolutionary consumer electronics devices later, is also when the battery world is still facing the consequences of another – much bigger – revolution: Suddenly batteries in a car shall no longer just start it. They shall move it. The era of vehicle electrification is here: Scooters, Bicycles, Cars, Trains, Airplanes, Ships… all want batteries.
And so, other than in 1999, engineers are no longer only forced to tackle those small battery packs for your pocket device. Now, engineers need to come up with reliable, long lasting, powerful and safe battery packs at a scale that is orders of magnitudes bigger – in all regards. Range is the new currency and investors want a lot of range- at zero risk. A significant engineering challenge.


But it seems there is not too much choice. As a result of a global climate change awareness, different measures, good or bad, have been taken to tackle the human CO2 net emissions. And vehicle electrification -while surely not the silver bullet – is one of them in an attempt to reduce the CO2 footprint coming from ground transportation, which represents ~20% of the global CO2 emissions.
Batteries, the new heart of vehicles
To support vehicle electrification revolution, cell design has become a massively growing market, to produce cheaper, safer cells, with longer life expectancy and higher range lithium-ion battery. The battery has become the heart of the electrified vehicle concentrating most of its value and technology innovations. Looking at the Lithium-ion cell energy density evolution since the 90’s, the graph below shows the effort put in place to accelerate on this key performance from 2015 onward.

Cell makers and car makers have invested billions of dollars in R&D and production to support this new demand. New start-ups have emerged in a bid to capture this large market with rapid growth and they’re coming with new innovative products, whether they are cells or cars. The “traditional” car makers are adapting to this new market and even reinventing themselves in a bid to retain their competitiveness and profitability. This leads all these players to seek new approaches in accelerating and improving their new products, while ensuring a good profitability in this time of global inflation.
One way has been simulation, and the reliance on it, to displace some, but not all, time and money consuming lab activities, and it is rapidly growing. But as vehicle electrification poses a massive disruption to the battery sector, the tools to design those need to keep up through their very own disruptive transformation.
Battery cell design: a three-dimensional challenge
Sure, tools like Simcenter Battery Design Studio have been part of this design process digitalization, for years, helping improving designs, but the increasing quest for better performances lead the cell designers to want and need more insights into their products. Their demand translated into a requirement for a high-fidelity cell design simulation solution, beyond the traditional offering, now accounting for 3D geometries and offering detailed and local behaviour of a cell response to a duty cycle.


Deep insights with new 3D battery cell design capability
And so this October 2023, 24 years after BDS said “Hello world”, Simcenter simulation solutions will strengthen its portfolio with a new 3D battery cell design capability, built within Simcenter STAR-CCM+, which will support high-fidelity 3D battery cell design simulations.
The solution is based on a template simulation file, which translates into an elaborated but finely prepared and customized pre-setup simulation file, that the user can immediately use and run. Also, as with simulation templates, these are simulation examples, and the user is free to edit the template to further customize it to their needs.
The first unique feature of this capability is the ability to design Lithium-ion cells in full 3D, which means geometrically resolved electrode layers, separators and tabs. It is entirely parametric making it easy to control over design explorations studies.

It also provides a high accuracy model with 3D solution of the electrochemical behaviour of the cell, thanks to an enhanced physics-based model from the initial Newman-Doyle-Fuller formulation. The model framework uses our unique phasic-porous media approach to solve for the 3D diffusion and migration of the charged species, as well as the charge transfer from the solid to the liquid phases and vice-versa.

The workflow within the template leverages existing and new automation features, for a customized, automated and tailored workflow for cell designers. It is the first time we build a solution on the powerful new automation feature called “Stages”, coming in Simcenter STAR-CCM+ 2310. The all new Stages enable you to handle multiple physics setups in a single simulation. In the context of cell design simulations, they allow for a seamless setup for Constant Current to Constant Voltage simulation, automatically switching the current boundary condition to a potential one. For more details stay tuned for a dedicated blog on new automation capabilities.
The 3D cell design template also provides industry-standard terminology and units and a useful cell specifications report to quickly review them against the user’s requirements. Currently three cell shapes can be observed as the industry standards: stack, cylindrical or prismatic wound. With Simcenter STAR-CCM+ 2310 release, the stack cell shape simulation template will be available and the other two are in the pipeline.


The 3D cell design capability has a simplified mesh setup with a few inputs and clicks, which makes its usage very accessible even for cell designers not familiar with CAE solutions and meshing tasks.

It also supports dedicated industry-standard post-processing to facilitate its access and let the user focus on the results analysis and spend little time on its setup.

Towards greater insights
With this in place, you get access to detailed insights of the cell performance like in-plane and through thickness 3D concentration distributions for the solid and liquid phases. But not only, many more electrical and electrochemical quantities 3D distributions can be reviewed on a cell model. You have then the unique benefit of understanding local and edge effects, which may be critical in situations of aging, fast-charge and other constraining duty cycles.
Overall, it truly provides a modern 3D validation and verification tool for cell designers seeking for improving and optimizing to the limits their Lithium-ion cells products to pursue innovation.
Needless to say, that since it is a fully integrated capability within Simcenter STAR-CCM+, it benefits from all its ancillary tools and solutions, such has HPC capability, automation, design exploration, CAD import/export and many more.
Hop on the 3D cell design train

As an example, let us here present a pouch cell design, detailed in this article, presenting a stack cell design for battery-powered electric trains. Such battery cells are typically used in electrified trains similar to the Siemens Miero shown above.
The cell is a 50Ah pouch cell with NMC (4,4,2) cathode and a graphitic anode.
Thanks to the templated geometry approach the cell is quickly entirely re-designed in our 3D cell design capability, and with automation and dedicated cell design inputs in place, quickly executed on the same article’s duty cycle to simulate its behaviour.


For the mesh, approximately 1 Million Finite Volume elements where generated, sufficient to capture the in-plane and through the thickness gradients.




The cell is tested under a 2C constant current discharge over a short period to capture some initial response of the cell in terms of temperature and concentration evolutions.
Temperature gradients across the cell is slowly building up and we can appreciate the gradient evolution through all the layers in the thickness direction. The 3D cell design capability truly allows for the study of surface or tabs cooling and capture the real behaviour.

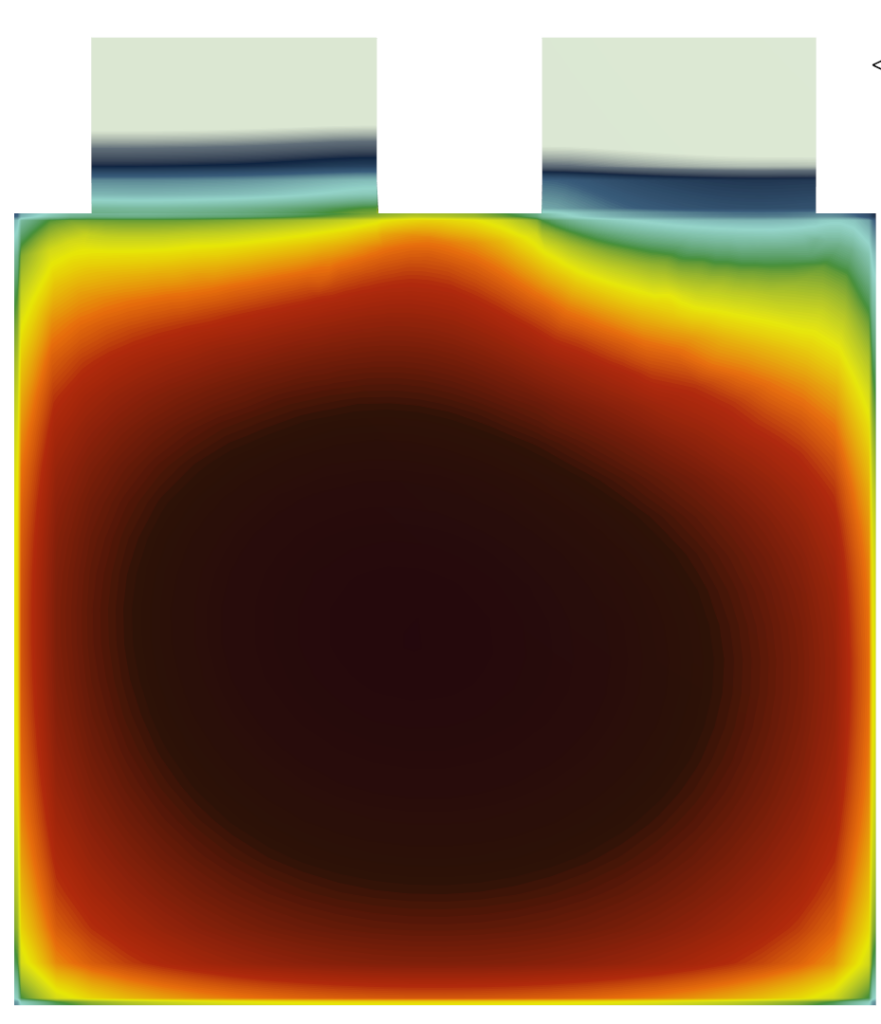

Also, we looked at the concentration evolution in the electrolyte, one can plot for the concentration across each electrode thickness thanks to our dedicated plotting tool.

One can also look at individual layers to single it out and plot the solid concentration distribution in 3D. Although the minimum and maximum values are close, one can see the gradients building up.

Finally, with the embedded battery cell design capability one can easily asses the electric current within the cell.
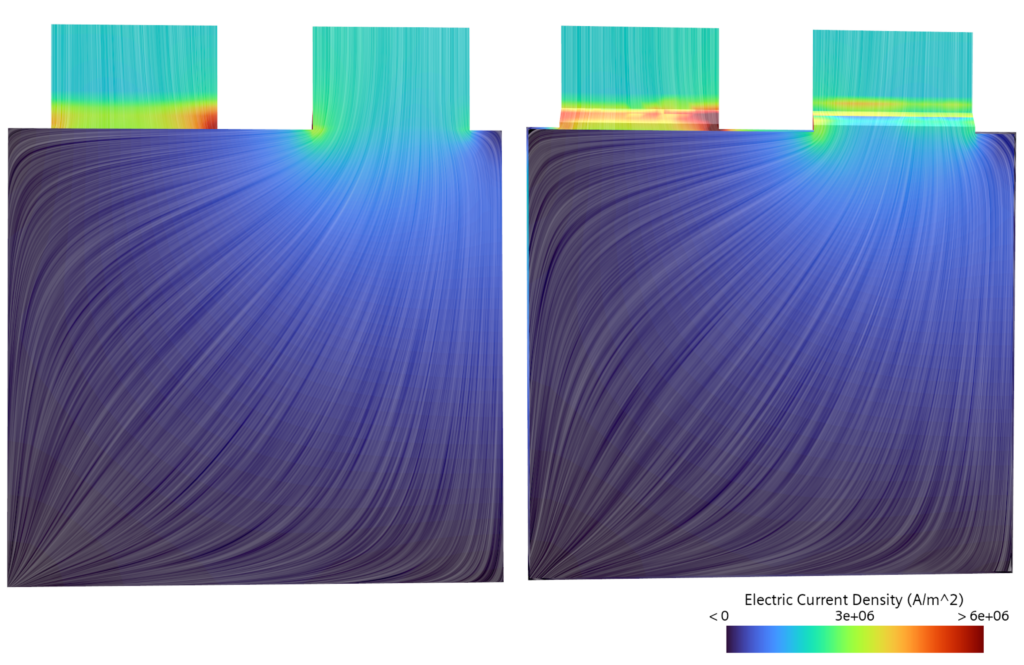
Overall the cell is responding well to the initial duty cycle and we will come back with more validation results in a future blog.
A comprehensive cell design set of solutions
Through the Batteries add-on license the new 3D cell design capability will add one more additional asset to your battery design and cell performance solutions. Simcenter Battery Design Studio, the powerful tool used for fast screening analysis, is now complemented with a verification and validation capability in Simcenter STAR-CCM+ as presented above. If offers a powerful set of tools for cell designers to help them in innovating with new products. The cell-centric view also supplements larger battery pack thermal analysis to asses battery cooling and thermal runaway and complements our performance models capabilities for battery system integration offered by our solution Simcenter Amesim and the molecular dynamics capabiltites of Simcenter Culgi.
So if you want to design better stack cells faster, visit the download section of the Support Center on October 25 and grab your cell template file.