Set sail for your transformative journey into a green marine future
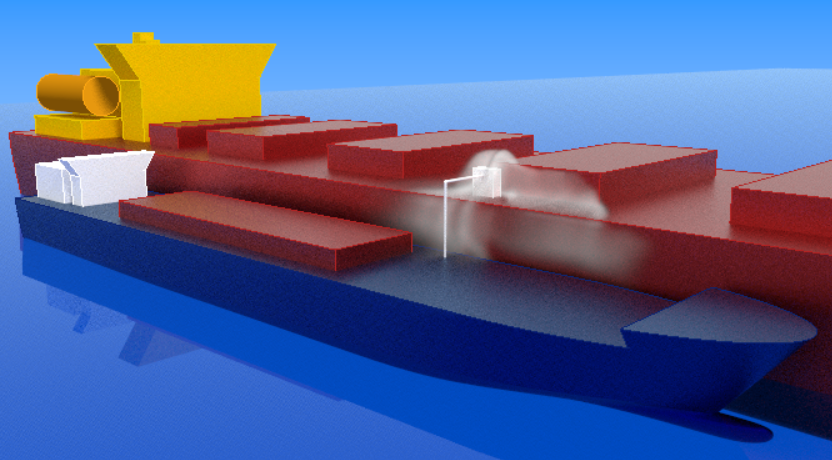
Earlier this year, the International Maritime Organization (IMO) set ambitious targets for achieving a green marine industry and net-zero emissions by 2050, a drastic acceleration from the previous goal of 2100 (see more details here). The industry has been sailing heavy seas since, with widespread implications on ship life-cycle management, from concept design to live operation and decommissioning. Most industry stakeholders have foreseen this development, having observed the sequence of progressively stricter environmental regulations.

During the Clean Energy Action Forum 2022 American Bureau of Shipping (ABS) CEO and President Chris Wiernicki outlined so-called credible fuel pathways, which will be the key driver in ship operators’ selection of new fuel types to meet zero-carbon goals. The technology readiness timeline is at the core of decision-making, which can be broken down into a short-, mid-, and long-term period. According to Wiernicki such readiness is given if the following four pillars can be established:
- A solid business case
- Scalability
- Provision and usage of certifiable data
- Mitigation of unintended consequences
Short-term solutions for a green marine industry
Short-term solutions are Liquified Natural Gas (LNG), methanol, and first- and second-generation drop-in biofuels. According to Clarksons, 4.1% of the world’s trading fleet can use LNG as a fuel. This accounts for 91% of the total alternative fuel-capable portion of the fleet. Further, the dominance of LNG is reflected in the current order books, with 33.3% opting for LNG, followed by Liquified Petroleum Gas (LPG) wit 2.3%, methanol (1.2%), ethane (0.3%), and hydrogen (<0.3%). Orders combining LNG with ‘ammonia-ready’ option make up to 10% of such orders. The main incentive for drop-in biofuels is that the existing fuel infrastructure requires little to no adjustments. For smaller, short-sea, and coastal vessels, adequate battery solutions are already available, and successful prototypes of fully-electric and autonomous vessels can be referenced.

Mid-term solutions
The mid-term period will see further advance of methanol, with ammonia on the rise as compatible engines will become more available in the next two years.
Long-term projection
Long-term, green fuels (fuel produced from biomass sources through various biological, thermal, and chemical processes) will be available along with blue hydrogen, i.e., hydrogen produced from natural gas and supported by carbon capture and storage (CCS). CCS technology readiness is crucial both onboard and onshore. Classification societies are leading the assessment of nuclear powering as an option for large commercial ships which can accommodate the technology. A critical pilot study has just been published.
Simcenter simulation chain – setting sail
Each stage of the net-zero journey comes with distinct engineering challenges for ship operation; to name a few:
- Gas dispersion
- After-treatment
- Sloshing in tanks
- Tank boil-off (the process of undesired temperature rise in tanks compromising the cryogenic state of the gas).
- After-treatment for emission reduction and removal (scrubbers)
- Leaks of cryogenic gas during bunkering (the process of refueling)
- Voyage planning – generation fuel and emission profiles
The multi-physics capabilities of Simcenter STAR-CCM+ for hybrid multiphase modeling are being leveraged to provide simulation-based predictions for these problems both in concept design and forensic analysis.


At a higher systems level Simcenter Amesim enables analysis of engine and propulsion configurations with various levels of detail and fidelity, extending all the way into voyage planning, fuel consumption, and emission profiles.

The first coastal ships are already sailing fully-electric while the boating industry has started to embark on its electrification mission. Simcenter Amesim, Simcenter Motorsolve, and Simcenter STAR-CCM+ offer many templated solutions to consider battery pack sizing drive train design or help prevent thermal runaway.

Big ships, zero emissions, green marine solutions
Circling back to larger ships and the workhorses of global trade, we want to focus on how simulation technology from the Simcenter suite is aiding engineers in addressing the short- and mid-term solutions for alternative fuels. Among the four pillars of viable fuel pathways, when it comes to ammonia, mitigation of unintended consequences must be addressed early on in the implementation.
LNG and ammonia are stored in cryogenic state, which means that any exposure to environmental conditions, e.g., through leakages during bunkering, will lead to instant vaporization (flash boiling), putting the crew at risk and presenting numerous environmental hazards. Flash boiling of the liquid spray from a pipe leakage into the environment occurs because the ambient pressure is below the liquid fuel’s saturation pressure. Depending on the direction of spray and distance to adjacent structures, rainout of the dispersed vapor cloud can occur: the impingement of remaining liquid droplets from the mostly vaporized spray, then highly flammable.

Case study: Bunkering
Bunkering is a critical operation onboard ships at sea or in port. Successful bunkering requires safely transferring fuel into the ship’s tanks without overflow, spills, or leakage.
Simulation can aid in the very first steps of the bunkering process
At the beginning of the bunkering process stands the voyage planning to determine the amount of fuel to be bunkered. Simcenter Amesim’s marine library allows you to plug your engine and drive train model into the voyage and maneuvering simulation environment considering hotel loads, auxiliary engine fuel consumption, wind, waves, and current effects on powering characteristics.



After the amount of fuel, including reserves to be bunkered, has been determined, the planning of which tanks will receive the fuel commences. Here, a model of the tanks, piping and valves, ballast system, and fuel intake through the bunkering itself is instrumental to performance prediction and monitoring, and ensuring the ship’s desired hydrostatics. These items and action plans for leakages or spills are usually discussed in the pre-bunker conference – which can be digitally supported by fast-time models to obtain quick responses to what-if scenarios.
The key to success
Simcenter Flomaster’s simulation environment allows you to generate result envelopes of different bunkering scenarios but can also serve you upstream in the design phase to dimension the pumps and lines to achieve the optimal time for filling, emptying, and sounding of the tanks. Ultimately, rule-critical metrics from the simulation can automatically be fed to the oil record book in compliance with Annex I of MARPOL.

Avoid potential system failures and hazards
We are now primarily interested in potential system failures and hazards to crew and environment. Our templates can be set up to yield explicit responses for relevant regulations, e.g., IMO IGC and IGF codes for LNG. LNG is usually stored at around -162◦ C and poses both cryogenic hazards like frostbites and burns to human skin and fire and explosion risk when transitioning to a gaseous state within the flammable range. For ammonia, skin burns, irritation, and inflammation of the respiratory system and eyes can occur for the crew. High airborne concentrations of gas, especially in confined spaces, can lead to explosions or fatal outcomes for human life.

Learn how CFD simulation can aid you in analyzing undesired consequences
To better understand the hazards of spray flash boiling and gas dispersion, we look at the replenishment at sea problem, where we simulate cryogenic ammonia dispersing from a pipe due to a leak during bunkering. Utilizing simulations with Simcenter STAR-CCM+, the complex physics of flash boiling of cryogenic gas dispersion can be studied. Sought-after metrics comprise the extent of the plume, the concentration of ammonia at given point locations, and whether or not rainout will occur. Even though it is unlikely that the workers on deck in fresh air would be exposed to fatal concentration levels exceeding 2000 ppm for 30 minutes or more, stinging or burning sensations in the eyes and respiratory system can occur from exposure to as little as 70 ppm over the same time span, according to the National Institute of Health.
These levels are not unattainable inside closed rooms like engine compartments, which underscores the importance of employing simulation technology for risk assessment and the design of countermeasures.
In our fictitious bunkering scenario, liquid ammonia discharged from a leak horizontally onto the receiving ship’s bunker infrastructure at a pressure of 8 bar, causing rapid dispersion into the environment. Throughout 10 seconds approximately 1 ppm could be metered at point locations typical for work operations. No rainout was detected on deck, i.e., the entire leaked mass transitioned into the gaseous state.
Stay integrated – all hands on deck for a green marine future

We learned about the engineering problems related to green marine targets, ranging from concept design to onboard operation and aiding in generating mandatory documentation. There will certainly be implications of your component or problem-specific studies to fundamental aspects of general ship design. In the likely event of being overwhelmed by the complexity and inter-connectivity of spanning the design space, Simcenter HEEDS will provide nautical waypoints to the port of solutions.
Unveil the ultimate solution: harness your insights for optimal results
The role of Simcenter HEEDS is twofold. For one, its workflow manager acts as the spider in the web of Simcenter CAE tools through around-the-horn I/O mapping and administrating. Moreover, its multi-disciplinary design optimization can be leveraged on the sub-tool, holistic process, or a combination of both. Setting realistic optimization constraints and leveraging Simcenter HEEDS’s powerful post-processing suite to derive the insights that matter will be key for a safe return to port.
Time to anchor
There is an ocean of engineering problems when it comes to the design and operation of ships and floating platforms, and Simcenter has many more tools in store than those mentioned in the blog at hand. Have you ever wondered about passenger safety and comfort for your fast boat? Simcenter Madymo is the lighthouse to follow.
Go full-steam ahead towards your green marine future using integrated performance engineering with Simcenter. Stay tuned as we finalize a forthcoming white paper on CFD simulation solutions for multiphase challenges. Meanwhile, download this white paper, focusing on driving ship design through simulation tools and explore practical insights to enhance your approach to marine projects.
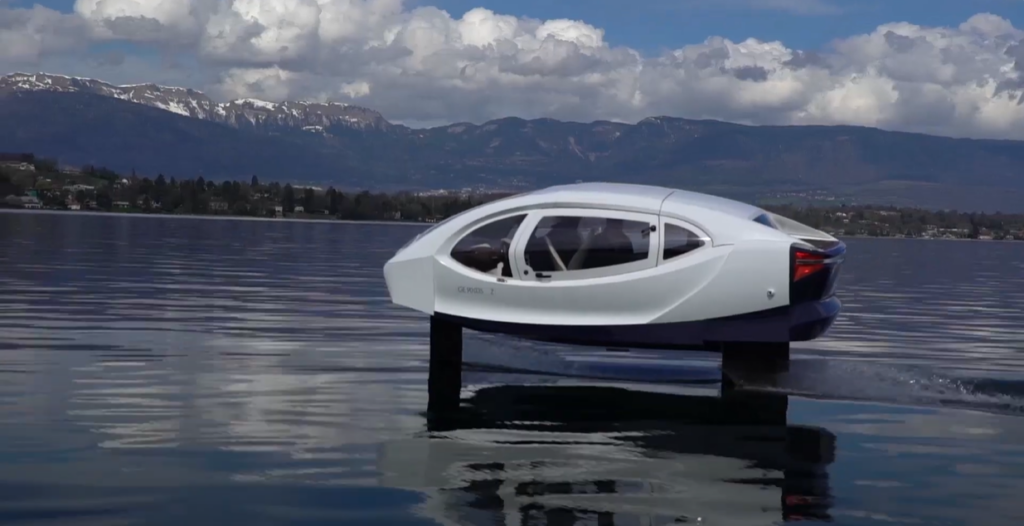
VIDEO CASE STUDY
Caponnetto-Hueber uses Simcenter to navigate digital waters