Simcenter 3D 2019.1: What’s New?
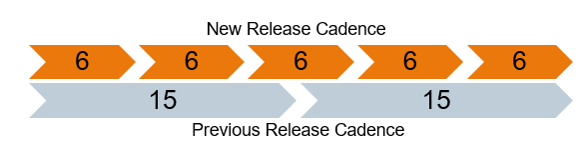
Product development and design are being reinvented to make use of new materials, create lighter shapes, and take advantage of new manufacturing methods. The latest release of Simcenter 3D integrates future technologies for faster modeling, more accurate simulations, and multiphysics integrations to help engineers drive innovation and reduce the effort, cost and time needed to predict product performance.
Simcenter 3D 2019.1 highlights at a glance:
- Simulation for the future through generative design and additive manufacturing process simulation.
- Expanded simulation solutions like transmission simulation that extend Simcenter 3D’s capabilities.
- New ties to the digital thread through synergies with the broader Simcenter portfolio.
- A new path forward for existing LMS Virtual.Lab customers.
Simulation for the future
Manufacturing is changing. New materials and production methods are challenging traditional design and manufacturing limits. With the industrialization of additive manufacturing, you can now design and manufacture new shapes that were never possible before. But how do you generate ideas for these new part shapes and how will you know the as-manufactured part will match the as-designed shape? Simcenter 3D 2019.1 will help you solve both of these problems.
Enhanced topology optimization: Generative engineering with topology optimization lets you use simulation to drive and optimize the shape of a completely new design. For the 2019.1 release, Simcenter 3D’s Topology Optimization is more robust, easier to use, and adds design objectives or constraints for structural integrity of a part when subjected to critical loads including buckling. Resulting designs from topology optimization are lighter weight, yet still strong enough to meet performance requirements. However, topology optimization often leads to unique, organic looking shapes that can be difficult to make with traditional manufacturing methods. Additive manufacturing is an ideal means for producing parts design from topology optimization.
However, the additive manufacturing process fuses layers of metal together with tremendous heat. As the layers build up, residual heat can cause the part to distort inside the printer. This can cause various problems, from structural issues within the part itself, to print stoppage. Issues such as these cause many prints to fail, and make getting a “first-time-right” print very difficult. Simulation of the printing process has the potential to alleviate many of these problems.
New Simcenter 3D Additive Manufacturing process simulation: As industrialization of additive manufacturing accelerates, the need to get a first-time-right print also increases. Simcenter 3D’s new additive manufacturing process simulation solution can help manufacturers achieve a quality print the first time, saving enormous amounts of resources, cost, and time. This solution uses a digital twin of the build tray including parts, support structures, and residual powder to simulate the metal deposition process. This allows industrial manufacturers to adjust the printing process, improving the quality of the final print.
“Using the Simcenter 3D AM Process Simulation solution at toolcraft will allow us to complete our additive manufacturing workflow,” said Christoph Hauck, Managing Director, MBFZ toolcraft GmbH. “Through real-world testing, we have gained confidence that the Siemens’ AM Process Simulation solution will assist us in ensuring quality output from our print process.”
Expanded simulation solutions
Simcenter 3D 2019.1 expands and deepens the level of simulation technology available within the open and scalable simulation environment. Simcenter 3D’s unique simulation environment helps you achieve much faster CAE processes than what can be achieved with traditional CAE tools, and this release expands its simulation footprint to help simulate new solutions that would otherwise be too challenging to complete.
New Simcenter 3D Motion Transmission Builder: Simulating transmission behavior has traditionally been a tedious and error prone process requiring multiple simulation tools. The new Simcenter 3D Motion Transmission Builder automates the creation and simulation of transmission motion simulation models entirely within a single, integrated simulation environment. Simcenter 3D Transmission Builder can reduce your transmission simulation effort by 80%. Additionally, these models can then be seamlessly combined with Simcenter 3D Acoustics to perform gear whine analyses. According to Horim Yang, Senior Research Engineer at Hyundai Motor Company, “Transmission Builder is a useful tool that lets us model the gear train with different levels of fidelity depending on our analysis requirements.”
Simcenter 3D Aerostructures with composites: In the last release, we introduced Simcenter 3D Aerostructures, which streamlines the aircraft structural analysis process by up to 30% – from CAD geometry to finite element simulation and margin of safety calculations to reporting and traceability for certification. However, modern aircraft are engineered using lighter, yet stronger composite materials instead of aluminum. With 2019.1, Simcenter 3D Aerostructures can now calculate margins of safety on composite structures. This means airframers using composite materials can realize the same margin of safety process gains with Simcenter 3D Aerostructures.
New ties to the digital thread
Tie your simulations to the broader digital thread. Simcenter 3D is a part of the Simcenter portfolio of simulation solutions that span 3D simulation, 1D simulation, and testing solutions. Simcenter is comprised of a number of well-known products such as Simcenter Nastran, Simcenter STAR-CCM+, Simcenter Amesim, Simcenter Test.Lab, HEEDS, and much more. The 2019.1 release strengthens these ties to help you better predict product performance.
1-way coupling with STAR-CCM+ and Simcenter 3D for aero-acoustics: Efficiently explore and eliminate the source of unwanted noise originating from air passing over the side mirrors in a car, or noise coming from airflow within an HVAC system. Connections between Simcenter 3D and STAR-CCM+ now allow you to turn CFD results from STAR-CCM+ into equivalent acoustic sources for use in Simcenter 3D Acoustics to perform aero-acoustics and aero-vibro-acoustics simulation. With this solution, you can improve cabin
comfort for the end users of your products.
Simcenter 3D Flexible Pipe support for electrical cables: Electrical wires in moving mechanisms can sometimes get caught up in the machinery, or possibly get bent in a way that causes the harness to fail. However,
understanding how a wire harness behaves within a mechanism is a challenge because a wire harness is actually constructed out of many different wires that are bundled together with other wires of different sizes and materials like tape. A single, equivalent cable analysis won’t be accurate. In the 2019.1 release, you can now study how an electrical wire harness (or sub-harness) will bend and move within your assembly with Simcenter 3D Flexible Pipe. This solution imports stocks from NX Routing and models the interaction between all cables, external taping, contact, and possible section distribution changes. Simcenter 3D Flexible Pipe ultimately gives you deeper insight into how your wire harness will behave in a moving mechanism.
A new path forward
For LMS Virtual.Lab users, Simcenter 3D 2019.1 represents a new path forward that delivers all of the functionality from Virtual.Lab with the exceptional, integrated environment that will help you achieve faster CAE processes along with even more new simulation solutions. Key capabilities from Virtual.Lab that are now in Simcenter 3D include:
Simcenter 3D Specialist Durability: Fatigue specialists are concerned with complex loading events, weldments, new materials like composites as well as with the direct influence of the manufacturing process on local material behavior. The new Simcenter 3D Specialist Durability product provides the functionality of the well-known LMS Virtual.Lab durability solvers including the analysis of welds and composite materials. Simcenter 3D Specialist Durability migrates this key functionality to Simcenter 3D’s open and scalable environment that can use the results of popular third-party finite element solvers as well as Simcenter 3D multi-body solvers.
Simcenter 3D Correlation: Simcenter 3D Correlation helps you understand how well your FE morel represents reality. Simcenter 3D Correlation compares and correlates simulation results with physical modal test result that are captured in Simcenter Test.Lab. Once Correlation establishes the differences between both representations, Simcenter 3D Correlation can update the FE model to more accurately represent reality. Afterwards, the correlated FE model can serve as a basis to provide an optimal comparison to avoid testing errors.
Additional changes
Finally there are some additional changes that we are announcing with this release.
New names, same great solvers: First we have made name changes to two of our popular finite element solvers to align them with the rest of the Simcenter portfolio:
Simcenter Nastran: Previously named ‘NX Nastran’, Simcenter Nastran is a premier FEA solver for structural analysis. Available as a standalone solver or integrated into Simcenter 3D, Simcenter Nastran covers structural solutions for linear, nonlinear, dynamics, acoustics, and topology optimization.
Simcenter Samcef: Previously named ‘LMS Samtech Samcef’, Simcenter Samcef is a powerful finite element solver that is primarily used for simulation and evaluation of composites-based structures performance. Simcenter Samcef excels at composites-specific behavior such as progressive damage simulation which includes classic failure criteria like critical ply, value, and load case, along with inter- or intra-laminar damage modeling. In addition to part behavior simulation, Simcenter Samcef also simulates composites manufacturing processes, like curing, which can impact the final part shape as well as the part’s structural performance.
Faster release cadence: Up until now, Simcenter 3D was released on a roughly 15 month cadence. Starting with Simcenter 3D 2019.1, Simcenter 3D will be released on a 6-month cadence going forward. By incorporating agile development principles, Siemens is now able to deliver major functional enhancements faster which can help you improve your productivity. And with a consistent schedule for updates, you can better plan adoption of new technologies that are available to you. You can expect the next release, Simcenter 3D 2019.2 in June.