Latest simulations reveal data about hydrogen-powered aircraft and an integrated aircraft design
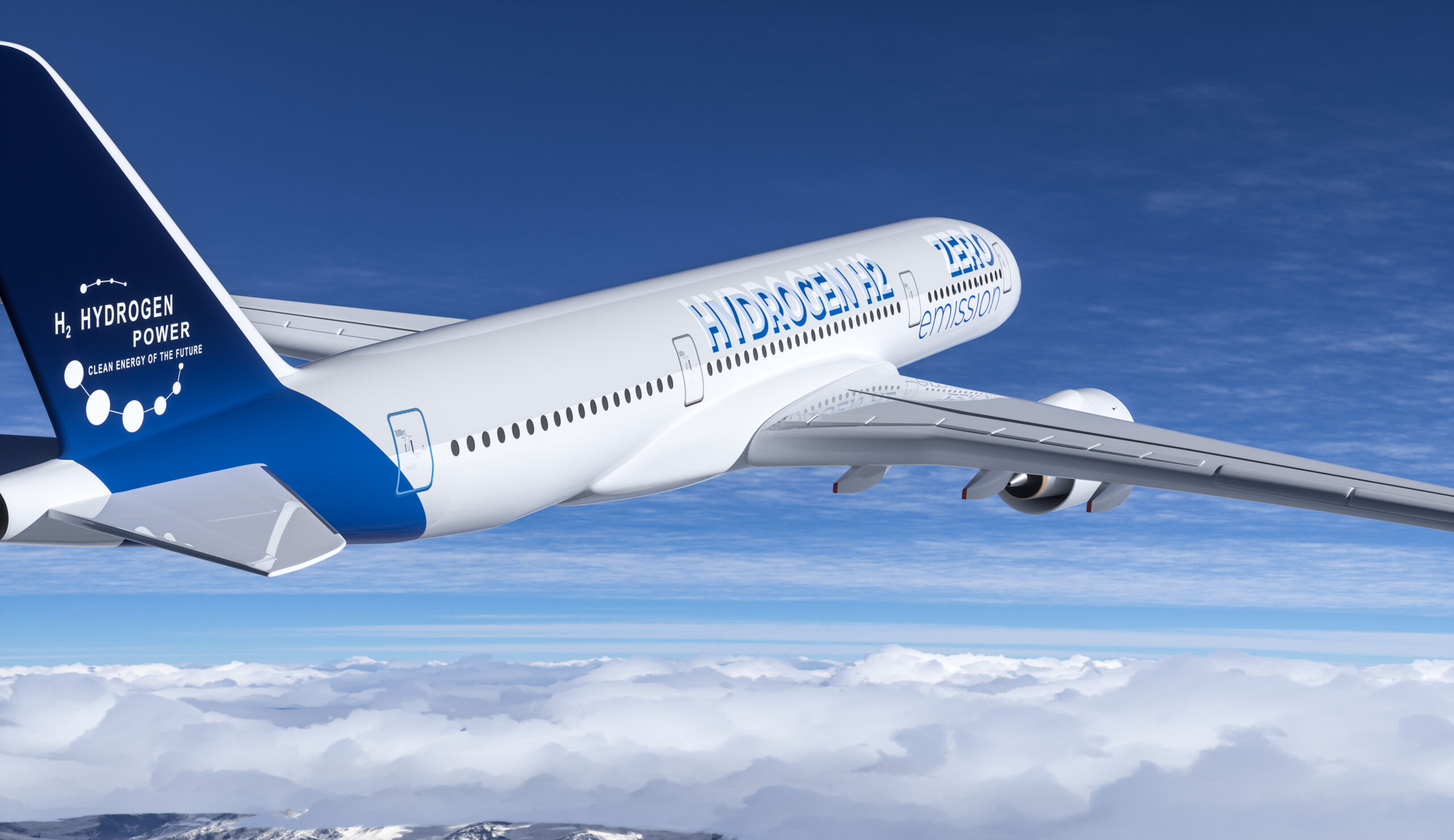
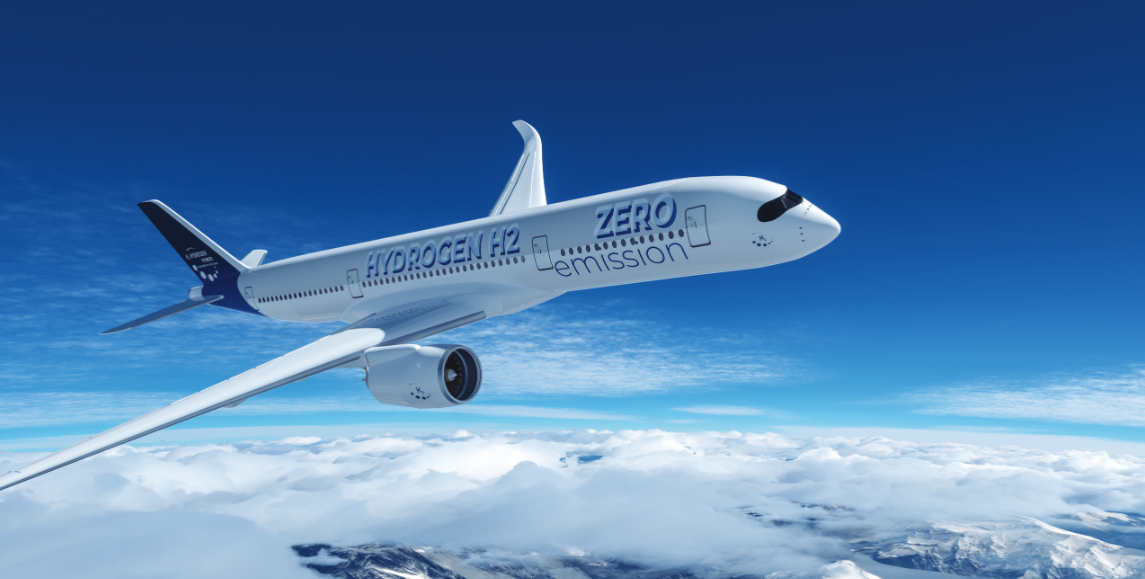
WHITE PAPER
Leveraging preliminary design and simulation to drive next-generation propulsion systems
How will the physical design of aircraft evolve to accommodate propulsion by hydrogen or other sustainable fuels? It is clear that the configuration of the entire aircraft will need to be re-imagined to reach sustainable designs and cleaner skies. The industry has therefore been studying how hydrogen-powered jet engines and hydrogen fuel cells will drive the next generation of propulsion systems and what this means for aircraft subsystems.
Siemens Digital Industries Software has been simulating the performance of an ATR-72 regional jet with hybrid propulsion using fuel cells and ultracapacitors in a typical flight mission and comparing this with the performance of the same aircraft propelled by direct hydrogen combustion. This shows us how hydrogen-burning turbo propellors will perform compared to hydrogen fuel cells.
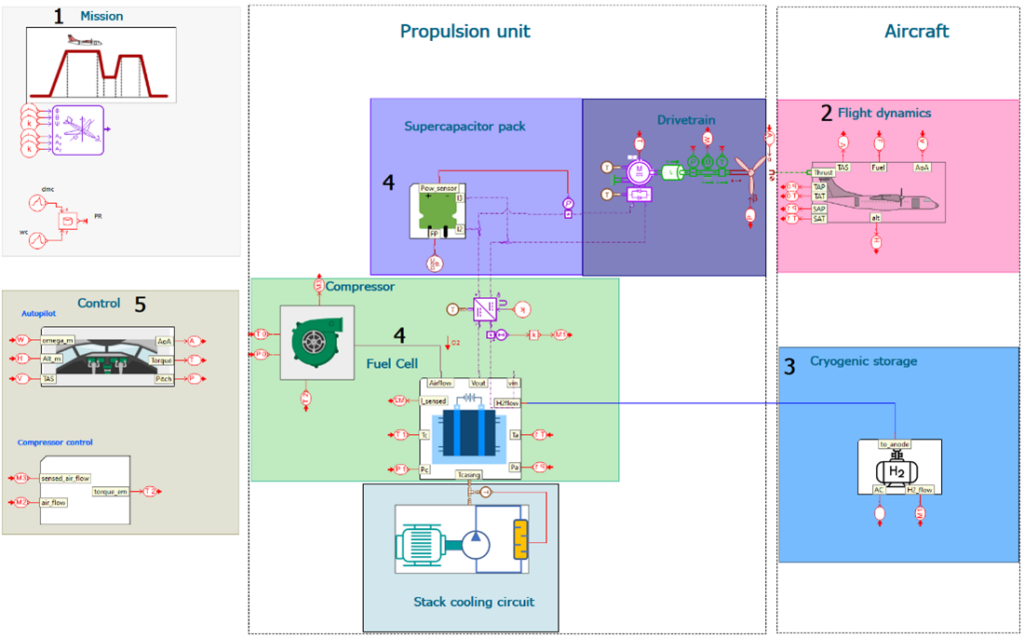

There is a great deal to learn. Will hydrogen deliver enough power to operate the propellors at sufficient speed? How many propellors will be needed?
Hydrogen appears to be the most promising alternative to kerosene due to its high specific energy and low greenhouse gas emissions and we could use it to generate electrical power via a stack of fuel cells. But fuel cells need cooling, so which method of cooling will be best? How can we use ultracapacitors to store energy and bring additional energy to fuel stacks?
Other sustainable fuels exist but hydrogen is the most promising because it can be burned directly inside a turbine engine burner. It also has a high gravimetric energy density, which matters more than the absence of CO2 emissions. The greatest challenge with hydrogen is to store enough of it, and its properties at ambient conditions. With a density roughly 10 times lower than kerosene, it needs to be stored under pressure in large containers. Its volume is much less in liquid form, but this brings another challenge: how to handle a liquid at temperatures as low as -253 degrees Celsius. Will this need new intensive insulation and heat exchangers and a new form of cryogenic tank?
We have some answers but there are many more questions. How will the new power components link to the larger aircraft subsystems? How will these new assemblies change the shape and form of the aircraft in our skies today? What is the most feasible approach in economic terms?
Simulation provides data and some answers
The EU’s Green Deal is providing funds to support investigations like these. At this early stage, there are no test results, but one route does offer clear insight into sustainable aircraft design: simulation.
Siemens Digital Industries Software is supporting customers across Europe with early-stage design support, using digital twin technology to explore the challenges of optimizing performance by virtual testing of fluid, thermal, mechanical, electrical and other system domains that must be re-imagined before green aviation designs can take off in the real world.
The Simcenter Amesim software and Virtual Integrated Aircraft (VIA) methodology were used to compare fuel volumetric and energy densities, specific heat capacity and storage temperatures required for hydrogen in three different aircraft designs.
- Simulations showed the combustion of hydrogen in an engine similar to the ATR 72-600 and modeled the gas turbine performance to obtain a model for the engine,
- New concepts for hydrogen-powered turbo propellors were modeled with Simcenter Amesim,
- Further simulations showed a flight mission that reaches the necessary altitude and airspeed.
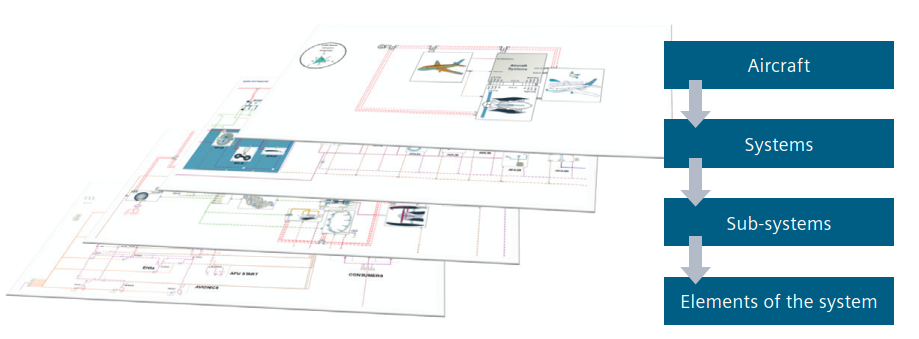
Using a PLM process can accelerate the early-stage designs so that we can model a complete hydrogen-powered aircraft where all of the powerplant systems come together in one integrated aircraft design.
Already, this work is bringing useful data and insights to aid future designs. Engineering workflows are key and simulation offers a synthetic view to design sustainable products for the future, which will have smart verification and traceability right through from the requirements stage to engineering test data.
Our results suggest that hydrogen-burning propellors could provide the fastest route to a lower carbon footprint for aviation. But fuel cell propulsion architecture is also promising and could use energy in a more optimal way than hydrogen propulsion.
Simulation can give us answers, and the VIA methodology points to a viable design for sustainable aircraft.
Go deeper
In the following white paper, discover the results of Siemens Digital Industries Software’s work on new propulsion systems and early-stage fuel cell concepts, and models of a complete hydrogen-powered aircraft.
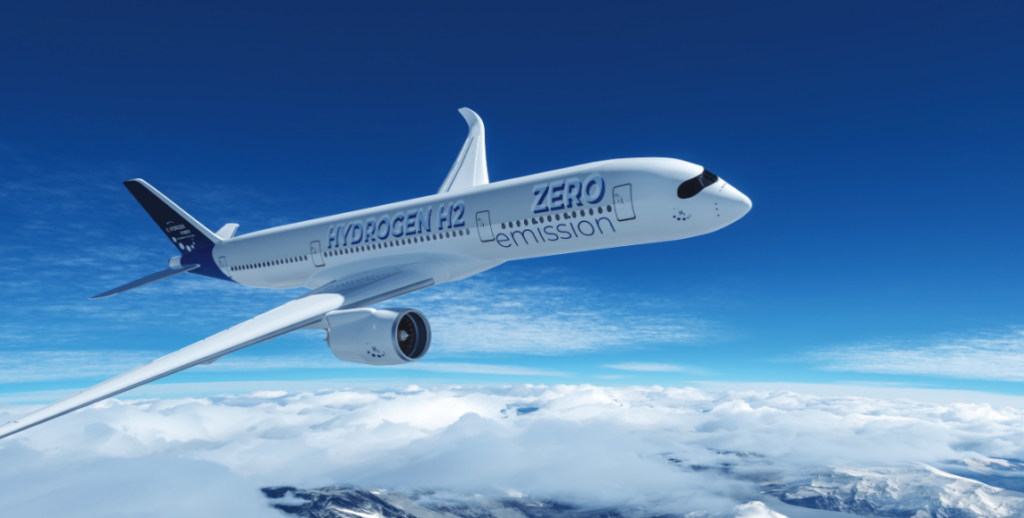
White paper
Leveraging preliminary design and simulation to drive next-generation propulsion systems