Simcenter STAR-CCM+ 2402 Released! What’s new?
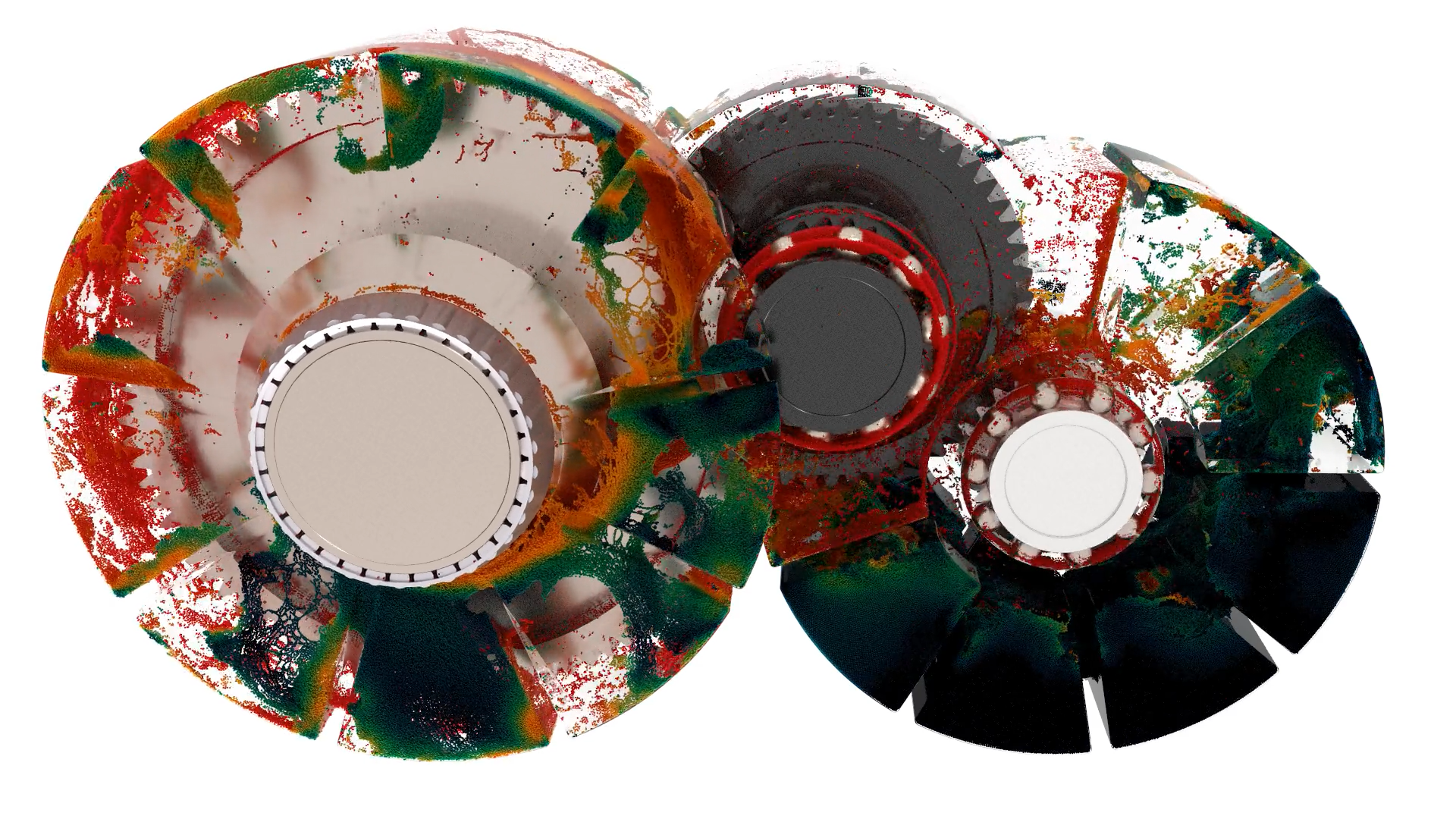
Leverage integrated SPH technology. Go faster with more GPU hardware options. Run faster, more accurate turbomachinery CFD. Model the complexity of strongly coupled fluid-structure interaction. Plus, many more features.
With the release of Simcenter STAR-CCM+ 2402, we provide engineers across industries with computational fluid dynamics (CFD) capabilities to go faster while modeling the complexity of today’s products. Leverage exciting new features to explore engineering possibilities and turn complexity into a competitive advantage.
Learn how to use Support Center
New enhancements in Simcenter STAR-CCM+ are aimed at helping you:
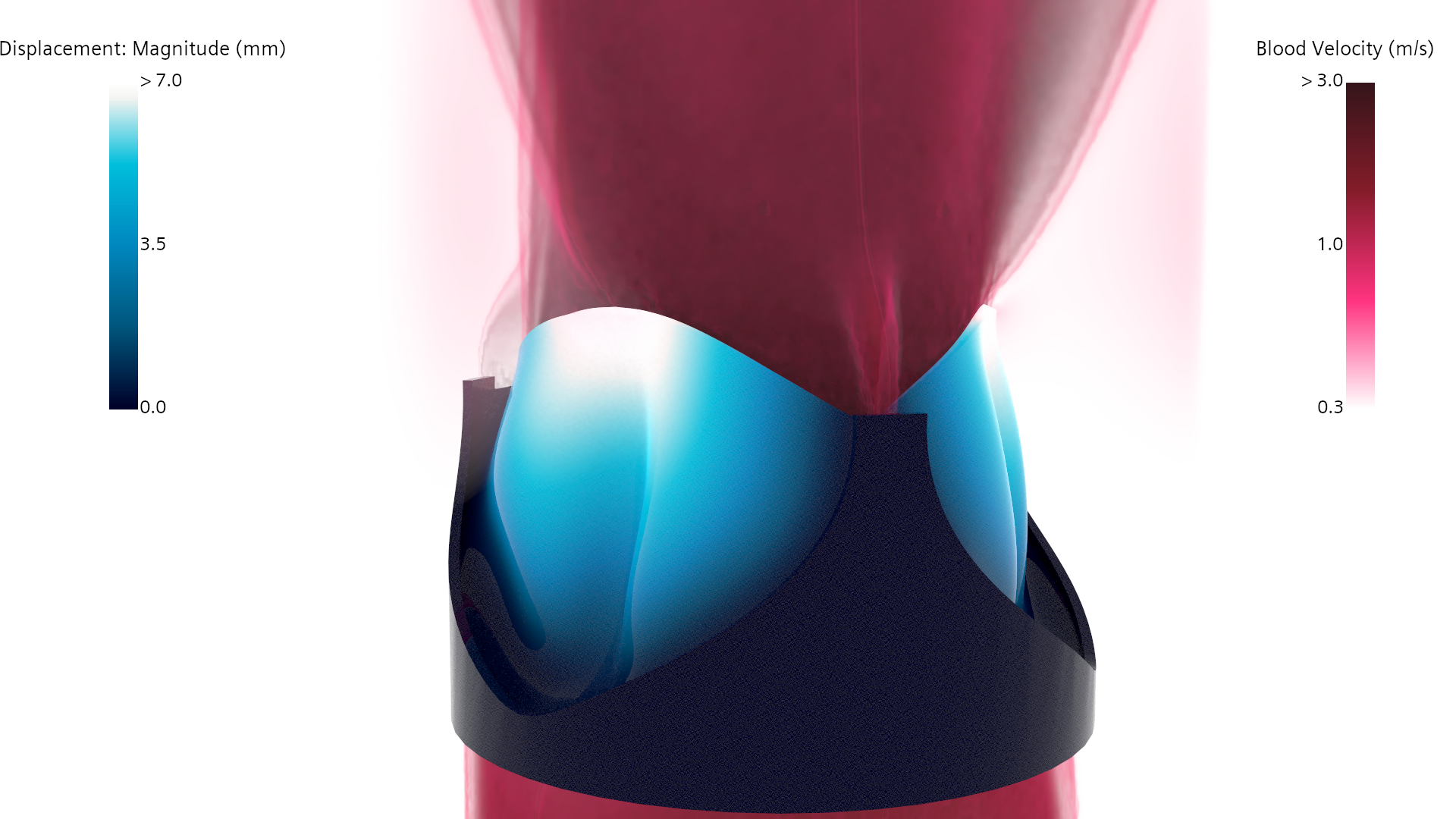
Model the complexity
Run faster, more accurate industrial axial turbomachine simulations
Meshing turbomachinery blade passages with polyhedral meshes leads to a comparably high cell count. This typically manifests in increased run times of turbomachine aerodynamics simulations.
As the major solution structured meshes have been introduced in Simcenter STAR-CCM+ earlier. Those enable a faster turnaround time for axial machines making the mesh smaller compared to polyhedral and allowing a faster simulation time. Structured mesh also offers high-quality flow-aligned cells in the main blade passage, providing faster convergence in simulation and higher accuracy of the solution.
With Simcenter STAR-CCM+ 2402, we are further expanding the Turbomachinery structured mesh capability with support of blade fillets. These fillets can be either at the shroud or at the hub. A seamless user experience is guaranteed with the fillet being automatically detected as part of the blade surface input without any additional input.
Overall, the structured turbomachinery mesh, together with automatic fillet support leads to a further increased accuracy and faster time to solution with no additional user effort.
Tackle highly dynamic fluid loads leading to large solid deformations
For applications where a strong 2-way coupling between a dense fluid and a very flexible structure exists convergence and stability of a CFD simulation are very hard to achieve.
With Simcenter STAR-CCM+ 2402 we introduce a set of new features that enable exactly that kind of complex Fluid-Structure-Interaction simulations, where highly dynamic fluid loads lead to large deformations in the solid structure: The new Dynamic FSI stabilization method gives you very good control over the simulation with only one adjustable coefficient while being fully compatible with the solid stress load step solver. And with the Backward Differentiation Time Integration scheme now also being available for the solid stress solver, full kinematic consistency between solid and fluid is now ensured even for setups using 2nd order time integration.
This next-generation Fluid-Structure Interaction (FSI) modeling lowers the barriers to tackling highly dynamic strongly 2-way coupled FSI applications.
Enable applications involving radiation in participating media
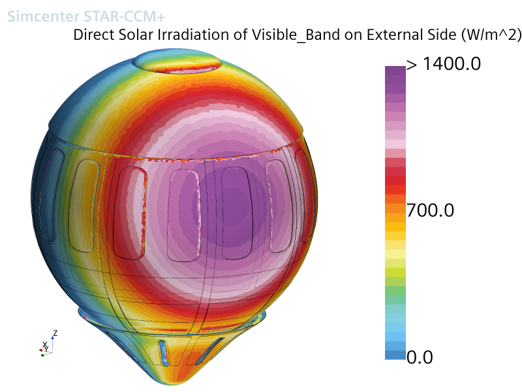
Many applications in the food and beverage, medical, and process industry or in Additive Manufacturing, heavily rely on the volumetric interaction of radiation with a processed material. Hence to tackle such scenarios with CFD simulation, you need an accurate model of radiation absorption and scattering in the presence of a participating media.
With Simcenter STAR-CCM+ 2402 we are expanding the already existing Surface Photon Monte Carlo SPMC model (which only considers surface-to-surface radiation and ignores participating/volumetric effect) to a fully Volumetric PMC. Generally, PMC, a statistical method for solving the Radiative Transfer Equation, is considered one of the most accurate solution approaches. With the expansion to Volumetric PMC we enable a combined volumetric and surface radiation modeling and hence provide an even higher-fidelity approach.
This allows for more accurate modeling of complex phenomena like absorption and scattering of the radiation when it interacts with a participating media. To capture the interaction of radiation with liquids it can be run in conjunction with Volume Of Fluids (VOF). Thanks to the Hybrid Volume-Surface Scheme, users can efficiently use VPMC only in the region where absorption accuracy is needed, while keeping the rest with Surface PMC. This allows for impressive speed-ups of up to 37x compared to a pure Discrete Ordinate Method (DOM) solution.
VPMC is further expanding the already rich physics offering of Simcenter STAR-CCM+ for radiation modeling (DOM, Spherical Harmonics P1, Surface-to-Surface, SPMC) with the most comprehensive high-fidelity approach.
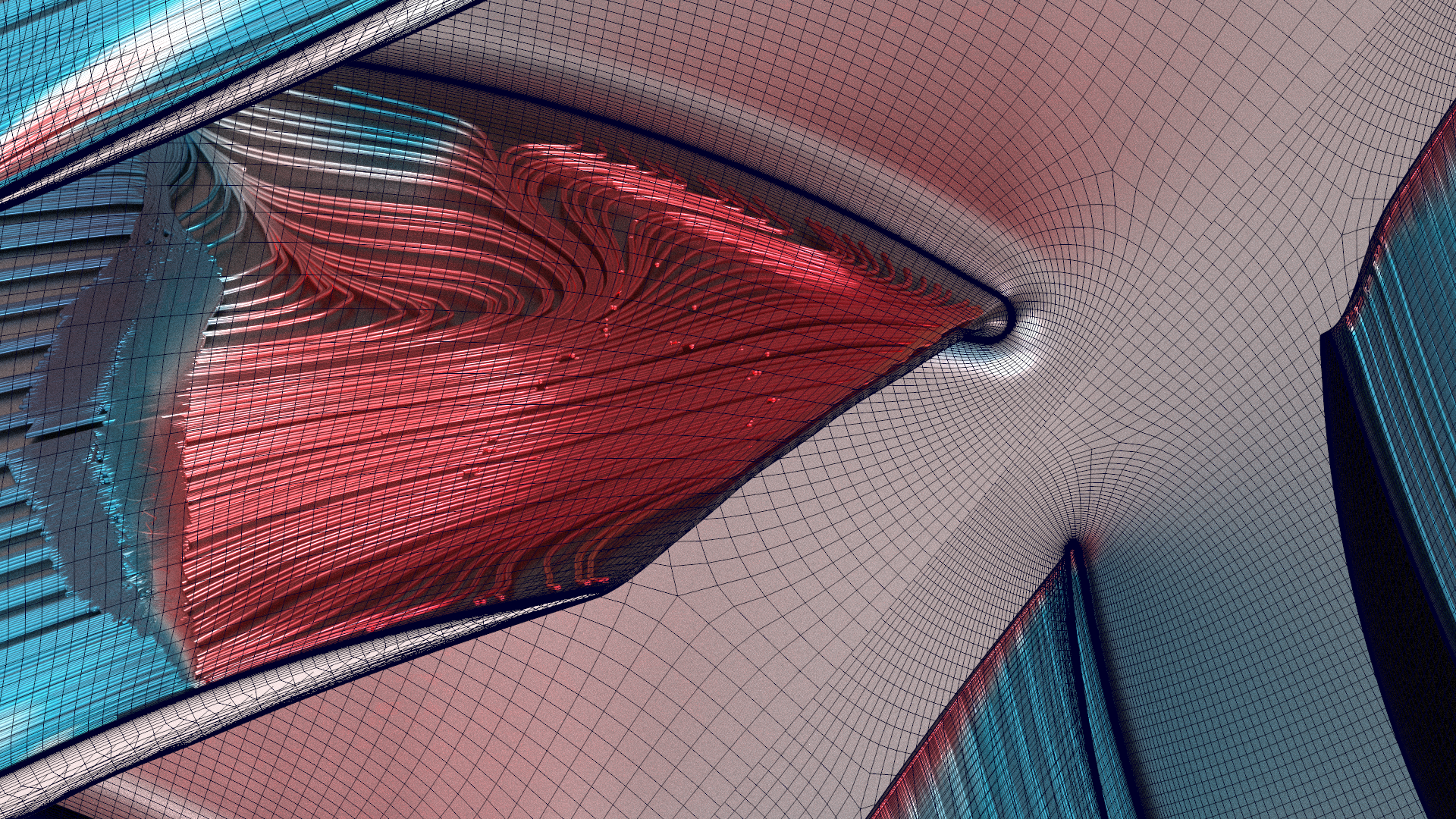
Explore the possibilities
Unleash cross-functional synergy for Design Exploration
In a world of ever more complex products, the consideration of trade-offs across engineering disciplines is of fundamental importance to maximize product performance in a holistic way. Therefore, siloed untracked Design Exploration studies in a single CAE discipline pose the risk of unrealized performance potential.
With Simcenter STAR-CCM+ 2402 we are introducing an integration of the Design Manager in Teamcenter Simulation. The integrated solution will allow to get real-time updates and notifications on geometry changes, requirement changes, parameters, etc. from the other engineering teams which may affect your Design Exploration project.
The integrated Design Manager will help your teams accelerate time to market by leveraging Teamcenter capabilities for Design Exploration: Team members can directly access the right data in Teamcenter, ensuring traceability between requirements and results and leveraging a centralized database of project/product information. The embedded study launch from Active Workspace is further democratizing design exploration.
With the resulting enhanced cross-organizational collaboration you will be able to leverage the full potential via informed cross-functional product performance optimization.
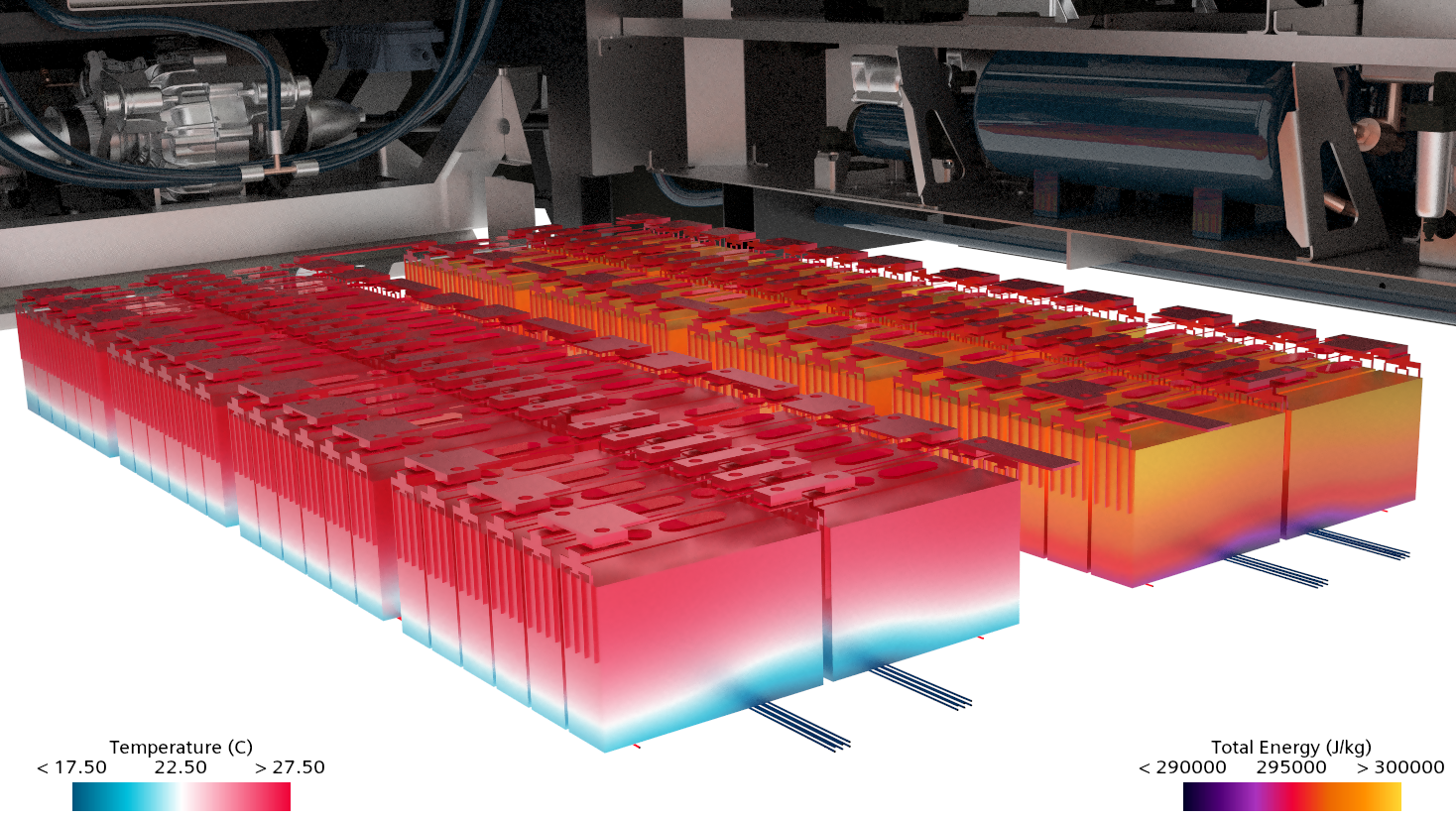
Go faster
Perform faster surface preparation for complex geometries
In external aerodynamics, CFD engineers need to strive for an efficient distribution of prism layers in exterior and interior parts of the vehicle. Using existing surface repair tools, the splitting of low y+ and high y+ surfaces can be a tedious process that can take hours or days depending on user experience and model complexity. Splitting of part surfaces is also important in any study when for example reporting of a quantity on a specific boundary or assignment of boundary conditions is desired.
In Simcenter STAR-CCM+ 2402, we are introducing an interactive classification tool in surface repair that expedites the splitting of part surfaces. The feature comes with an intuitive user interface and state-of-the-art algorithms that enable a fast and efficient classification allowing to save time. The tool can be applied to individual parts or a collection of parts that can have different tessellation levels.
The classification process is fast, and faces can be classified within seconds. The tool also allows the recording of a macro, for an even faster classification of distinctive design variants. Therefore, for external aero simulations, valuable surface preparation time can be saved as well as mesh count. This leads also to solver run time reduction with minimal drag count differences.
Go faster with access to a wider range of hardware for GPU-native acceleration
The benefits of GPU-enabled acceleration of CFD simulations are meanwhile without any doubt. Significantly lower per-simulation cost for the same number of designs, massively reduced energy consumption and the ability to replace thousands of CPU cores with a single GPU node. However, to date the GPU-enabled acceleration in Simcenter STAR-CCM+ was tied to a single GPU hardware vendor, limiting your options.

In Simcenter STAR-CCM+ 2402, we take an important step forward in our GPU offering. Now, Simcenter STAR-CCM+ computations can be undertaken on AMD GPUs and NVIDIA GPUs alike. In this release, you can now leverage GPUs from the AMD Instinct™ 200 series (MI210, MI250, MI250X), with an unchanged consistency in results regardless of the hardware chosen, be it CPUs or GPUs. This gives you a wider selection of hardware, easier access to GPU-accelerated CFD, and ultimately more flexibility to get your CFD results as efficiently as possible.
Run CHT and multi-timescale simulations more efficiently with GPU-native solvers
As outlined above GPU-accelerated CFD simulation poses a long list of benefits, including the potential to run your simulations in a cost and energy-efficient manner. Accordingly, our benchmarks over the last release cycles have proven the excellent performance of Simcenter STAR-CCM+ on GPUs. And so, it is of fundamental importance to expand the ability to leverage GPUs to more models, and hence more applications.
With Simcenter STAR-CCM+ 2402 we therefore continue the porting of solvers and capabilities to become equally available for GPU- and CPU-native simulations. The new version offers GPU-native Fluid-Solid and/or Solid-Solid Implicit and Explicit Mapped Contact Interfaces and a GPU-native Multi-Part Solid material properties model.
Together these enhancements enable you to run Conjugate Heat Transfer (CHT), Vehicle Thermal Management (VTM), and other multi-timescale simulations on GPUs with all associated benefits. A CPU-equivalent solutions is ensured by maintaining a unified code base.
Significantly speed up simulations of multi-species coupled flows
Applications involving reactive flows can be found across many industries. And while CFD simulation can cover all related aspects of chemical reactions with a high level of accuracy, it comes at a cost. Typically, fully coupled flow, energy and species simulations can be computationally very demanding.
Therefore, in Simcenter STAR-CCM+ 2402, you now have the possibility to use the Segregated Species solver in conjunction with the Coupled Flow and Energy solver, as an alternative to a fully coupled Flow-Energy-Species approach. Solving the species transport in a segregated fashion reduces the computational time for the whole system, with great speedup benefits up to x10 depending on the use case or – more precisely – the number of species involved.
Note that while Coupled Flow/Energy with Segregated Species approach can provide significant speed-up for multi-species simulations, it is expected that certain more complex reactive cases will require a full Coupled Flow/Energy and Coupled Species approach.
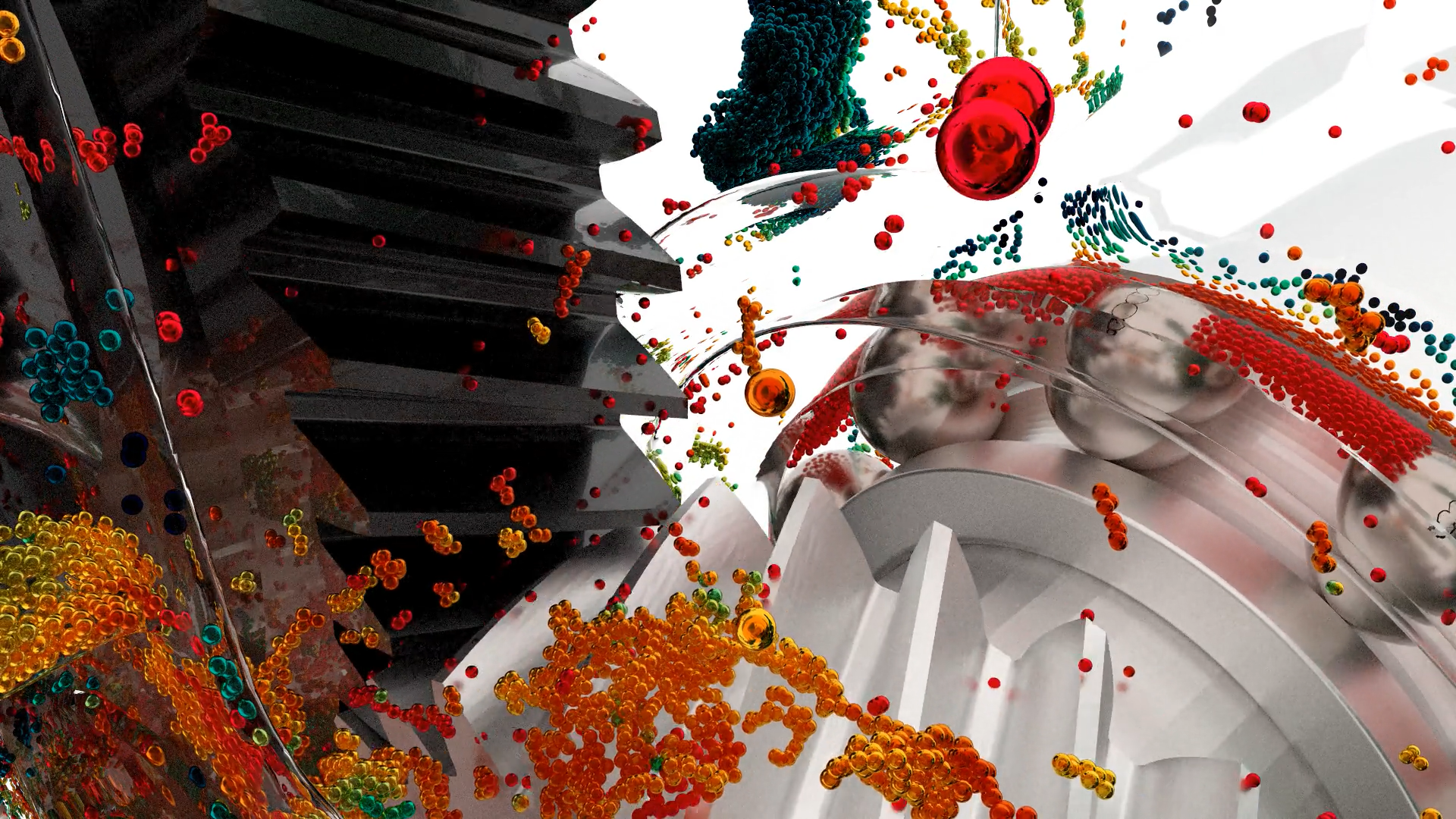
Stay integrated
Smoothed-Particle Hydrodynamics (SPH) integration into Simcenter STAR-CCM+
The Smooth- Particle Hydrodynamics (SPH) technology is a very powerful and rapid alternative method to model complex transient flows with highly dynamic free surface flows including jets and splashes. However, standalone tools for SPH and meshbased-CFD force users and engineering teams to choose the tool a priori and eventually work in multiple different tools depending on the exact simulation requirements.
In Simcenter STAR-CCM+ 2402, we are releasing the first version of the SPH solver fully integrated into the platform enabling you to run SPH and mesh-based simulations from the same tool alike. As SPH does not require volume meshing, it allows you to quickly handle complex body motion even with contact and complex geometries. Through the integration into Simcenter STAR-CCM+ you will immediately benefit from the power of Simcenter STAR-CCM+ as a CFD simulation platform: Integrated end-to-end workflow automation, advanced pre-processing with an embedded CAD tool and seamless external CAD connectivity, powerful data analysis and embedded design space exploration with Design Manager.
The integration ultimately allows you to run various types of multiphase applications in one single environment expanding your choices beyond established finite-volume methods like VOF or MMP, to a rapid meshfree SPH method. All that without the need to learn and maintain an additional CFD software tool. In this first release, we target the powertrain lubrication with oil bath application. Note that to be able to run the SPH solver, customers will need an additional license.
These are just a few highlights in Simcenter STAR-CCM+ 2402. Those features will enable you to design better products faster than ever, turning today’s engineering complexity into a competitive advantage.
Best CFD simulation software
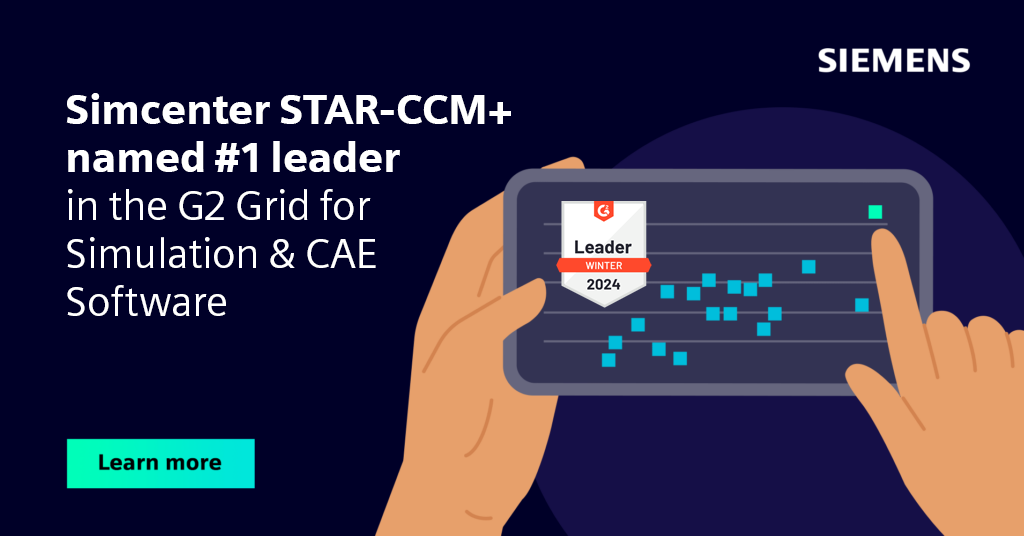
User perception is critical; it’s a reflection of how well Simcenter is doing, and whether our continuous software release cycles are resonating with you. Simcenter STAR-CCM+ G2’s peer review latest results suggest we’re making great strides in the community and recognized as the best CFD simulation software. We’re thrilled to announce that Simcenter STAR-CCM+ has secured the number one position in the Simulation & CAE Software category on G2. It’s a testament to the great strides we continue to make every year. We are beyond grateful to our wonderful users for this recognition.