Electric vehicle NVH challenges: The mindset and tools you will need
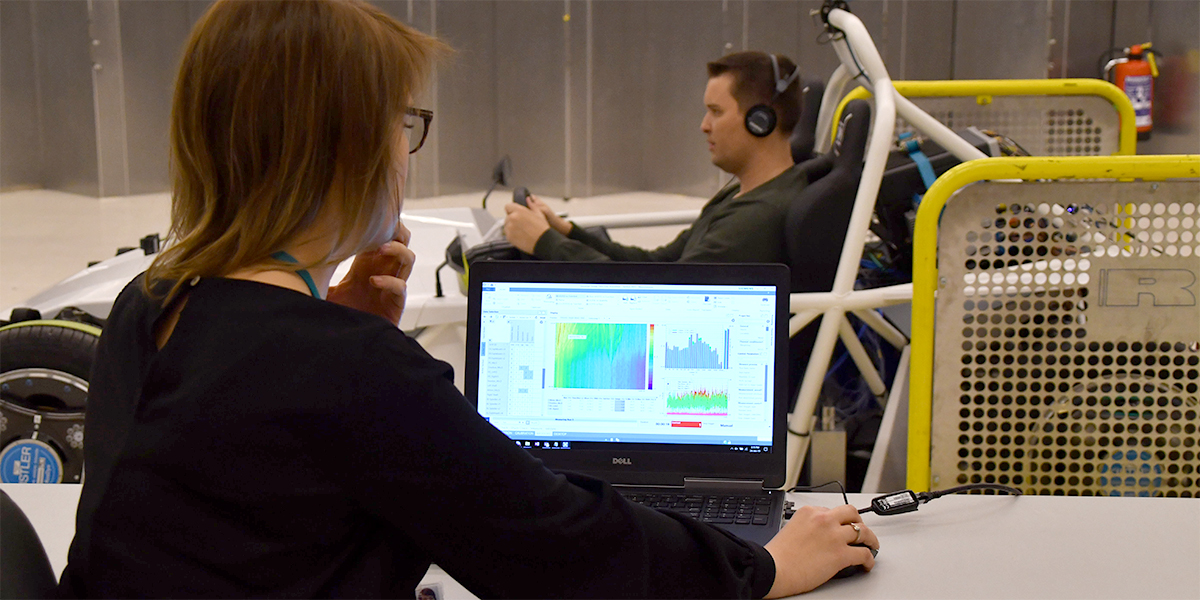
The question of the day is – would you buy an electric vehicle (EV) today?
Maybe. Although, during the upcoming years, you are more likely to answer: “Yes!”. Let’s face it. Avere, the European association for electromobility, estimates that there are already 1 265 441 passenger electricity powered cars driving around the Europe, using 161 426 public charging points. And both numbers will increase in near future. Countries world-wide are introducing the mobility visions promoting and supporting electric cars (e.g. Electromobility in Germany: Vision 2020 and Beyond,etc.). According to Bloomberg New Energy Finance, 55% of all new car sales and 33% of the global fleet will be electric by 2040.
Electric car development hits bumps in the road
However, there are also some important bottlenecks that cause reluctance to switch to electric cars. One of the most important is the driving range of the electric vehicles. The EV development teams strive to reduce the vehicle weight to increase the driving range. But reducing weight of the vehicle chassis and body is not given! Finding the optimal balance between vehicle weight and performance attributes, such as durability, NVH, ride and handling, becomes more important than ever. Yes, you need to increase the driving range, but on the cost of reduced durability performance that could lead to earlier vehicle damage. Also, reducing vehicle weight can deteriorate handling performance. It means your vehicle may lose stability when performing certain driving maneuvers.
Here is another engineering dilemma – how do you balance the vehicle body stiffness while keeping up with the right NVH characteristics? At Siemens Simcenter, we recognize these challenges and we aim to provide our customers with solutions for different vehicle development teams to tackle all these problems and help to find optimal lightweight vehicle conditions without loss in performance.
What are the other electrical cars development shifts?
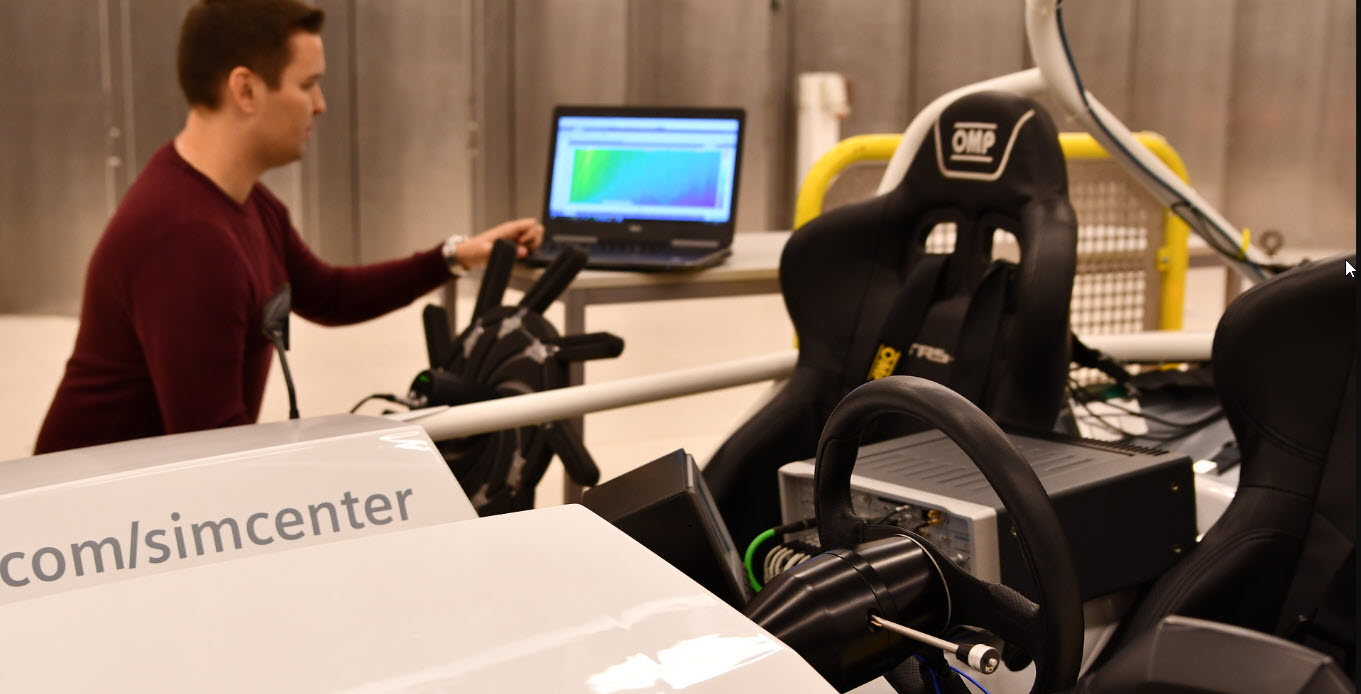
Electric vehicle noise in the spotlight
The trend towards electrical vehicles poses both challenges as well as opportunities for car developers. The absence of the internal combustion engine (ICE) changes the signature of the interior cabin noise dramatically. The most obvious game changer is the fact, that the withdrawal of the traditional powertrain unveils the other noise contributors or make them more audible and prominent. In 2011, G. Goetchius (Leading the Charge – The Future of Electric Vehicle Noise Control, Sound & Vibration) estimated the noise contributors in ICE vehicles and predicted the noise morphology in the electrical ones. According this publication back then, in the traditional ICE vehicles, the biggest noise contributor is the powertrain followed by the road, wind and ancillary system noise. While in electrical vehicles, the road noise and wind are the most dominant noises. And what’s more, the new structure reveals noises that were originally masked by the combustion engine (such as ancillary system – whine gears, steering rack, air conditioning system, wipers, ABS module, pumps etc.).
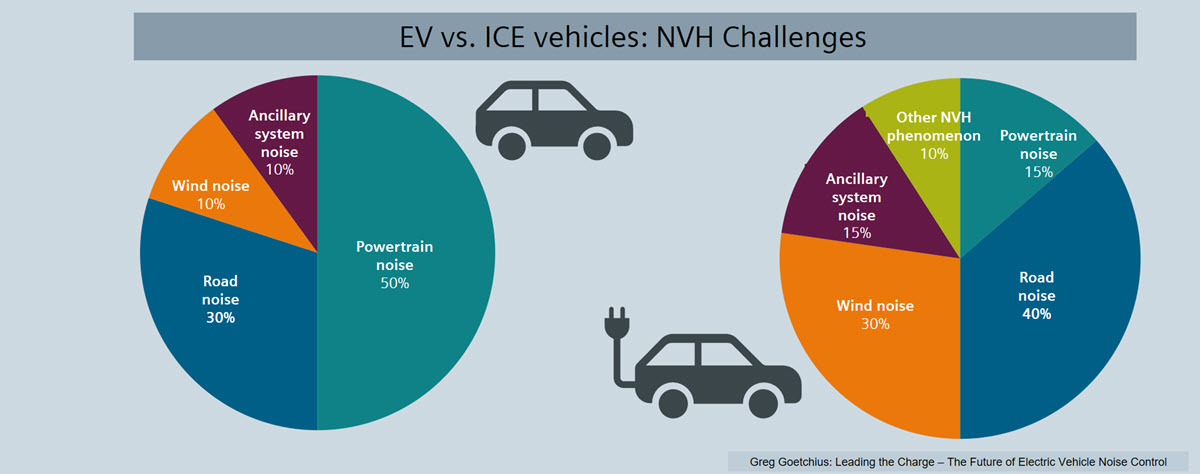
EV vs ICE vehicles NVH challenges
Without any surprises, the structural changes in electric vehicle noise will need new engineering approaches to optimize the NVH performance with appealing sound quality.
Here are three strategies you should focus on to make the ride in your electrical vehicle to sound as a symphony.
Act on the present noise source
Firstly, you may need to find the noise root cause and act on it. Depending of the origin of the noise source, different NVH analysis techniques are required. Reducing wind noise, for instance, happens most effectively in wind tunnels. These allow to effectively isolate the wind noise from other noise sources and find the most effective measures to reduce this annoying source. However, as these tests are extremely costly, it is crucial to test with extremely efficient measurement techniques. The use of industrialized testing processes based on large beamforming arrays that allow identification of the exterior noise sources, and use this data to decide what to test next, becomes more and more a reference.
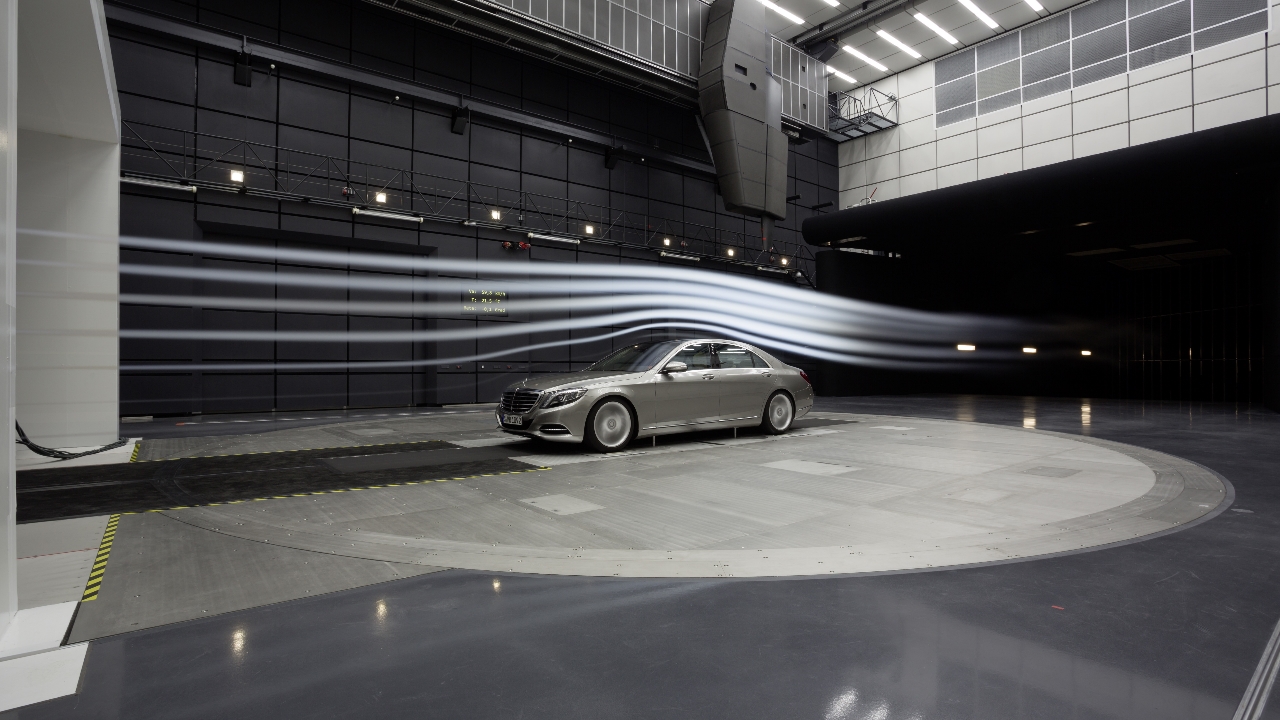
Road noise needs to be handled with effective and reliable techniques, such as transfer path analysis (TPA). This technique allows to pinpoint the noise critical paths on the chassis and car body contributing to the interior noise. To be able to handle the complexity and closely spaces loads of suspension systems, more advanced techniques such as strain-based TPA becomes another necessary building block.
For other auxiliaries, the key information can be provided by wide toolset of NVH tests and analysis techniques. And again, for many of these subsystems the traditional transfer path analysis (TPA) can help to identify the component or structure causing the noise issue.
Acting on the noise source, however, does not always provide solutions early enough. In case it is not too late in the vehicle development cycle, the responsible team can proceed with component design adaptations and improvements. But in real life, there are situations, when design adaptations are impossible or cause conflict with other attributes (such as weight, durability, etc.). Or often, the results of the TPA leads to pragmatic and expensive additions of damping and trimming to the vehicle. The disadvantage is that damping material increases the vehicle weight – which will directly reduce the vehicle range, add extra cost and prolong the vehicle assembly. What’s more, this strategy is limited and doesn’t offer an optimal solution in all the cases.
Master the electric vehicle sound quality including active sounds
There is good news. The shifted noise structure of the electric vehicle brings an option to add new noises. This opens an opportunity to create new and pleasant driving experience for your customers. From this perspective, sound quality engineering is the key tool to develop high-performing sounds within the vehicle. This technology is currently gaining ground in the automotive industry.
It all starts with the acquisition of realistic sound data, including for instance binaural recording. Secondly, to be able to analyze the acquired sounds, you can proceed with audio replay, using different filtering and analysis through different sound quality metrics. And finally, you shall organize a Jury testing, which is based on subjective audio perception. Sound quality engineering combines objective analysis metrics with subjective analysis. This strategy will provide you with detailed insights to find answers to questions like – what do the customers like to hear? What sounds do they prefer in different corners of the world?
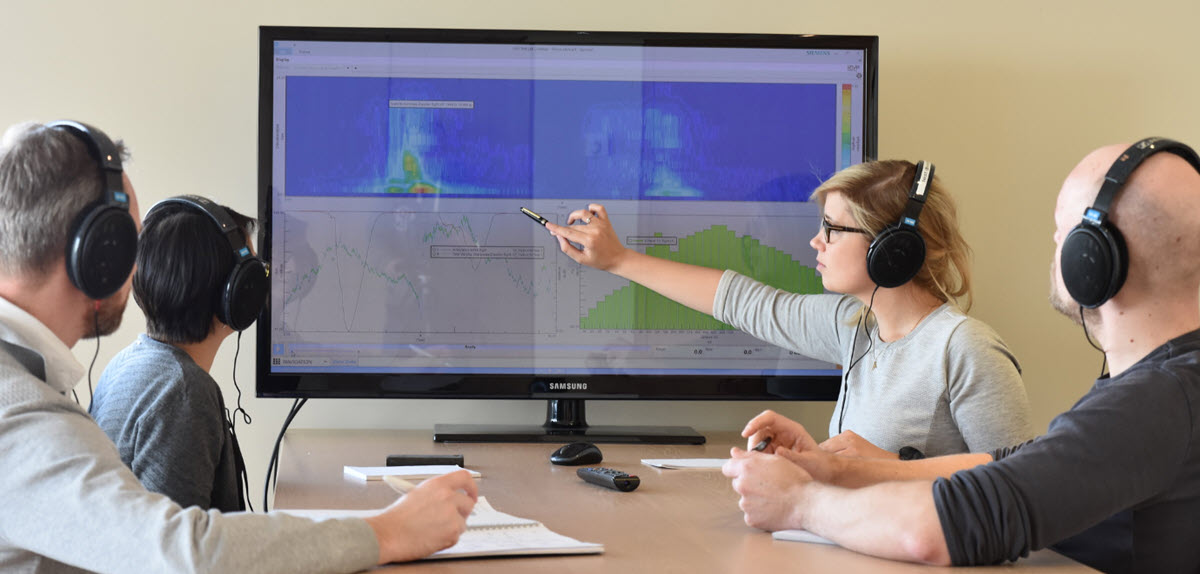
Simcenter Testlab Jury testing for EV NVH development
Another application, where sound quality is currently gaining importance, is the exterior artificial sounds generated by the acoustic vehicle alerting system (AVAS). This system warns pedestrians of an approaching vehicle. Developing new exterior warning sounds is something of a novelty. Different countries around the globe currently impose new certification requirements for electrical cars. Car producers need to design and certify warning sounds that the electrical cars must exceed traveling at low speeds. Anc at the same time, automotive OEMs are highly concerned about the perception of the new vehicle sounds. Designing new artificial sounds that reflect the brand DNA requires the right toolset for sound quality engineering.
Speed up vehicle development time by blending simulation and testing together
To keep up with the market, automotive OEMs need to react fast and develop advanced vehicle models rapidly. This creates the need to take control of the vehicle NVH performance as quickly as possible, earlier in the development cycle ever. This translates into the demand to be able to predict the component or subsystems behavior before integrating them into the vehicle. In practice, this also leads to introduction of new technology that merges the simulation and physical testing together throughout the vehicle development cycle. While in the past simulation and testing where two separate worlds, the future evolves more into hybrid approaches. This concept can drastically impact and improve the development time.
Component-based TPA is one example (here you can find a related white paper). The compelling combination of test and simulation enables the NVH engineers to predict the final vehicle NVH performance before assembling the first full prototype. In a nutshell, this technology enables you to predict a component or subsystems behavior prior to integration. Consequently, it enables the dream to create a virtual vehicle prototype by assembling different components (e.g. electrical engine, suspension system, body, etc.). Component-based TPA is very powerful concept not only because you may get an accurate prediction of the vehicle NVH behaviour in development stage, when implementing design improvements is still easier. But also, the component-based TPA enables you to work with a standardized platform to virtually assembly countless vehicle variations with much lower time investments.
Another example is the trend to combine 1D simulation and test in a more hybrid approach, so called Model-based system testing (MBST). With MBST technology, the use of physical component in combinations with 1D models becomes more and more the industry standard.
These are the key trends in NVH testing that will drive electrical vehicles development in near future. Besides, it is important to realize, that is not only the product changing. It is also the OEM’s frame-work that will change soon too. There will be new requirements and expectations that team members will have to fulfill and skills the engineers will need to learn.
Are you interested to understand the EV development trend in more detail?
Check out this website to find more details.
Pss, one more tip. Subscribe for the automotive newsletter. In this way you will get the latest industry insights and you will never miss a free webinar invitation.
Comments
Comments are closed.