3 aero-(vibro)-acoustic scenarios to solve flow-induced noise
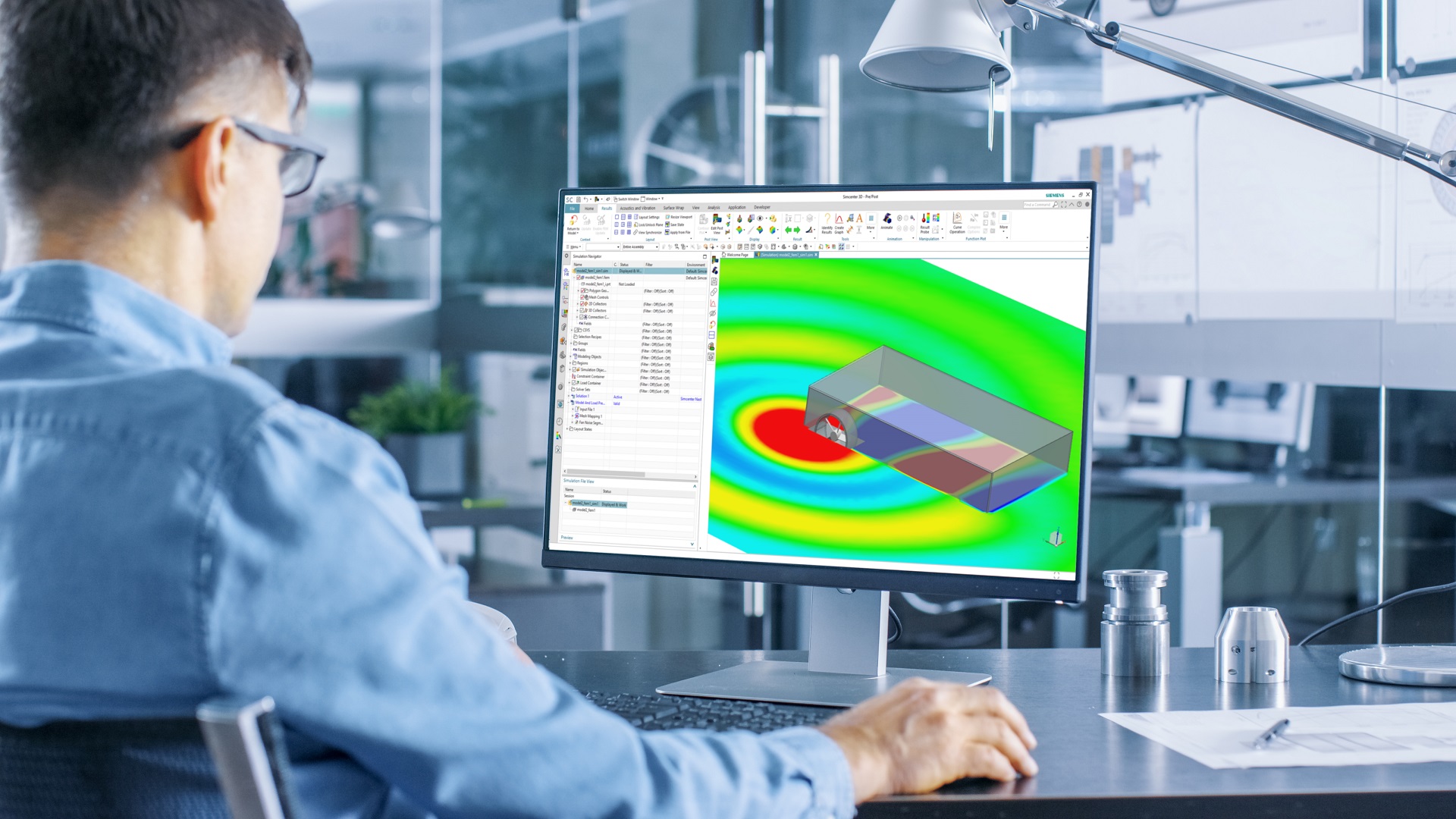
Inside the car’s cabin, and especially for a hybrid or an electric vehicle, the overall noise level is primarily dominated by HVAC, cooling and wind noise. These are usually simulated using FEM models. Yet, there are FE models and FEM models. What is meant with ‘lean’ FEM models? And how can you benefit from these lean FE models to facilitate the prediction of flow-induced noise?
The supremacy of lean FEM models to solve flow-induced noise
Finite Element Model Adaptive Order, or FEMAO, does the trick. Adaptive models contain the right number of Degrees of Freedom (DOFs) at whichever frequency of interest. They offer the same accuracy and level of detail, but much faster than standard FEM simulations.
How? Well, unlike standard FEM simulations which need to use very small FE elements to capture pressure fields at higher frequencies. FEMAO uses a coarse mesh to represent an acoustic domain, while the solver automatically adapts the order of the polynomials that were used to describe the pressure field within the FEM elements. Hence, the mesh is not refined with frequency. Yet the number of shape functions and their polynomial order is increased per element and per frequency. Moreover it is fully automatic, based on accuracy criteria. 1-0 for lean FEM models!
OK. Back to solving aero-acoustic and aero-vibro-acoustic source generation and propagation. Typically, this simulation solution supports three types of scenarios. These are described and demonstrated during the free webinar: 3 validated aero-(vibro)-acoustic scenarios to predict noise levels. We give you a glimpse hereunder.
1. Wind noise
Wind noise originating from a flow around a side mirror and A-pillars is emitted towards the car interior from side-window vibrations due external fluid loading. Logically, we need to compute acoustic pressure levels at driver’s ear.
To solve wind noise, we start with accurately analyzing the naked external aerodynamic loading on the CFD mesh boundaries. Next, we prepare wind loads for the vibro-acoustic model via advanced mapping. Eventually, we compute efficient FEM vibro-acoustic simulations using single coarse physical mesh for all frequencies of interest of the side-window and car interior using wind loads.

2. HVAC noise
As there is no masking noise from an internal combustion engine, flow induced acoustic sources on static components, such as HVAC noise is more prominent in electric and hybrid electric vehicles. There are various alternatives to handle the flow induced noise from duct components; with Simcenter STAR-CCM+ only, or by coupling Simcenter 3D with Simcenter STAR-CCM+ software. Both provide accurate results with different assumptions in free-field, while the hybrid solution also provides the acoustic response in presence of installation effects (including absorbing and reflective surfaces in the cabin).

3. Fan noise
Depending on the user’s application, flow induced acoustic sources on rotating bladed components that generate fan noise, is addressed by either deploying the workflow with Simcenter STAR-CCM+ or by combining Simcenter STAR-CCM+ and Simcenter 3D solutions. Both methods rely on transient CFD simulation and provide the same results in free-field for tones and broadband levels (when there are no reflective or absorbing surfaces in the environment of the fan). In case you want to compute the acoustic propagation in presence of so-called installation effects such as walls, filters, heat exchangers, we couple both software solutions.

Interested to hear more? Watch the on-demand webinar: 3 validated aero-(vibro)-acoustic scenarios to predict noise levels and discover how to predict and address flow-induced noise at an early stage of the design cycle.
Korcan Kucukcoskun
This aero-acoustic modelling approach for flow-induced noise enables lean, surface pressure-based source creation for stationary or rotating surfaces. It requires minimized input data from CFD solution for source generation. Coupling the FEM structural solver with FEMAO acoustic solutions also allows to account for installation effects in sound propagation.
- Webinar: https://www.plm.automation.siemens.com/global/en/webinar/aero-vibro-acoustic-simulation/63791
- Simcenter 3D Acoustics solutions: https://www.plm.automation.siemens.com/global/en/products/simulation-test/acoustic-simulation.html
- Simcenter solutions for fluid dynamics: https://www.plm.automation.siemens.com/global/en/products/simulation-test/fluid-dynamics-simulation.html