Simcenter Testlab 2019.1: Model-based system testing embeds simulation within testing
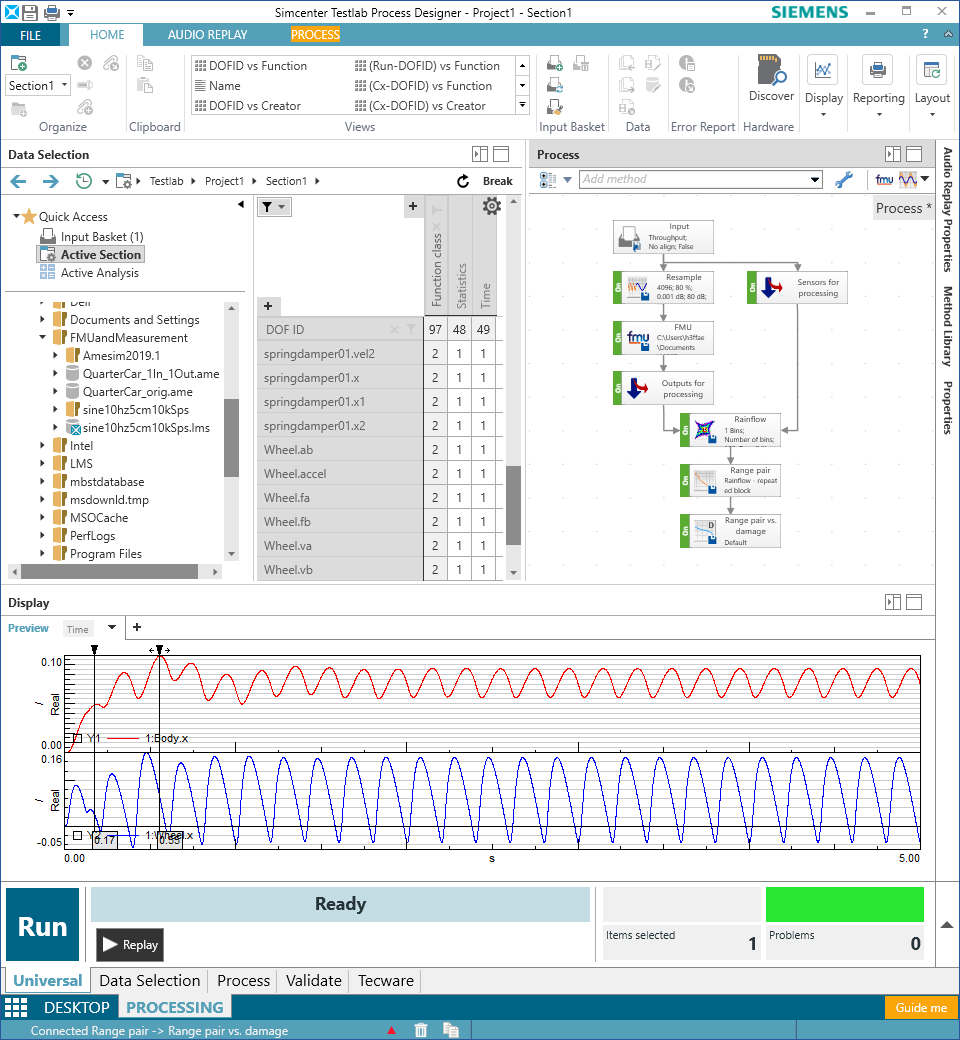

Discover model-based system testing and blur the boundaries between test and simulation!
How do you master today’s systems engineering complexity in a productive way? This is definitely one of the major challenges engineers are currently facing across industries. The answer is Model-based Development or MBD.
Put simply it means increasing the use of simulation during product development with the aim of reducing physical testing. To be successful in applying MBD, engineers need to combine test and simulation throughout the product development cycle from concept design to system simulation, to component testing, and finally to field testing. To deliver on its promise the MBD approach requires predictive simulation models, and to be predictive, models have to be validated against reality. But how do you do that? And how do you do it efficiently? Also, how do you enable collaboration between test and simulation engineers? Can you do more than before with predictive models? Keep on reading to find out how to overcome these challenges.
Discover model-based system testing
Our mission is to provide you with a range of engineering solutions made to enable and optimally balance the combined use of test and simulation. We call this range of solutions Model-based System Testing (MBST) or also known as Virtual sensing. It covers a broad and varied set of solutions to validate functional performance using proven analytics and to perform attribute engineering on virtual models, on virtual-physical systems and on physical prototypes. We have prepared the below infographics to help you understand the 3 main categories defining MBST. If you are a Simulation engineer, “Test for simulation” is your gateway to the test world. If you combine test and simulation for real-time testing “Test with simulation” has solutions for you. And as a Test engineer, we provide solutions to use more simulation during testing in “Simulation for test”.

Let me now show you 2 of these MBST solutions that will make your life easier when applying the MBD approach.
Exploit the Amesim Sketch Viewer
We call the first solution the “Amesim Sketch Viewer”. It is part of Simcenter Testlab Neo. You can check in the picture below what it looks like for a servovalve system. It allows you to access your Amesim simulation results directly from a test environment by interactively using the sketch of your Amesim model. You can now import your Amesim data in a natural way inside the test environment. Once your data is imported you can use the extensive capabilities of Testlab Process Designer to post-process your simulation data with the metrics of your choice. You can also start correlating your system simulation models against test data. Having your simulation and test data in one environment enables you to process them using the same methods thus ensuring consistency during data analysis. You see, MBST is all about helping you in optimally combining test and simulation.
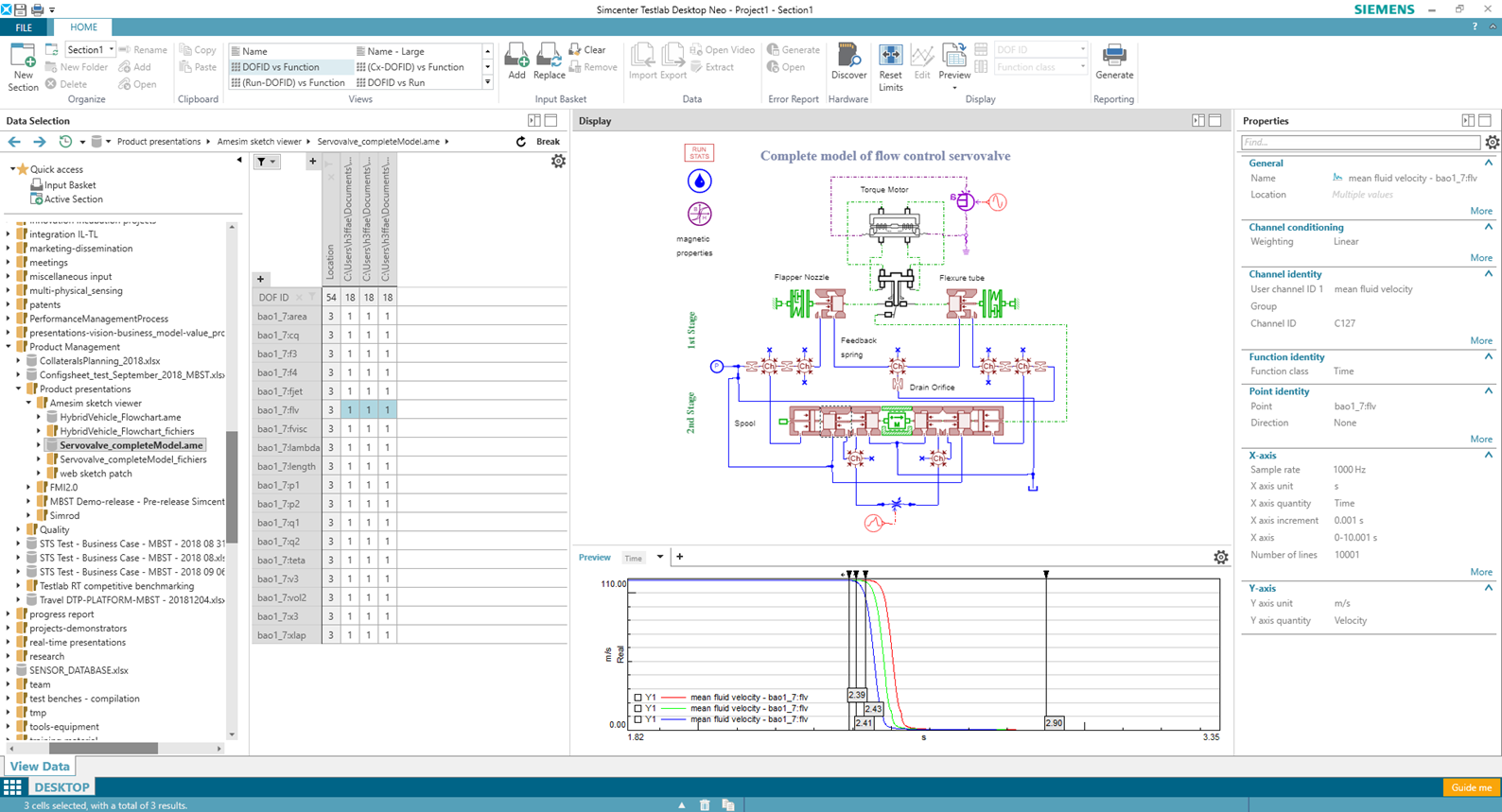
Explore FMI co-simulation
Now, the second MBST solution that I want to show you now brings simulation and test even closer together. Imagine not having to exchange huge data files anymore between your simulation environment and your test environment to correlate your models or to extend your test measurement with simulation results. This is what Simcenter Testlab Neo offers. Indeed, we have incorporated support for the number-one standard for model exchange, FMI 2.0 for Co-simulation. You can now embed simulation models using the FMI 2.0 for Co-simulation format in your test environment.
I let you have a look at the picture below to see how we integrate the support of FMI 2.0. Thanks to this support, you can now easily feed your simulation models with gigabytes or terabytes of measurement data for model correlation or for creating model-based virtual sensors. The sensor data feeding the models can for example have been acquired using the Simcenter SCADAS multi-physics data acquisition system. Once an analysis process containing embedded simulation models also called Functional Mockup Units (FMU) has been created, Testlab Neo will take care of running them and of making all simulation outputs available in the test environment. You now see how closely test and simulation can be combined together to ensure the efficiency of the MBD approach.

Learn more about model-based system testing
To conclude, the 2 MBST solutions that I present here are 2 concrete examples of solutions ensuring efficiency in your everyday work on MBD. They optimally combine test and simulation in a single environment. They also enable a higher level of collaboration between test and simulation engineers.
Do you want to know more about Model-Based System Testing? Visit our website for more information!
Do you want to learn more about the solutions presented in this article? Follow these links
Comments
Comments are closed.
Have Simcenter Testlab and Simcenter Amesim? Here are some tutorials to get started:
https://community.sw.siemens.com/s/article/Accessing-Simcenter-Amesim-Models-in-Simcenter-Testlab
https://community.sw.siemens.com/s/article/Simcenter-Testlab-Neo-and-Functional-Mockup-Interface