Unleashing the power of CFD to design a record-breaking model aircraft – Part 1
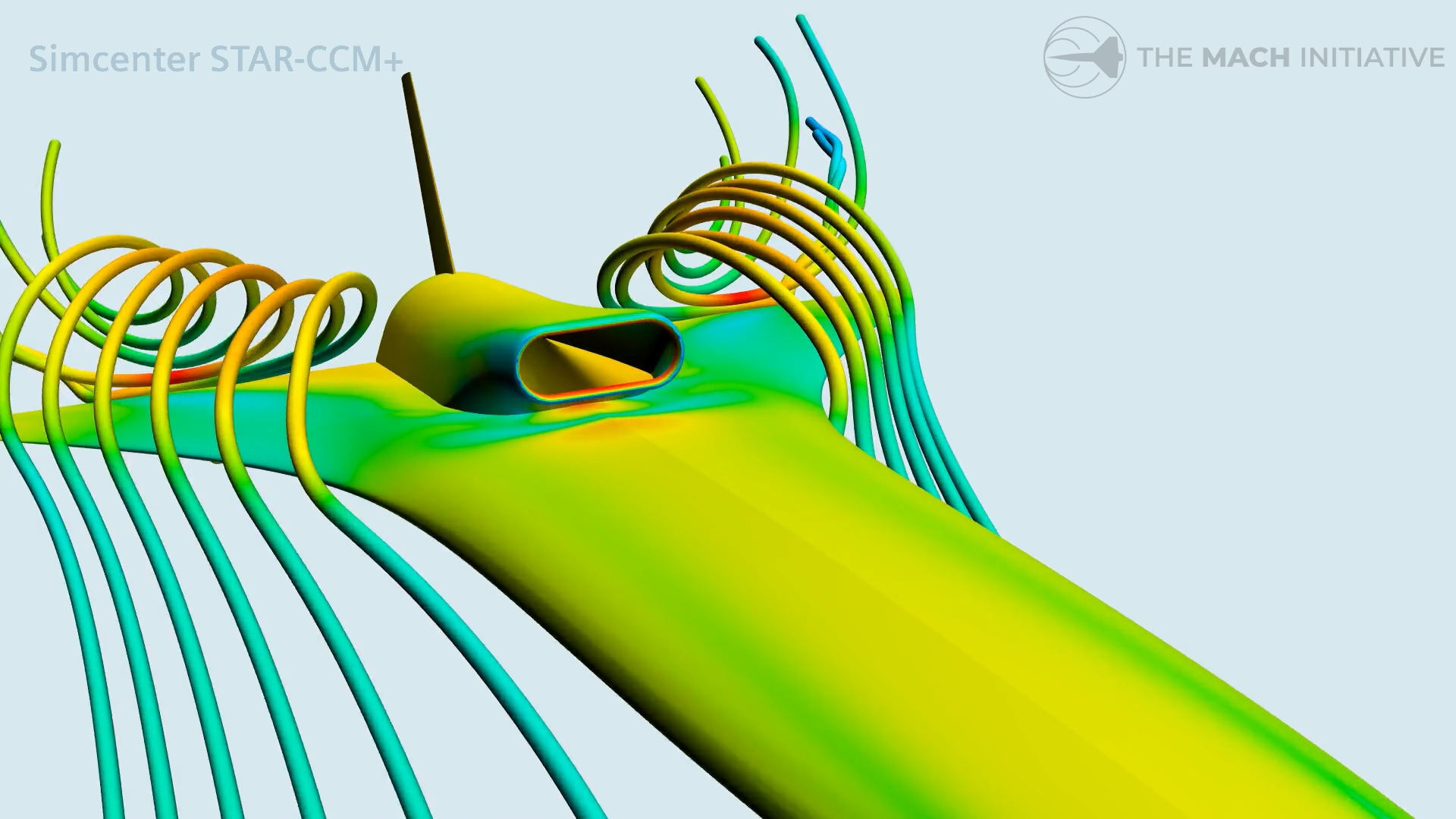
RC model aircraft design hobbyist
It’s an awe-inspiring video to watch, made even more impressive when you consider that the model aircraft was designed entirely by Niels himself Having been an RC hobbyist for over 20 years it’s not hard to see why Niels is the king.
RC model aircraft design is a mature hobby at this point. It’s well-known what works and what doesn’t, and over decades of experimentation and developing empirical methods, designing an aircraft that can fly has become a streamlined process. However, there are only a few aircrafts that have flown faster than 300 mph.
From an aerodynamics point of view, the looming threat of transonic flight begins to explain why record attempts are few and far between. The record is soon approaching the speed where shockwaves can start to creep into the flow, with unpredictable and often catastrophic results.
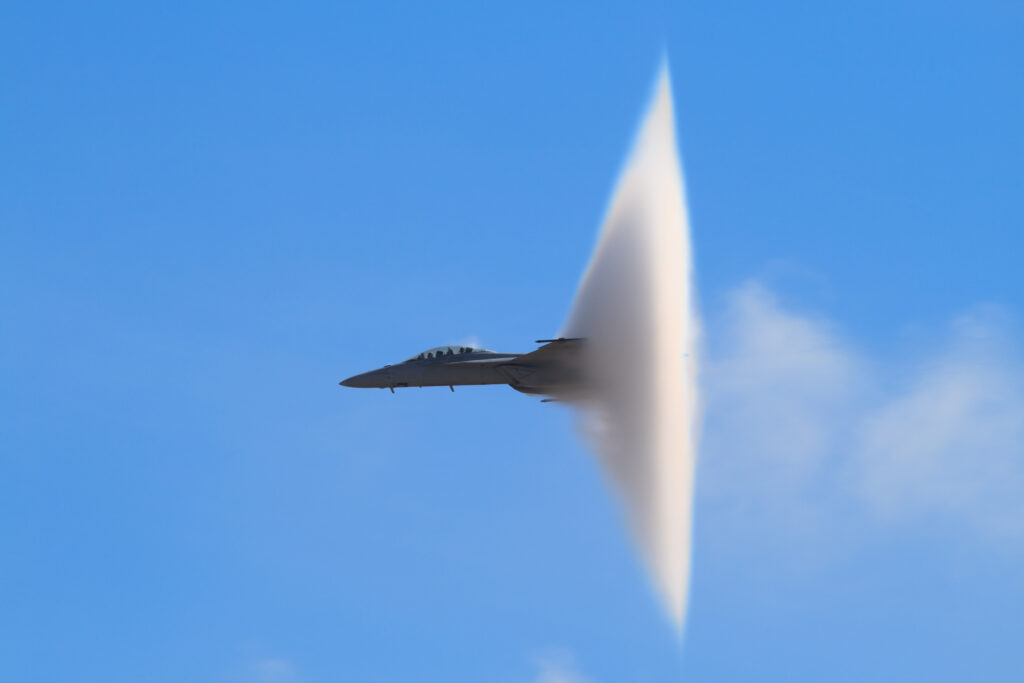
Perhaps it’s people not wanting to trust the familiar techniques in a domain where they’re unproven. Maybe it’s people not wanting to risk damaging expensive turbojets in test flights. Or could it be that people are just scared of the unknown?!
Using CFD from the beginning of your design flow
But what if there’s a way to get around all that uncertainty? Computational Fluid Dynamics allows aerodynamics to be considered from the very start, and hundreds or even thousands of experiments to be run without any of the cost, mess, and potential danger of real-world prototyping.
Consumer hardware and commercial software have made leaps and bounds in the last 20 years. Gone are the complicated user interfaces, the nightmare meshes, and the weeks of computational time! With modern software, is there a reason why, with a CFD informed design, a student team couldn’t break into the space?
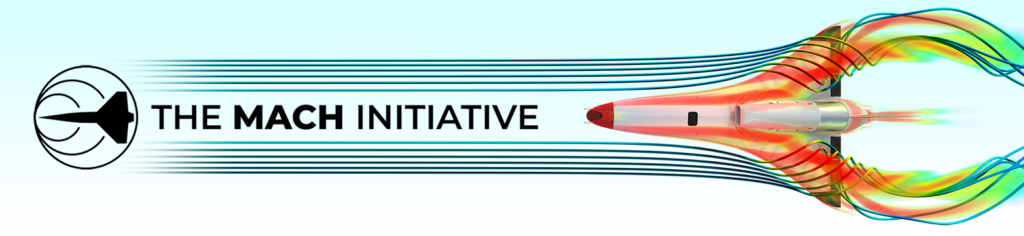
The Mach Initiative
With that in mind, in the summer of 2022 myself and a fellow student from the University of Bath founded the Mach Initiative, a student project with the goal of setting a new model aircraft speed record.
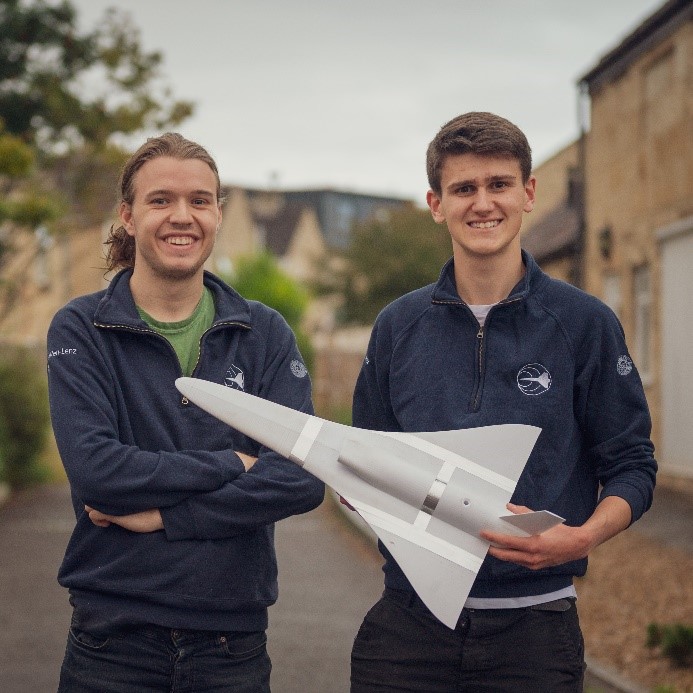
At that point, Dan and I were unsure of the full scope of the project – but we both knew that the first step was to acquire the software that would be paramount to our design. Luckily, Siemens were happy to help, signing a sponsorship agreement that granted us access to their entire Simcenter suite. Once the access was set up, I was giddy for days, just looking at all of the programs I had yet to try out – although granted I am a bit of a nerd like that.
Even with our first sponsorship under our belt, it was difficult to know where to start. While it needed to be an aerodynamically driven design – neither of us had the experience required to be able to predict what the structural and integration concerns might be. Things might look good on paper if the model aircraft is speedy, but if the elevons don’t work and the wing falls off, we might as well not have bothered!
Concerns about manufacturing, procurement, and logistics were even further out of sight.
Joining forces with the University of Bath
It was about at this point towards the end of 2022 that the University of Bath’s group business design project started looming around the corner. This would turn out to be our second big stroke of luck! If we could make it an official university project, we could get a bigger team!
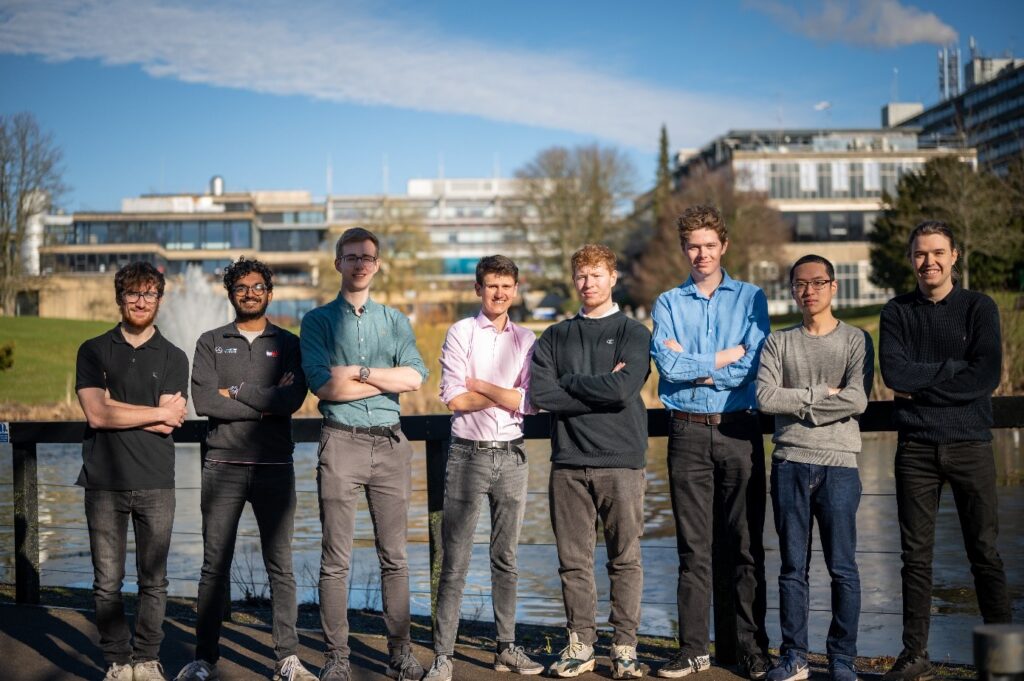
Fast forward to the summer of 2023, and that’s exactly what we did! The team has expanded to 8 members, signed a second sponsorship agreement with Callen-Lenz, and spent 4 months creating a prototype design.
The first prototype
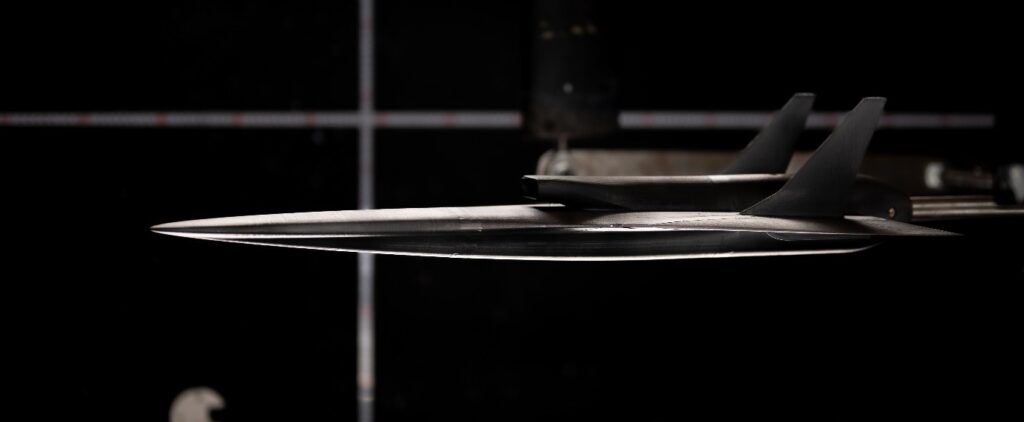
With a turbojet engine and an aerodynamic design that made use of both CFD and a valuable day of wind tunnel testing, the Kingfisher was born. And while I wasn’t sure about naming it after something that flies into the water, I couldn’t deny that it was catchy.
The design does have a few quirks that set it apart from the competition. The double-delta wing is significantly smaller than that of the competition, keeping our drag low and helping us push that Mach 0.8 target.
With a normal wing we might encounter issues with a blazing fast landing speed, but a double-delta wing is special, harnessing the leading-edge vortex to blanket the wing in high-speed flow, upping the lift generated and delaying stall to daredevil angles of attack. While delta-type wings are much more complicated and harder to model empirically than a standard wing, with Simcenter STAR-CCM+ on hand both the lift and the stability characteristics could be determined and de-risked just in time for our critical wind tunnel day, with superb results.
A second triumph in the design is the S-duct inlet. Jet engines are surprisingly fickle, give them too much airflow, or airflow that’s too turbulent and you run the risk of encountering compressor surge. If the airflow separates over the compressor blades, pressure waves ripple throughout the engine and fire blasts out of both ends.
It can damage the engine, it’s scary to watch and can be difficult to recover from. Therefore, designing an intake that can reliably slow high speed flow without inducing separation or turbulence is a must. An S-duct design is ambitious, but with both extensive CFD testing and planned experimental testing, we hope to have ironed out the risk.
Unique design feature
The eagle eyed amongst you may have spotted that, unlike on a fighter jet, the Kingfisher has the air intake on the top. Fighter jets have their intakes on the bottom because when they need high lift, eg. at landing, the angle of the fuselage can cause the flow to separate on top. And if the inlet is on top and sucks in dirty air, it could cause an engine flameout.
The Kingfisher however doesn’t have any landing gear, it lands on its belly on short grass. Common enough for RC model aircrafts, but with an air intake on the bottom it would suck in all sorts of plants and pebbles that would quickly destroy the engine. Our solution? Take off and perform the flight upside down, and roll around to right way up for landing. When your plane doesn’t have a pilot, there isn’t really a right way up!
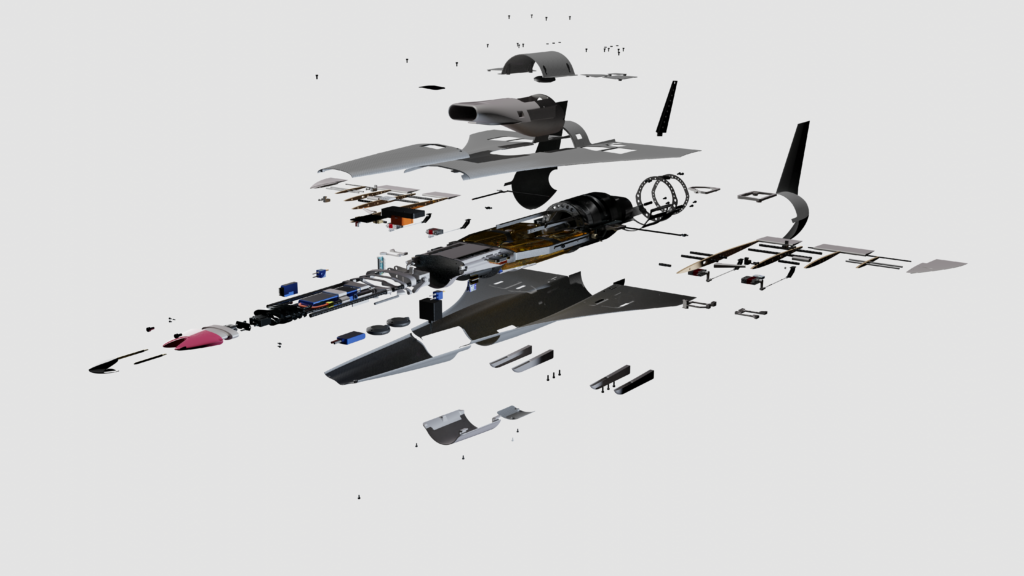
Manufacture and testing of a low-speed prototype has already begun, and once the university year starts, we’ll be able to begin the manufacture of the full scale Kingfisher just in time for our record attempt, in the summer of 2024.
Find out what happens in Part 2 of this blog … coming 2024!