Chengdu: ADAS lab to test and validate performance
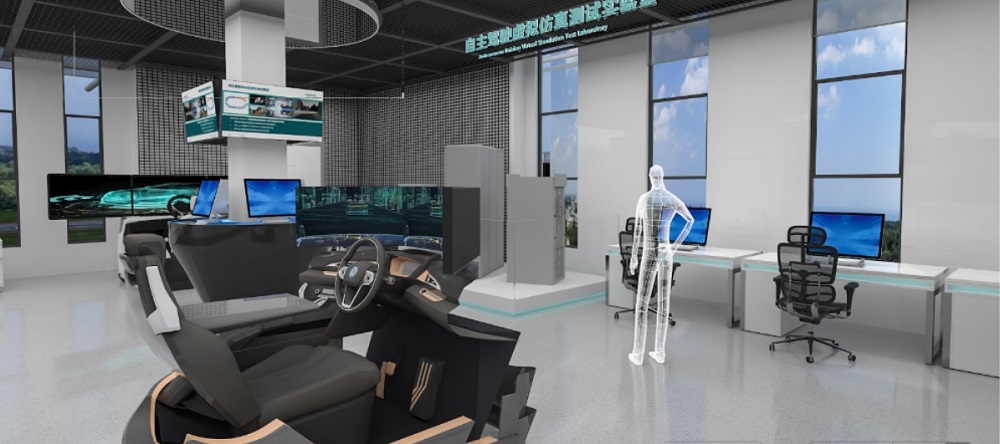
Where today meets tomorrow: building the future of automotive
Chengdu, a city of 16 million people located in Western China, bustles with innovation. When the Chengdu government decided to create an electrical and autonomous vehicle center, they turned to Siemens for support. Together, they embarked on this massive undertaking, poised to bring innovation, technology and the automotive industry to a whole new level in the region.
This engineering center brings the technology directly to the automotive industry. Visitors can see the comprehensive engineering solutions in action and get hands-on experience of what Siemens can deliver. The multiple disciplines offer real-world examples that customers can immediately deploy in their own development projects.
Siemens is not only helping to create this state-of-the-art facility but will have engineers and experts available to support businesses.
This blog series will focus on the many different aspects of the Chengdu AV/EV Engineering Center. It will give you a glimpse into how the advanced solutions are helping build next generation of vehicles. Chengdu is truly where today meets tomorrow in the automotive industry.
In this post, we will discuss the advanced driver assistance systems (ADAS) and various supporting labs.
ADAS and demonstrators
There are three demonstrators to support the development and testing of autonomous driving systems. The main purpose for the demonstrators is to thoroughly simulate and test ADAS controllers. They are:
- Hardware-in-the-Loop (HiL) for testing ADAS controllers in rapid prototyping environment
- Hardware-in-the-Loop (HiL) for testing ADAS controllers in final product testing environment
- Vehicle-in-the-loop (VIL) for testing the ADAS product within the actual vehicle
HiL rapid prototyping
At the very early design stage of development, the rapid prototyping environment solution plays an important role. It is used for testing a controller’s key algorithms against a large number of simulation scenarios.
For example, using the rapid prototyping environment, a real vehicle camera views a virtual world running on a screen. As the screen simulates the road, the camera sends that image to the rapid prototype platform. The perception algorithm is used to detect the lane lines in various conditions. The lane keep assist (LKA) algorithm processes the information on the LKA electronic control unit (ECU) and keeps the vehicle in-between the lane lines.
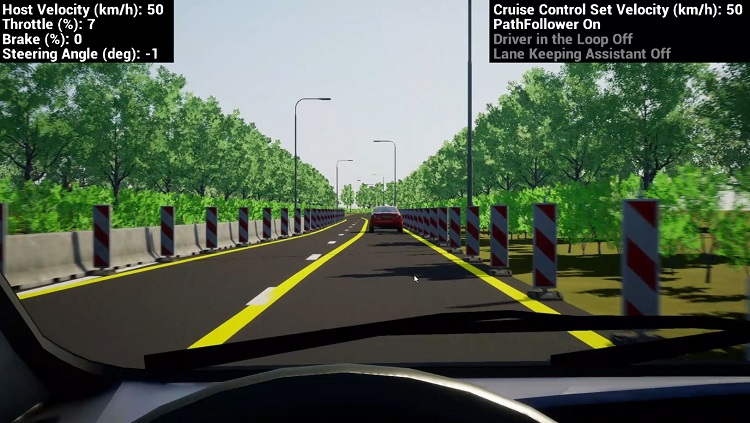
With sharp, brightly colored lane lines, the algorithm will deliver the correct information. In the real world, lane lines fade or may be covered with snow. As a consequence, they’re not always nicely defined shaped lines. The rapid prototyping environment can determine how the algorithm reacts in these outlier scenarios. Thereby allowing the design team to use the rapid prototyping environment solution to further optimize the algorithm. Additionally, it ensures to respond correctly to such wide-ranging conditions.
HiL subsystem testing
At this point in the design phase, the vehicle doesn’t have an ECU yet. This provides input and output over the vehicle CAN bus. Therefore, you move to the final product testing environment to incorporate a production-level ECU for the final subsystem testing. For example, the LKA algorithm block which was normally implemented as software on a general PC, will run in a dedicated LKA ECU with its own communication interface, attached to an industrial camera that has its own perception algorithm ECU.
ViL final product testing
Vehicle-in-the-loop comes after final product testing, where the algorithm on the production level ECU is installed in a real vehicle. It allows to experience real-life scenarios in a virtual environment, while the vehicle drives safely on an obstacle-free test track. Screens inside the vehicle display the virtual world to gauge the entire vehicle’s reaction to a pedestrian crossing, for instance. The sensors detect the pedestrian in the virtual world. Next, they generate a real signal on the compass of the car which is received by the brake’s ECU. If the vehicle is too close to the pedestrian, then the car will automatically brake. The automatic emergency brakes system engages, and the vehicle decelerates.
The VIL demonstrator ensures fast and reliable simulation with an intuitive graphical user interface. That makes it easy to pick and run a variety of scenarios. Although there is a live track for ADAS testing, the design team does not need real pedestrians or bicyclists. They can have the actual car ‘drive’ in thousands of scenarios. In just about any driving scenario imaginable, they generate outputs to determine if the algorithms, camera ECU and brake system all work as expected.
Setting up with Siemens Simcenter
The Chengdu government wanted to build an engineering center, for autonomous and electric vehicle, to showcase the latest technology. It is not just a display of future possibilities or visions. Instead it provides real-world capabilities which the user can immediately deploy in their development projects.
Visitors and potential customers can use this center to gain a competitive advantage needed to stay ahead in this market. For the Chengdu ADAS lab in particular, visitors see several steps of the overall development process. It shows how Siemens products and services help to validate ADAS algorithms in order to deliver safe and tested products.
Simcenter software, part the Siemens Xcelerator portfolio, forms the basis of all these setups. It ensures flexibility while providing advanced computational power to perform the simulations in real time. For developing the ADAS demonstrator, the Simcenter Engineering experts deliver advanced and innovative solutions by uniquely combining Simcenter Simulation and Testing tools. The AV/EV center provides popular systems like the lane assist system for final product testing along with vehicle-in-the-loop setups. Examples are adaptive cruise control and automatic emergency braking systems.
Check here our Engineering ADAS capabilities or read this interesting blog post on how to unlock orchestrated cluster-based simulation for large scale virtual verification.
The Chengdu ADAS lab – 5 years from now
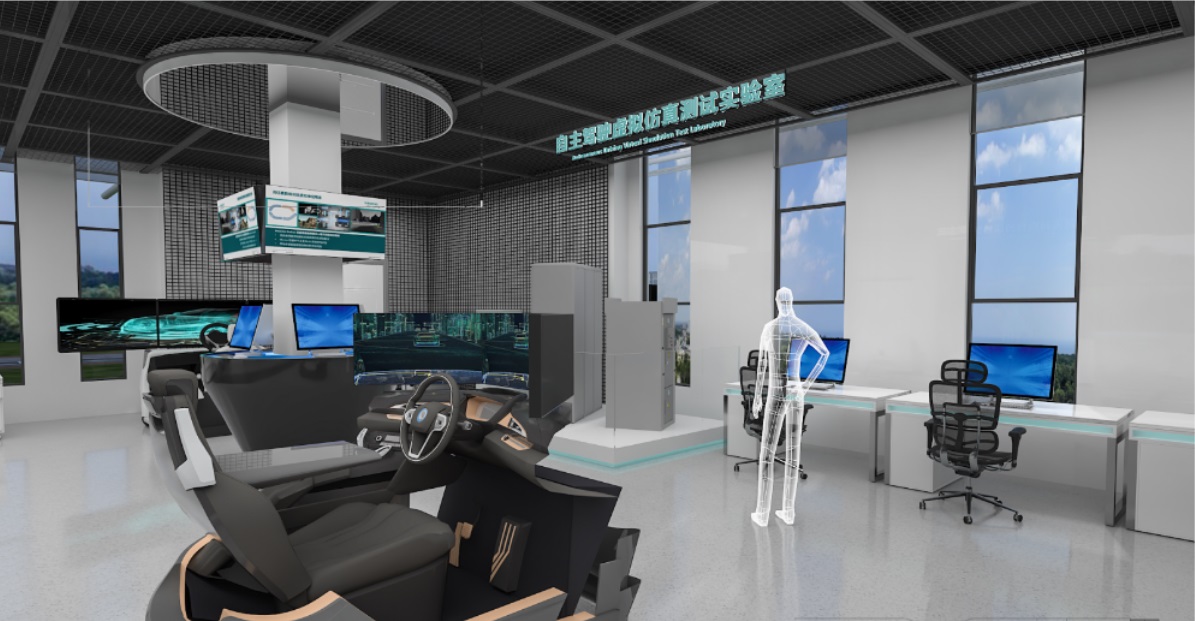
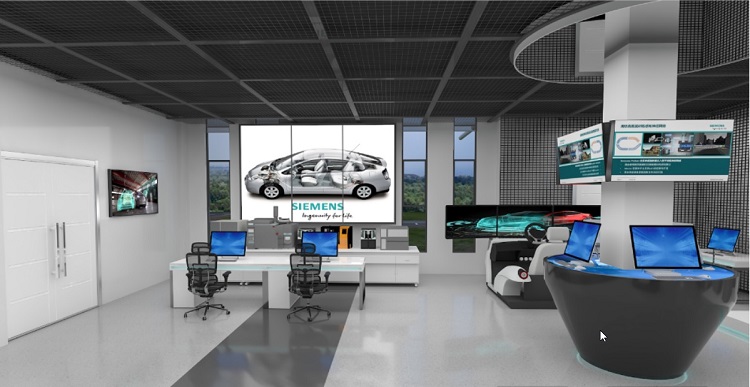
Both startups and larger car companies can use the Chengdu center’s technologies. However, startups will reap the biggest advantage because, for them, it provides invaluable hands-on experience. With these capabilities, they can quickly rethink and optimize their development approach and quickly deploy their technology solutions.
The center also includes the ability to set up tests and validate systems at their own companies similar to the ones shown in the Chengdu showroom. Due to these advanced technologies, the area, and the Chengdu ADAS lab, will attract companies starting their autonomous vehicle development. This in turn will hopefully enable the area to become a cluster and magnate for autonomous and electric vehicle development.
“The auto industry is one of Chengdu’s pillar industries. The Internet of Vehicles (Intelligent Connected Vehicles) is the future of vehicles,” the mayor of Chengdu stated. “Siemens boasts a long history of innovation and is a leader in this field. This is a massive step toward building Chengdu into the ‘Auto Silicon Valley’ and becoming a leading base for the Internet of Vehicles (Intelligent Connected Vehicles).”
Stay tuned for the next blog in this series where we discuss the vehicle center’s battery demonstrator.
A special thanks to the experts Raymond van Markwijk and Oliver Philipp for their insight and input for writing this post.
Want to know more about the project? Read first blog post in this series
Comments
Comments are closed.