Chengdu: battery simulation lab revolutionizes battery design

In the first blog of this series, we discussed the innovative new AV/EV Engineering Center in Chengdu, China. Next, we focused on the advanced driver assistance systems (ADAS) related solutions. It helps both OEMs and start-ups gain first-hand knowledge and support in advancing their technological capabilities. In this post, we will focus on the battery simulation demonstrator and how it can help electric vehicle (EV) automakers reduce development time considerably.

Building future batteries with modern, advance technology at the Chengdu battery simulation lab
The decision to build the battery design lab stems from the automotive industry’s evolution from combustion engines to electrification. In essence, the battery is the most important element in a car. Because all the components are electrified, an electric car is basically a battery with wheels.
That’s why battery research and optimization is critical, as it will lead to more reliable and robust vehicle electrification.
Almost everything in an electric vehicle revolves around the battery. And the battery transforms all of the components in an electric vehicle in ways which vehicle engineers don’t have previous know-how and experience. This means everyone is learning how to re-design the cars around the electric battery. The combustion engine had the luxury of 100 years of trial-and-error, but the electric car doesn’t have that. Now simulation is more important than ever.
On the basic level, vehicle engineers must refine the vehicle’s cooling and heating capabilities to optimize battery performance and durability. Doing so, they achieve maximum battery lifetime, while maintaining safety standards and requirements. Simulations can help predict the performance of the battery, with the goal of achieving as much accuracy as possible, as fast as possible, and with the shortest turn arounds.
Showcasing the power of simulation
At the battery lab in Chengdu, the feature solutions bring together accuracy and speed to the largest limit possible. It showcases the power of simulation for achieving optimal battery performance and durability. Specifically, the lab combines very detailed, three-dimensional physics-based simulation with one-dimensional capabilities that together. This delivers highly accurate, significantly faster simulation to support battery design space exploration.
The result is an extremely accurate simulation in a fraction of the time of traditional approaches.
Simulate 20 times faster
Here’s how that is possible. Usually, 3D simulations of the battery pack are executed based on multi-physics and computational fluid dynamics. To complete these, it could require from a few hours to days. This yields extremely accurate information about the underlying physics of the battery and its behavior that can then be exported into a 1D system-level simulation environment. From here, you can simulate very complex systems with many parts quickly.
Now thanks to the unique solution by Simcenter, you can merge the accuracy of 3D physics-based modeling with the speed of 1D system simulation. Then the overall simulation times can be improved by up to 20 times without sacrificing accuracy. Where one simulation alone typically took 7-10 days, with Simcenter technology it is now closer to four to five hours.
A better competitive advantage
It significantly reduces the time for simulation and achieving accurate results to give automakers a better competitive advantage. With nearly 500 companies developing electric cars and light trucks around the world, this level of speed and accuracy is critical as dozens of new start-ups focusing on vehicle electrification fight for competitive advantage.
At the battery level, the aspect that is of high importance is how to design all the different cells together while considering the heating. This means keeping the cells in the best environment, regardless of conditions outside the vehicle, such as extreme heat or cold temperatures.
Battery management is key
How do automotive manufacturers meet the challenge of putting all those cells together in a battery pack that will last long enough and be cost-effective? The consumer will not embrace vehicle electrification if they have to spend an exorbitant amount of money every few years to buy and install a new battery.
The battery packs, cooling systems and management systems must focus on making the batteries work smoothly within a wide range of possible negative effects on its durability.
This is what the lab focuses on — thermal distribution inside of the battery pack. As well as the different working conditions impacting the battery’s performance and aging.
Chengdu, known as the Silicon Valley of China, is the center of this dynamic.
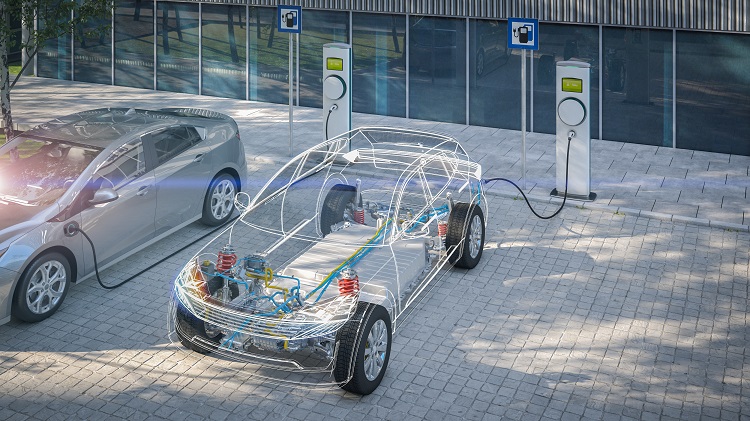
The next few years
The goal for the battery lab is to give engineers in the Chengdu area this kind of smart coupling between tools to help different teams or different departments of companies to work together. It delivers benefits in terms of shortening turn-around times and helping designers build batteries with much more efficient thermal management.
There are companies excelling in electrification, and traditional automakers and new startups struggling to keep pace. The engineering center and its simulation capabilities can help match and exceed the level of technological advancement of others in the industry.
Simcenter offers a wide variety of simulation and testing solutions. Getting the best out of this broad technology landscape requires the expertise of the multi-disciplinary team of Simcenter Engineering. Simcenter Engineering combined the power of Simcenter STAR-CCM+ and Simcenter Amesim to develop this advanced engineering process for battery simulation.
Stay tuned for the next blog in this series where we discuss the vehicle center’s multi-attribute balancing demonstrator.
- A special mention to the following experts for their insight and input for writing this post: Diego Davila, Peter Mas and Gaetan Bouzard
Comments
Comments are closed.