Digitalizing the semiconductor industry
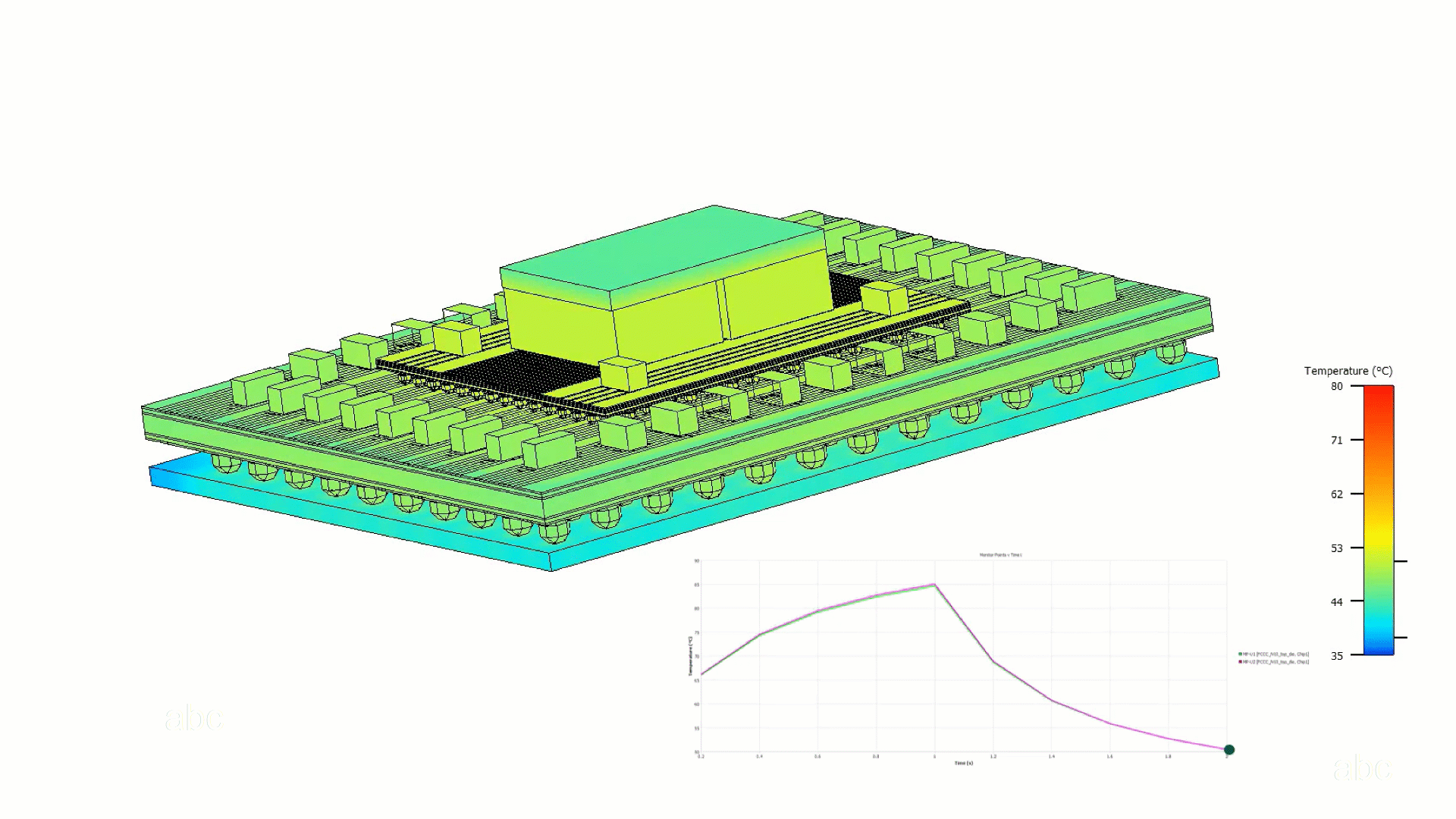
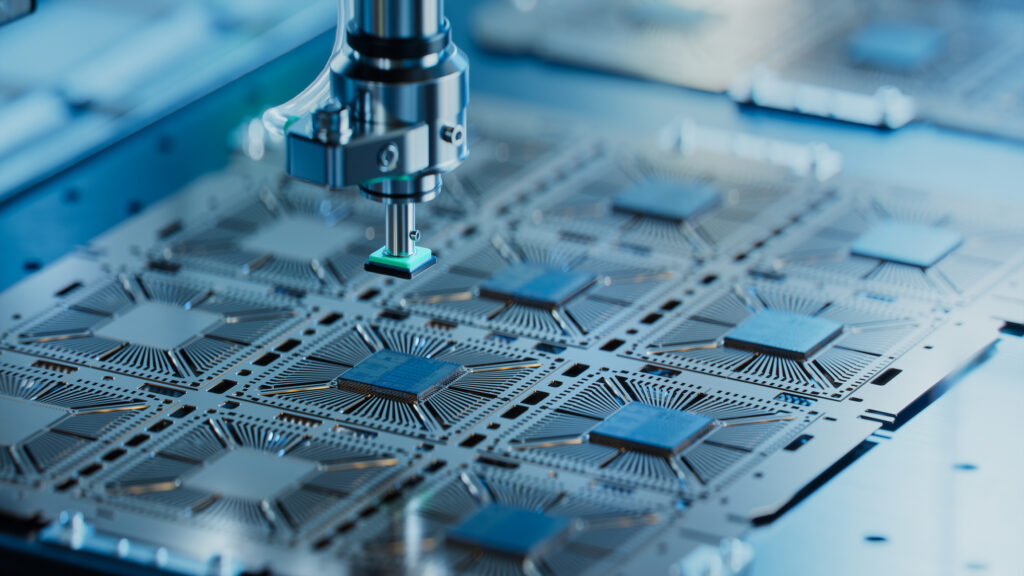
Why digital thread engineering and simulation are vital in shaping the next generation of semiconductor devices
The semiconductor industry has long been governed by Moore’s Law. This predicts that as technology progresses, every year or two, integrated circuit boards will shrink significantly while incorporating more and more transistors. This has been vital to technological advancement as they are so prevalent across electronic devices.
However, we have now reached an economic limit to that progress. The facilities required to maintain the pace of improvement are expected to cost tens of billions of dollars.
This is out of the reach for many companies so many manufacturers are becoming much more focused on the types of products they’re producing. They’re also looking at how to improve manufacturing processes to reduce build time and keep costs down.
The answer lies within the adoption of digital thread engineering. But what exactly does that mean?
What is a digital thread?
David Corey, Siemens Digital Industries Software Vice President for Semiconductor, describes a digital thread as “a collection of products or services that accomplish a specific subtask in the overall enterprise”. This begins with data about the requirements of the end product and ends with the verification and validation that these requirements have been met.
The increased complexity of semiconductor devices means that optimizing development now requires full product lifecycle management. But this has been difficult as most of these systems were invented for the automotive and aerospace industries. These involve designing thousands of parts and combining them to make a vehicle or airplane. With semiconductors you start with one wafer which you then use on different integrated circuit boards for different products.
There may be a thousand process steps in manufacturing the wafer, then another hundred or so in the assembly testing. This means a huge number of variables. And as companies strive to continue the improvement of semiconductor devices, they are trying out alternatives to silicon such as silicon carbide and gallium nitride – even more variables and data to deal with.
To manage this efficiently and effectively you need a way to control the master data. This is why Siemens has created a new lifecycle management system specifically for semiconductors.
Semiconductor Lifecycle Management
Within a digital thread is data for the design of every individual component that makes up the product. It also contains the data that shows that it will fit into the device it is being designed for and will perform effectively. For semiconductor devices, this means thermal stress analysis, mechanical simulation and vibration. It actually requires several digital threads to effectively manage the data – one each for integrated circuit design, package design, printed circuit board design and manufacturing.
But these threads need to work together, and this is where simulation comes in. In the past, each of these elements have been developed in separate silos by teams working independently. By the time they come together, redesigning significantly is difficult and expensive. According to Andras Vass-Varnai, a Siemens expert on electronics simulation, there is an antidote to this. Simulation allows teams to work much more closely together throughout the process. Virtual models are much easier and cheaper to build than physical prototypes, so these can be regularly updated and tested, and validated alongside each other. To do this you need to have a system that manages your data and ensures everyone is working with the latest designs.
Multiphysics simulation
The Simcenter portfolio enables multiphysics simulations throughout the design process such as power and signal integrity, and thermal and mechanical stresses. Of course, if you improve one area of the overall performance you may make another worse. So, workflows and automation are included within the software that help engineers reach the optimum design of each component in the most efficient way.
Without this integration, manufacturers must constantly import and export designs from one system to another, with multiple opportunities for human error along the way. And if you get to the end and the device isn’t mechanically viable you need to start again. A digital thread eliminates all this importing and exporting by having data flow seamlessly between products throughout, so the latest designs are always available.
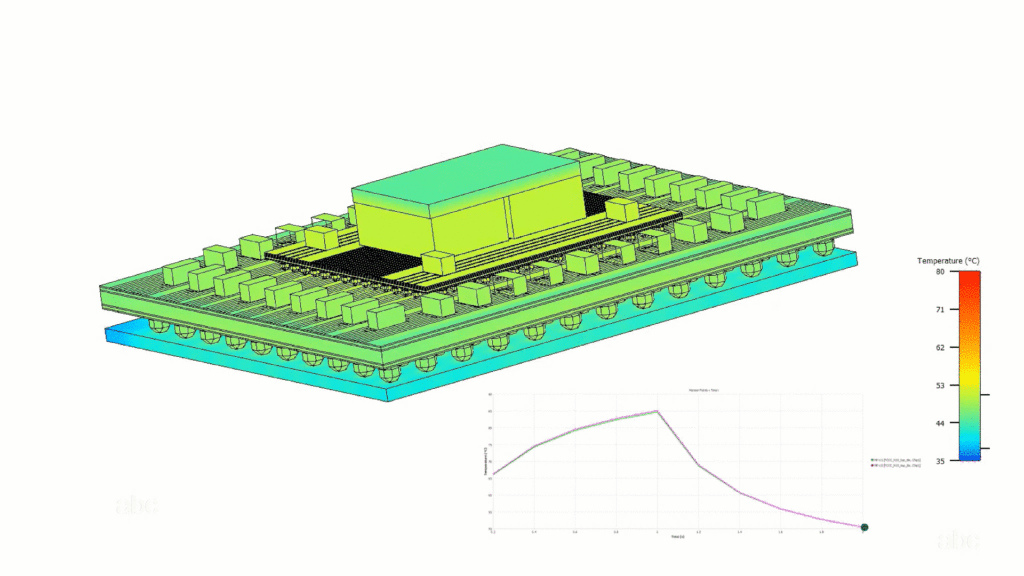
The industrial metaverse
When the term metaverse was first coined, it conjured visions of people escaping the real world to a virtual utopia. Like something from a dystopian science fiction movie. But the industrial metaverse is far from this. As Siemens’ CEO Dr. Roland Busch explained in the CES 2024 keynote speech, it’s about “redefining reality and transforming the everyday for everyone.”
The digital thread and simulation within it are part of the industrial metaverse – a virtual world where products of the future are created. By combining simulation with virtual reality headsets and sensors, design engineers will soon be able to sit inside the vehicle or product they are developing and interact with all the components that make it up. What better way to optimize design than to test the user experience before it’s built?
For a deeper dive into the importance of digital thread engineering for the semiconductor industry, watch our webinar featuring David Corey and Andras Vass-Varnai.
And if you want to discover more about the industrial metaverse and how it will shape the future, watch the full Siemens CES 2024 keynote speech here.