Durability: Isambard’s great quest to predict loads for a strength & fatigue analysis
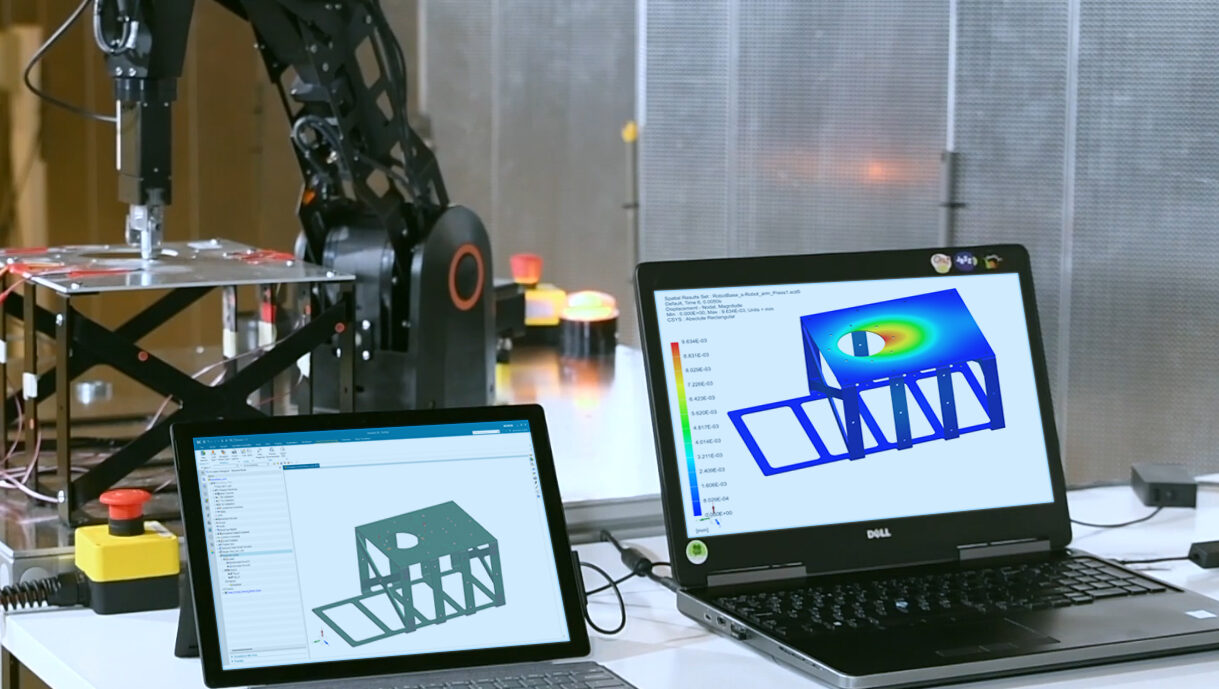
Full integration of strength and fatigue with finite elements and loads prediction
Isambard’s next hurdle
Accurately calculating the loads for a strength and durability analysis can be a challenge for any engineer and our friend Isambard is no exception. He has continuously benefited from being an early adopted of tools like the Simcenter 3D
Strength and Durability wizard since first starting his career and then going on to become a team leader, so how does he get accurate loads for his strength and durability analysis?
When standards just aren’t good enough
Having settled down in his job as durability team leader, Isambard is still keen to improve the processes and results that he and his colleagues achieve.
In many cases the loads that are applied for durability tests and simulations are derived from industry standards and have hardly anything in
common with the real loads acting on the structures. Isambard decides to investigate how colleagues and engineers in other industries approach this problem.
Durability guidelines and climbing mount stupid
Recently he had a video conference with his German colleague Ann-Christine who has been using durability guidelines to certify bottle machines. She explained how she is using a full multi-body model of the machine to predict the loads. She mentioned that once the Simcenter 3D Motion model is set up, the Strength and Durability tool uses a ‘Flexible Body Event’ that connects, with just a few mouse clicks to
the Motion results. She believes this to be much better than industry standards, since it is related to the project she is working on. Ann-Christine suggested that Isambard check out the latest White Paper and Webinar from Siemens to help improve his process.

Finding strength in the valley of despair
Feeling inspired, he invited his team to discuss working with the tool. They were not as positive as he expected,
“but we won’t know what loads to use!”
was the initial concern, shortly followed by
“and I can’t measure the loads the sensors don’t fit.”
Rose cheeked from his embarrassment, Isambard exits the meeting perplexed. He got a little over excited and missed the obvious facts but the engineers at Siemens must have spent a lot of time creating these tools, surely they had considered the missing loads issue. “well,” he thinks “the easiest way to find out is to simply ask” and decides to call his Siemens contact
Falling for a digital twin
His siemens contact is all too pleased to hear from him and begins to talk about digital twins and executable twins. Failing to see the relevance, Isambard stops him mid-sentence “aren’t Digital twins more for optimization of production processes or to help maintenance engineers?
What has this got to do with simulating loads in R&D projects?” The Siemens reps gives a wry smile “I think it is time I introduced you to Simcenter 3D Smart Virtual Sensing,” he answers.

Getting smart with virtual sensing
The rep goes on “in a nutshell Simcenter 3D Smart Virtual Sensing combines physical test and simulation so that the testing gives you the loads that your simulations need to get started or updated when a parameter changes, and your simulation can calculate the loads that you are unable to directly measure.” Impressed but doubtful Isambard queries the rep “you mean it’s an FE model where you select a node remote of the input data to find the load at a different location?”
“oh no,” the rep responds “it’s much better than that.” he then continues to explain that using an FE model would take an age to process, so it could not keep up with real-time changes. This package uses a reduced order model so that it runs in real-time updating as the data comes in from the sensors. Alternatively, it could be run years into the future to predict how a part may eventually fail.
Simcenter 3D Smart Virtual Sensing
- Simcenter 3D Smart Virtual Sensing can estimate operational loads from a few strains gauge measurement combined with an FE model
- The operational loads in time serials can be further used for durability analysis to find the reason for fatigue
- The load estimation is fully integrated into durability analysis using the new smart virtual sensing event

Climbing to enlightenment from strain to operational loads
In order to understand the mechanism deeper, Isambard investigates and discovers that Simcenter 3D Smart Virtual Sensing offers a robust framework for load estimation and field estimation. It combines measurement from the real world and the FE model, to estimate operational loads and field status. The estimation framework is self-updating, any change of the system will be accommodated automatically thanks to the measurement connecting to the real world.
It expands the measurement from strain to operational loads, as the estimation framework takes FE model prediction to augment the test data. This is how it can provide operational loads in a very practical way yet maintain high accuracy, which is exactly what Isambard needs.

Simulation and measurement in perfect harmony
Most importantly, Simcenter 3D Smart Virtual Sensing can harmonize measurement and simulation data via an integrated data fusion method with a Kalman filter. It is different to simple inverse load identification from an FE model, as it provides much more robust estimation. The smart virtual sensing estimation framework compensates both simulation inaccuracies and measurement noises by intelligently weighting the contributions of measurements and simulations, so that high estimation accuracy is ensured.
In Addition to the interaction with the test data, the FE model and subsequently the durability analysis is streamlined with an integrated workflow, that has a straightforward implementation. Simcenter 3D Smart Virtual Sensing provides an end-to-end workflow, that starts with the calculation of optimal sensor placement to ensure a high-quality test, it then reads the test results and performs the load prediction.
The estimated loads are then passed to the Specialist Durability analysis tool though the dedicated Smart Virtual Sensing Event, that can carry out the full durability post processing analysis.
Isambard remembers the flexible body event that Ann-Christine told him about and thinks: “That’s what we need here!”
Knowing it’s always a great idea to look for the new developments in Simcenter 3D, he checks for the new features in the Summer 2024 release and finds that it’s already there: The Smart Virtual Sensing Event.

Who does it help?
With all his new knowledge Isambard sees a lot of opportunities to further profit from digital twins in the strength and durability area. He also learns that this Smart Virtual Sensing tool brings his simulation divisions and the data acquisition/test divisions much closer together.
To prep for a new an improved meeting where he hopes to do a better job of convincing others of the benefits of Smart Virtual Sensing event, he considers the possible user cases
Isambard’s Possible user cases:
- Measure loads at locations where it is not possible to mount a physical sensor
- Use acceleration and strain measurements to complete safety factor assessments and fatigue analysis
- Make use of the connection to Simcenter 3D Strength & Durability Wizard to simplify the processes of the points above
With renewed confidence, Isambard recalls his meeting and invites other teams to join. He demonstrates to them the post-processing abilities of the Simcenter 3D Specialist Durability Tool. As he explains, he notices that the engineers are actually engaging with the idea, he can almost see the cogs turning inside their heads.
As the meeting ends and the engineers go for their coffee, Isambard overhears some of the conversations. He is thrilled to hear that they are still talking about it. ‘I must be on to something’ he thinks to himself, even the guys from physical testing seem to be interested.
Cooking up success
Now he has the other engineers interested, Isambard lists down the actions needed to ensure the company gains maximum value from this new capability. He decides to create a cook book for his colleagues from test and simulation:
Step 1:
Find out, where to place the measurements using Simcenter 3D Smart Virtual Sensing Optimal Sensor Placement
Step 2:
Perform physical testing with Simcenter SCADAS and get the strain measurements with operational loads
Step 3:
Predict the operational loads by inputting the measurement results and reduced order FE model into Simcenter 3D Smart Virtual Sensing
Step 4:
Complete the durability study within Specialist durability by connecting to the Smart Virtual Sensing Event
Predicting the future
Many new applications can benefit form this new strength and durability integrated connection between test and simulation. However, Isambard has a feeling that this is somehow just the beginning. He recalls the rep mentioning failure prediction. He decides to investigate this further and discovers it is possible to export the whole model as an eXecutable Digital Twin (xDT), that can be deployed on real-time platforms. This allows him to preform real time estimations on loads and field status. If run the simulation on into the future he could also predict the future failure, thus he can estimate the remaining useful lifetime in real-time. He ponders the implications of this.
Currently his colleagues require the customers to agree to fixed schedules of maintenance because they don’t know the real usage of the tool. For many devices this typically leads to large safety factors to include the worse case scenarios. However, with this new simulation capability it is possible to monitor and understand the in operation damage accumulation offering new possibilities for predictive maintenance. This capability means it is possible to support and optimize maintenance mission planning by identify the remaining useful life, reducing costs while ensuring the reliability of the device during operation.

Summary
In this escapade, Isambard faced confusion, excitement, embarrassment, and gratification as he discovered the capabilities of Simcenter 3D Smart Virtual Sensing and its integration with Simcenter 3D Durability. With the new tools he and his colleagues are able to measure where physical sensors can not reach, find both the local load and field estimation, complete an analysis of safety factors, produce a digital twin and predict future failure in real-time for better predictive maintenance. Just like Isambard, contact your Siemens rep or click her to find out more.