Efficient wind tunnel testing for the Aerospace Industries
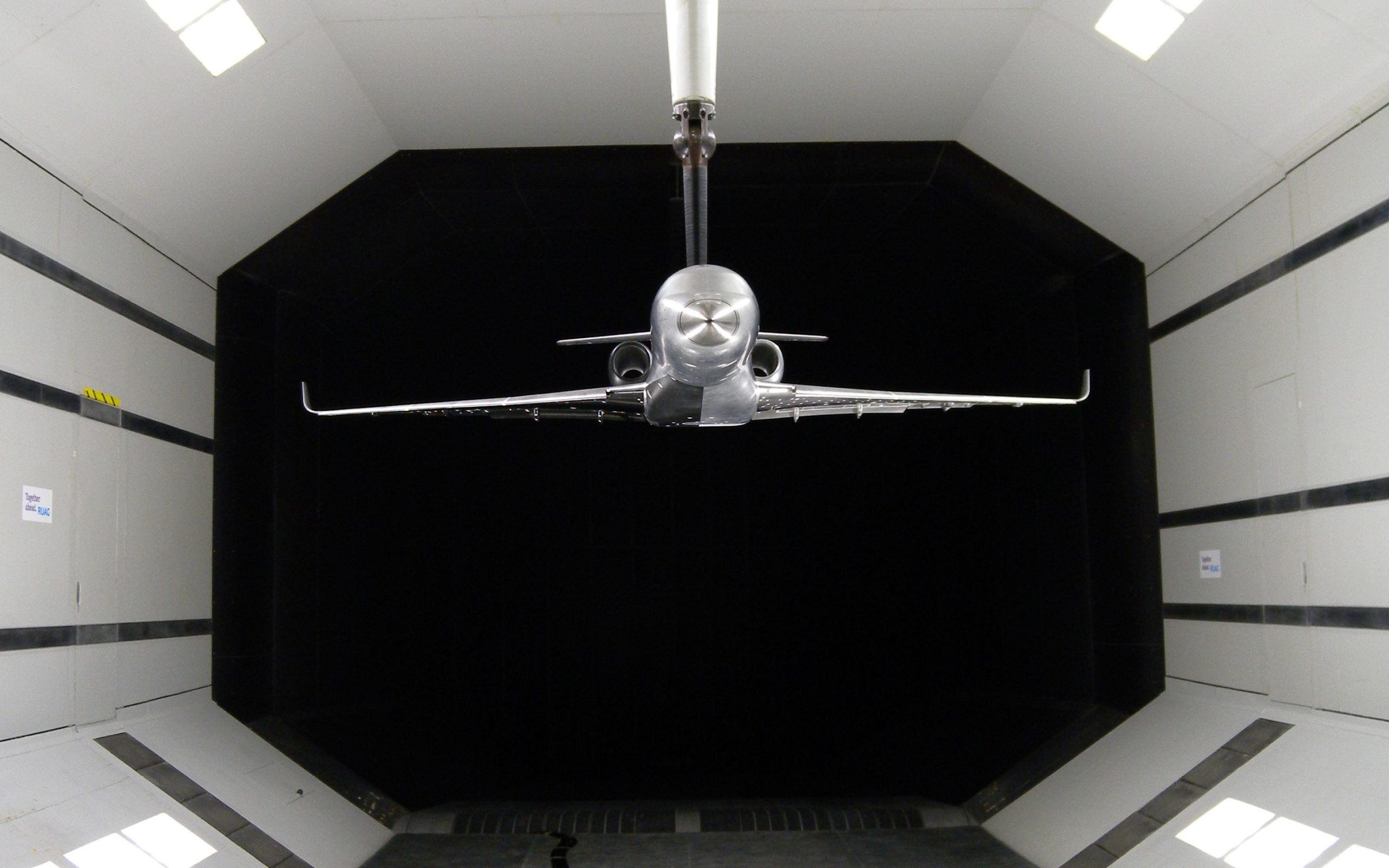
by Raphael Hallez
Trends in aviation involve a continuous pressure to increase performance, all the while reducing pollutant and environmental noise emission. And even with the industry’s recent efforts in aircraft noise reduction, airframe noise generated by landing gear, flaps, slats or other high-lift devices are still significant contributors to aircraft acoustic emissions, especially during approach and landing. Wind tunnel testing help investigate new aircraft concepts, verify performance of innovative designs, and validate prediction models.
Thanks to increasing computational power, more models are used in design phases, and wind tunnel testing is the ultimate way to validate these models long before the aircraft can actually fly. However, wind tunnel testing typically involves high costs linked to the preparation of the test item and operation of the wind tunnel and must be performed efficiently to get the most out of the limited testing time.
Siemens, in cooperation with its partner MicrodB, has developed a highly efficient solution for aeroacoustic wind tunnel testing. This solution allows detailed and accurate aeroacoustic measurements through its data acquisition system, the latest processing algorithms and customized acoustic array techniques. Measurements are best done in an integrated platform, where multi-physics testing, both for aerodynamics and aeroacoustics are conducted to gain the most insights possible into aircraft performance, and especially into noise generation mechanisms. Moreover, the productivity of the tests is of utmost importance and fast processing techniques are essential. Through smart data management and run comparison, many aircraft configurations can be tested and evaluated in a minimum time.
This is nicely illustrated in a measurement campaign performed at the RUAG LWTE (Large Wind Tunnel Emmen). An acoustic array with flush-mounted microphones was placed on the wind tunnel floor, about 2.4m from the aircraft model. This technique allows for a view of the source mechanisms to be obtained without perturbing the flow or the acoustic field of the source location. The Simcenter SCADAS high-speed data acquisition system acquired the pressure signals from the array microphones and pressure signals from kulite sensors mounted on the aircraft model to monitor aerodynamic performance. Simcenter Testlab software acquired aircraft position, aerodynamic data and acoustic data in a unified platform and with high synchronization accuracy.

A processing technique is used to analyze time delays between each microphone signal and reconstruct an acoustic source map of the aircraft for selected frequencies. With enhanced GPU-accelerated computing, the team obtained the detailed sound source localization results just a few minutes after the measurement, which allowed them to adjust the test plan on-the-spot and test the most relevant configurations. The source localization map provides a detailed aircraft image with the noise sources colored according to relative intensity.
This dedicated testing solution developed by Siemens combines the essential elements to provide higher efficiency and deeper insights for wind tunnel testing. As testified by the airframe noise senior engineer in charge of this test campaign, “The sound source localization technique developed by the Siemens and MicrodB team, together with the acoustic array provided by RUAG Aviation, proved to be very accurate. It allowed us to clearly identify complex aeroacoustic source generation mechanisms. These measurements provide essential engineering insight in the development of quieter and more efficient aircraft.”
Follow this free on-demand webinar to learn more about efficient wind tunnel testing.