Electric vehicle tire NVH: Solving the supplier-OEM puzzle
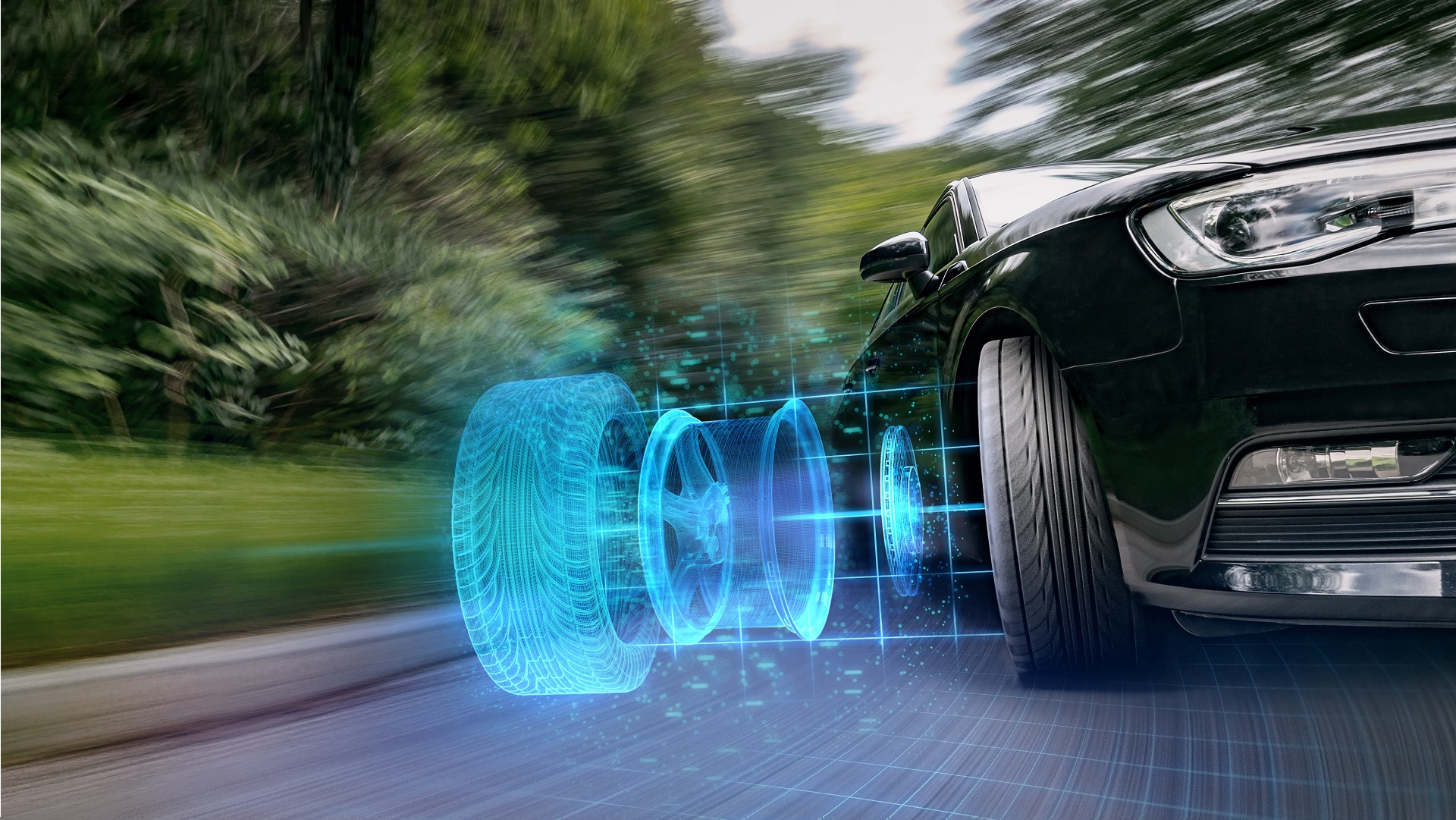
This blog post was co-written with Domenico Minervini, associate research engineer, and Jie Zhang, research engineer, at Simcenter Engineering.
Imagine working on a 1,000-piece jigsaw puzzle.
If you’re anything like me, you spent the better part of COVID lockdowns working on a countless number of puzzles (and then panicking when you finished one because what in the world were you supposed to do with your time now???).

Just as you’re about to finish, you realize that the last piece is from a different puzzle. You can try to force it in, you can try rearranging the other pieces to accommodate it, but the plain fact is that this piece was not designed to fit into your puzzle. It is one piece of a different, equally complex puzzle. In this other puzzle, your misfit piece would fit perfectly. But in yours, it does not fit at all because it was not designed with your puzzle in mind.
Disconnect between OEMs and tire suppliers
In automotive engineering, OEMs and their tire suppliers rely heavily on their Computer-Aided Simulation (CAE) models to predict performance of both overall vehicle systems and individual components. However, OEMs designed their models to fit in with OEM simulations, and tire suppliers designed theirs to fit with tire supplier simulations. These models are not suitable for direct integration due to their very nature.
OEMs use full-vehicle models that rely on lightweight, frequency-based tire descriptions. Conversely, tire suppliers need high fidelity time-domain simulation models in order to gain a comprehensive understanding of each tire’s unique properties, dynamics, and performance predictions.
The full exchange of models between the two parties is also difficult due to the confidential nature of simulation models.
However, the needs of tire manufacturers and of OEMs are directly connected. Both need to achieve accurate prediction of vehicle performance. Both parties have a stake in ensuring that the end user has a pleasant driving experience. Finally, both need to make sure that even though they are working on different puzzles, their pieces can still fit seamlessly and allow engineers to gain full insight into both part and system behavior.
Complexity of tire NVH modeling

In addition to integration issues with their OEMs, tire suppliers also face a challenge due to the nature of a tire itself. The tire is a complex system to describe and simulate for several reasons:
- High nonlinearities due to use of rubber (a nonlinear hyper-elastic material)
- Radial ply chords and reinforcements (non-isotropic structure)
- Presence of different thicknesses (non-uniform material distribution)
- Tread patterns (important source of excitation)
In addition to structural difficulties, the inclusion of operational effects due to rolling, preload, and contact patch deformation also contribute to modeling complexity for tires.
Rise of electrification
Additionally, the rise of EVs has delivered a new tire NVH challenge for suppliers. When an ICE vehicle is put in drive, the driver and passengers are hearing many sounds occurring at the same time: the pistons being forced up and down by tiny explosions, wind pummeling the windows and roof from the outside, and the drivetrain working to power the vehicle forward are all significant contributors of noise (if you’re interested in how all this noise has affected our world and human health, check out this blog post). These noises are all reaching the driver and passenger ears at the same time, making it difficult to distinguish where the noise is coming from.
With the advent of electrification and removal of the ICE, ICE-related noises are no longer present in the vehicle. This causes noise from other components to sound much louder to the people inside the vehicle. EVs are also much heavier than their ICE predecessors due to lithium-ion battery weight, which presents another challenge for part suppliers.
For tire manufacturers, developing and optimizing the tire NVH early in the development cycle can lead to significant reductions in time and cost to market.
Simcenter Engineering services has developed a unique model-test based approach to help tire suppliers solve these challenges. It combines a fast and adaptable conceptual model that is easily interchangeable between automotive OEMs and tire suppliers with a development procedure that targets both physical tire dynamic behavior and the patch to rim transfer, taking into account full-vehicle integration.
Generating an adaptable tire model
The Simcenter Engineering team’s Conceptual Tire (CT) model is set up in Simcenter Nastran and allows the user to easily and accurately model both the tire and the rim. It allows the user to create a profile based on similar commercially-available tires – it does not require any direct measurements.
Once the desired tire profile is achieved, the user has the option to increase or decrease the resolution of the mesh. The CT model then uses an internal meshing script to automatically generate a compatible mesh for the target tire. In order to maintain computational speed without sacrificing accuracy, the CT model makes it possible to link the same material properties in regions that are close to each other and have similar relationships.
The model-test loop

After setting up the CT model, Simcenter Engineering services executes two loops to compare the model’s behavior with that of the physical tire. The first loop is a modal-based optimization loop that evaluates the results of the modal analysis. The second loop is responsible for updating the virtual tire patch to rim transfer with the physically-measured one for different boundary conditions.
Engineers set up this process in HEEDS, which uses a proprietary search algorithm to search multiple designs and optimize the model. This reduces the time and computational cost of running simulations, as the user no longer needs to do this work manually.
These loops provide the user with much more detailed and accurate information than either test or simulation alone could. The customization offered in this model enables easy integration in full vehicle models and allows users to adapt or change tire design parameters to assess the impact on the full vehicle.
Tire behavior characterization in static and rolling conditions
To perform the model-test loop, Simcenter Engineering services developed a contactless test approach that enables engineers to characterize tire dynamic behavior in both static and rolling conditions. This is done using a scanning laser both on tire test rigs as well as full vehicle testing on the chassis dyno.


In order to test this technology, the Simcenter Engineering services team combined scanning laser Doppler vibrometry to characterize the modal behavior of the tire sidewall and accelerometer-based measurements to identify the patch to rim transfer.
Using this approach, the Simcenter Engineering team found that the correlation between test and software was highly accurate. Additionally, the team expanded this measurement approach, making it possible to use test to identify the operational phenomena that would impact behavior, including doppler effect, traveling waves, mode splitting, and more.

Electrification holds significant promise – both for our planet and for consumers. However, companies need to adjust their engineering methodologies and processes to account for the tire NVH issues that EVs now present. What if suppliers and OEMs could rely on one model that is easy to integrate into their existing simulations for tire NVH analysis? Simcenter Engineering services can help build such a model and integrate it into a company’s already-existing simulations.
To learn more about Simcenter Engineering services solutions for NVH, check out the resources below: