How to embed Executable Digital Twins into Physical Testing in 4 steps
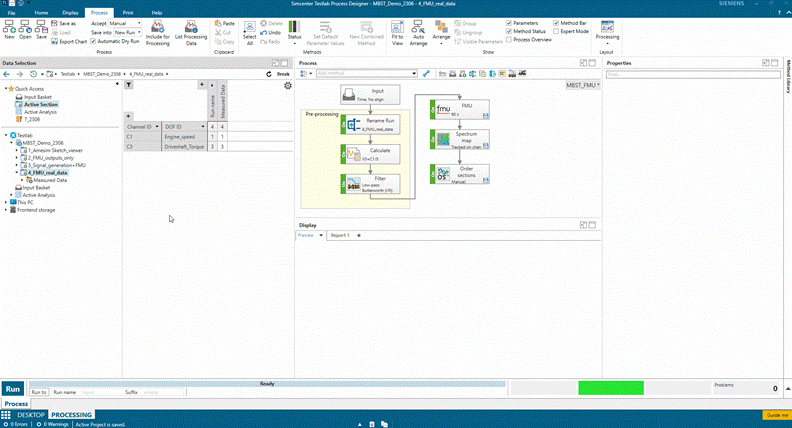
Executable Digital Twins (xDTs) will continue to dominate engineering in 2024. While the previous blog post explains the 5 reasons why, this blog post will get practical and dive deeper into how xDTs can be embedded into physical testing. We will look at how Simcenter Testlab Neo 2306 helps you to both correlate the predictions of xDTs and calculate engineering performance metrics with ease. xDTs simulating different types of physics such as mechanics, hydraulics, electrics can be used to cover the needs of different industries. So let’s proceed to experience how xDTs bring together the best of the simulation world and the physical testing world for all your Model-based System Testing needs.
The 4-step process
Simcenter Testlab Neo 2306 brings forward a new 4-step process for efficiently embedding xDTs into physical testing solutions. This process is meant to assist you in gradually moving your Digital Twins from their authoring simulation software to the physical testing software (Simcenter Testlab Neo in this case). Once inside the physical testing software, the Digital Twins can be executed (a.k.a Executable Digital Twin) to correlate their prediction, calculate engineering performance KPIs or augment physical measurements. This process helps you build trust that your Executable Digital Twins are providing you with the valuable system predictions you are looking for.
The 4-step process takes place in Simcenter Testlab Neo Process Designer. This powerful post-processing tool allows the calculation of engineering KPIs for both your simulation and test data. This enables easy correlation or extension of datasets from both xDTs and physical tests in 1 environment and with 1 set of processing parameters. Let’s dive together into how each step is done in practice.

Schematic of the 4-step process showing the methods to be used in Simcenter Testlab Process Designer.
Step 1: Start by accessing the simulation data in the Test environment
The first step in validating your Digital Twin’s accuracy is to transfer the pre-existing simulation results to the Test environment (Testlab Neo). This allows you to calculate any engineering Key Performance Indicators (KPIs) and the correlation KPIs of your choice. Thanks to the Testlab Neo drivers for simulation, the simulation data from Simcenter Amesim, Simcenter 3D, and many other simulation software are directly accessible without any intermediate data conversion.
The below video shows for example how easy and intuitive it is to access data from Simcenter Amesim models in Simcenter Testlab Neo.
Direct Simcenter Amesim model and data access through the Simcenter Amesim Sketch Viewer in Simcenter Testlab Neo
Step 2: Embed the Digital Twin in the Test environment using the original inputs
Step 1 quickly becomes cumbersome when you want to do parameter sensitivity studies or when the amount of data to be accessed is more than a few GB. You would have to make new simulation runs and re-import the data every time into Simcenter Testlab Neo. To avoid these problems, a better choice is to export the Digital Twin and embed them into Simcenter Testlab Neo, effectively turning them into Executable Digital Twin.
A widely used format to package Digital Twins is the Functional Mock-up Interface standard. Many simulation software vendors such as Simcenter Amesim, Simcenter 3D and Mathworks Simulink support this standard to export their models. The exported models are called Functional Mock-up Units, also known as FMUs. All software supporting the FMI standard can be found on their website. Simcenter Testlab is listed on the FMI website as both an export tool for State Space Modal Models and, more relevant here, as an import tool for FMUs from any compatible provider.
So, to embed your Digital Twin in Testlab Neo, the first step consists of exposing the variables of your choice as FMU outputs while keeping the rest of the Digital Twin unaltered. The Digital Twin inputs remain the original ones. They will be embedded inside the FMU and are therefore not being exposed as FMU inputs. Once the Digital Twin is imported in Testlab Neo, it can be parametrized and executed at will. The FMU outputs are saved directly (and only) in Simcenter Testlab Neo this time, thus allowing you to save many GB or TB of data efficiently. The FMU outputs are then used for calculating engineering KPIs or just to check that the same results as in the original simulation are obtained.
The figure below shows an example of how to expose FMU outputs in Simcenter Amesim.

Example of a Simcenter Amesim model with variables exposed as FMU outputs.
The below video shows a complete example on how to embed and execute a Digital Twin in Simcenter Testlab Neo using the method “FMU (outputs only)”
Example of the use of the method “FMU (outputs only)” in Simcenter Testlab Neo to embed Digital Twins only exposing their outputs
Step 3: Embed the Digital Twin in the Test environment and use synthetic inputs
Following step 2, the need to execute your Digital Twins with a variety of input data quickly arises. This means shifting from the predefined inputs in the FMUs to a wider range of inputs created in the Test environment. For that, the FMUs now need to expose their inputs to the Test environment. It is good practice to first use known, noise-free signals as input data as they allow you to further understand and explore the behavior of your Digital Twins in controlled conditions. Such input data can be generated for example with the “Signal generation” method available from Testlab Process Designer 2306.
A complete example for step 3 in Simcenter Testlab Neo is shown in the below video.
Example of the use of the methods “Signal generation” and “FMU” in Simcenter Testlab Neo to execute Digital Twins in controlled conditions
Step 4: Embed the Digital Twin in the Test environment and use physical measurements as inputs
The full power of the Executable Digital Twins is reached in step 4, in which physical measurements are used to feed the xDTs instead of internally embedded or synthetic data. This brings many new benefits to your engineering process. You can for example re-enact virtual scenarios in Testlab Neo which you previously measured in the field. The Digital Twin channels will be used to extend your physical measurements with virtual data to provide you the full engineering insight. Going a step further, you could change the parametrization of your Digital Twins and try out variants of your xDT. This way you can explore virtual variations of your scenarios or do sensitivity studies. And while you are at it, you could even have a Digital Twin of the next generation of your system and compare its performance against previous generations in realistic scenarios. In step 4, there is just so much you can do to engineer your system. I leave it to your imagination.
The below video shows you how to perform step 4 in Simcenter Testlab Neo.
Example of the use of the “FMU” method and physical measurements in Simcenter Testlab Neo to execute Digital Twins in realistic conditions
Correlation and engineering performance metrics
From step 1 to step 4, you need to process your system data (simulated or measured) to calculate correlation metrics or engineering KPIs. This is precisely what Simcenter Testlab Process Designer can support you with. It covers many of your post-processing needs for different engineering attributes such as NVH including Acoustics processing or Durability. For a demo, follow this link.
In a nutshell
Having Executable Digital Twins at your disposal in Simcenter Testlab Neo opens up many new opportunities to facilitate your work as a Test Engineer or as a Simulation Engineer. With Testlab Neo 2306, we bring you a new 4-step process to embed Executable Digital Twins in Testlab Neo with ease and confidence. If you are interested in reading about example use cases from the field, you can find an example related to the durability of shock absorbers here and another one related to the testing of wind turbine blade longevity here.
If you want to explore more ways of combining Test and Simulation, check out our Model-based System Testing solutions on our website.