Empowering Design Simulation in a Multi-CAD World
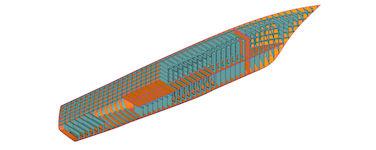
If it feels like your job is speeding up, you’re not alone. Engineers are a first-hand witness to the accelerated product development cycles manufacturer’s face today. While there’s a number of modern-day reasons for the need for speed, most of them come down to time to market. The first manufacturer to market, particularly with a new and innovative product, has a leg up on sales, marketing, and leadership.
While the product development cycle won’t be slowing down any time soon, a manufacturer’s commitment to quality certainly can’t be compromised. Products that fail to perform lead to recalls, change orders, and worst of all, damaged brands. Modern products need to operate correctly right out of the gate.
Engineers have found ways to speed development and ensure products performance. For this, they rely on one particular function: simulation. Such analyses allow engineers to predict how their designs perform in their operating environments. This includes engineering physics such as structures, excitation, fluid dynamics, thermodynamics and much more.
Running simulations, however, isn’t a snap. There are many challenges engineers must navigate along the way. One of those is working with designs from suppliers that come in a wide array of CAD formats.
Many Suppliers, Many CAD Files
Today, manufacturers of almost every size work with suppliers of some sort. And the simple truth is, companies that work with a lot of suppliers will be getting CAD models in many different formats. Sometimes it can seem like you have as many CAD formats to deal with as you have suppliers. That is, no two suppliers will seem to use the same CAD format. That’s just the reality today.
A manufacturer could dictate the format a supplier can use when doing business with the company, but that manufacturer is likely to have far fewer quality suppliers to choose from. Suppliers simply can’t keep any number of CAD applications in house, much less train their own engineers on the use of multiple files.
The bottom line is this: manufacturers have, and will continue, to get designs in a wide range of formats. They need to simulate those designs, despite the plethora of formats.
Working with Models in Many Formats
Given the modern reality of getting designs in many formats, and the need to digital check their performance, most manufacturers must find a way to rise to the challenge.
The first step is working in a simulation tool that allows users to open models from a wide range of formats. Sometimes, this requires opening models in native formats like Creo, NX, CATIA, Solid Edge, SOLIDWORKS, and plenty more. Other times, it means working with designs in neutral formats like STEP and IGES.
Regardless of how the model is opened, there will be a need to modify and tweak the design geometry. Most designs include small details that add complexity to the simulation model without affecting performance. Many users will simplify or abstract such small details away. The issue lies in making such changes. Models brought in through native or neutral formats lack features or parameters to drive geometry change. It is a simple solid. So instead, direct modeling capabilities are needed to make changes.
Easy Part and Assembly Analyses
In general, suppliers are responsible for ensuring their components meet the specifications laid out by the manufacturer. And those components must be tested. The component may meet the manufacturer’s requirements, for example, but fail when subjected to other circumstantial loading. That’s the big reason components must be simulated before they can be manufactured.
All of that, however, carries some implications for how the manufacturer simulates performance. They often will not need to conduct piece part analyses. Instead, they will place components in an assembly, define contact points between the parts, and run an analysis. Keep in mind that the parts in this assembly will often come from different CAD applications in different formats.
In this case, quick and easy assembly simulation modeling is critical. Automation in setting up contact is key. Automated meshing for assembly simulation is also important.
Recap
- It is simply a reality today: manufacturers are going to be getting models in a wide range of formats from their suppliers.
- While suppliers are responsible for the performance of their parts, they will not be able to account for all of the loading cases in higher assemblies. Manufacturers will need to conduct simulations to account for this fact.
- As a result, manufacturers will need simulation tools that can open models in a variety of native and neutral formats. They also need direct modeling capabilities to tweak such models, given they will have no underlying features or parameters to make changes.
- Assembly simulation modeling will also be a key capability. Manufacturers will need to pull together models in different formats into a single assembly, define contact between them, and quickly run assembly simulations.
The capability to simulate designs supplied from any number of CAD systems is key for today’s quick design cycles. It allows engineers to get to the important job: simulating the design, right away. In fact, engineers don’t need to think much about the CAD format used for the simulation. Their main job, simulating the model to ensure it meets specifications, happens quickly and smoothly.
Siemens PLM provides a range of capabilities that directly address the multi-CAD reality of modern simulation. For more details on how FEMAP addresses these needs, download our complimentary eBook.