Feel the (clean) burn

The heat is on
You don’t need me to tell you the planet is getting warmer. In my humble opinion, the biggest engineering challenge of our time is to convert the systems that have helped create the world as we know it into sustainable products. As an Application Engineer for combustion CFD I helped a lot of customers, across many industries, to simulate the burning of methane, propane, gasoline, diesel and more. Of course, the objective is always to use simulation to design efficient combustion systems that minimize emissions and maximize performance. However, for these combustion systems, Internal Combustion Engines, Gas Turbines, Process Burners the heat is on to reduce their carbon footprints.

Excellent design of combustion systems that burn fossil fuels can only take you so far. A large focus of engineers is now to adapt or design from scratch combustion systems that will burn alternative fuels such as e-fuels, hydrogen, or ammonia.
Ice, Ice Baby
Decarbonisation of the automotive industry is what I imagine comes to most people’s minds when considering the “clean up” of combustion systems. There are many articles and column inches discussing the long running debate between internal combustion engines (ICEs) and battery powered vehicles – check my colleagues blog on the matter from 2018! I will not add to that here (except to plug the fact that Simcenter STAR-CCM+ is the tool for designing both). Ultimately ICEs will be required moving forward for industries where batteries are not viable and if they can be run such that they produce negligible CO2 emissions, then they should form part of the mix in the future of transport.

Luckily, Simcenter STAR-CCM+ has been adding the tools to ensure that simulation can be leveraged to design such systems. And so, over the last few years, Simcenter STAR-CCM+ has been continually improved to allow for analysis of novel fuels and emissions.

The fuels proposed for use in In-Cylinder applications can have different fundamental reactive properties. One important example is Laminar Flame Speed (LFS). In Simcenter STAR-CCM+ you can directly calculate LFS for any fuel blend and use it with Flamelet, ECFM and Complex Chemistry combustion models. Below we can see an example of an ICE using a blend of Gasoline and Hydrogen as fuel, the simulation having been carried out using Simcenter STAR-CCM+ In-Cylinder Solution:
The methodology allows a quantitative prediction of raw emissions as a function of the hydrogen fraction:
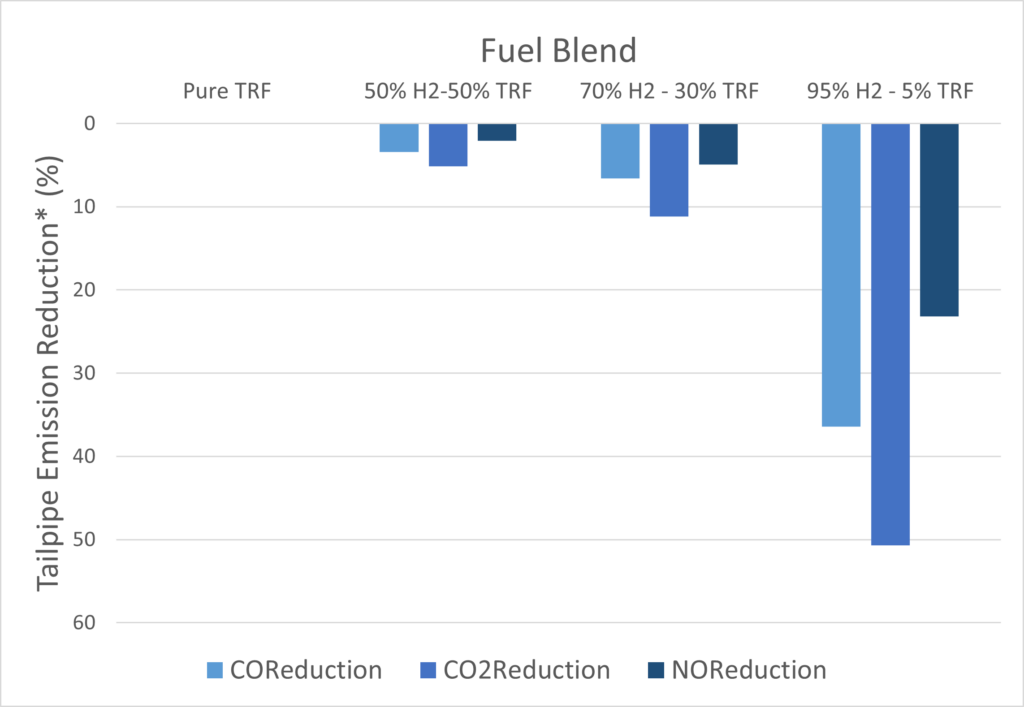
Rock The Boat
The marine industry is of course not immune from the need to burn cleanly. Maritime shipping is responsible for around 2.5% of all greenhouse gas emissions but is essential, as 90% of all the worlds goods are transported in this manner. While there may be use-cases where electrification is a viable approach, for large carriers, batteries (alone) may never be the solution. Engineers who design maritime propulsion systems are having to rock the boat of conventional fuel use and explore other (decarbonized) fuels during the design process.

One such option is the use of Ammonia. Ammonia can be burnt without generating any CO2 and is relatively easy to store, making it a good candidate as a fuel of the future of the marine industry. Once the logistics are sorted out (distribution, availability) for ammonia, it may be the number-one topic for internal combustion engine development for the foreseeable future. However, despite the potential, Ammonia has its own challenges, such as high ignition energy being required. For that reason, Ammonia can be used in conjunction with small amounts of diesel to kick start the combustion process. Ultimately this still provides a much cleaner combustion than traditional fossil fuel usage.
Simcenter STAR-CCM+ can be used by designers to understand this process. In the example below, Ammonia and Diesel jets at various injection timings and angles are studied.
For certain conditions, e.g. insufficient or too strong an interaction of the two fuel sprays, misfiring can occur. Being able to accurately simulate this reduces the need for extensive testing and allows for detailed understanding on how to design to avoid such a scenario.
Using the Complex Chemistry combustion model, excellent prediction of misfiring instances as well as regular combustion can be predicted.
How green is your sim?
Ok so I guess I can wrap the blog up there? Safe in the knowledge I have played a (small) part in bringing a tool to combustion engineers who can then go and do some proper engineering to design low / zero emissions systems? No! Most industrial CFD simulations are reliant on High Performance Computing (HPC) and crunching the numbers takes energy which inevitably carries its own carbon footprint.
Don’t take my word for it, this article from the British Computing Society highlights the challenge and states that CO2 emissions from HPC data centers is expected to grow 2-9 fold in the next 10 years.

The obvious course of action is to clean up the energy powering your CFD simulations, but of course that is most likely not in your control, and besides, it leaves me with nothing to do! With Simcenter STAR-CCM+ 2306, combustion engineers can now leverage GPU-native Flamelet combustion modelling. Leveraging GPU hardware allows engineers to run their simulations using significantly less energy, reducing emissions and costs, as well as typically getting your answer faster (a rare win-win-win).
So, let’s take a combustion system, in this case a pressurised annular combustor [1] and add some hydrogen to the fuel in order to reduce the CO2 emissions generated.
Great, but nothing in life is free, and I’ve spoken in the past about how the simple act of adding hydrogen can mess up the thermoacoustic stability of the combustion system. All is not lost as this system can be analysed using high fidelity LES combined with the Flamelet Generated Manifold combustion model to accurately predict the thermoacoustic behaviour [2]. And even better this can all be performed natively on GPUs.
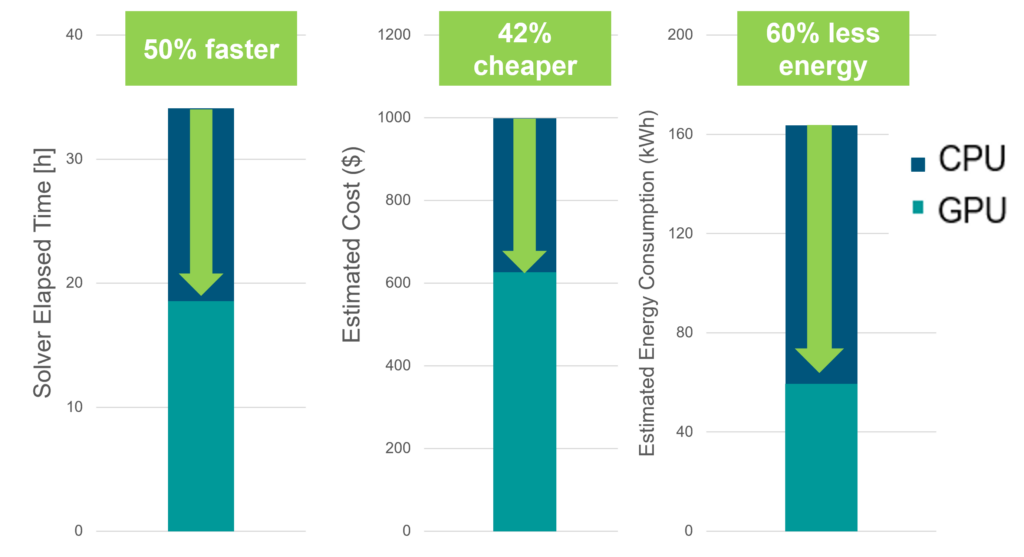
The end result is a solution a whopping 50% faster and estimated to use 60% less energy as well as being 42% cheaper. Even more importantly, the frequencies of the thermoacoustic instabilities generated due to hydrogen addition are also excellently predicted and can therefore be designed out or mitigated:

What we have here folks is a case of Simcenter STAR-CCM+ inspired carbon emission inception: we save on emissions whilst designing to save on emissions! And with that knowledge, now we can wrap up the blog!
[1] Thomas Indlekofer, Byeonguk Ahn, Yi Hao Kwah, Samuel Wiseman, Marek Mazur, James R. Dawson, Nicholas A. Worth, ”The effect of hydrogen addition on the amplitude and harmonic response of azimuthal instabilities in a pressurized annular combustor”, Combustion and Flame, Volume 228,2021,Pages 375-387,
[2] Jen Zen Ho, Sandeep Jella, Mohsen Talei, Gilles Bourque, Thomas Indlekofer, James Dawson,
Assessment of the LES-FGM framework for capturing stable and unstable modes in a hydrogen / methane fuelled premixed combustor,
Combustion and Flame,Volume 255,2023,112904,https://doi.org/10.1016/j.combustflame.2023.112904