Why Simcenter System Simulation is key for Hydrogen – Part 1
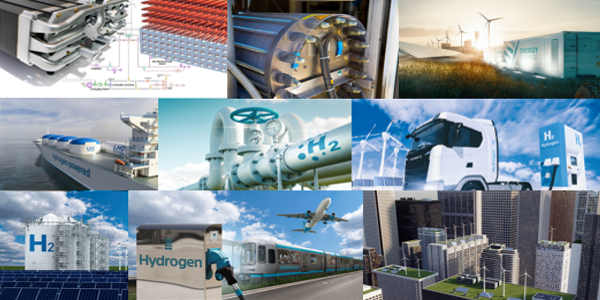
This blog post is the Part 1 of a blog series for highlighting how to predict and optimize the Hydrogen system performances with multi-physics and scalable digital twins thanks to Simcenter System Simulation. Additional applications are covered in the Part 2 for the Hydrogen production, distribution and storage. While another Part 3 is dedicated to the Hydrogen usage in Mobility (passenger cars, trucks, forklifts, excavators, airplanes, ships, railways, …) and stationary applications (hydrogen refueling stations, residentials, …). So that we’ll show you an extended view of all the capabilities you can benefit to reach your Hydrogen targets in your company, whatever your applications, in all industries.
Ready to succeed with Hydrogen in the Energy revolution (green, renewable, decarbonized energies)?
Clean Hydrogen marks an essential piece in the transition towards a more sustainable energy future. As the world seeks to decarbonize and energy consumption is projected to triple by 2050, the global demand for hydrogen is expected to grow fivefold by 2050. Contrary, fewer than 50% of organizations expect to meet decarbonization targets by 2030.
Customers tapping into the rapidly emerging hydrogen market face uncertainties on evolving technology, geopolitical strategies, multiple vendors and operation interfaces, high operating costs and challenging time-to-market. While Siemens is committed to support making hydrogen a business for its customers – future-proof, profitable and at scale.
We’ll introduce how Hydrogen applications ☀️ 🌬️⚡⛽ ☘️ 🌏 can be addressed with Simcenter System Simulation 💻📊⏱️through digital twins for performances, controls and energy management, up to connecting them to PLCs (programmable logic controllers) for Automation.

Building on our expertise in digitalization, automation and electrification we are dedicated to support our customers along their “hydrogen” journey and project lifecycle. So we deploy System Simulation into many segments to tackle all types of Hydrogen challenges. Especially with Simcenter Amesim since it includes by default the multiphysics components (gas, liquid, thermal, electrics, controls, mechanics, …) and platform capabilities (system integration, analysis tools, quick execution, coupling with 3D CFD or FEA, Reduced Order Models, …) for your Hydrogen digital twins. We identified these five segments that correspond to the usual Hydrogen sectors we’re familiar with:

Our tools cover everything from first pilots to scalable & standardized solutions including the generation of green electricity and grid connection, as well as hydrogen production, storage, transportation, and utilization in mobility or stationary applications.
Your digital twins with Simcenter System Simulation answer all your hydrogen questions
Paving the way to a profitable hydrogen economy at scale requires openness and collaboration across the entire ecosystem. With System Simulation, we enable customers to implement solutions easier, faster and at scale. Below are some key characteristics of System Simulation for Hydrogen:

We’ll show through various applications how Simcenter System Simulation can help transition to these new requirements in various industrial sectors.
Practically, it’s related to tackle many design requirements:
📐 Sizing and performances, from architectures to detailed components
📚 All hydrogen components (valves, pressure drops, …) available, from predefined libraries
💧 Real gas at high pressure with the right Equations of State (EoS)
🌡️ Thermal management, cooling
🎛️ Advanced control strategies like Statechart, PID, Model Predictive Control (MPC)
☀️ With Renewables like Solar photovoltaic or Wind turbine depending on weather conditions and GPS locations
🔌 Connection to the PLCs (Inputs / Outputs) and Hardware devices
⚙️ Automation and Virtual Commissioning
🩺 Virtual Sensing, Condition Monitoring, up to Health Management
⚡ Including power electronics (inverters, AC/DC converters, …) and micro-grids
⌛ Minimizing refueling/filling/performance time to few minutes (similar to fuels)
♻️ System efficiency (influence of compression, highest percentage %)
💥 Safety, no risk of explosion (operators, …)
💰 Cost effective (CAPEX/OPEX)
⏱️ With very fast execution for simulations running in few seconds of CPU-time
That’s a lot to manage. Let’s see how System Simulation can help there!
System Simulation is key to tackle the Hydrogen challenges!
System Simulation offers many capabilities to address all Hydrogen challenges:

More into detail, Simcenter Amesim and Simcenter Flomaster are reference system simulation platforms that can be used for many hydrogen applications in various industries:
- They include multi-physic libraries in an integrated environment to represent different physical domains as mechanics, electrics, fluids, thermal, … and all these domains interact all together in the same system simulation model
- Libraries offer multiple levels of model complexity: from 1D to 3D models, from functional to detailed geometry-based models, from quasi-static to dynamic models adapted to the specific simulations needs
- Simcenter system simulation also supports the control development by easily coupling high-fidelity physical models with control logics, in MiL (Model-in-the-Loop), SiL (Software-in-the-Loop) and HiL (Hardware-in-the-Loop) environments. The Automation Connect interface also makes it possible to couple a system simulation model with the PLC automation either as SiL or HiL environment in case you have an emulated PLC or a real PLC connected to the virtual model
- While many other interfaces exist to combine 1D system simulation with CAD, CFD or any 3D simulation softwares and Optimization tools.
While our wide engineering service experience, product vision and strategic partnerships are continuously driving the development of new capabilities and workflows.
Let’s transform the everyday together
We can see that all the Hydrogen applications combine multiple physics simultaneously, such as controls, fluids, thermal, electrics or mechanics. They are typically “mechatronics” systems.

There, a plant (i.e. physical) model is used as a physical and dynamic description of the full multi-physic system with power exchanges between each component.
Then, some classical design issues are addressed by system simulation, for instance:

- What is the best architecture for my system?
- What’s the best sizing for each component?
- What is the best control strategy for my subsystems?
- How subsystems interact together?
- How will the system behave considering multiple scenarios: actuation of a component, severe operating conditions, failure…
- Is there any risk of over pressures or temperature impacting safety?
- How much hydrogen can the system produce?
- How fast can I refuel a hydrogen tank?
- How much hydrogen or energy will the system consume?
That’s a lot of engineering pains customers face in their daily work that can be solved with System Simulation. Not only for Design (CAE) when computed on your laptop, the digital twins can also be deployed onto Hardware devices for “In Operations services”.
Reasons to use Simcenter System Simulation for Hydrogen
Let’s focus more on some other aspects of the benefits using System Simulation in an End-to-End perspective. From “Simulation for Design (CAE)” up to “Simulation in Operations”, System Simulation is actually used all along the V-cycle:

📐 A classical development cycle representation is the V cycle. Simulation can be used at various steps of this development scheme and needs to embrace several techniques and methodologies.
📊 At early design stages, Simcenter Amesim cand be used for system presizing and component requirement definition. At verification stage, Simcenter Amesim can be used for the complete system assessment and control testing. Keywords to recognize the addressable activities are Requirements, Co-simulation, Model-in-the-Loop (MiL), Software-in-the-Loop (SiL), Hardware-in-the-Loop (HiL), Reduced Order Model (ROM) or executable Digital Twin (xDT) once embedded onto the hardware devices.
🏭 Virtual commissioning is possible since Simcenter Amesim can easily couple with PLCs (programmable logic controllers) with the Automation Connect interface. So you can exchange data between Simcenter Amesim and the virtual PLC (in Siemens TIA Portal / PLCSIM Advanced) or directly with the real PLC onsite into your hardware systems or plants/factories. Coupling practically with SIMATIC S7 PLCs and supporting various communication protocols like OPC-UA, OPC-DA or Modbus TCP.

So at the end, you’re sure your Hydrogen system will be well designed at first sight, from a perspective of performances, controls, or energy balance. To finally significantly reduce your installations and operational dry-runs.
Well done! We can now better understand how System Simulation can help for Hydrogen applications to succeed in the Energy revolution (green / renewable / decarbonized energies).

Let’s switch to practical real use cases from industries to understand what it is.
Summary
In summary, embracing hydrogen in system/subsystem/component development requires a strategic approach, and advanced tools like physics-based digital twins to navigate the complexities and leverage Hydrogen as a competitive advantage.
The real application use cases introduced in the two other parts of this blog series give a good overview how Simcenter System Solutions can help to be successful when addressing your Hydrogen targets. Let’s now read the Part 2 of this blog series about the Hydrogen production, distribution and storage, also the Part 3 to get more info about the Hydrogen usage with Mobility (passenger cars, trucks, forklifts, excavators, airplanes, ships, railways, …) and stationary applications (hydrogen refueling stations, residentials, …).
Learn more about Siemens Simcenter Amesim
Simcenter Amesim is the leading integrated, scalable system simulation platform, allowing system simulation engineers to virtually assess and optimize the performance of mechatronic systems.