Going from hot and cold testing of engines to a robust end-of-line testing system for electrified vehicles
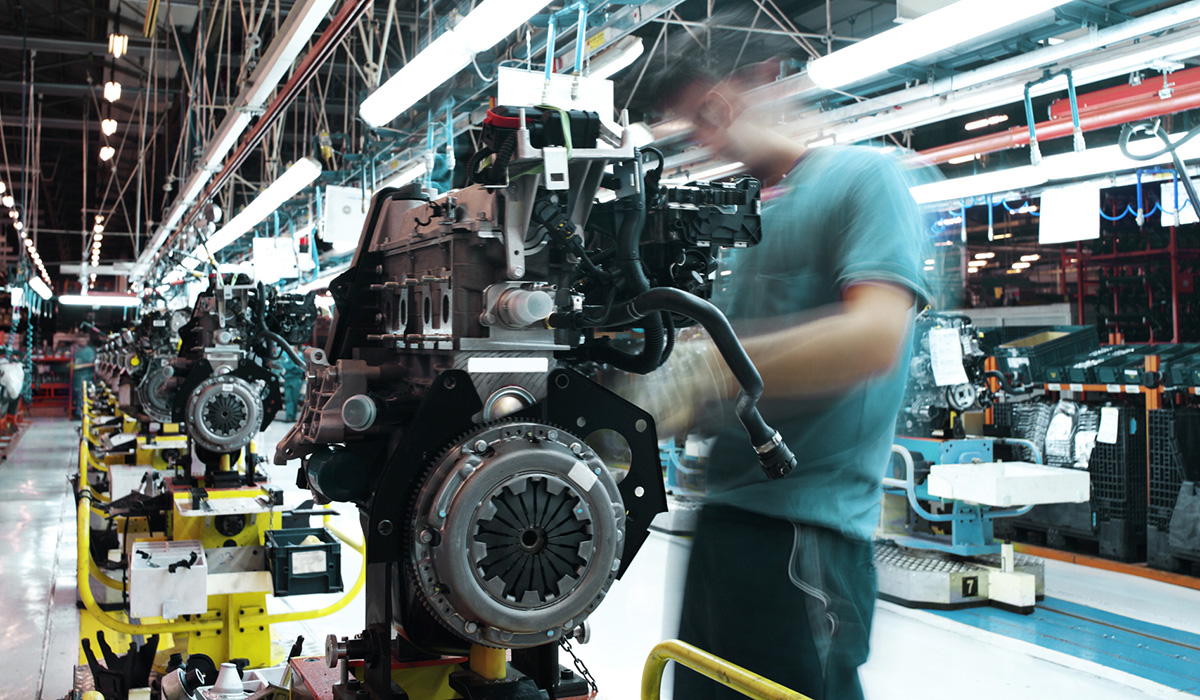
The current trend of electrification in the automotive industry challenges not only the development teams, but also the production lines and quality testing. While the ICE (internal combustion engine) production rely on the well-established hot and cold testing of engines applying vibration and sound measurements; assembly of electrified vehicles requires new advanced end-of-line (EoL) testing methods and standards.
Why? Electrified engines operate on much lower sound levels compare to ICE and can have faults prominent at higher frequencies, which consequently means that each production imperfection become much more audible. This fact diminishes the tolerance for imperfections. Put in other words, the quality testing standard become more stringent.

Seeking for powerful and reliable end-of-line testing
Spotting this need, Siemens extended its Simcenter™ portfolio with a robust and reliable industrial quality testing system, the Simcenter Anovis™ system, which can be easily integrated into EoL test benches and production lines. This system helps to deliver product quality at lower production costs while preventing outages and reliably identifying defects. Moreover, Simcenter Anovis is designed to provide valuable insights for further product advancements by indicating the possible root cause of problems, facilitating streamlined data transfer between manufacturing and the research and development teams.

The new Simcenter Anovis system compiles all required sensors registering large bandwidths, including vibration (accelerometer or laser vibrometers), sound (microphone), rotational speed (high-precision tachometer), temperature and torque. These sensors are coupled with accurate sound and vibration signal recording hardware.
In seamless conjunction with dedicated test bench control Simcenter Anovis software, it provides smart signal analysis to precisely perform pass/fail checks. The software enables users to analyze recorded signals based on smart methods operating in frequency, order, angle and time domain, and reliably detects relevant fault patterns. Statistical assessment procedures dynamically tune thresholds and turn it into a self-learning system, reducing setup effort and required expertise. As a result, the responsible team can deliver a formal report confirming the quality, meaning the part meets specifications and operates safely.
Advanced end-of-line testing methods for all powertrains
The Simcenter Anovis system has excellent process speed. The innovative sound and vibration-based fault detection algorithms in combination with automatic limit adaptations and classic NVH measurements enable the Simcenter Anovis system to detect product or process imperfection within seconds. It can be adapted to a broad range of automotive applications.
Simcenter Anovis system covers EoL testing and early damage detection using vibration and sound measurements for most of the automotive powertrain and steering components. Internal combustion engines can be examined with the automated cold and hot testing methodology both for diesels and petrol engines. Electric motors are inspected for quality with automated checks during production of electric drives and servo motors. Turbochargers are quality checked by order analysis at high-revolution speed.

Simcenter Anovis can be used for EoL testing for all types of transmissions – automatic, continuously variable and manual transmissions. In addition to the core applications related to the automotive powertrain, this EoL testing system, using the same methodology, can be applied to electric motors for small components. Although the vehicle interior is generally becoming quieter, acoustic testing of these components is growing in relevance. This also applies to parts such as modules for motorized drive mechanism like air conditioning units, seat structures and beyond.


Simcenter Anovis embodies decades of expertise in automated, proven NVH test procedures, providing OEMs with precise testing solutions requiring minimal time. Globally supported, Simcenter Anovis facilitates continuous process improvement by providing valuable insights for developing product and production digital twins.
Are you looking for more technical information? Check out this knowledge base article.
If you would like to learn more about the theory and mechanism of end-of-line testing more interactively, join us for this webinar: The concept and mechanism behind NVH-based end-of-line (EOL) testing. It’s a unique opportunity to meet the expert and raise your possible questions. Olaf Strama, the webinar host, who has more than 25 years of experience in this field, will be happy to answer them.
Mark in your agenda: May 5th at 12 PM CET.
Comments
Comments are closed.