High Accuracy Performance Predictions and Permanent Magnet Protection of Electromagnetic Devices

Designers of modern motors, generators, transformers, actuators and other electromagnetic (EM) devices are beginning to face challenging performance criteria for new designs which are beyond the capabilities of currently available commercial options. Developing designs with better performance and higher energy efficiency levels rank high among the priorities. Another key concern is to minimize Product Lifecycle Management (PLM) costs using robust designs with adequate safeguards against material degradation and the ability to operate under extreme environmental conditions.
Robustness has typically been assured by applying safety factors and/or through the over-design of devices to account for contingencies. However, as the industry requirements shift, the flexibility to over-design has become increasingly narrow, making it necessary to develop novel techniques that may be enabled by modern simulation software.
Most modern electromagnetic devices operate at fairly high efficiency levels already, ~90%. For robustness, design methodologies have evolved to ensure that reasonable levels of safeguards be implemented based on empirical data and best practices. Yet, opportunities remain to achieve greater performance and efficiency levels, and for minimizing PLM costs by considering novel materials and topologies as well as improvements to existing options.
A critical requirement for enabling these opportunities is developing material modeling capabilities in commercial software to provide accurate magnetic field values, machine performance parameters, iron loss calculations and predictions for material degradation under a variety of operating conditions. Recently, a number of features addressing these issues have been added to Siemens’s Simcenter MAGNET and Motorsolve software.
Improved Hysteresis Modeling and Iron Loss Calculations
The first major addition is the hysteresis modeling capability in Simcenter MAGNET. This is an improvement over the anhysteretic approach (which assumes an idealized single valued, symmetric B-H material characteristic). The anhysteretic approach has been the industry standard in commercial FEA based software because it provides a computationally inexpensive and practical solution to modelling the magnetic behavior of soft irons and their non-linearities. It, however, cannot model the true nature of soft irons which display hysteresis during their magnetization, demagnetization and remagnetization cycles. As a result device performance parameters including efficiency calculations are approximated in a post-processed step.
Simcenter MAGNET’s hysteresis solver can be used to model the time histories of magnetic fields, including minor loops (multi-valued B-H characteristics). As a result, higher accuracy field values, machine performance predictions and efficiency calculations can be made. In addition, a major advantage of this feature is that it does not require the user to provide material data beyond any that are typically supplied by material manufacturers.
A comparison of the effects of hysteresis modeling to the anhysteretic approach is shown in Figure 1. The Figure shows the magnetic field distribution, the output torque and iron losses calculated using both approaches for a traction motor, designed for the U.S. Department of Energy FreedomCar Project. The results clearly show differences between the two approaches.
It is important to note that the hysteresis solver can be computationally expensive. To improve the calculation speed, MAGNET’s current release uses multi-core processing capabilities which results in faster solutions of the order of nearly three to four times compared to its predecessor. This makes it possible to apply the hysteresis solver from early to later stages of design, ensuring that the most accurate results can be on hand as needed by the design engineer.
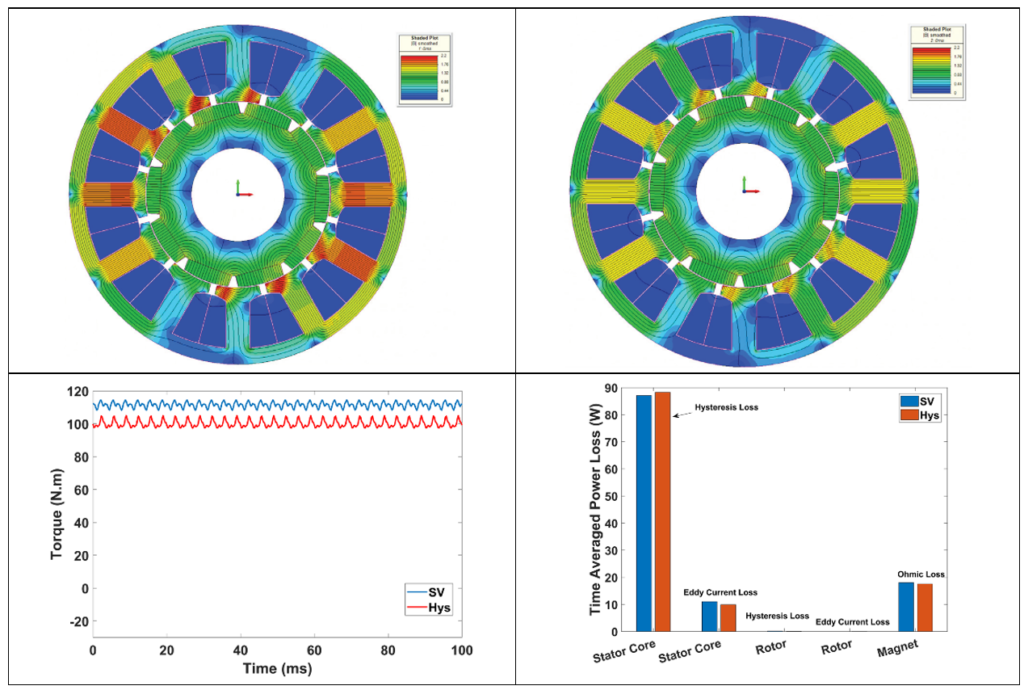
Another important improvement is the addition of iron loss calculation capabilities for design problems that can be solved using the time harmonic (TH) solver. This has greatly enhanced the utility of this solver for applications such as induction motors, transformers, etc. for which TH solvers are used frequently.
Improved Demagnetization Prediction
Permanent magnets are common in electromagnetic devices. The reliability of these devices are dependent on the magnets retaining their rated or expected strength throughout their life cycle. However, unexpected events such as surges in winding currents or elevated temperature due to machine faults may lower their remanence and coercivity, or worse, demagnetize them completely. To safeguard against this, it is important to be able to predict their susceptibility to demagnetization during the design stage.
In Simcenter MAGNET and Motorsolve 2019.1, a robust demagnetization model has been implemented for predicting the B-H characteristic changes of permanent magnets at various temperatures or due to system faults. The model can be used to identify hot spots or regions of a magnet where demagnetization may occur.
An example of the application of this feature is shown in Figure. 2. It shows the changes to the B-H characteristics of the magnet in an internal permanent magnet motor (IPM, similar to the Prius) due to the application of a short circuit both before and after the application of the fault. It also shows regions of demagnetization susceptibility of the magnets of the same machine at an elevated temperature.
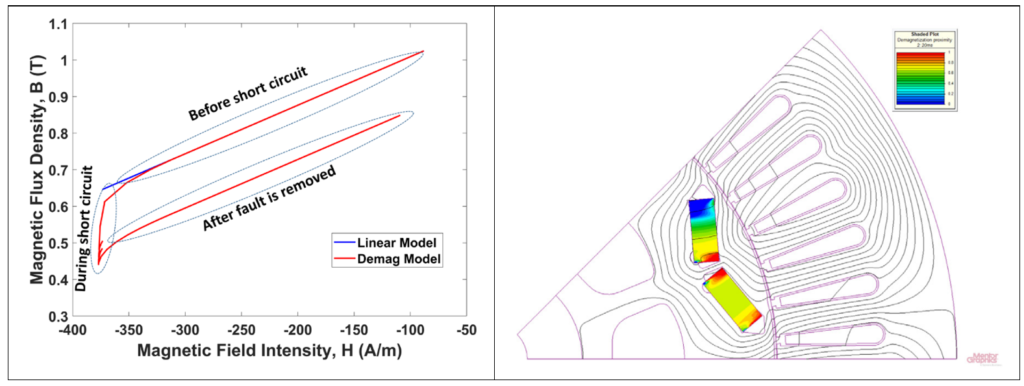
There is currently a race and an urgency to provide the most accurate and computationally efficient material modeling solution to contemporary machine design engineers. While some of the computational challenges will continue to be researched for the foreseeable future, it is incumbent upon software developers to innovate and provide state-of-the-art solutions to meet the challenges that engineers today face. The new enhancement to Simcenter MAGNET and Simcenter Motorsolve 2019.1 place these products firmly in the lead in terms of these capabilities.
References