How to empower aeroelasticians with parametrization!
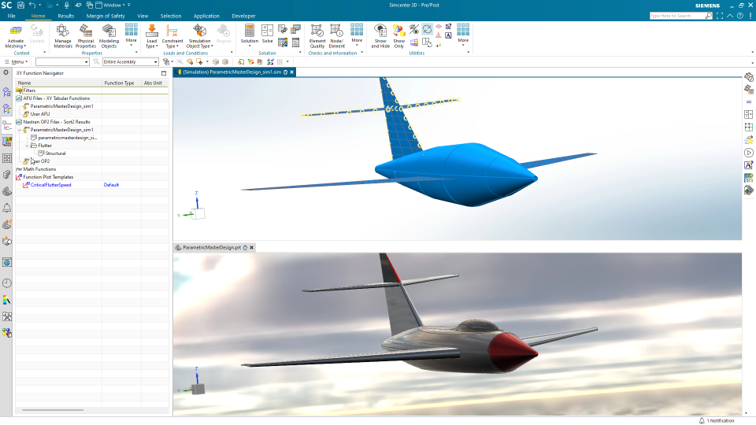
Getting started with Aeroelastics
Aeroelasticity analyses are key from the very beginning of preliminary studies of an aircraft program. They provide the raw order of magnitude for flight loads, as well as for flutter critical speed (which must remain beyond the flight envelope). All the preliminary structural work will be thus driven by these analyses.
Creating multiple models for each configuration (sweep angle, span, etc. for both wings and tails) can be quite an extensive task. Aeroelastic experts often use analytical formulas to make an informed estimate about what would work best. Then, they convert that into a aerodynamic model, which limits the design exploration right from the beginning of the project.
In-house tools
A typical alternative is to make an in-house program that generates models using key dimensions. In-house programs work fine provided you have the resources with sufficient knowledge in programming and an aerodynamic model set-up to do so. It will also mean that as you go forward in the design process you will be required to maintain and adapt this program.
Particularly when under pressure, Engineers will often look for the easiest way to make progress. Reusing old programs to complete new tasks is common, however, switching from one aircraft to another, there is always the chance that the in-house development would be re-used as more than an “inspiring example”, and inexperienced engineers may copy sections that they do not fully understand.
It would therefore be beneficial to make, without any programming, a parametric model that would adapt to dimension changes.
Working with designers
There are few aeroelasticians, and they have a lot to do. Consequently, they have very little time to share knowledge. Since they have no means of providing non-experts with an easy-to-use simplified parametric model, they usually bump into the designer’s “nice but physically irrelevant” new designs. In such situations, being able to provide a parametrized model that updates automatically against a set of dimensions would save a significant amount of their time!
In the meantime, aeroelasticians envy designers as they can parametrize their CAD model with any dimension they want, with a few clicks and with direct 3D updates to visually inspect the resulting model.
How can we parametrize an aeroelasticians daily duties?
There is software that allows aeroelasticians to parameterize models called Simcenter 3D!
When it comes to modeling, this tool offers an exceptional range of options to develop your own fully parametric geometry (such as sketches, surfaces, and points) during the initial stages of an aircraft program. It also allows for the idealization of pre-existing designs for later analysis. However, this is just geometry. To create an actual mode both the structural and aerodynamic models can be defined associatively to the parametric geometry. They can even have their own level of parametrization if required. To connect both models, nodes (from the structural side) and boxes (from the aerodynamic side) need to be associated. Ordinarily, this is a recurring manual task but with Simcenter 3D you can achieve this for every update. The process can now be fully automated using smart associative tools that gather nodes or boxes relative to a given location (relative to parametrization, of course) or a reference number.

Simcenter 3D
Simcenter 3D provides an interactive and codeless way to define a fully parametrized model for aeroelastic analyses. Once set up, such a model allows you to update key dimensions, that in turn automatically update the meshes (both structural and aerodynamic) and the analysis setup. Just solve the analysis and you’re already post-processing results for a new variant! Such models can of course be shared, providing a straightforward way to share expert knowledge on aeroelasticity analysis setup, and capitalize from one program phase to the next, as well as, from one program to the next.
Finally, this associative workflow can become the core of an automated design space exploration! This dramatically broadens the number of configurations any aeroelastician can investigate, and thus raise the innovation capacity for new aircraft designs.
Simcenter 3D 2306
This blog was just one in a series to highlight the Simcenter 3D 2306 release, for more information see the release blog