How to get the best out of your wind tunnel testing
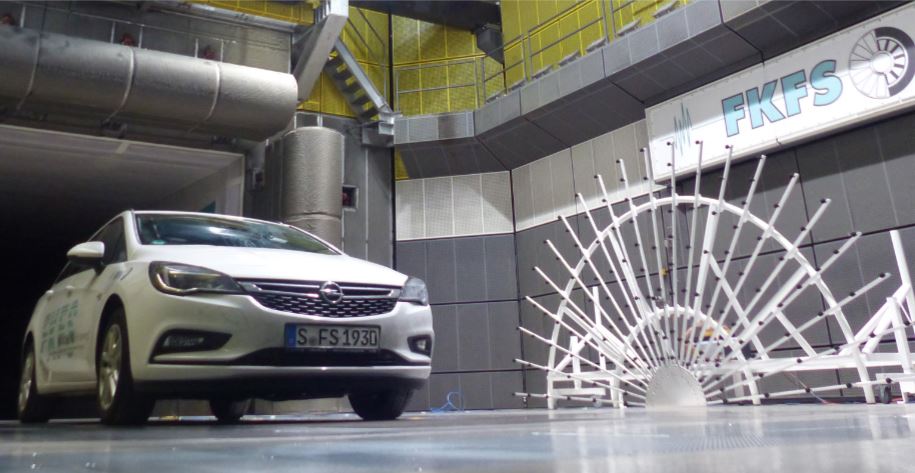
The future is electric!
If I had a euro every time I heard this sentence in the last 10 years working in the automotive sector, I would not need to worry about my pension plan anymore.
But while the automotive industry has made big steps towards its electrified future in the last decades, replacing traditional vehicle designs with electrified architectures still comes with strong challenges.
Take noise emission for example: by design, an internal combustion engine would mask most of the other noise sources in the vehicle, from wind to road noise, while an electric powertrain that operates at much lower noise levels will make them more audible to the end user.
Among all the elements to consider for ensuring an ideal acoustic performance and thus a pleasant driving experience, aero-acoustic noise soon appeared as one of the highest in priority, and most challenging to tackle during the vehicle development.
Sure, you can make simulations in early stage to evaluate the influence of your design choices on the acoustic performance, but then why a big part of the design troubleshooting, evaluation and validation is still done via testing?
The reason is that aero-acoustic simulations are typically very resource intense (we are easily talking about days or weeks of pure CPU time) and are not very suitable for troubleshooting leaks and weak spots in seals, which are the top cause of poor acoustic performance.
So, the solution is to plan a test campaign in a wind tunnel and fine-tune the vehicle prototype, right?
Well, yes, but this is easier said than done!
First, wind tunnels are expensive: the cost to rent a facility for a day can easily exceed 20,000 US$ (excluding operational costs) while building it will cost you millions. So, believe me when I say that once you have it, you want to get the most out of it.
That’s why ensuring efficiency in wind tunnel testing has been one of Siemens’ focus area in the past years thanks to its Simcenter solutions for areo-acoustic engineering. These involve the use of advanced testing technologies to visualize the acoustic sources outside and inside the vehicle cabin, measure all data streams together in an integrated dataset, and deploy this data collection, visualization and analysis methods as a streamlined process to maximize the return on investment of the usage of such expensive facilities.

What is done in practice in a typical wind tunnel test campaign?
We start from the evaluation of a baseline vehicle configuration, where the interior noise is measured for different operating conditions (wind speed and yaw angle). From there, different modifications are applied, and tests are repeated to understand their effect on the cabin acoustics.
A critical success factor here is to have test results immediately available for comparison with previous designs, in a way that engineers and acoustic experts can take quick decisions on what to try next.
And how can the Simcenter aero-acoustic solution be of any help?
The ambition is clear: provide on the spot insight as much as possible during the test campaign. This requires a combination of insightful measurement technologies on one side, but more importantly implemented in a completely automated way.
On the one hand, we want to introduce combined test methods to increase the insight into the root cause of high noise levels. Up to four microphone arrays can be placed around the vehicle and the wind tunnel nozzle to measure the exterior noise source distribution and use that information to link to the cabin acoustic performance. Same story for the interior, where dedicated technologies such as the Simcenter Testlab 3D Acoustic Camera are available to perform sound source localization in the vehicle cabin (i.e. understanding from where exactly the noise from outside leaks in).
Next to that, we want to integrate these different testing methods into one single automated and user-friendly process. Wind tunnel test conditions can be controlled from the acoustic test system, making it easy to automatically run and process test scenarios that were planned beforehand. By combining outputs of the different test technologies into one single dataset, Simcenter Testlab offers the possibility to have immediate access to all results at once in interactive views to allow easy comparison. All of this with a drastic decrease in processing time on top (a full processed dataset is few seconds away).
Do we have good examples of this?
Just take a look at what Honda is doing:
Here I just wanted to give you a glimpse of what is possible. If you are starving for more details, I suggest you a couple of reads that will make your day.
Check out this white paper where we go for a deeper dive in our different testing technologies for automotive aero-acoustics:
And if you want to get the essentials of automotive wind tunnel testing without reading much, then this webinar is for you: