Streamline GVT and flutter certification – get to the first flight faster
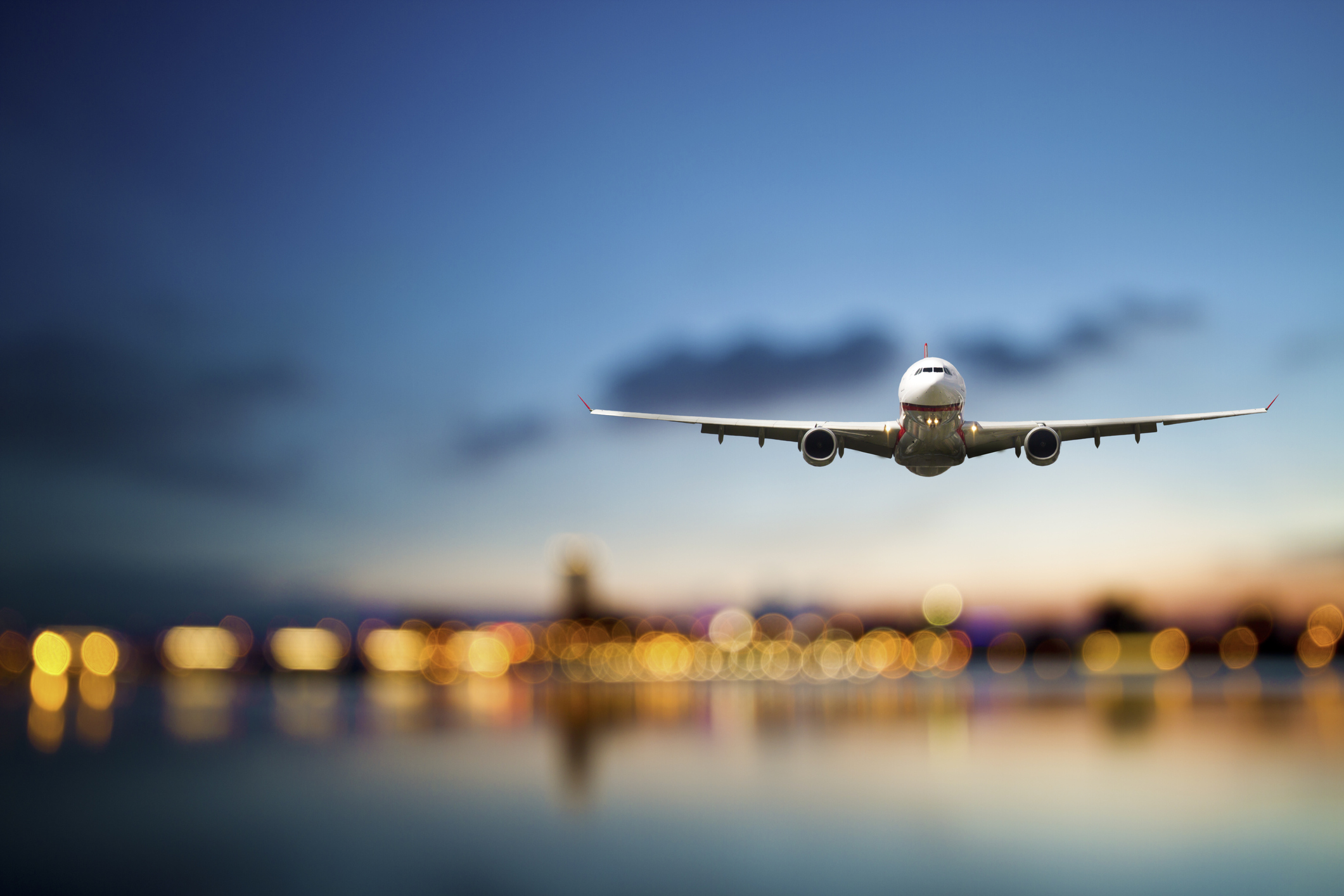
Do you want to learn how to streamline GVT and flutter certification, and realize the first flight faster and safer?
By the year 2025, Lilium plans to launch a “flying car”, an electric five-seater air taxi, into the air-mobility scene. With such innovative aircraft models, we are dealing with new architectures, with no previous knowledge, with unknown dynamics, and with many configurations that need to be designed, redesigned, and tested—and these companies want to realize their first flight very quickly!
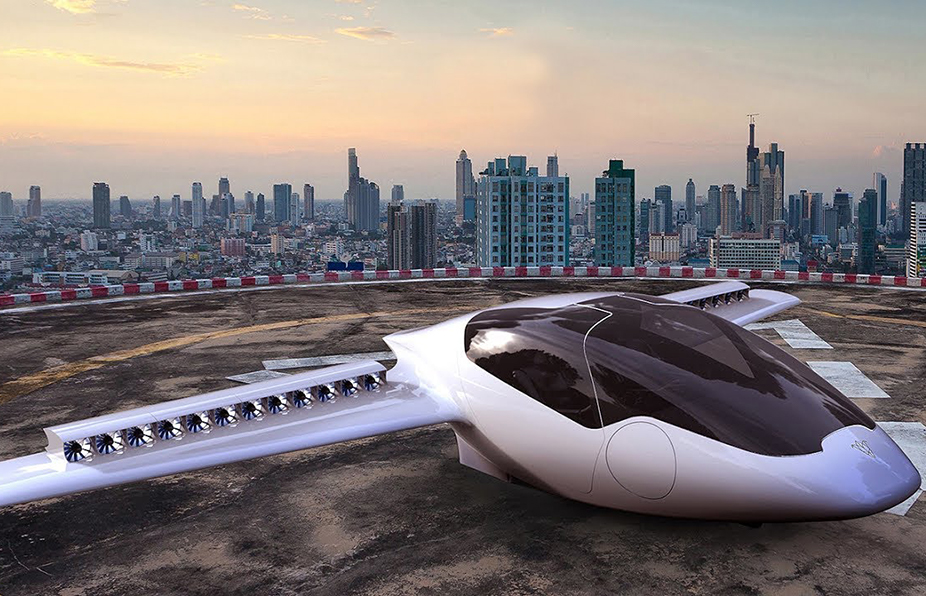
Ride the innovation wave
In the past, aircraft bodies used to be made almost entirely out of metal, and the performance and dynamics of the materials used were well-understood.
However, today, many aircraft companies are already developing the airplanes of the future; experimenting and testing innovative designs, and with innovative materials. The layouts and structures of these new models are also different from those in the past. But with innovation, comes uncertainty.
Using more composite materials contributes to achieving lighter bodies. But that means that you can no longer rely only on historical knowledge or classical experience. Even a small change, like changing some hinges, will affect the structural dynamics of any model.
– already in the design phase
For a successful new aircraft, many steps are necessary before actually flying it. First, you must design the aircraft model. This step is crucial, as it needs to be as accurate and prepared as possible before manufacturing an expensive prototype.
Here is where the use of a structural finite element (FE) model comes in handy. It allows you to play with the model to design the highest structural performance for as little weight as possible – all in simulation.
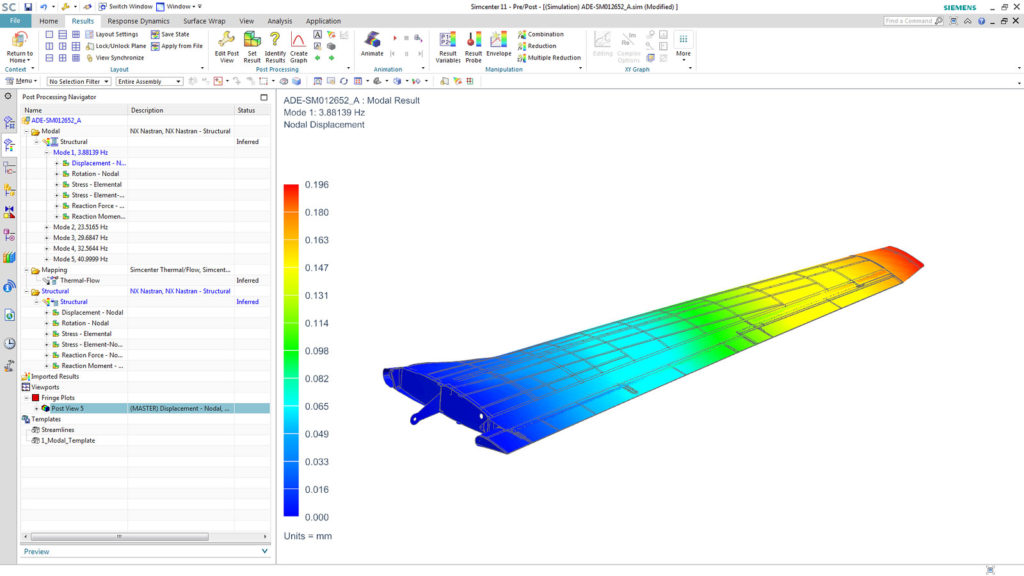
Streamline GVT and flutter certification in the validation phase
After the design is finished, the validation process takes over. These are all tests that occur later in the program, once the design is complete and the model built. At this stage, the pressure and stakes are very high.
A major milestone in the aircraft program is the verification of the structural dynamics performance of the fully integrated aircraft. The ground vibration test (GVT) provides profound insight into the structural dynamic behavior of the aircraft and helps calibrate simulation models used later on for critical flutter predictions. The last step of the validation process is a real-life flutter test. It confirms that there is no aeroelastic instability within the flight envelope, in accordance with Part 23 or Part 25 of the certification requirements.
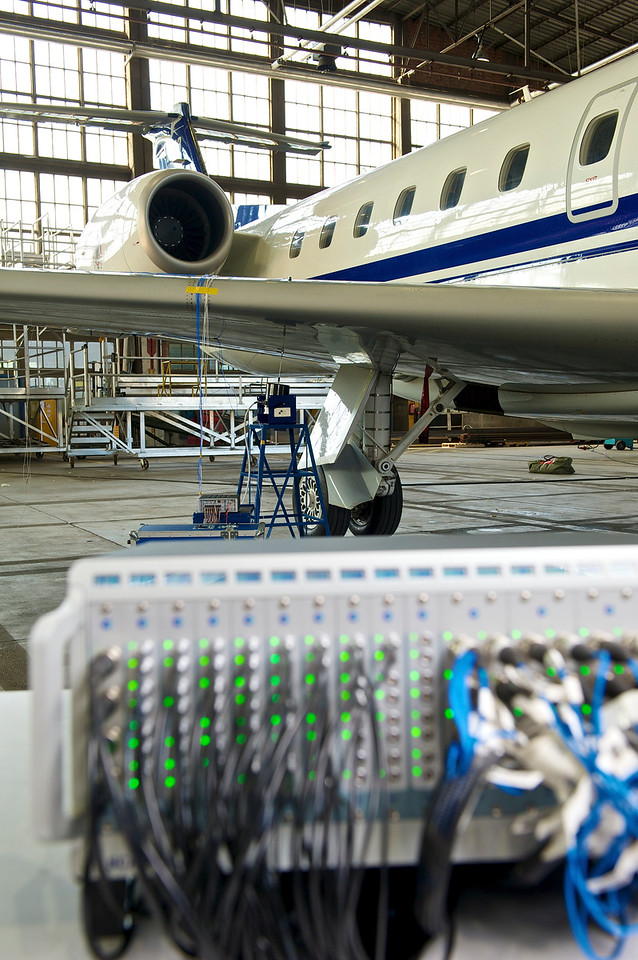
Tackle the engineering challenges
This validation process, of course, comes with its own challenges. During the design phase of an aircraft, the challenge is to validate and optimize everything as quickly as possible. The quicker you do it, the more designs you can validate. You want to make sure there is a smooth flow of data from the simulation team to the testing team, and vice-versa. The verification of the structural dynamic performance must be efficient, as you want to get as much as possible in a limited amount of time. You also want to make sure not to miss any critical phenomena, and yet, accelerate the process.
Typically, there are delays already before reaching the validation stage, which not only cost time, but an incredible amount of money too. This means that the validation phase needs to be well-prepared and performed properly.
The goal, then, is to balance accuracy and risk, performance and time, as well as efficiency and traceability.
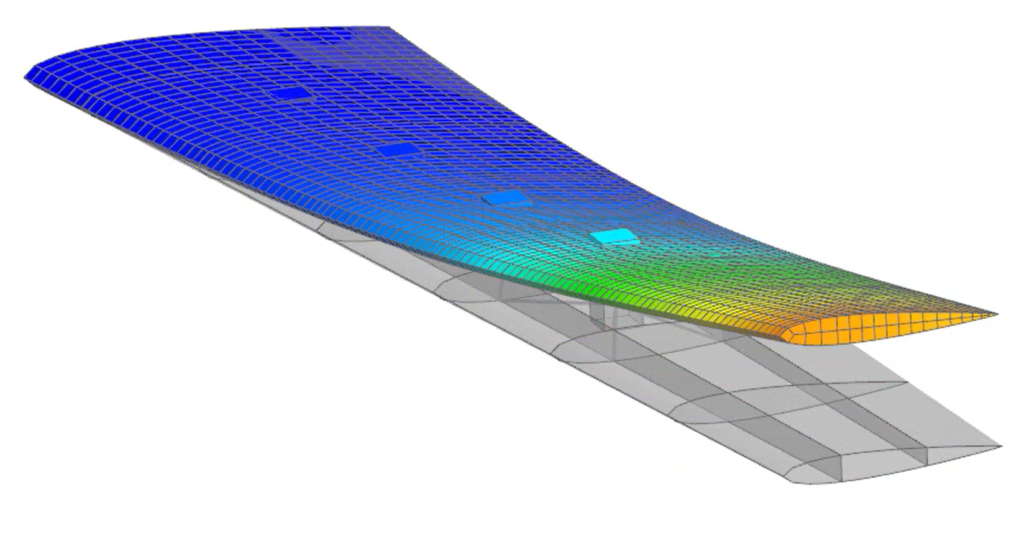
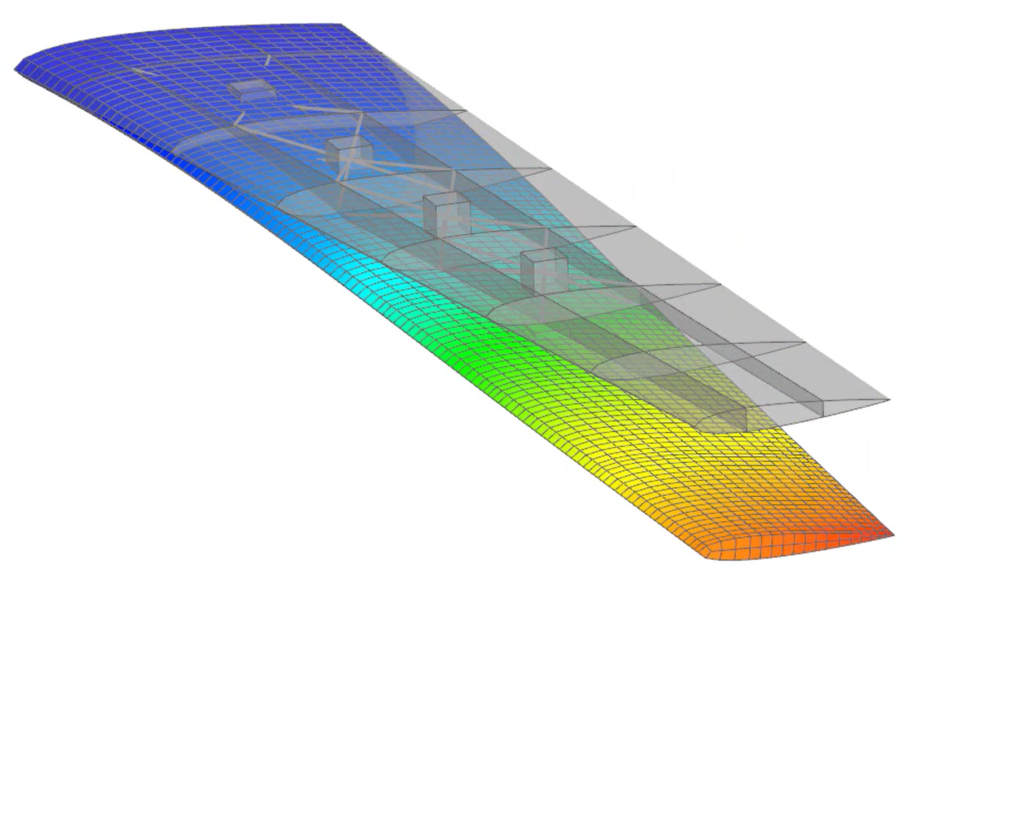
Streamlined process for GVT and flutter certification
With our Simcenter Testing Solutions, we seek to alleviate these concerns and meet the goals mentioned above. Through the Simcenter simulation and testing software and hardware, we can accurately capture all relevant phenomena related to aircraft structural dynamics, minimizing the risk of missing an important detail. With these solutions, engineers can perform tasks in the fastest time possible, ensuring efficiency during the entire process from detailed FE model creation to validation of these models with experimental data and accurate prediction of aeroelastic response. With a focus on data traceability, the pairing and feedback between test and simulation streamline both the aircraft’s design and the validation process and allows to accelerate and secure the aircraft certification process.
To learn more about aircraft validation processes, GVT and flutter certification testing, and more, watch the on-demand webinar.
Comments
Comments are closed.