How to perform a multi-attribute vehicle analysis with Simcenter System Analyst?
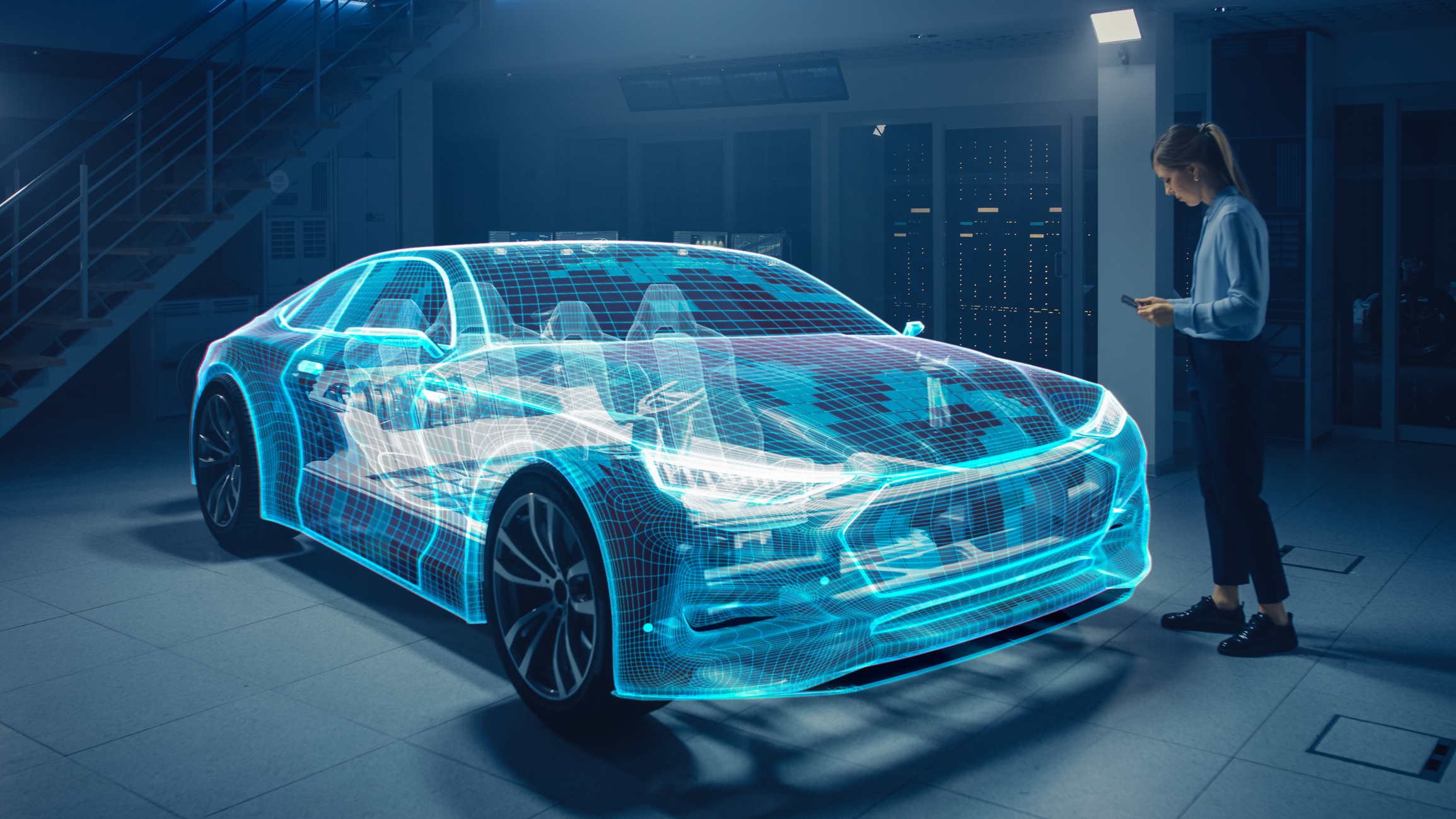
Who has never dealt with multiple models and analysis scenario? When it comes to ensure that parameters are consistent between the models and with the reference system variant, this is usually a tedious and error prone task. This is also especially the case if the system variant follows several evolutions during its design cycle. In addition, creating a synthetic dashboard of the multi-attribute results and ensuring that it is up to date all along the design cycle is another task that requires rigor and clear processes.
Such task is today in the hand of few CAE experts and this creates bottleneck when project teams need more and more this type of analysis. That’s where Simcenter System Analyst helps. In just a few clicks, a multi-attribute analysis can be set-up and this article will guide you through the different steps required for that.
Choosing a system variant from the database
Simcenter System Analyst allows to built multiple variants of a system and version and manage them in a database. Filtering all those system variants, called Technical Definitions in Simcenter System Analyst, allows to query the one that is required for carrying out the multi-attribute analysis.
For conducting the analysis required, we will pick-up a P2 hybrid SUV based on a M segment car body.
Figure 1 : Technical Definition query dialog
The queried Technical Definition (TD) is now available in the system variant definition window for additional settings, if required. We can see that the queried TD is an architecture made of several components (battery, electric motor, engine, …). Each component of this TD can be changed through this system variant definition window. All components available and on which the user has read rights are displayed and can be selected. This then easy to switch from a M segment vehicle to another segment available in the OEM database.
Figure 2 : Technical Definition system variant definition window
Definition of the Component variability
It is proposed to evaluate the potential added value of replacing the current 2.0 L and 4 cylinders gasoline engine of the SUV by the new 1.5 L and 4 cylinders engine that is now in the database of the OEM. To do so, the analyst has to fill the Component variations container with the new engine component that has to be evaluated.
Figure 3: dialog for filtering and choosing the Engine component to be evaluated
Definition of the analysis: Taskpad definition
In Simcenter System Analyst, analysis templates can be stored in database. These templates can contain several scenarios to be run with the Technical Definitions but can also contain cascaded simulations in case complex workflows have to be done to fulfill an analysis.
The Taskpads are computing one or several criteria that will be used by the analyst for judging the respective merits of the various system variants.
In our analysis case, the analyst will query a performance and fuel consumption Taskpad that is valid for evaluating Hybrid vehicles. To do that, the analyst will open the Taskpad query dialog and will filter the available Taskpads by using the attributes window. By selecting hybrid architecture and then fuel consumption and performance analysis, one type of Taskpad is retrieved in the database.
Figure 4: choosing the Taskpad(s) that fulfills analysis requirements
Here the analyst could also have chosen the Taskpads by filtering those by type of criteria computed (maxim speed, tip-in peak to peak jerk, fuel consumption, …).
Once opened in the Simcenter System Analyst GUI, the analyst can look at what are the various criteria computed by the Taskpad that was queried.
Figure 5 : criteria computed by the Taskpad “performance and consumption on hybrid”
One can see that this Taskpad computes 5 performances criteria and one fuel consumption criteria. The fuel consumption criteria is a weighed average over 3 normalized cycles: FTP06, WLTC and HWFET. Each Taskpad contains 5 simulations: one for each normalized cycle, one full open throttle from 80 km/h to evaluate the time from 80 kms/h to 120km/h and one last simulation with a full open throttle from 0 km/h to evaluate the last 3 performance criteria.
Definition of the Taskpad variability
We are at the last stage before running the simulations. The target is to define what type of batch analysis we want to carry out on the Technical Defintion. The analyst can create variations over the components that were defined in the Component variations container and can also add any variations based on any parameter from the Technical Definition.
The variability manager below, the analyst has defined a set of runs where he will evaluate successively the default Technical Definition for having a reference, and then the same Technical Definition but with the 1.5 L engine rather than the original 2.0 L engine. In addition, the final drive ratio of the gearbox is varied over a couple of values in order find the good tuning in term of performance versus fuel consumption.
Figure 6: Definition of the parameters variability
Simulation and post-processing
All the Taskpad runs can be now created. Like already mentioned, each Taskpad contains 5 simulations, on top of which we perform a batch of 5 system variants. This makes a total of 25 simulations o be carried out.
All the simulations are started from a single simulation button. If available those can be run on a High Power Computer machine to avoid overloading of your local machine.
Figure 7 : The Taskpad variability being simulated
At the end of the simulations, the analyst can visualize the results of the criteria evaluations, made at the end of the 25 simulations. Various plots are available to display those in a meaningful and attractive way. Underneath we can see the results in a spider chart, where the reference Technical Definition is plotted in red and the 4 batch alternatives with the 1.5 L engine are plotted in blue, yellow, green and pink. Each of those alternatives being computed with a different final drive ratio value.
The analyst can indeed quickly identify that the new 1.5 L engine is giving less performances but much more fuel economy than the more powerful 2.0 L engine. Variations of final drive ratio can help to do a fine tuning in term of fuel consumption versus performances. The valuation of a weighted criteria based on marketing requirements will help to define the right value.
To conclude
Simcenter System Analyst offers a straightforward interface that allows engineers with no CAE experience to build and run simulations on complex and powerful system simulation models. The simple definition of System variants (Technical Definition), Analysis Template (Taskpad) and system variability through the variation of components and/or parameters is a simple workflow that can applied by any project, design, planning, test engineer for fulfilling its everyday mission.
Watch the Tech Tips video on how to quickly set up simulation runs:
RELATED CONTENT :
Read this article to discover the first applications of Simcenter System Analyst.
Discover the Simcenter System Analyst in the video below:
About the author:
Romain Gonard is the product owner of Simcenter System Analyst. His main activities are focused on developing the vision and the development strategy of this new product in interaction with already numerous key customers.