Capture HVAC flow-induced noise early in the design cycle
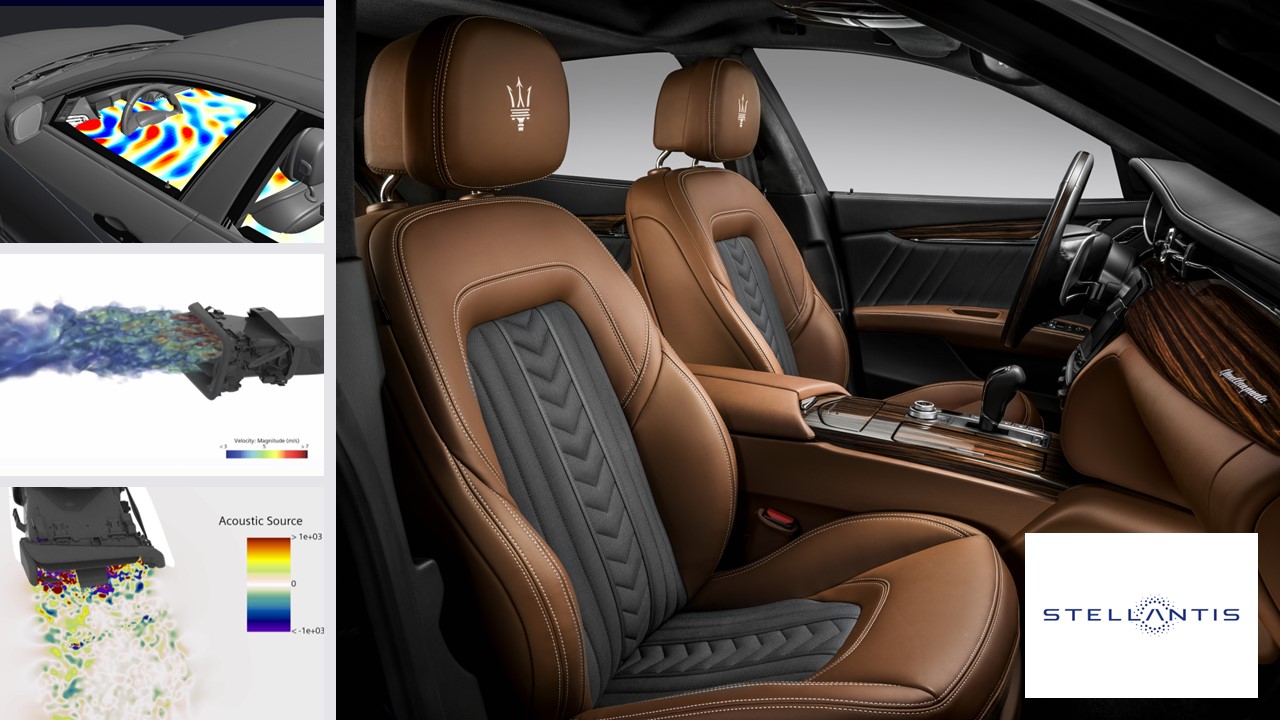
Acoustic comfort is one of the key attributes of passenger comfort in a vehicle design. And not just for the sound system. A lot of work goes into designing speakers that optimize how sound travels through the cabin but managing background and exterior noise is equally essential. For many years, this only received significant attention in luxury cars to maximize the comfort of passengers. Most road users accepted the noise of an internal combustion engine as part of the driving experience. In fact, for some, this sound was an essential and desirable factor.
But with electric vehicles becoming more common, this is changing. Road noise and wind noise are more audible than before. In addition, new noises such as the whining of electric motors or auxiliary noises are introduced. Manufacturers seek solutions to reduce these annoying noise sources by analyzing the root cause of noise and vibration problems, optimizing vehicles to improve brand image, and increasing the perception of quality.
The main vehicle noise sources can be broken down into:
- Structural noise: road noise, electric motor noise, and noise propagated through flexible components of the cabin
- Flow-induced noise: Wind noise and HVAC system noise are two contributors to interior noise
To capture these physics, it is critical to have a working solution between a strong computational fluid solver for the flow-induced noise, and a finite element solver to analyze the structural response. The focus of this blog is on HVAC duct noise.
Modeling HVAC noise propagation
Studies have shown that HVAC equipment is responsible for most of the noise inside an electric vehicle at low cruising speeds. So, acoustics modeling of HVAC noise propagation is vital to understanding it.
The first step to managing these noises is identifying the source. If you do not know exactly how and where the noise is being created, how can you go about reducing it? Then, you need to look at how all these noise sources are transferred throughout the vehicle and adapt designs to mitigate them.
This is no easy task. It takes a lot of time and money, which manufacturers can ill afford. Yes, customers demand quality, but they also require competitive prices. To remain successful, engineers must reach the optimum designs within a reasonable time and minimize development costs.
Simulation has been able to carry out these tasks for some years, but while the accuracy was good, it took 10 days or more to get the required results. So, a significant effort has been focused on speeding things up by making full use of the available hardware and GPUs and improving how the simulation software works.
This led to the implementation of the Lighthill wave and the development of the perturbed convective wave (PCW) models in Simcenter STAR-CCM+. These are both hybrid aeroacoustics models targeted for better results, faster. Yet, PCW includes flow convection effects, while Lighthill neglects the effect of the flow field on sound propagation allowing evaluation of sound away from the source. Both methods solve an additional equation for the sound source based on an acoustic source term computed from the flow field. Also, they are much less computationally intensive and run in parallel to an incompressible transient scale resolving simulation which provides significant performance improvements, as well as less mesh dependency compared to compressible simulations.
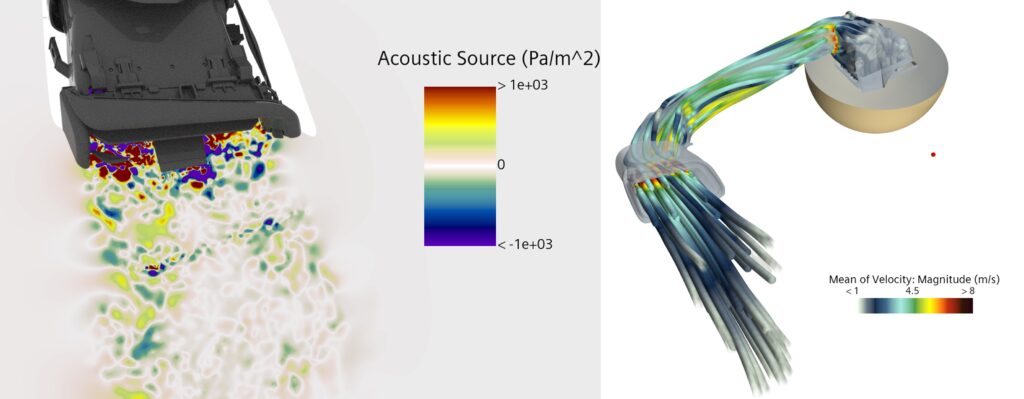
Leading multinational automotive manufacturer Stellantis used the latest developments in Simcenter STAR-CCM+ to devise a new method that accurately and quickly predicts a vehicle’s cabin acoustic noise levels. Previously, Stellantis had a multi-step method for calculating HVAC duct alone. While accurate, it was very time-consuming due to needing an acoustics mesh as well as a fluid domain mesh. But thanks to the hybrid acoustics solvers built into Simcenter STAR-CCM+, this was condensed into one single step helping Stellantis to streamline the process. In the recent SAE technical article: HVAC noise prediction using Lighthill wave method, Stellantis helped validate the new hybrid models by comparing them to in-house test rigs.
With these simulations, engineers compare unique design iterations and rank them in terms of the amount of noise generated. So, in this instance, they can easily see which duct designs have the higher noise levels across the frequency. The simulations also allow engineers to identify airborne noise sources by visualizing the volumetric sources. In this case, the Lighthill noise source scalar field along with comparing the vortex structures and velocities were analyzed to understand how noise is generated.
GPU’s providing faster, more cost-effective turn-around time
One of the big challenges for flow-induced noise has been how to run the acoustics simulation within a day. The challenge is that you need a time step, and grid size to capture the acoustics sources. The hybrid acoustics model helped reduce the load by a factor of 2-3, but to enable design exploration and enabling 100’s of cases, further cost reduction and speed-up are needed.
Recent developments in GPU hardware have helped reduce time and cost. What was taking 1000’s of processors to achieve 24-hour run-time can now be solved on smaller GPU workstations allowing turn-around time within 10-14 hours. This becomes another key game changer for engineers to look at more designs, faster.
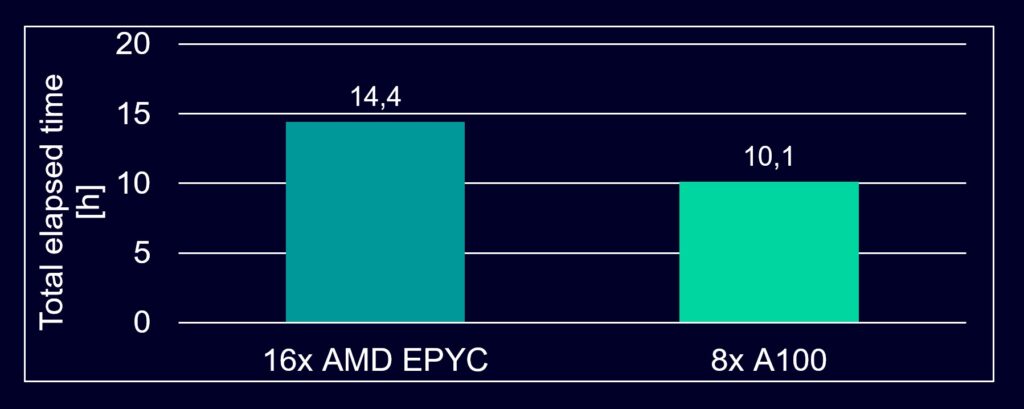
Faster HVAC duct leading to faster cabin noise evaluation
Using the hybrid aeroacoustics models implemented on the fly to the CFD analysis allows you to solve the HVAC duct acoustics in the time domain. In the next step, Simcenter 3D is used to consider the acoustic field in the cabin in the frequency domain. The perturbed convective wave model has the added benefit of separating hydrodynamic and acoustic pressure to help transmit the acoustic noise source into Simcenter 3D. A new conservative mapping algorithm has also been added in Simcenter STAR-CCM+ to map the aerodynamic entities onto the cabin structural model which helps to greatly reduce data transfer between fluid and structural simulations.
Noise sources from both mechanical and flow-induced regions can be combined for complete noise evaluation inside the cabin. As an example, an NVH engineer can look at contribution of both the HVAC noise sources combined with side mirror noise.
Fluid-induced noise sources from both exterior as well as HVAC duct noise
Typically, the HVAC duct design comes from the cabin team, while the aerodynamics team looks after the external wind noise. But using a unified NVH cabin model, the contribution of noise sources can be combined and evaluated at the driver location. Here, the NVH engineer can compare the noise level with just HVAC noise, or add the exterior wind noise contribution to the investigation. It does not stop there. Noise sources from the underbody to the electric motor noise, road noise, to the acoustics of the speakers can all be combined to get a complete overview of the noise levels in the cabin.
Discover more
To get the full story on how Simcenter is speeding up the simulation of cabin acoustics, watch the webinar featuring Binoj K. George, Stellantis HVAC CFD simulation engineer, and Fred Ross, and Korcan Kucukcoskun, both from Siemens Digital Industries Software.
Whether you are dealing with cabin acoustic noise, road noise, wind noise, powertrain or electric drive noise, or noises related to system integration, Simcenter simulation and testing solutions help to gain insights into how to reduce noise and vibrations, assess systems interactions and their influence on other performances, while striking an excellent balance between cost-efficiency, weight, and performance. Visit our NVH & Acoustic web page for more information.