[Hyster Yale] How to convert a conventional lift truck into an electric truck?
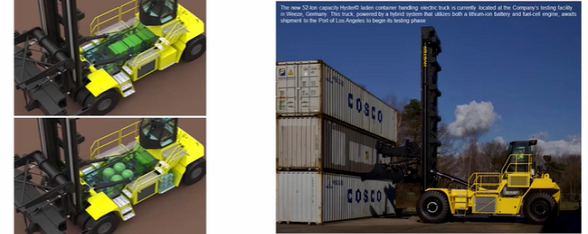
The estimated volume of international freight movement for 2020 was around 4 million tons per day. Or an average of 1.3 million containers handled daily. To optimize their logistics at major ports and terminals, FREIT uses high-performance and reliable container handling equipment. Hyster-Yale is one of the biggest suppliers of handling equipment. It offers its customers a broad line of products and power options.
As a responsible global operation, the company has begun to address climate and environmental concerns. In doing so, has focused on the emissions of their handling equipment. To maintain its position as the market leader in heavy forklift machinery, Hyster-Yale has to consider the conversion of its machines from fuel-powered to fully electric versions. Converting a 120 tons gross weight machine (80 for the machine and 40 tons for the lifted load) into an electric vehicle is not a straightforward process. Indeed it should offer similar or better operational performance as a conventional machine over duty cycles.
Rob Damen is a project engineer at Hyster Yale, based in the Netherlands. He is part of the Innovation & projects team at Hyster Yale Big Truck development center. He has a focus on testing and simulation of the equipment. During the last Siemens Realize Live event, Rob explained how, with his team, they succeeded in converting a Laden Container Handler into an electrified machine. That vehicle is now in a testing phase. The team used simulation to virtually explore all the possibilities. They came up with one design to fit all the market expectations and regulations without compromising development time or cost.
Know your kilowatt
Before exploring what the power options for electrification were, the engineering team virtually modeled the current truck. Using Simcenter Amesim, the Simcenter system simulation solution, the team captured the machine behavior into a virtual environment. They analyzed the energy flows through different areas of the machine. To proceed, they divided the machine model into different systems and sub-systems. They also identified all the parameters of the machine components that they could virtually capture in the model.
From that model of the truck, Rob’s group was able to identify where they could simplify and make some assumptions but still keep a model that would deliver accurate results. “We were able to develop our model thanks to pre-defined components on Simcenter Amesim”, said Rob.
To make the model even more representative of a real-life system, the team instrumented one truck at their premises. There they captured data over predefined cycle steps. That analysis allowed them to compare the test-data results (vehicle speed, lift height, engine speed/power/torque, fuel consumption, etc.) with the Simcenter Amesim model results to refine and validate the model.

Collecting real-life data to refine model complexity
However, in real life, machines are subject to so many different duty constraints and usage. Consequently, the team went to various customers to capture multiple types of data (GPS, lift, hydraulic pressures, etc.). They measured the performance of their machines with sensors over long durations. Those measurement campaigns enabled the team to define various duty cycles, depending on the nature of the application, with different patterns of energy distribution.

One major finding identified during this benchmark test was the need to improve energy recovery. Over the measurement campaigns, Rob’s team identified an opportunity to recover up to 15 percent potential energy especially during load lowering and braking phases. This energy can be recovered using electric storage.
Virtually explore and validate the Hyster Yale’s electric machine concept
“Once we got our benchmark model and our truck duty cycle, we were finally set to come up with an electric powertrain concept that fits the truck needs”, explains Rob. The group made the selection based on ranking categories and drivetrain concepts to determine the best-ranked concept.
The team chose a hybrid approach combining fuel cell and battery. In this case, the battery can store and benefit from energy recovery from load lowering and breaking. Such a system enables the recharge of the battery and improves systems’ lifetime.
At that stage, Rob converted the conventional benchmark model into the electrified version. From that defined concept, the group was able to precisely virtually assess where energy recovery could happen during braking and load lowering. This next step in virtual benchmarking using Simcenter Amesim helped to define 3 main things. The battery state of charge, how to size the battery, as well as hydrogen consumption.
The model analysis for the opted strategy opened the discussion to a new set of questions about thermal management of the battery, related to a dissipated heat and battery cooling strategy definition. Rob explains that “the list of topics that we can cover with simulation is so wide. This is definitely a good thing for us. Indeed, it can help on reducing a large number of physical testing. That is a win in terms of development cost and time for our company”.
Develop an energy recovery system on load lowering
A highlight of the project is the development of the energy recovery system on load lowering, which Rob and the team collaborated on closely with Hyster-Yale’s supplier. “In that collaboration, the use of Simcenter Amesim made it easier to answer questions that require specific data with our suppliers”. The system uses one electric motor on load-lifting but split the flow over two motors during lowering as it is almost twice as fast and with that, the power is also twice high.
“From our initial simulation model, we continued further detailed work of the truck systems”. The team worked on 3D simulations based on an advanced electric model design. Then they performed tests on a machine to compare simulation and real-life results of the electrified version of the vehicle. “The test bench results and the Simcenter Amesim models results matched really well” concludes Rob.

Next step: going faster and deeper into details for future electrification project
“With that laden container handler experience, we are now ready to initiate a new project on one of our other big machines”. For that new project, Rob and his team will use a similar approach. With their learning of the previous project, they are able to go faster and deeper into details through the overall process. “We clearly benefit from Simcenter Amesim into our innovation project. It gave us the ability to simulate, analyze and adjust the truck systems in a very short time frame”.
Learn more section :
- Read the blog : Reassure your end-users on their electric-powered heavy equipment investment thanks to simulation and testing
- Browse over our website on our offer for heavy equipment electrification
- Watch the on-demand webinar about System simulation: a key differentiator for designing electrified heavy equipment
- Watch the on-demand webinar about Electrifying the future of the heavy equipment industry
- Watch the on-demand webinar about Improve the thermal management of an hybrid heavy equipment using Computational Fluid Dynamics (CFD) simulation
- Read another customer success story French construction machinery manufacturer uses Simcenter Amesim to develop first electric wheeled excavator