If you can’t take the heat… Simulate it! Reducing VTM costs & time to market
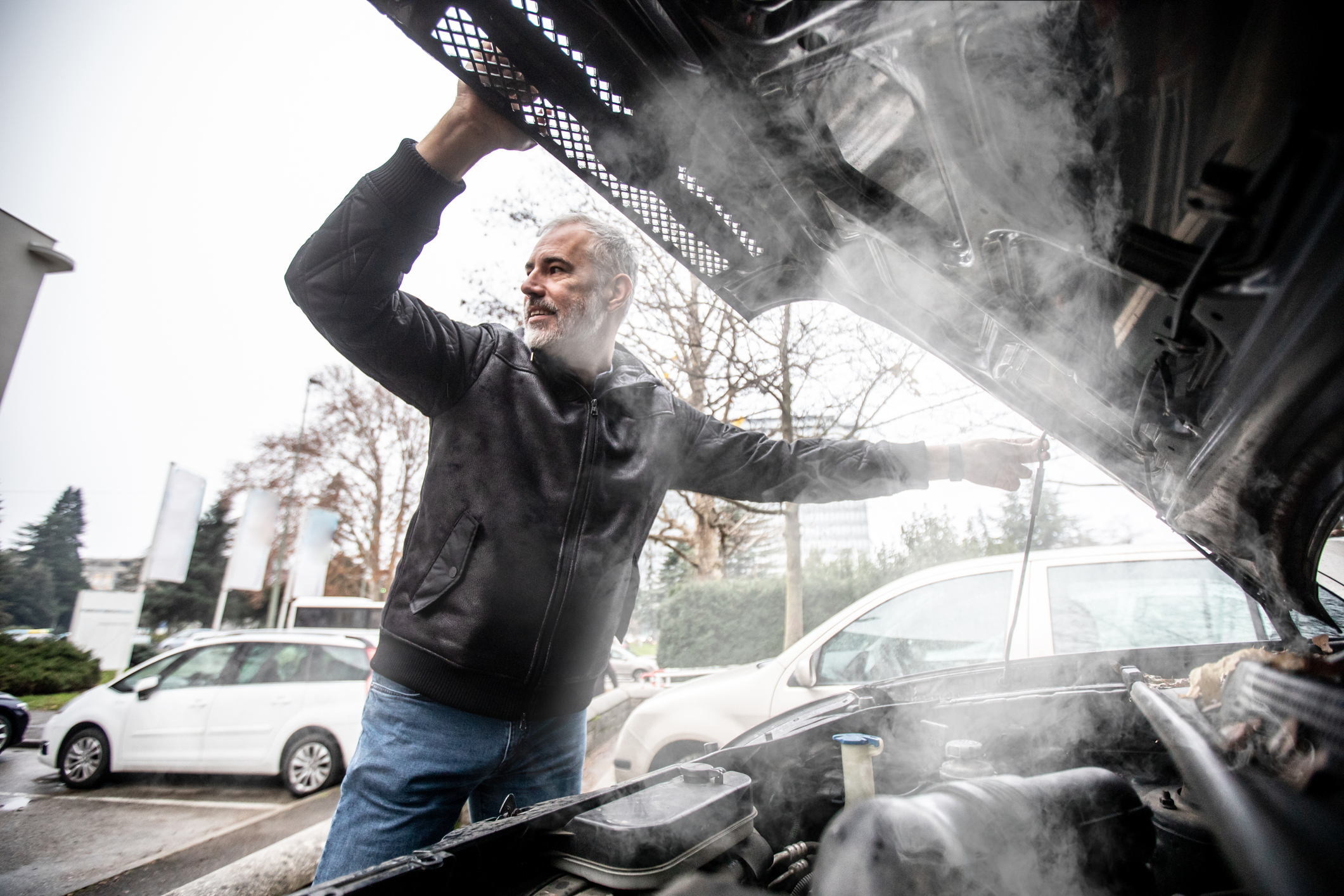
This blog post was co-written with Nick Amato, Manager of CFD Applications, Simcenter Engineering at Siemens Digital Industries Software.
Over a car’s lifetime, several components are repeatedly exposed to temperatures up to several hundred degrees Celsius. These high temperatures occur continuously over years and parts can be exposed for hundreds of thousands of hours. These conditions are especially harsh on components under the hood, which has limited airflow and houses most of a vehicle’s most critical components.
What is VTM?
Vehicle Thermal Management (VTM) is the practice of evaluating the temperature of parts across the vehicle and mitigating exposure to excessive heat. VTM is critical for every automotive OEM and the cost of getting it wrong can be extremely high. Recalls due to part failure or quality issues that require extra repairs after a product is on the market not only lead to negative publicity and a tarnished reputation for companies but are also immensely expensive and time-consuming to resolve. For example, a recent Hyundai EV recall due to battery fire risks will cost the company about $900 million. In 2016, Daimler Trucks voluntarily recalled 9,000 trucks due to the possibility of overheating HVAC units.
In most cases, these after-market VTM issues are preventable. VTM problems can go unaddressed during the design process due to lack of time to make modifications, lack of proper materials, or not enough simulation of a design.
Why is VTM so difficult to model?

One challenge presented by VTM is complexity, including both the physics being modeled and CAE software being used.
VTM issues are complex
Heat-induced part failure does not happen spontaneously. It occurs when parts are consistently exposed over time to critical temperatures. This is very difficult for engineers to properly analyze and predict. Physically monitoring each component during testing is impossible. For example, putting thermocouples onto some components can be challenging due to space limitations. Additionally, if you add too many thermocouples or monitoring devices, the added hardware could compromise the integrity of the data by altering the flow or nature of the heat transfer in the area. All these factors can make it tough to determine the root cause of failure. Did the part fail because it was getting too hot due to radiation from a nearby hotter part? Or because of a lack of airflow? Perhaps a bad heat shield or poor material choice? Simulation can help provide many insights into the where, how, and why of thermal issues.
The limitations of simulation software for VTM
In addition to the physical complexity, the simulation software that can be used to predict VTM issues can be complex. A VTM simulation is very process-oriented and requires a great deal of preparation and bookkeeping of components and results, which are many times unsteady in nature. While the accuracy of simulation is continuously improving, the scalability of simulation processes from subject matter experts or design engineers remains a challenge.

Simulations can also be set up inconsistently from one user to another. This discrepancy worsens when simulations are shared among teams that span different geographical locations or follow different processes.
Additionally, the amount of time that it takes to run simulations can be prohibitive. If engineers wish to achieve high-fidelity simulations, the CAD to solution time can be extremely long. Setting up simulations involves several manual steps that often need to be repeated if modifications are required further in the design phase, which is usually too late to make significant changes. Once the results are generated, the postprocessing and data analysis adds even more time to the process.
CFD simulations in particular require extensive training to set up models and run the simulations accurately. The more complex a simulation is, the more knowledge of best practices and bookkeeping is required by the engineer to make sure the work being done is accurate.
Engineering teams face restrictive timeframes
Another obstacle for engineers involved in VTM is the timeframe that OEMs impose on product development teams, driving them to find way to reduce turnaround. OEMs may only give their engineering teams 10-12 weeks to run simulations, review the results, and provide feedback on performance to the designers. There can be anywhere from 10,000-30,000 parts that need to be analyzed and simulated during this timeframe, each with varying boundary conditions and materials.
Additionally, each part requires an engineer to assign properties, prepare geometry, run the simulations, and review the results. All of this must be done not only on the component-level, but also in a way that ensures that all parts and components will function properly within the vehicle system.
Delays in getting new vehicles to market can cause companies to lose market share to competitors, who may be able to release new models more frequently. As a result, some companies skip detailed simulations and opt for “quick and dirty” approximations, which consequently leads to some VTM issues going unnoticed. In addition to allowing preventable VTM issues to go unchecked, this also makes it difficult for engineering teams to do what they do best: try new designs, explore new ideas, and improve product performance.
Advancing VTM simulation practices
To address these issues, the Simcenter Engineering services team has developed workflows that provide a structured process for engineers to go from CAD to results without having to be a CFD expert. These workflows allow the user to choose from different levels of fidelity in order to achieve results within the designated timeframe.

There are three levels of fidelity that a user can select:
- Sub-system modeling
- Early digital prototypes
- Digital twin simulations
These options allow engineering teams to simulate various levels of model complexity, ranging from a simple front-end flow to a complex drive cycle analysis, and increase the complexity as required. They provide an entirely customizable and automated experience to allow users to choose not only which level of fidelity they would like, but also how quickly they would like to see results.
Sub-system modeling (Level One)
For engineers who are working in the initial design phase or looking to get an idea of overall performance trends, Level One modeling is an ideal solution. It provides a fully automated process and requires minimal input from the user. Tailored for sub-systems, such as brakes, it allows for up to 500 solid parts to be modeled and can provide results in half a week.
In this example, a Level One simulation is performed for a brake cooling application.
During braking, kinetic energy is converted into heat by friction. The brake disc absorbs the majority of the heat, while the remaining portion is absorbed by the brake linings. The brake components must be able to resist these high thermal loads in order to ensure consistent, reliable brake performance. The heat absorbed mainly by the brake disc and brake linings is then dissipated by convection, heat conduction, and radiation to the ambient air and the surrounding components such as the brake caliper, rim, and wheel carrier.
To model a brake cooling simulation, engineers need to set up a complex transient drive cycle. If one wanted to evaluate geometry modifications such as cooling duct-shaped or various wheel configurations, traditional simulation methods would take an enormous amount of time to set up and examine the effects of each design on brake thermal performance. Using a streamlined and automated process, such as the workflow provided by the Simcenter Engineering services, can significantly reduce the amount of time required to test each configuration, running a complete drive cycle in as little as three days. This automation allows users to couple data to aerodynamic simulations and balance drag vs. thermal performance of a given wheel design for WLTP considerations.
Early digital prototypes (Level Two)
For teams still in the early design phase but looking to examine more parts, Level Two modeling offers a semi-automated process and a higher level of fidelity. Level Two allows for modeling of several thousand parts and offers a one-week turnaround. This stage is recommended when CAD, such as the internal engine block, may not be complete, or when the design is still changing.
The above example shows a Level Two process buildout for a thermal soak. In this example, a vehicle cruising at a steady speed comes to rest. This load case is crucial for all automotive companies, as it evaluates thermal failures of components under the hood that may heat up due to absence of any forced convection once the vehicle is at rest and the fan has been turned off. The temperature time history of various components can provide valuable insights on the choice of materials and design elements that would allow hot air trapped under the hood to escape.
In this example, 5,000 solids parts were modeled using the semi-automated process. This type of simulation is ideal during the intermediate design stage and beyond, such as during vehicle development when enough solid components and boundary conditions are available.
Digital twin simulations (Level Three)
The Level Three workflow allows for true digital prototyping. It enables companies to move from physical testing to a digital verification and validation process. In Level Three, steady state simulations to complex drive cycles are possible.
Using Level Three, engineers can easily simulate 10,000+ solid parts using a semi-automated process within four weeks. It offers the highest level of fidelity, capturing all modes of heat transfer from multiple sub-systems and models all the available boundary conditions, making it suitable for later design cycles.
Daimler
Daimler, Germany’s OEM powerhouse, has been able to identify a significant majority of its VTM issues and implement corrective countermeasures using simulation alone. Leveraging Simcenter Engineering services experts, Daimler has been able to develop and continuously improve a state-of-the-art thermal model which contains over 10,000+ components that are tested for peak temperature during various load conditions and drive cycles, all in a virtual environment. This allows thermal failures to be prevented prior to the first prototype being built, reducing physical testing and associated costs.
This transition to full-vehicle digital twin has significantly reduced costs and time to market for Daimler. Today, Simcenter Engineering services continues to support the development of heat protection and has increased the level of detail possible for components and drive cycles.
VTM workflows in action at Simcenter Engineering services customer sites
Changan Auto
Changan Automobile is China’s leading manufacturer of passenger cars, microvans, commercial vans, and light trucks. The company recently partnered with Simcenter Engineering services to evaluate and improve the thermal performance of both a PHEV battery and the vehicle itself.



To accomplish this, the team at Simcenter Engineering services built a Level One simulation process that leveraged 1D-3D coupling. Simcenter Engineers developed a novel reduced-order modeling methodology that helped predict transient battery performance with excellent accuracy while reducing the simulation time to hours. They also developed a custom interface to allow Changan engineers to import data, visualize and set up a 3D underhood model. The team used Simcenter STAR-CCM+ to build the 3D model, while the connection to Simcenter Amesim was seamlessly integrated to allow transient modeling of the battery in 1D. This novel approach enabled Changan engineers to set targets and optimize the performance of the Thermal Management System.
FCA Group
Energy management and thermal management can often go hand in hand. The overall energy management is even more important when it comes to EVs. Instead of using waste heat from combustion to provide heating for passengers, in EVs, electric heaters are used to control cabin temperature and heat up vehicle batteries to reach operating temperatures. With everything now running off the battery, energy efficiency is even more important as it will have a direct impact on vehicle range and usability.
In order to investigate this issue, a 1D and 3D coupled model was created to model various sub-systems in higher fidelity to give more robust data for engineers to review. With this methodology, simulations such as drive cycle become more computationally affordable and physical behavior can be captured more realistically. It also enables an OEM to balance the customer comfort while optimizing the battery range.
VTM simulations that meet engineering demands
In 2019, about 39 million vehicles and 14 million vehicle parts were removed from US roads. These recalls cost OEMS millions of dollars, negative publicity, and degrade a brand’s reputation.
Transitioning to a simulation approach is a step in the right direction, but as model and vehicle complexity has increased, more advanced simulation approaches are required. Simcenter Engineering services can help make CFD simulations for VTM more flexible, more accurate, and more intuitive to meet engineering demands at every level of the design phase.
The Future of VTM
The future of VTM is constantly evolving as new technologies and methodologies are developed. In the near future, we anticipate that AI and Machine Learning will help accelerate everything from data preparation to design exploration. By automating certain steps of the simulation process, such as sorting of CAD parts for simulation and weeding out bad designs, AI and Machine Learning can make engineering processes faster and more efficient. This frees up valuable time to allow engineers to work on higher-value tasks and innovate faster. When engineers are given the freedom to explore their ideas and solve more challenging problems, companies and consumers benefit from better, safer, and more reliable products.
To learn more about Simcenter Engineering solutions for VTM and AI, check out the below resources:
- Enabling fast, effective thermal soak simulation
- Accelerating vehicle heat protection analysis to find problems earlier in the design process
- How artificial neural networks aid in mechatronic system development
- Chengdu: battery management system lab to reduce testing
- Process automation: Streamlining simulation workflows
- Monolith AI and Simcenter STAR-CCM+ bring machine learning to CFD simulations
- Tighter timeframes, tougher requirements, less stress? The argument for 1D-3D co-simulation
If you’d like to get in touch with Simcenter Engineering services, email us at engineeringservices.sisw@siemens.com.