Is vehicle virtual prototyping possible? Predict your car’s NVH performance.
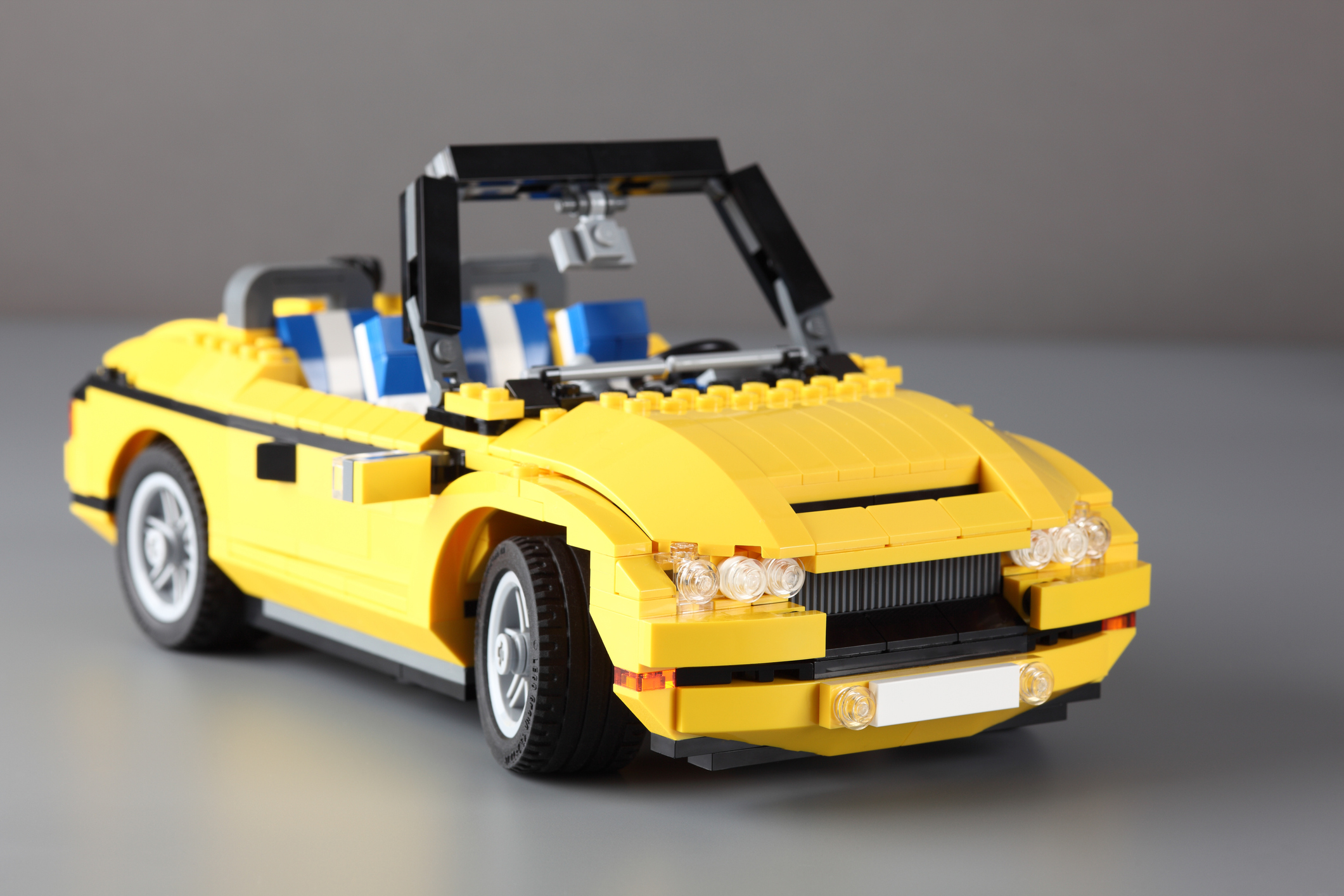
Virtual prototyping: fiction or reality? Learn how you can predict the vehicle’s noise, vibration and harshness (NVH) performance before it exists!
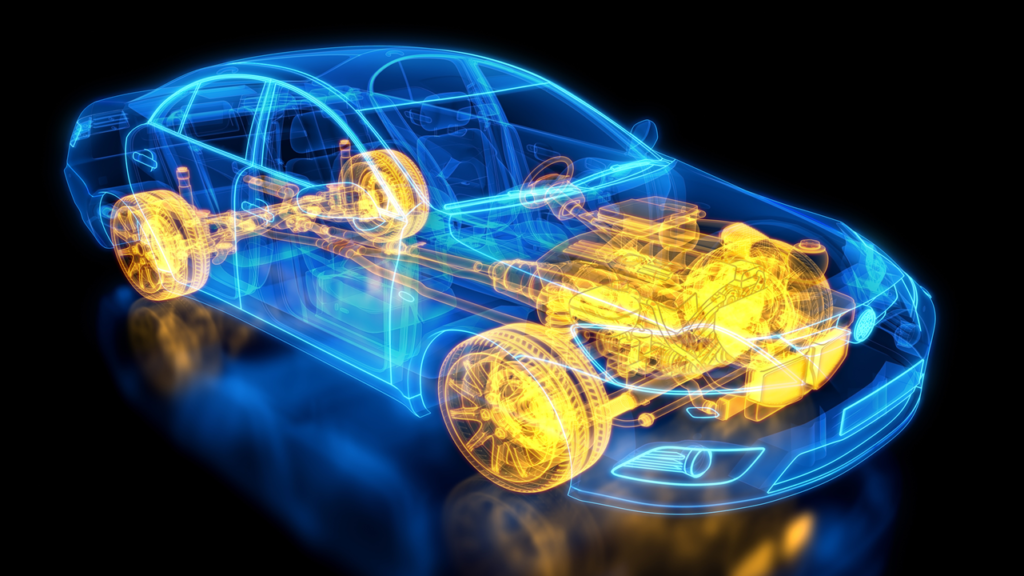
Oh, I love science and technologies! Every time I meet my colleagues from the engineering department, I’m impressed by the innovations they bring to the market. And I love spending time checking out what our research team is working on. It is so exciting to get a glimpse of what the future will bring! I’m also fascinated with the pace of innovation, how innovative technologies from the past developed into interesting methodologies and products.
Discover transfer-path analysis
Have you heard of Transfer Path Analysis (TPA)? Well, picture a vehicle with all its components. Every component may contribute to the cabin noise or to the seat vibration. Thanks to TPA, engineers can easily evaluate the contribution of every system to the overall noise or vibration performance. This enables efficient troubleshooting.
TPA is interesting, but it can be used only when the physical vehicle prototype is available.
How powerful would it be if engineers could forecast the NVH performance of the full vehicle before it exists?
Enable virtual prototyping with component-based TPA
Good news! Virtual prototyping is already feasible today, thanks to technologies like component-based TPA. This technology allows modeling a component or a subsystem independently from its receiver structure. And it can be done for a wide variety of systems: from the tire to suspension, to the engine, to the electronic power steering, to the wiper system, to an HVAC, and so on.

Using a modular virtual integration, the engineers can predict the component noise and vibration behavior as if coupled to different receivers. As result, they can predict the NVH performance of the vehicle before it exists. This makes the full development process more efficient and prevents expensive troubleshooting.
At the same time, the suppliers can rank their components variants independently of their receiver. Great, isn’t it?
Understand how component-based TPA works
Do you want to know more? Then, let me explain the concept with a concrete example.
One of the challenges in the automotive industry is the powertrain electrification. From an NVH perspective, new phenomena must be considered. A tonal, high frequency, annoying sound coming from the inverter (a device that converts DC to AC power in an electric motor) just to mention one.
Firstly, we need to characterize our source in an accurate way.
1. Independent source characterization
We evaluate the e-motor NVH performance independently of the vehicles it will be powering.
The benefits are many: it allows the engineers to rank the sources independently of the receiver and to easily compare the effect of a modification to the source, without worrying about the receiver structure.
How is it possible? Well, we can identify independent forces in test (for example on the test bench) or in simulation for every noise source variant.

The forces and moments are independent of the boundary conditions. It means that we are not measuring interface forces, but we identify so-called blocked forces.
There are different ways to measure or calculate blocked forces based on ISO standards:
- Direct blocked force (measured directly on a rigid test-rig)
- Free velocity/acceleration (source in free-free based on the ISO 9611)
- In-Situ TPA (calculate the blocked forces while the component is attached to any receiver – ISO 20270-2019)
- Contact force on test bench method (under development – ISO/FIDS 21955)
The OEMs can also outsource the measurements to suppliers or perform tests on different laboratories, on different test-benches, even in different countries!
It’s well known that one of the main challenges is the precision in the measurements, especially if we are looking also at the high frequencies.
Simcenter has a great solution for that!
Explore the Simcenter solution
It offers:
- Guided measurement and post-processing procedures with dedicated tools. This yields fewer errors for non-experts and increased accuracy. It also covers an increased frequency range due to dedicated measurement tools and validation checks.
- Accuracy in the measurements thanks to the Qsources (precise measurements even in very small places or difficult to reach).
- Lastly, certain interface points are difficult to access for direct measurements. The difficulty can arise for different reasons, such as a continuous interface or a lack of accessibility of the connection Degrees of Freedom (DOFs). The Simcenter Testlab Virtual Point Transformation (also called geometrical reduction) helps overcome this issue.

2. Target assembly and virtual prototyping
To be able to predict the behavior of the component in an assembled condition, we need to virtually couple the source and the body. The first step is to transform the blocked forces in the ‘new’ interface forces (virtually connecting the component to the vehicle). Secondly, we need to virtually integrate the component into the body. Also, this last step is easy in Simcenter Testlab thanks to the Frequency Based Substructuring (FBS) technique.

Simcenter Testlab will guide you in all the steps. Therefore, this increases the confidence in the final results! You visualize matrices at each step, therefore making it easy to detect possible errors.
We don’t have to forget the airborne contribution: it’s important for this specific application. Also, in this case, the Simcenter Qsources can support with a wide range of suitable sources.
3. Performance assessment
Everything is ready: we have a new model that can be used for objective and subjective performance evaluation. Plugin the selected source into a certain receiver and generate the expected loads and contribution for every chosen assembly.

This analysis helps optimize the final design.
Detect problematic operational forces or transfers, check the effect of modifications, or set targets: all of this is possible at the early design stage at a lower cost!
This modular way of working is exactly what the industry is looking for.
The model-based development for NVH allows reduction in physical prototype testing, better control on the NVH performance & more realistic design target setting towards the component suppliers.
All of these allow to speed up the development of new products and to avoid costly troubleshooting activities at the end of the cycle.
So, are you interested in digging deeper? Please, download our white paper for more info!