Jet Engine Performance: Making Cleaner Skies the ‘New Normal’
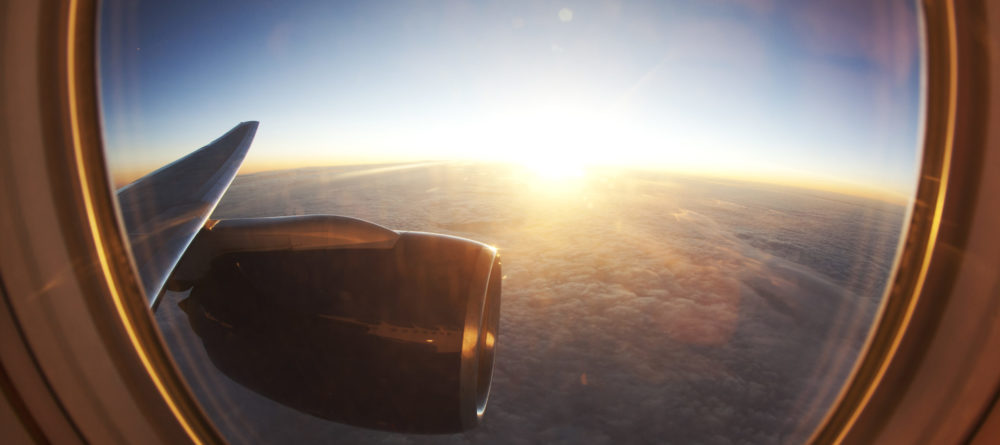
One of the inadvertent effects of the current pandemic has been a drastic reduction in global air pollution. Amidst this unfolding tragedy, this paints a picture of what our future can be if we decide to continue on the path to climate change.
It’s Not Easy Being Green
The aviation industry is responsible for 12% of CO2 emissions from all sources of transport and its primary source is the gas turbine engine. It’s no surprise then that jet engine performance is a key driver in the development of more fuel-efficient and environmentally-friendly aircraft.
Don’t Fail Me
A second non-negligible factor is reliability. When the world recovers global air traffic will return and as always, aircraft will need to perform at peak performance:
Airlines are unwilling to get out of bed for anything less than “99.5%” dispatch reliability, says Clark: “We are not in a business to deal with aircraft that don’t function properly.”
Flight Global
And one only needs to look at the delays currently to Boeing’s 777X due to the engineering challenges of the biggest turbine engine ever built.
Manufacturers can address these jet engine performance challenges with Simcenter. If this sounds familiar it’s because it is; the aforementioned issue with the Boeing 777X was due to challenges with variable stator vanes (VSV); we recently talked about the E-Break project and VSVs using Simcenter 3D to reduce emissions.
Get Better
Engineering an efficient, robust & reliable jet engine starts with its thermo-mechanical performance. Register to watch this on-demand web seminar on “Improving aircraft engine thermo-mechanical performance” where we discuss how we can help address the thermo-mechanical challenges of aero-engines. These challenges can be summarized in three areas:
- Whole Engine Thermo-Mechanical Performance
- Whole Engine Vibration
- Component Structural Integrity & Lifing
Whole Engine Thermo-Mechanical Performance
Jet engines are complex because they deal with complex physics. They work by taking air, cleaning, compressing and streamlining it, they deliver highly pressurized and heated air into the combustion chamber. This, in turn, ensures a more efficient fuel burn. However, pressurization and heat lead directly to thermal and structural problems.
Whole Engine Vibration
For the engine to perform its primary function efficiently, delivering thrust, it needs to rotate vibration-free. If not, given the rotating speeds this could lead to catastrophic failure.
Component Structural Integrity & Lifing
Engine components operate in the harshest of environments, subject to thermal, structural & rotational stresses and fatigue. In addition, they do not perform in one steady environment over the entire mission profile of the aircraft. For example, on a cold day with high air density at ground level, higher thrust is produced; however, on a hot day or at high altitude the situation is reversed. Furthermore, the engine isn’t operating constantly 24/7, rather it is subject to abrupt starts & stops which will affect its overall life.
How can these challenges be addressed? Deep dive into the Simcenter suite of solutions and learn how they can help address these mission-critical challenges for aero-engine manufacturers.
Are you interested to explore aircraft engine thermo-mechanical performance in depth?
Sign up and watch this on-demand web seminar and discover all the possibilities this technology can bring to you.
Comments
Comments are closed.