Lifecycle Insights – Guided simulation workflows: A shift-left simulation strategy
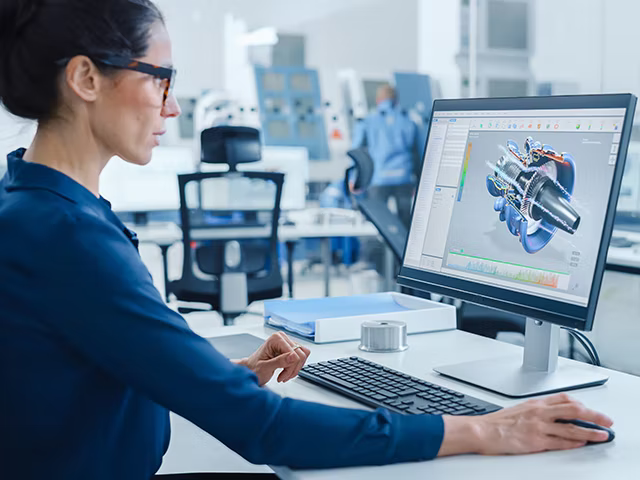
Engineers are increasingly adopting simulation early in the design process. And it’s easy to see why this shift-left strategy is gaining popularity. Simulation enables engineers to meet tight deadlines and satisfy multidisciplinary product requirements.
But companies must overcome some hurdles before they can successfully integrate simulation into their product development processes. Some simulation solution providers are introducing innovative and intuitive tools that address these issues and guide the design process. These tools make it easy for design engineers to embrace simulation, which speeds product development and enables more innovative products.
In this post, Arvind Krishnan from Lifecycle Insights provides his perspective on how simulation templates and guided workflows help companies successfully adopt a shift-left simulation strategy.
Arvind is joined by Patrick Farrell from the Simulation and Test Solutions team at Siemens Digital Industries Software and will provide his perspective on the trend and how Siemens can support companies in their digitalization efforts.
Gaining confidence in using simulation early in design
Design engineers use 3D computer-aided design (CAD) to convert their ideas into digital product definitions. These product ideas still need to fulfill a set of requirements. The requirements for today’s complex products often span electrical systems, electronics, software, and mechanical hardware.
Many engineers still use physical prototyping and testing to confirm that products meet these requirements. This helps them evaluate how the product works under real-world operating conditions. However, these physical prototypes and tests occur late in the design process. If issues arise, they invariably lead to stretched—and often missed—budgets and deadlines.
There is another way: adopting a shift-left simulation strategy. Here, engineers use simulation early in the design phase to digitally test whether their products meet these requirements. They can detect problems early and rectify them. They can explore many design alternatives earlier in the design phase, when changing designs is easier and less disruptive. This approach also reduces the number of physical prototypes and tests required.
Shifting left does have its challenges, however. In this post, we examine those challenges and focus on one simulation capability that addresses them: guided simulation workflows.
The challenges of a shift-left simulation strategy
To use simulation solutions effectively, engineers require specialized knowledge and skills. Unfortunately, many engineers do not have these skills. Sometimes, it takes hours of specialized training to become good at using these simulation solutions. Given today’s tight development schedules, this is a luxury that few engineers can afford.
It can also be difficult to obtain accurate results from the simulation solution. Simulation result accuracy is very sensitive to the inputs, so getting accurate results from simulation requires some experience working as an analyst. Unlike analysts, engineers who only occasionally perform simulations don’t have such experience. Simulation experience gives engineers confidence in simulation. This happens when they see their simulation results correlating with physical testing.
Arvind: Patrick, can you expand on the features in Simcenter that address the challenges associated with a shift-left simulation strategy?
Patrick: Simcenter offers simulation scalability to both design teams at large companies and design engineers at small companies to address these issues. Large companies often have many simulation experts, but they can’t keep up with the demand for their services. So one way to increase their simulation capacity is by automating much of their routine simulation tasks. Simcenter 3D provides a means to easily capture and automate simulation processes and best practices. And since Simcenter 3D is based on the same platform as NX for CAD, the next logical step is to expose some of these guided simulation processes in the NX environment. The porting of these guided processes into the NX design environment helps designers and other less experienced engineers get immediate benefits from using simulation as part of their design process without waiting in a long queue for the simulation team.


Guided simulation workflows using templates
In a guided simulation workflow using templates, an engineer walks through a sequence of predefined steps to set up and perform a simulation. Since these steps are well defined, with only a limited number of input variables, most engineers can navigate through them. The inputs are immediately validated to minimize errors. The simulation outputs are also specified in the template. So, engineers can read the results and compare them against product requirements. Since the templates are fully validated, the engineer can be confident in the accuracy of the results.
Automation also plays a key role here. Using templates as inputs, engineers can easily run many simulations on their designs in an automated manner. If the design changes, they can execute these automated scripts again to get the simulation results for the new design. In other words, the automation engine is like a black box. Engineers just add their template-based inputs to study a specific class of problems and get results quickly.
We have seen what a guided simulation workflow does. Now let’s explore the specific role played by the two stakeholders: analysts and design engineers.
Analysts: Companies that employ simulation have analysts on their teams. The analysts are simulation experts who use these tools daily to tackle many complex problems and verify product requirements. These in-house analysts package their expertise into specialized, problem-specific simulation templates.
Engineers: Novice design engineers without simulation experience can use these templates to perform simulation and identify design problems. The simulation outputs are also specified in the template. So, engineers can read the results and compare them against their requirements.
We will illustrate with a few examples:
- Using a guided simulation workflow template for a boat design, the design engineer selects the parts of the CAD model of the boat where loads and constraints are located as an input, answers some questions about the operating conditions, and runs the simulation. The automation delivers simulation results to the engineer, guiding design decisions.
- Using a guided simulation workflow template for a heating coil design, the design engineer selects the coil CAD model, picks the operating power, chooses a material for the coil from the library of materials that the company uses, and runs the simulation. The temperature profile of the coil guides the engineer to make changes to the coil design.
- Using a guided simulation workflow template for drop testing of electronics, the design engineer selects the CAD model of the electronic component, specifies the drop height, angle of impact, and runs the simulation. The stress plot allows design engineers to make informed decisions about the suitability of the electronic packaging.
Companies adopting guided simulation workflow using templates can realize the following advantages:
- Novice design engineers can embrace the power of simulation and automation. They don’t need to worry about the fine simulation details of setting up a problem, meshing, or result processing. They can confidently use simulation while they go about their design work.
- Analysts can put their expertise to work, creating many such workflows for different product requirements. This allows them the time to focus on tougher product challenges while design engineers take care of day-to-day simulation needs.
- Companies can easily adopt a shift-left simulation strategy. This allows them to build better products, tackle complex product challenges, and bring products to market faster.
Arvind: Patrick, can you give us a case study of a company where simulation templates or guided simulation workflows in Simcenter have helped with a shift-left simulation strategy?

Patrick: One example is with a company that develops plastic (PET) bottles used for consumer beverages. Beverage companies will approach bottle makers with new bottle design ideas that can help make their drinks stand out on the shelf. However, the bottle designer can’t just make any design their customer wishes because, besides being manufacturable, bottle designs must be able to withstand considerable forces when they’re stacked in pallets and when transported from the plant to the store.
A beverage maker will approach the bottle manufacturer with a bottle design idea. The bottle designer will create a CAD model and then pass this model to the simulation team to conduct studies like the top-load analysis. The bottle designer needs to be sure that the new bottle design won’t crumble under that weight, and this is a routine analysis that’s done on every bottle design.
However, the simulation team is small, and the bottling company is constantly working on many designs for different customers. In addition, the bottling company is competing with other bottling companies to win the business, so response speed back to the customer is key to winning the business.
This bottle manufacturer’s design team uses NX. Their simulation team decided to use Simcenter 3D to automate the simulation processes, like the top-load simulation, and then expose the simulation to the design team as a guided workflow. The design team can use this guided workflow to quickly check if new designs could hold up to the stress of top-loading and iterate with the bottle design to arrive at a functional design that meets all the requirements. This new process of design engineers using simulation early in the design phase ultimately led to winning as the company could respond to their customers faster with working designs than their competition.
Integrating guided simulation workflows with SPDM
Guided simulation workflow templates enable earlier simulation. But these workflows can add even more value when integrated with your company’s simulation product data management (SPDM) capabilities.
When templates are integrated with SPDM, design engineers can access guided simulation workflows to get answers to their design questions. They can pursue design exploration without having to worry about tracking and managing design iterations. They can also connect simulation results to the requirement documents and check designs against requirements.
In this scenario, even external stakeholders like suppliers can use the simulation workflows set up by the analysts. In modern product development, many suppliers provide critical product components. These suppliers can use these guided simulation workflows to test their components to ensure that they meet the requirements. Thus, engineers in the company can digitally verify the supplier’s products and confirm their suitability.
SPDM is also used to manage the automated scripts that engineers use for simulation. Using SPDM, engineers and analysts can know which version of the automated scripts was used to execute the simulations for a particular design variant. SPDM systems also track which load cases, materials, and much more were used for a specific analysis. If the automated scripts themselves undergo a change, the SPDM notifies all stakeholders in the design team and ensures that the team always uses the latest scripts.
Conclusion: Simulation-led design now available to all
A shift-left simulation strategy can help companies continually test products against their requirements. This expedites the design process and reduces costs.
Guided simulation workflows can help engineers who lack the confidence and experience to execute simulation during the product design process. In guided simulation, expert analysts or simulation software providers deliver workflow templates. Engineers input these templates into a black-box simulation to study a specific class of problems. This makes simulation accessible to engineers without specialized training.
To fully realize the power of simulation, engineers can integrate their guided simulation workflows with the company’s SPDM. This makes the guided simulation workflow available to both internal and external design stakeholders. It becomes a true company asset.

About Arvind Krishnan
Industry Analyst, Lifecycle Insights
Arvind Krishnan is an industry analyst covering product design and simulation programs for research and publications. His expertise spans mechanical, electrical, and electronics domains, offering powerful insights to companies transitioning to smart, connected products and adopting simulation-driven product development. His twenty-plus-year career has concentrated on advocating for technologies that make a tangible impact on organizational performance