Lowering the design development time of electric motors
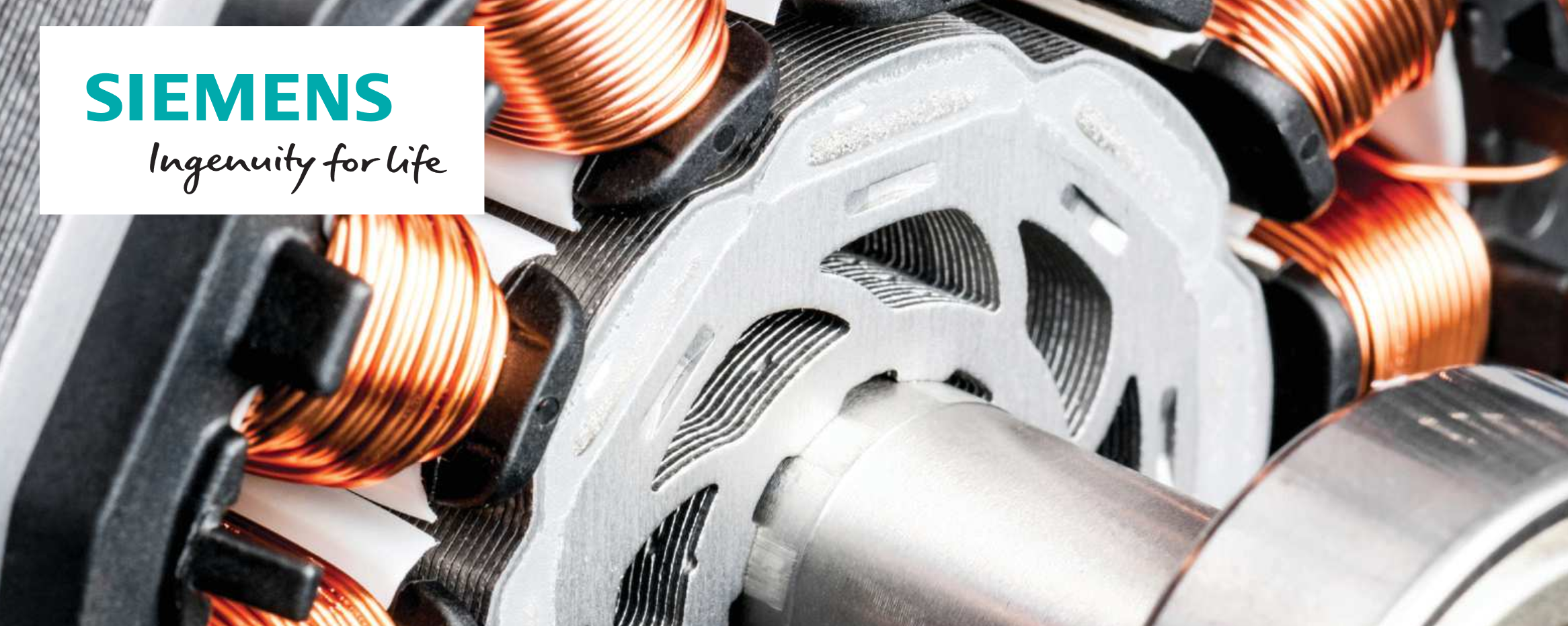
Advances in computational electromagnetics often shift design paradigms of electromagnetic devices. In the 1970s, finite element analysis (FEA) based computational algorithms and tools were being developed. These changed the standard for accuracy so that even to this day during the final stages of design FEA based simulations are carried out to validate model performances.
Another computational method that has been of significance is the so-called magnetic circuits based approach. Compared to FEA, the magnetic circuits based method is relatively faster. It is, however, not as adept as FEA for modeling material non-linearities, flux leakages, etc.
For a modern electromagnetic motor design engineer, the ideal combination of tools to possess are both. During the early stages of design, hundreds, perhaps even thousands of designs have to be evaluated. Fast turnarounds are important for making design decisions with respect to the number of poles, slots, winding configurations, material choice, or, even the machine type. During this stage a magnetic circuit based analysis would be ideal. However, as choices are narrowed and the design progresses, greater accuracy is needed for evaluating machine performance. At this stage FEA based solutions are needed.
Two software, Simcenter SPEED, a magnetic circuit based tool, and Simcenter Motorsolve, an FEA based software, changed the design paradigm for motor engineers. Both are template based. This approach unburdened the designer’s need to set up the model equations, develop computational analysis tools, etc. It also reduced the design development time and became the new paradigm for motor design. Connectivity or seamless model sharing between the two software would further streamline the design process.
In the latest release of Simcenter Motorsolve 2019.1 capabilities to seamlessly share models between Simcenter SPEED and the former has been added. It is now possible to export Simcenter SPEED models to Simcenter Motorsolve, essentially, with-a-click! The following example illustrates this.

The Prius motor has been created using the Simcenter SPEED software and has been analyzed within it. Fast calculations have been carried out to obtain the motor’s back emf, torque speed characteristics and other results which have not been shown. The model has been exported to Simcenter Motorsolve 2019.1 using the SPEED PC-BDC Importer 2019.1. The model efficiency map and nodal forces on the stator calculated using Motorsolve 2019.1 are shown. This process can be applied iteratively to take advantage of the computational powers of both Simcenter SPEED and Simcenter Motorsolve.

Comments
Comments are closed.