Model-based verification and design optimization of controller calibration
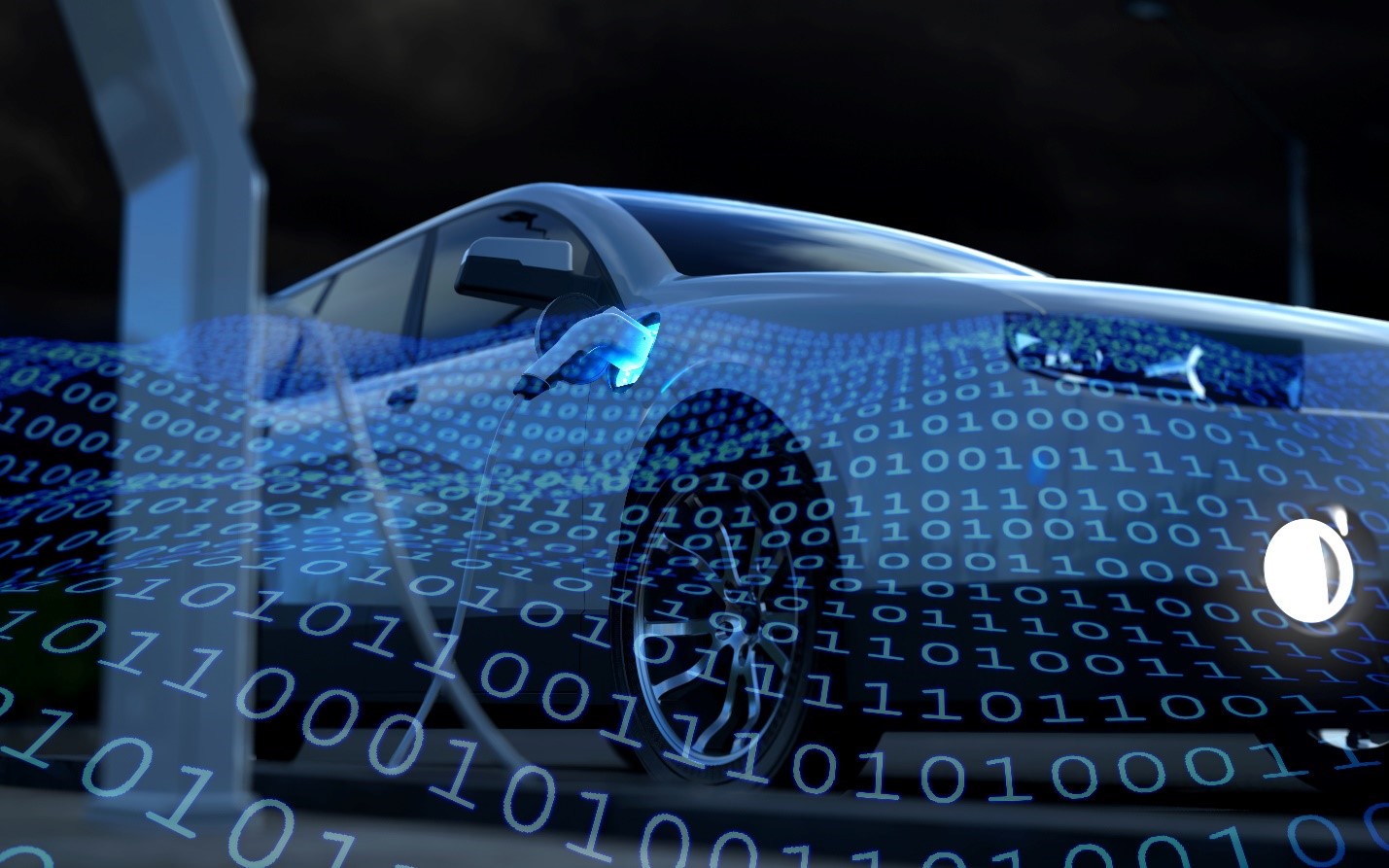
In 1968, Volkswagen became the first company to use a computer in a car. The D-Jetronic, created by Bosch, controlled the fuel injection system in Volkswagen’s Type-3 models.
In 2009, high-end, luxury vehicles relied on 100 million lines of code or more.
Today, even the most basic of vehicles contain millions of lines of code. According to McKinsey Center for Future Mobility, software will account for nearly 30% of a vehicle’s total content by 2030.

“Once, software was a part of the car. Now, software determines the value of a car.”
Manfred Broy, emeritus professor of informatics at Technical University, Munich
The two factors driving this transition? You guessed it – electric and autonomous vehicles.
Electric vehicles

Electric vehicles (EVs) present new complexities and demands of the software that drives them. The software needs to balance emissions, vehicle performance, battery range, and multiple motors for AWD vehicles.
Autonomous vehicles

Autonomous vehicles and vehicles that integrate assisted driving features also complicate software requirements. The most glaring issue for ADAS engineers is the sheer quantity of scenarios needed to test software functionality. Couple this with the fact that, due to liability and safety, these scenarios cannot be reasonably tested in a physical environment.
There have been several high-profile cases of autonomous features not working as intended. Consumers have reported several accidents and injuries caused by automatic emergency braking (AEB) initiating “phantom braking” on roads. Lane keeping systems (LKS) are also experiencing similar issues. The American Association of Automobiles listed the most common assisted driving issues as:
- Abrupt disengagements (sometimes during critical situations)
- Failure to engage
- Erroneous disengagements
- “Ping-ponging” within the lane
- Becoming uncomfortably close
- Complete lane departures within: curves, pavement transitions, exit ramps, on ramps
Clearly, a change is needed.
Controller calibration as a solution
First, let’s define calibration. At Simcenter Engineering Services, we define calibration as the act of adjusting values for certain parameters, functions, and/or tables within the controller to get the desired total system behavior.
Until recently, calibration was done only on physical prototypes. However, this method is no longer an option.
Thanks to model-based development (MBD) and virtual verification, automotive engineers can now frontload and automate controller calibration. This is safer, less costly, and more efficient than traditional on-road testing and calibration.
Accelerate controller calibration applying system simulation
Simcenter Engineering Services’ Ammon Wright recently presented a webinar to demonstrate how MBD and virtual verification can help companies:
- Use system simulation for MiL, SiL, HiL, ViL, and controls validation
- Understand the requirement differences between controller calibration and verification models
- Address differences between virtual calibration and calibration challenges
- Frontload controller calibration at different stages of the development process
- Deploy optimization tools to find the optimal calibration parameter