Modernize Your Simulation Process: Efficient FEA model creation
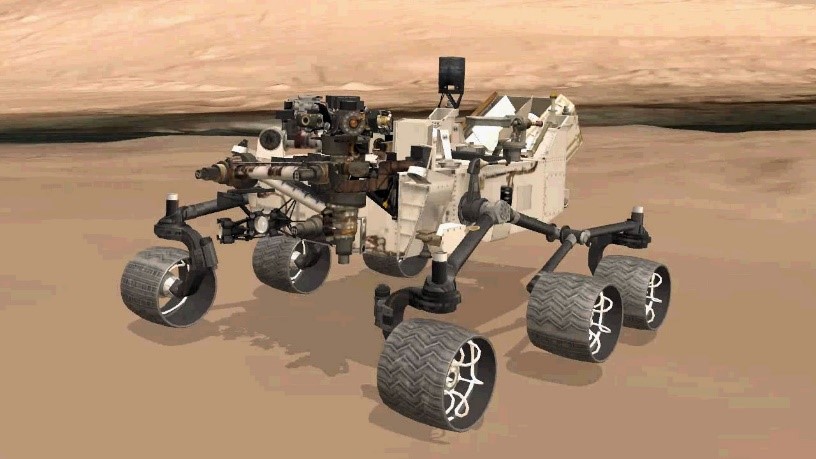
FEA model creation can be filled with a variety of challenges. Traditional obstacles that analyst face every day include the use of existing CAD data, idealizing that CAD geometry to create an accurate FE model, and the process of meshing that model creating a finite element model.
Importing and fixing geometry
In general, the imported CAD model contains more information than is required to create a simulation model with details like fillets, chamfers and holes that may be just too small to be of any significance. If left in the model they will lead to the creation of small elements that try to capture the small detail giving rise to overly large FE models.

Besides small detail, the CAD model may also contain problematic geometry that can impede the creation of a finite element model. Items such as sliver surfaces, short curves etc. will misguide the FE mesher, if left unheeded, and can lead to the creation of badly shaped elements.
Idealizing geometry
There are certain approaches in finite element modeling that adopt different model topologies to improve the efficiency of the model by reducing the model size. These allow you to create smaller FE models without compromising accuracy. Solid element meshes cannot realistically be employed to represent certain modeling topologies, such as thin-walled or frame type structures – the resulting models would be unmanageable. This requires a departure from 3D to 2D, 1D or even 0D finite element types through model idealization.

More advanced analyses, like dynamic response and nonlinear, are more numerically intensive and can also require an iterative solution approach requiring multiple solves.
Reliance on solid elements to represent the design model can lead to the generation of very large inefficient models that take a long time to run (if they can be run at all) and may limit simulation scope to exclude more advanced types of analysis.
Pre-processing
Meshing determines the degree of model discretization and has a direct impact on results accuracy as well as the efficiency of the solution.
In the creation of a finite element mesh, it is important to create a mesh with well-shaped elements – the more distorted the element, the more inaccurate the results that element will display. Badly shaped elements can even stop the solver from completing the analysis. Locating bad elements in a model can be difficult and fixing them time consuming. Model checkout is therefore important, and a lot of time can be saved if errors in the mesh are found before the analysis is submitted, in the modeler where they can be dealt with efficiently.

Other preprocessing challenges include the modeling of complex loading conditions and modeling composite materials.
Keys to success
The challenges listed above, importing and fixing key geometry, idealizing geometry, and pre-processing, are key processes that drive efficient FE model creation success.
Efficient FEA model creation requires the use modern simulation software that takes advantage of up-to-date modeling techniques. Simcenter Femap provides just that, and more. Simcenter Femap provides a complete mesh-centric analysis environment across the simulation cycle, from FE model creation and analysis setup through to postprocessing helping you to gain an accurate, in-depth understanding of your design as quickly and efficiently as possible.
Check out this 30 minute on-demand webinar to learn how Simcenter Femap quickly and easily addresses the process challenges above, for more efficient FEA model creation.
Modernize Your Simulation Process: Efficient FEA model creation