New electric motor design tools with realistic workloads
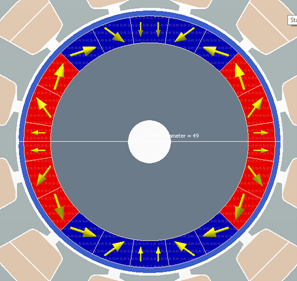
Simcenter E-Machine Design and Simcenter Amesim working together for better electric motor design
The typical electric motor design sequence involves many iterations, especially during the early design stages. Identifying the most important load points for a given design problem is necessary but complex.
Our release of the Simcenter Motorsolve software in 2020 added a new set of experiments which leveraged user-defined duty-cycles. This capability has been enhanced in Simcenter Motorsolve’s replacement, the Simcenter E-Machine Design software. With an exchange of the machine performance requirements from Simcenter Amesim, Simcenter E-Machine Design can use realistic vehicle behavior to advance the design process. The losses and top five most important load points are calculated and transferred between the software.

This technology includes several standard Electric Vehicle drive-cycles for the automotive sector. To activate this feature, the user simply defines the desired vehicle torque and rotor speed details.
Pulse Width Modulation analysis with arbitrary voltages
Calculating machine performance based on measured or arbitrary voltages using traditional finite element analysis [FEA] can be time-consuming and impractical due to the signal’s switching frequency. In Simcenter E-Machine Design, the Pulse Width Modulation (PWM) analysis experiments utilize analytical analysis coupled with FEA to determine accurate performance in a timely fashion. An additional option of assigning user-defined arbitrary voltages to the Phase Windings is now part of the PWM analysis capability.
Therefore, digital twins or model calibrations can be based on measurements imported directly from dynamometers or other sources.

Halbach Array electric motor design in Simcenter E-Machine Design

Simcenter E-Machine Design
Rotor templates support the creation of Halbach array patterns with even and odd numbered magnet segments per pole. It also includes the ability to apply unevenly distributed segments with user-defined magnetization directions. As a Halbach array generates the poles in a desired volume (the air-gap), there is a secondary benefit to the Rotor design. There is flux cancellation in the volume where the core would be, and so no back iron or steel is required; a nonmagnetic lightweight core can be used instead, significantly reducing the mass of the Rotor.
“…electric motors based on the Halbach array offer measurable benefits over conventional designs, including high power density and high efficiency. One of the enablers of these benefits is that a Halbach array motor does not require Rotor laminations or back iron, so the motor is essentially ironless. This significantly reduces eddy current losses and hysteresis losses… “
Excerpt from “What is a Halbach array and how is it used in electric motors?” by Danielle Collins highlights the benefits of Halbach array electric motor designs.
Maximum torque and flux weakening control
Motor performance is highly dependent on the control strategy. This link between the motor and the electronics impacts performance parameters like efficiency, loss and the machine’s output power. Simcenter E-Machine Design continues to support these two key control strategies.
- Maximum torque per amps
- Flux weakening based on optimal load points
You can have confidence that your experimental data more accurately replicates the physical conditions using these control strategies.

The figure above showcases the Efficiency map experiment for an electric machine where the newly added MTPA drive cycle and the Flux weakening control strategy are combined.
Simcenter E-Machine Design impacts the electric machine design process. Significantly improve your efforts by including realistic vehicle behavior and control strategies in your experimental outcomes.
To learn more about Simcenter E-Machine Design please consider the following:
Learn more about Simcenter E-Machine Design and Simcenter Amesim workflows in this video.
In this episode, we’re joined by Adrian Perregaux, Product Manager of Electromagnetics at Siemens Digital Industries Software, His team focuses on low-frequency electromagnetic solutions within the Simcenter portfolio. Adrian shares his insights into the evolving world of electric motor design and the role of simulation software in enhancing this process.
The story of electric machine design is changing at a fast pace. With Simcenter E-Machine Design as their ally, engineers can conquer challenges, accelerate their time-to-market, and create products of unparalleled quality, efficiency, and performance. Find out more in this blog