Optimizing a delta robot design and performance using system simulation
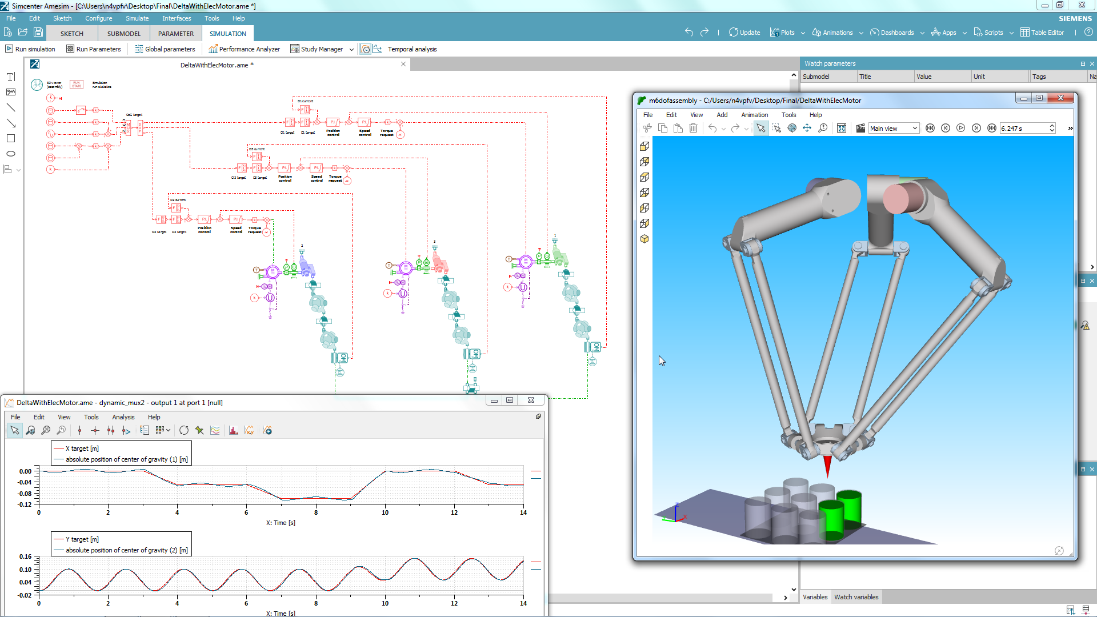
Handling delicate pieces of chocolate with care so that they arrive intact in their box requires a lot of thoroughness. For manufacturers, the packaging process is no longer done manually and is now an automated process performed by machines for the sake of productivity. However, combining the two concepts of automation and manipulation of delicate foods does not seem obvious. The end product could get damaged.
This is what Raymond Clavel and his colleagues from the Polytechnic University of Lausanne acknowledged during a visit to a chocolate factory. Specialized in robotics, the team of researchers investigated on how to move small, light elements as smoothly as possible while achieving throughput and reliability targets set by the manufacturer. This spawned the idea for developing a new type of robot: the delta robot.
Delta Picker manipulating chocolate bars
A robot composed of three arms able to handle small objects at up to 300 movements per minute. This ensures excellent throughput for the manufacturer that requires packaging within industries such as pharmaceuticals or foods … but how do you make sure that the machine will minimize rejections, be precise enough or not consume too much energy? Of course, physical testing can be performed on prototypes, but it is expensive and time-consuming.
This is why the use of simulation to design a machine like a delta robot and to analyze its performance in the early design phase, appears today as essential. Introducing simulation into your product design process allows you to define the optimal architecture based on the best balance between performance attributes. Luckily, this balance and optimization can be achieved through analysis using system simulation.
In the webinar: Improve machine productivity while focusing on energy efficiency using system simulation, Lionel Broglia first introduces the machinery market trends and challenges, and how Siemens’ system simulation solution, Simcenter Amesim, can be a key tool for industrial machinery players.
In the 2nd part of the webinar, Lionel jumps into the topic of interest: showing a live demo of how using Simcenter Amesim can help you pre-design your delta-picker architecture and analyze the drive performance on the whole system so that you can meet and balance all of your performance requirements.
Optimizing Delta picker design using Simcenter Amesim
The demo is done on 3 parts
- First Lionel shows how you can do early sizing of a multi-physics system and start creating a model without having CAD geometry.
- Then you will learn how to evaluate specific performance requirements by the computation and analysis of requests for speed and torque
- Finally, once the motors are selected you’ll understand how to do a virtual integration into the whole system. By performing simulation over various working scenarios, you will see that you can check and compare performance, precision and energy consumption.
Connect and learn more about optimizing the size of electric drives for a delta picker robot while enjoying a nice – non-squashed – confectionery.