Perfecting transmissions need not be at evolution pace
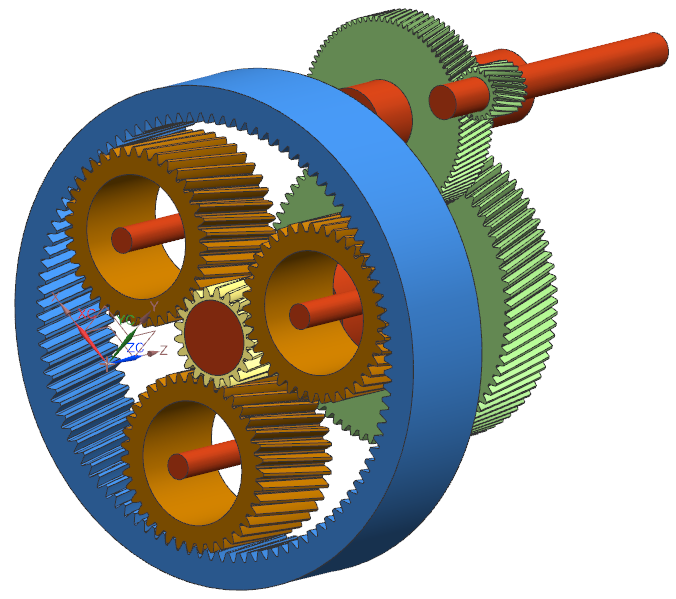
Gears are undisputedly engineering marvels. Ever since their existence (some predict it as early as third century B.C.) gears were used in sophisticated transmissions – rotating mills, irrigation wheels, the water clock, and other complex mechanisms. But have you come across a gear that was neither carved, cast nor forged nor 3D printed, but biologically evolved? I can hear you saying spiny turtle characterized by a sharp, pointed, spiky-edged carapace and wheel bug’s back. Let me give you an additional clue – a functioning intermeshing gear mechanism capable of generating 400 gs of acceleration and velocity of 6 meters a second.
Issus coleoptratus planthopper insect measuring 6-millimeter size is an ingenious bug when it comes to gear transmission. The species evolved over centuries in pursuit of an ideal jump. Eventually, its genes mastered a perfect transmission, which helps to synchronize the hind legs during jump within 30 microseconds. Using the build-test-improve engineering approach, we humans too have performed incremental innovation on gears over centuries. Minimizing vibration and noise of gears without compromising efficiency and reliability remains a key area of research
Every mechanical engineer recognizes that gears and machines (rotating) are bosom buddies. Any imbalance due to ineffective designs will lead to disproportionate speed/torque increasing vibration and noise radiation. Industrial machinery, especially rotating machinery factory floor comprises various noise sources such as motors, gears, fans, compressors, fluid flow, electrical machines, etc. A noise contribution analysis of the factory can highlight the importance of reducing noise from gear transmission. Rotating machine manufacturers and transmission understand that the elastic deformation of gear mechanisms or even the teeth are the cause for the noise. As the design of gear systems involves many parameters (misalignment, gear microgeometry, housing flexibility), modeling and analysis tools are the sustainable solution to master the complexity of gearboxes.
Drivetrain simulation
A gear transmission system consists of various components such as gears, shafts, and bearings. Modeling, parameterization, and iterations for relatively complex transmission models could take multiple days. Moreover, analyzing a transmission at a system level to achieve better performance in terms of efficiency, noise, and reliability, is challenging even for a sophisticated analyst. Designers of transmissions can choose from two software solution families to support their design and simulations:
-
- The first solution is targeted at gearbox design and provides gearbox-specific know-how that can be used in the design process. This solution lacks certain system-level dynamics simulation capabilities.
-
- The second solution includes general-purpose multibody simulation tools (for example Simcenter 3D Motion), in which the drivetrain geometry must be created along with simulation-specific elements (joints, axis systems, bodies, force elements). In this simulation environment, users can predict nonlinear dynamics, noise and vibrations and durability performance sufficiently accurate and in a feasible timeframe.
To help transmission engineers predict transmission behavior in view of NVH, transient, durability and other advanced analyses accurately and efficiently, Siemens Digital Industries Software has introduced a new software ‘Simcenter 3D Motion Transmission Builder’ with the Simcenter 3D 2019.1 release.
Simcenter 3D Motion Transmission Builder
Until recently, building a full transmission model in a multibody simulation tool was a tedious and error-prone manual process. With the Simcenter 3D Motion Transmission Builder engineers can efficiently set up simulation models in the multibody simulation environment, and effectively predict and optimize their designs based on accurate simulations. The software key highlights are listed below.
-
- Simcenter 3D Transmission Builder brings in-depth, gearbox-specific ease-of-use into the multibody simulation process
-
- The contact detection method in the software has been validated against nonlinear finite element (FE) solvers to dynamically account for effects such as microgeometry modification, misalignments, tip contact, wedging and others
-
- In addition, a novel method based on model order reduction (MOR) is adopted to efficiently analyze lightweight and ring gears in a dynamic multibody simulation environment
-
- The Simcenter 3D Motion Transmission Builder enables engineers to breeze through transmission challenges
Below I show a sneak peek of the software in action while building a 750-kW wind turbine gearbox taken from NREL. The gearbox technical data is available to the public from NREL.
Still not convinced? Are you working on gear transmission and interested in knowing more about using simulation for industrial transmission applications?
Join an engaging webinar on the topic “Predict and reduce gear vibrations in rotating machinery”. The webinar is offered free of cost. So be our guest.
Download our technical article “Industrial Drivetrain Simulation: From Gear Layout to NVH Analysis”
Both the webinar and whitepaper gives you more insight into the latest technology to accelerate gearbox engineering.