Simcenter 3D Powder Bed Fusion: New voxel mesh and other improvements
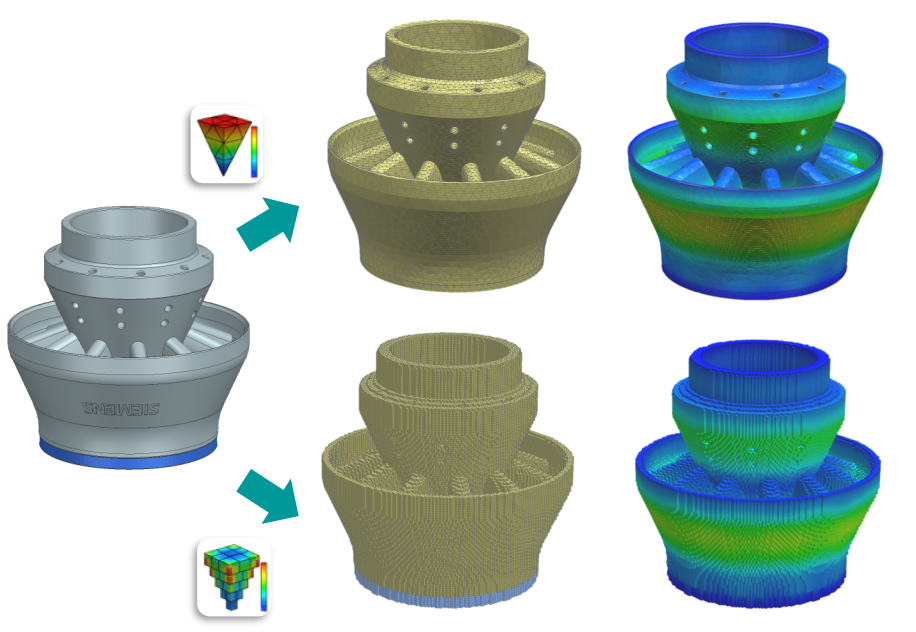
Additive Manufacturing and why it’s a growth industry
For Additive Manufacturing Engineers, knowing how the part will deform during printing and after cooldown is essential. Tools that provide this information quickly are critical to the modern development workflow. Any supporting software, therefore, needs to be relatively easy to use without geometry clean-up operations or meshing failures.
Where has Additive Manufacturing been utilized?
According to Mckinsey reports, Powder bed fusion was, in 2020, a €13.4 billion industry and is expected to grow significantly. New technologies within the field are removing barriers to adoption and opening it up to new markets. At the same time, the green agenda and high fuel prices are encouraging many industries to find new ways to design and manufacture. The benefits of 3D printing include its ability to make parts without a long and costly tooling process. This has long been an advantage to those prototyping new ideas in small specialist teams and specialist part manufacturers with short product runs. However, its limitations, such as its slow method of manufacturing parts have, until now, prevented it from being used widely in mass manufacturing.
Why is Additive Manufacturing growing now?
The green revolution that the world is currently embracing demands that vehicles become more efficient. This is particularly true for electric vehicles, where the fear of range anxiety can be a significant barrier to customers. Subsequently, manufacturers are looking to light-weight their products to reduce the demand on their fuel source. With 3D printing, all non-essential material can be removed from the design. Mckinsley has reported that Airbus has produced an additively manufactured titanium bracket that is 30 percent lighter without compromising performance or durability. With such possibilities, mass market manufacturers will also look to benefit from 3D printing in both the development and manufacture of products. The complex structure of these organizations with expert design, production, and various other engineering sub-division may highlight other complexities of using 3D printing on a large scale.
What is holding Powder Bed Fusion up?
Powder Bed Fusion, process simulation engineers face common reoccurring problems. These problems can make building their models significantly longer, require highly skilled individuals to resolve, or just be long processes of many person-hours. These problems can be categorized into the following groups:
The difficulties that Powder Bed Fusion needs to overcome
Meshing
Meshing that follows the geometry of the product, known as exact meshing, often has meshing failures. These occur because of inaccuracies or problems in the geometry provided. Fixing such geometry problems takes the skill of an experienced engineer, increasing the time and cost of the project. However, In many such cases, the fine detail provided by a geometry mesh is not essential.
Support structure modeling
With exact meshing solutions, the user must obtain the mechanical properties of the supports through a homogenization procedure. This is a laborious process since it requires the engineer to apply the properties to each individual support structure geometry type.
Long processes that require experts are not appealing to any organization, but they are particularly undesirable to mass-market manufacturers that require economies of scale to get a return on investment. Therefore, to make 3D printing more appealing to an organization such as an automotive manufacturer, they needed a solution that would reduce the burden on a specialist engineer and allow a more generalized engineer or even a technician to perform a significant amount of the workload.
Calibration
The heating and cooling, that takes place during the printing process, will produce high internal stresses. These internal stresses will result in deformations of the parts being printed. The complex physics of this process is not modeled directly but replaced by a simpler type of simulation. The input values that we need for this simulation are inherent strains, i.e., initial strain values that are injected into the elements. These inherent strains can be orthotropic and are obtained via an automatic calibration procedure.
How are these difficulties being resolved?
With Simcenter 3D Powder Bed Fusion the meshing and support structure issues are no longer a concern due to the introduction of features to directly tackle these challenges:
Meshing
Since the introduction of voxel meshing, the complexity of meshes can be significantly reduced, removing the need for a specialist on many meshing tasks. With the new voxel solution, meshing failures will no longer appear, and the meshing can be done automatically. Even geometries containing small imperfections can be meshed correctly.



Support Structure modeling
The laborious process of obtaining mechanical properties and adding them to your model has been significantly simplified, resulting in a huge reduction in the total effort. In Simcenter 3D Powder bed fusion, the volume fraction of every voxel element is automatically calculated i.e., the percentage of volume taken up by the support structures. With this volume fraction value, the application directly calculates the mechanical material properties of the support structure. This automatic procedure calculates the material properties for every support structure.
Calibration
The 2212 Simcenter 3D release saw the introduction of a new calibration process, which was made possible due to the new simulation capability of the cut-through operation. This feature allows a whole new technique to be used in the calibration process, with the aid of the new wizard, empowering even less experienced engineers to complete the task. The procedure involves printing two beams, cutting them partly off the build-plate, and measuring their resulting bending deformation.



Speed up your process and free up your experts
Large products such as Simcenter 3D can if not properly managed, become cumbersome and hard to use simply because there are so many options and user personas. In the case of Powder Bed Fusion, there are a growing number of functionalities, and as a result, a non-expert could become overwhelmed if all possibilities are available. Conversely, an expert may become frustrated if the required features are hidden behind endless walls or wizard GUIs.
To overcome this concern, when the developers created the new voxel-based meshing tool, they designed it knowing it would need to work for a less experienced engineer. While the existing tetrahedral mesh would be a solution where an expert would want full control. As a result, there are now two options in the Process Simulation ribbon, as shown in Figure 6. The new voxel mesh and common tools such as those used to model mechanical (constant strain), and simple cut-off operations, are available under ‘Start Powder Bed Fusion.’ This tool significantly simplifies meshing, support structure modeling, and calibration. While the tetrahedral mesh and more advanced tools, such as those used for thermo-mechanical simulations, are available under ‘Start Advanced Powder Bed Fusion.’

Summary
The latest version of Simcenter 3D enables engineering teams to stay integrated by increasing the number of tasks that are possible for the non-specialist, reducing the risk of teams becoming siloed. With voxel meshing methods, the time taken to complete the meshing process is significantly reduced, allowing the whole manufacturing process to go faster. These two advantages free up meshing specialists in the organization, allowing them to generate more income by exploring the possibilities that it takes an expert to investigate, rather than spending their time on relatively repetitive tasks.