Reach great Sustainability successes with Simcenter System Simulation – Part 2
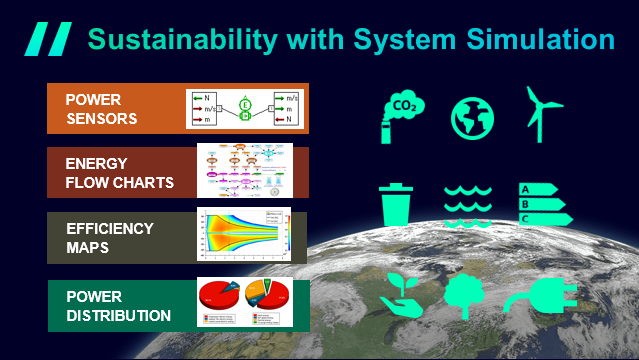
This blog post is the Part 2 of a blog series for addressing industry Sustainability challenges with Simcenter System Simulation . A quick overview is introduced in the previous Part 1 with explanations why Simulation is really appropriate to address Sustainability challenges.
In this blog let us explore how simulation helps to address sustainability challenges of components supplier i.e., everything ranging from gears, pumps, compressors, extends up to renewables and energy saving, or simulation in operations. They all contribute to reach your Sustainability targets in your company. Let’s have a look together to understand how System Simulation can help there.

Sustainable components with suppliers
Sustainability encompasses a broad range of subjects that cater to diverse user profiles, extending beyond integrated systems and production machinery to include individual components integral to smart products. Upon closer examination, virtually every component within machinery holds implications for sustainability. Addressing these challenges early in the design process has the potential to transform them into a sustainable competitive advantage by gaining a deeper understanding of the functional physics involved.

Practically, we see that System Simulation is well adapted for all components. It concerns gears, pumps, compressors, heat exchangers, etc.

💧🌡⚡️ You can see that there’s the “energy efficiency” topic always listed when designing or upgrading these components. For the hydraulic/pneumatic components, the thermal-hydraulic or two-phase flow components, or the electro-mechanical systems. With some additional moves towards electrified components.
Within few seconds of execution, System Simulation can provide metrics about power losses, efficiencies or energy saving, so it’s easy to investigate multiple scenarios. Simulation can also help to justify the investment for better components, to buy better efficient products that are usually more expensive, or to switch to electrified components that require some adaptations.

⚡️🌡🔋 Practically, we can think about electrified gear pumps, or electric fans or any other components to replace your legacy components. You can investigate the thermal management of e-machines, up to the battery runaway to ensure safety and to prevent the risk of fire. All these aspects need to be formally checked during your sustainability journey to convert the components you’ve been using for years to more efficient or electrified components. That’s where digitalization is of great help and makes the difference with other traditional approaches.
Renewables and energy saving
Let’s now look at the renewables and energy saving. Just to say that we have such energy application with Simcenter Amesim. For example with the Green hydrogen production.

♻️💧⚡💰 We can predict in few seconds the distribution of Hydrogen production over months thanks to wind turbines, solar panels, wave energy converters and an electrolyzer to store energy in the hydrogen tanks. At the end, green energy is produced and it can be used for your production machines or plant facilities, so that your carbon footprint is significantly reduced.

♻️⚡🔌 Also we can go more at the electrics side, with this digital twin of a green hydrogen-based microgrid. The goal is to optimize the global system efficiency considering thermal management. You can check your power mix (solar, electrolyzer, fuel, cell, battery, …) over months. To finally verify that it’s compatible with the electric load, and that it can be supplied properly to the grid.

☀️⚡🌻🌏 You can even consider using solar panels for producing electricity with solar energy, which can be stored in batteries with BESS (battery energy storage systems). The digital twin can help find the optimal settings for sizing the solar panels depending on your GPS location (if you’re located in Tokyo, Berlin, Madrid or Detroit) with different solar irradiances, weather conditions, …) to simulate if it’s sufficient to supply enough electricity for all your factories depending on the seasons or during the different months of the year.
🚢🐟 For ship delivery when shipping your production to different countries worldwide, you can consider retrofitting cargo ships with Flettner rotors to improve propulsion. It’s a way to increase fuel economy and get significant reduction of CO2 emissions with just a small investment.

You can even study the influence of the sea route conditions (good weather, bad weather) and the ship speed (slow, fast) on the travel time, fuel economy and CO2 emissions.
Just to say that System Simulation is perfect and well appropriate to reach nice achievements for sustainability in your company.
Everyone is quite impressed by all these capabilities to get great outcomes. But it’s not only during the product engineering process with “Simulation for Design” that you can benefit from System Simulation capabilities to achieve sustainability goals., Also through the “Simulation in Operations” where practical significant gains can be reached directly onsite, close to the hardware devices.
Simulation in operations
The “Simulation in Operations” technique helps to leverage the simulation model built during the design phase to have insights during machine operation or in-services. Either with Edge computing or with Cloud computing.

Here’s an example of « Simulation in Operations » with an Executable Digital Twin (xDT). It’s an industrial heat pump for districts with Model Predictive Control (MPC).

🏘️🌡️♻️🔥 Practically it’s a gas turbine combined cycle (GTCC) with a heat-pump added, also a storage. It’s executed in real-time, using a mixed approach between the field streamed data and the results of the dynamic simulation model. So it allows predict in real-time the future behavior so one can benefit from the strong fluctuations in energy price and production profiles. With a significant reduction of OPEX (operating expenses). Practically, it’s software (controller) and hardware (plants) onto a real system.
We can also imagine other use cases in operations. For example, with artificial intelligence (AI) where the digital twins can help generate a large amount of synthetic data. So it would replace the data generation with hardware devices in operations, which needs to be repeated until new scenario is being found, online. The high-fidelity simulations can quickly mimic the hardware behavior and generate the necessary data and reduce the costs, investigating many scenarios in few seconds of execution. Thereby the virtual data can complement with the real operational data, to train the AI algorithms upfront, offline.
To conclude, we can extend the scope of System Simulation to help achieve the sustainability targets, up to a sustainable production at the factory level. Typically customers have interest to get metrics for its CO2 transparency, to optimize its Energy management or to better know how to use On-site Renewables.

🏭🚗🚚 Target the carbon neutrality of your factory, implementing renewables energies or hydrogen fuel cell forklifts, batteries or engaging with process electrification. There are many technology options available. System Simulation can definitely provide insights to select the best options, storage systems, plant configurations while optimizing the cost of operation. One can also take into account industrial buildings’, its HVACR or surrounding systems to become more sustainable. It helps to take strategic decisions to transition your assembly plants or facilities to reach carbon neutral operations. What a great objective!
Takeaways
It’s now time to sum-up the main benefits of using System Simulation for Sustainability.

- Advance your Sustainability activities, as Simcenter System Simulation solutions offer all the out-of-the-box capabilities needed- the energy/power analysis tools, to check the impact of bio-materials, to minimize resources, …
- Address new challenges or requirements with System Simulation as the industries shift towards more sustainable options.
- There are also some certifications like the ISO 50’001 and few others that help the organizations to integrate sustainability in their daily operations.
- Finally consider a good understanding of the expectations, considering green targets with energy saving, not just cost saving. In such case, System Simulation is well appropriate to be successful.
If you’ve missed it, please read the Part 1 of this blog series to get a general overview how System Simulation helps being successful in your Sustainability journey thanks to digitalization.
Learn more about Siemens Simcenter Amesim
Simcenter Amesim is the leading integrated, scalable system simulation platform, allowing system simulation engineers to virtually assess and optimize the performance of mechatronic systems.