Products
Saving lives with brake assistance systems
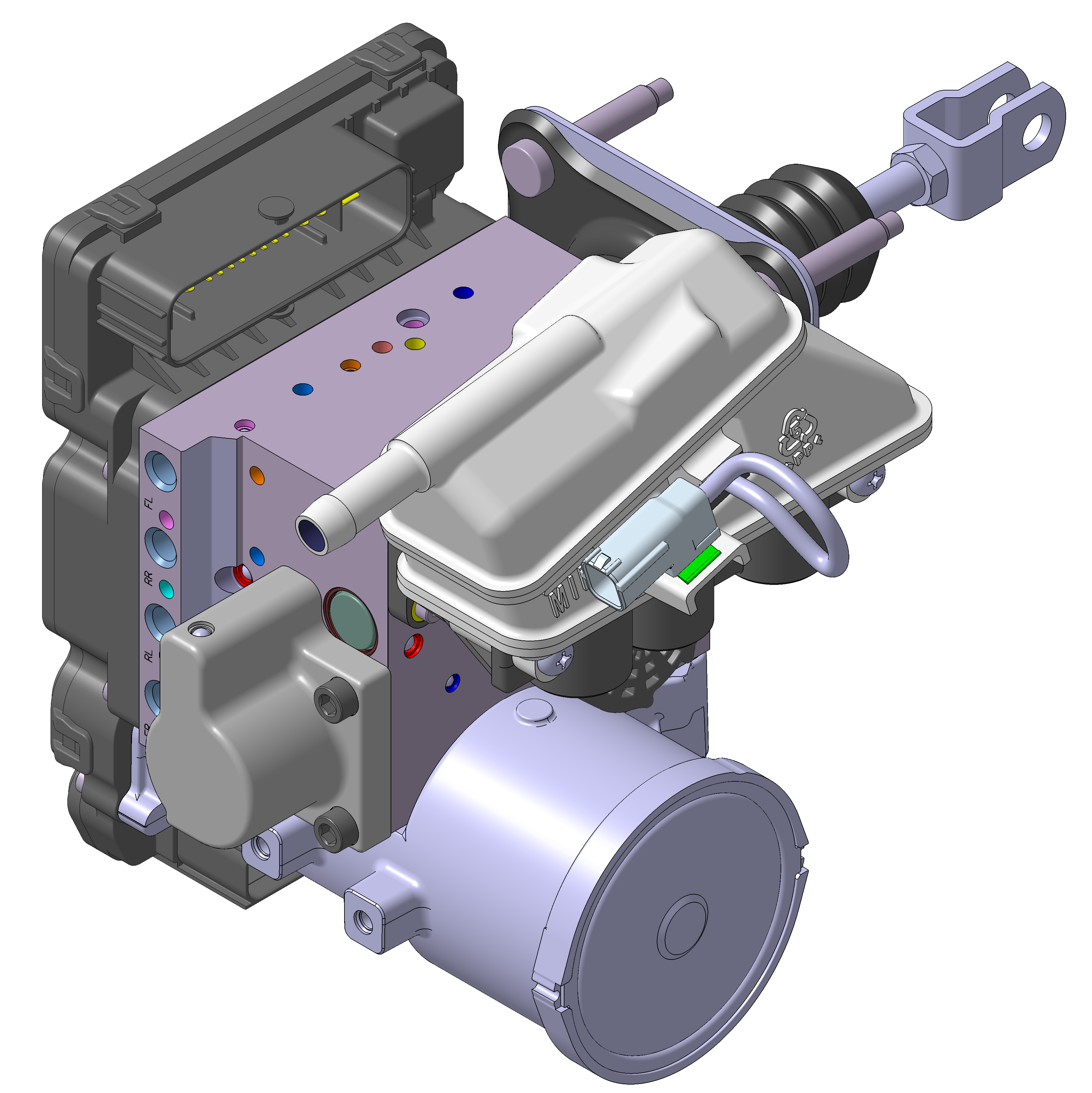
ERICH WACHTER |
TI-QUANH NGU |
|
Expert in the development and
|
Development and simulation of electronic braking systemsMando Corporation Europe in Frankfurt, Germany |
|
What are the current challenges for your company? | ||
Erich Wachter: Automated driving and vehicle electrification have drastically changed all automotive systems. Braking systems have been no exception to this trend. Of course, emergency braking systems still need to fulfill their main role – to save lives, – but in the context of automated driving functions, they now require ever-faster pressure buildup. Moreover, unlike internal combustion engines, hybrid and electric vehicles often miss vacuum to actuate the brake booster. To provide braking support in emergency situations, additional components are needed. To address these challenges Mando has developed an innovative electro-hydraulic braking system – the integrated dynamic brake (IDB). | ||
What’s different about Mando’s IDB? | ||
Ti-Quanh Ngu: The key differentiator of our IDB is a greatly reduced braking distance. How do we achieve this? The braking impulse is transferred electronically from the brake pedal via a sensor to an actuator. This actuator generates the hydraulic braking pressure by means of a powerful brushless direct current (DC) motor, which moves the hydraulic pistons via a screw drive. The electronic control system takes over the driving dynamics control functions. A mechanical connection between the brake pedal and the hydraulic unit still exists – as a backup to ensure the braking function in case the vehicle’s electrical/electronic systems fail. In contrast to conventional electronic stability program (ESP) systems (where the electro-motor only functions when the control system modulates the pressure), in electro-hydraulic braking systems, the electro-motor is activated for every braking maneuver and is, as a central component, responsible for the pressure buildup, and braking performance. | ||
How did this innovative design impact your development processes? | ||
Erich Wachter: Obviously, such innovative systems in charge of human security must be thoroughly tested before being released to the market. That increases the costs. To be faster and more efficient than our competitors while continuing to ensure security, we maximize the use of simulation, particularly the use of Simcenter Amesim. | ||
What kind of analyses do you run with Simcenter Amesim? | ||
Ti-Quanh Ngu: For the IDB, we used our Simcenter Amesim hydraulic model of the brake assistance system to find out how changes in the hydraulic circuit and variation of different parameters impact the overall braking system’s performances (time-to-lock value, stopping distance…). By changing the performances of the electrical motor, as well as hydraulic properties, we can adapt the braking system to the vehicle configuration without running any physical tests. What is exciting about Simcenter Amesim is that every small change in the hydraulic circuit and its components can be captured by the software. | ||
What do you appreciate the most in Simcenter Amesim? | ||
Erich Wachter: You can use the same model from the initial concept, to system and component design, until vehicle integration; and it can be also exported into another software. We can easily create S-functions to couple our models with Simulink. Finally, we use our models to demonstrate to our customers that our products behave as expected once integrated into the vehicle. Simcenter Amesim enables us to run as many simulations as we need without damaging hardware, keeping our development costs under control. | ||
How did Simcenter Amesim impact your day-to-day work? | ||
Ti-Quanh Ngu: Simcenter Amesim has completely eliminated the need for dealing with mathematical formulas: we can rapidly get accurate results by simply using the validated components, and evaluate the performance of multiple IDB configurations under different operating conditions. We can even exceed challenging customer specifications: for instance, we have found out a design which reaches caliper pressure gradient of hundred bars within less than 150 milliseconds.
To find out Mando’s use case and simulation results, download this ATZ article.
|