6 Things YNTK About Simcenter MAGNET & Motorsolve 2020.1
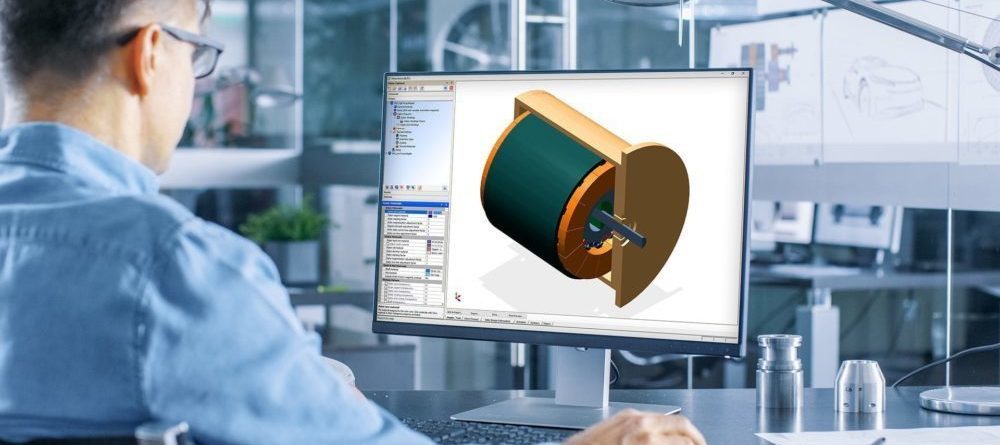
In this release, we’ve added many new capabilities to Simcenter MAGNET 2020.1 and Simcenter Motorsolve 2020.1 to provide a comprehensive digital twin for electromagnetic simulations, extending the multiphysics and enhance the user experience. For example, we address the challenges facing motor designers in a number of industries with new loss modeling and demagnetization predictions. Also, the lumped circuit modeling in the finite element domain is a crucial addition for bus bar designers. Let’s explore the top 6 things You Need To Know:
Comprehensive Digital Twin for Electromagnetics
1. New Demagnetization Model in 3D

Consider the huge demand for permanent magnet motors in electric vehicles and aerospace applications. This is due to the high power density of PM motors.
However, one drawback is being susceptible to demagnetization by:
- Current overload. For instance, during acceleration
- Increase in temperature. This happens as the motor goes through the drive cycle.
In addition, the 3D effects can be significant. The irreversible demagnetization behavior of permanent magnets shortens the lifespan of these motors. It must be avoided without over-engineering as permanent magnets are costly.
However, this process is challenging to simulate because it takes into account many dynamic factors (e.g., magnet operation in terms of nonlinear characteristics and operating point in terms of loading and temperature) and requires data to capture the magnetic characteristics accurately.
With Simcenter MAGNET 2020.1, there is now a demagnetization model for permanent magnets in the static, transient and transient with motion solvers in 3D.
Model nonlinear permanent magnet materials:
- With constant permeability before the knee point
- With dynamic irreversible behavior (recoil curves are desired in the 2nd quadrant)
- Ease of defining magnets from information that is already available in data sheets (remanence, knee & coercively)
- Computationally fast: the same order as a linear model

The demagnetizing behavior of an axial flux machine. Left: Demagnetization field. Above: Simcenter MAGNET model view.
2. Lumped Circuit Components in Electromagnetic Solution Domain
In many cases it is necessary to insert circuit components into the model geometry to create a realistic digital twin. For that reason, we added the ability to insert circuit components between coil interfaces inside the electromagnetic field solution domain. As a result, parasitic and other phenomenological effects can be modeled in a single transient solution.
For example, an application that benefits from this new addition is bus bars. Bus bars play a significant role in power applications, creating interfaces between the power module and the rest of the system. Applications range from power electronics to large transformers.
To illustrate, the image below shows part of an IGBT. It is possible to add a switch linking two branches of a bus bar and therefore, simulate and perform the double-pulse test with a single transient run.


3. Losses in Laminated Materials
Another area of interest, particularly for automotive and aerospace applications, is accurately estimating losses in high power density machines. Consequently, improvements to core loss calculations using the anhysteretic approach is significant because of the speed of calculations that it offers.
Specifically, two new data fitting models have been added and an analytical eddy loss coefficient has been implemented.
Most noteworthy, the absolute error fit for the identification of the Steinmetz coefficients for determining iron losses. The absolute error fit performs great at moderate to high magnetic induction levels and at medium to high frequencies.
Extending the Multiphysics
4. Time Average Loss Export
Another improvement expands on the export of nodal forces and force density fields introduced in Simcenter MAGNET and Simcenter Motorsolve 2019.1 release by now including time average total losses for use in thermal and CFD analysis.
In addition, for Simcenter Motorsolve, the time average total loss in each component is exported separately:
- Rotor core
- Stator back iron + teeth
- Stator coil sides
- Rotor magnets


Enhance The User Experience
5. Reduce material data input discrepancies
Next, let’s discuss material data. When entering the coefficients of the Steinmetz equations for iron loss calculation or providing an increasing or decreasing branch of the hysteresis loop for the identification of the Jiles-Atherton parameters, the quality of the fit can be studied to ensure there is no discrepancy.

6. Avoid Ill-defined Optimization Problems
Finally, it is sometimes difficult to ascertain if the design space of an optimization problem satisfies the user defined constraints. As a result, this may affect convergence of the optimization algorithm and the solution might fail, which can be a waste of time and very frustrating!
For that reason, a preprocessor has been added to Simcenter MAGNET Design Optimization 2020.1 to deal with ill-defined design optimization problems, involving several objectives, constraints and design variables that satisfy the constraints.
Comments
Comments are closed.